Spindle problems can spin out of control
Spindles are a bit like the people who run them. Ignore minor aches and pains and small problems can turn into systemic failure. Disregard routine maintenance and the machine will…
Spindles are a bit like the people who run them. Ignore minor aches and pains and small problems can turn into systemic failure. Disregard routine maintenance and the machine will soon need surgery.
One of the biggest problems with CNC technology is that it invites such complacency. After decades in the woodshop, these routers have become so reliable and predictable that we tend to forget just how much work they are doing. We also sometimes forget that a spindle rebuild can cost about the same as hiring a man for a whole month.
So, if you haven’t done so lately, this might be a good time to pull out the owner’s manual and have a look at some suggested and required maintenance schedules. Does the manufacturer suggest steps such as warm-ups at the start of the day or using a vacuum instead of compressed air to clear dust? Are your people doing these things diligently? Routinely skipping minor maintenance can add up to big problems over time. As Ben Franklin used to delight in telling folks: “Beware of little expenses. A small leak will sink a great ship.”
The point here is that a few minutes of warm-up can get the lube flowing properly around bearings before they are asked to go to work. Or checking runout every so often can pinpoint a failure before it happens. Some signs that your team might be dropping the ball here include a change in the way the spindle sounds, increased heat when you physically touch the housing, any kind of vibration or an error code. It doesn’t seem to matter much what type of bearing it is: those signs of trouble are fairly universal.
As with most metal, the main enemy is too much heat. Even in air-cooled aluminum spindles, if fans can properly dissipate the heat then the spindle will enjoy significantly longer life. Let heat build up because of undue friction and there will be repair bills. Can you improve the air flow? Or pre-chill the fluid in a liquid system? Ask your factory salesperson if these are options. As Mr. Franklin used to say: “an ounce of prevention is worth a pound of cure.” Chilling the fluid can extend the life of bearings by several times and even deliver more power to the cutter. But chillers, like spindles, also need routine maintenance such as checking filters and fluid levels and occasional flushing. And if they’re equipped with an alarm system that monitors heat buildup or fluid levels, a woodshop needs to make sure its operators know how to respond.
Involving operators in routine maintenance is absolutely essential, even if the shop has a designated repairman to perform these tasks. The woodworker who is actually running the machine will be the first to notice something amiss, as long as he/she is trained to do so. Here’s another quote from Ben that seems especially apt here: “Tell me and I forget. Teach me and I remember. Involve me and I learn.”
Preventative maintenance
Long-interval routine maintenance, as opposed to daily or weekly tasks, can be a bit of a challenge to implement or even plan. There is such a vast array of choices when it comes to spindles that it’s difficult to reduce them all to simple rules of thumb. For example, some shop owners used to think they should routinely replace or rebuild spindles at set increments (perhaps every couple of thousand hours). But most shops nowadays will just run until there’s a problem and then seek repair or replacement.
By the way, if you are replacing an original spindle with a reconditioned one, pay special attention to the warranty. It will probably not be as strong as the original equipment one and might require routine maintenance to be valid.
Depending on the production schedule and budget, woodshops with more than one milling center that share the same spindle model will often keep a spare on hand, so there’s no downtime if one fails. Others are willing to pay a stiff premium to have a repair done in a couple of days, rather than waiting for weeks. If the horsepower is low enough, it can sometimes be less expensive to replace than rebuild. And on some models, upgrading the horsepower (or the configuration — is it time for an aggregate?) might be a viable option. An underpowered spindle will fail sooner than an overpowered one. Plus, matching RPM to the tooling diameter, the path speed and the material density is something one might want to talk over with the router and/or the spindle manufacturer’s rep before overwork takes its toll. There are so many variables here that it takes both specifications and experience to get the formula right and avoid excessive or traumatic wear. Sometimes, for example, the material might even require slower RPM.
Discovering why a spindle is either misbehaving or has already suffered a substantial failure is usually the province of professionals. For that, most shops need to ship it out to get the right answers. But sometimes, a little research ahead of time can pay dividends in avoiding failures or dealing with them once they occur. High Speed Technologies (HST, online at highspeedtechnologies.com) has a really interesting page on its website called “Why did my spindle fail?” Based on more than a hundred thousand repairs, the article goes into detail on the most common causes of failure including contamination, mishandling, incorrect preloading, overloading, lubing, imbalance, drawbar mechanism and statistical bearing failures.
When something fails
If you’re lucky, you might be able to replace an off-the-shelf, inexpensive top bearing in-house, which might shut down production for a few hours or even be fixed overnight and not interrupt a kitchen’s delivery schedule. Many shops keep one or two spare bearings on hand for just such an emergency.
But odds are that your spindle repair won’t be a DIY project. If something is out of true or building heat, then it’s usually time to talk to an expert. In most cases, that will be the company that supplied the spindle, its authorized repair facility or the supplier that originally sold you the CNC center.
If those aren’t options, then a woodshop will need to source an aftermarket repair facility. To get an idea of the process involved in doing that, Woodshop News recently spoke with Bob Barone of PDS Spindles (online at pdsspindles.com), which operates repair facilities in the U.S., Germany and Brazil. Barone is headquartered at the company’s offices in Bessemer City, N.C., and his team processes repair orders from across the country. They work on all brands, both belt-driven and electric.
Whether you’re working on spindles in-house or shipping them out for repair, routine maintenance and team training are the keys to reducing ongoing costs. Spindles are expensive elements in the manufacturing process and a failed unit can cost a lot more in downtime than the price of repairing it. So it’s absolutely essential to train people in more than just operational procedures: they must also be involved in maintenance and hopefully be able to recognize when something is going wrong before it actually does.Once a woodshop ships a spindle to PDS, the repair sequence generally begins with an initial free inspection that’s designed to discover why the spindle failed. This is critical, as it could reflect the way other spindles in the woodshop will behave and also how this particular spindle might avoid or at least delay future repairs. What the technicians find is then included in a written quote, which is discussed with the customer who must give approval before work begins. If the woodshop decides not to proceed, the company will simply ship back the spindle at the customer’s expense. In most cases, PDS will be able to offer a standard three-to-five business day (plus shipping) repair service that comes with a written warranty on both rebuilds and upgrades. PDS also offers an emergency spindle repair service for shops that need to finish a job and get it out the door in a hurry. In that case, the woodshop needs to call ahead to discuss schedules and special fees apply because people and parts will need to be reserved.
As old Ben liked to say: “An investment in knowledge pays the best interest.” He also admonished us that “By failing to prepare, you are preparing to fail.”
This article originally appeared in the January 2017 issue.
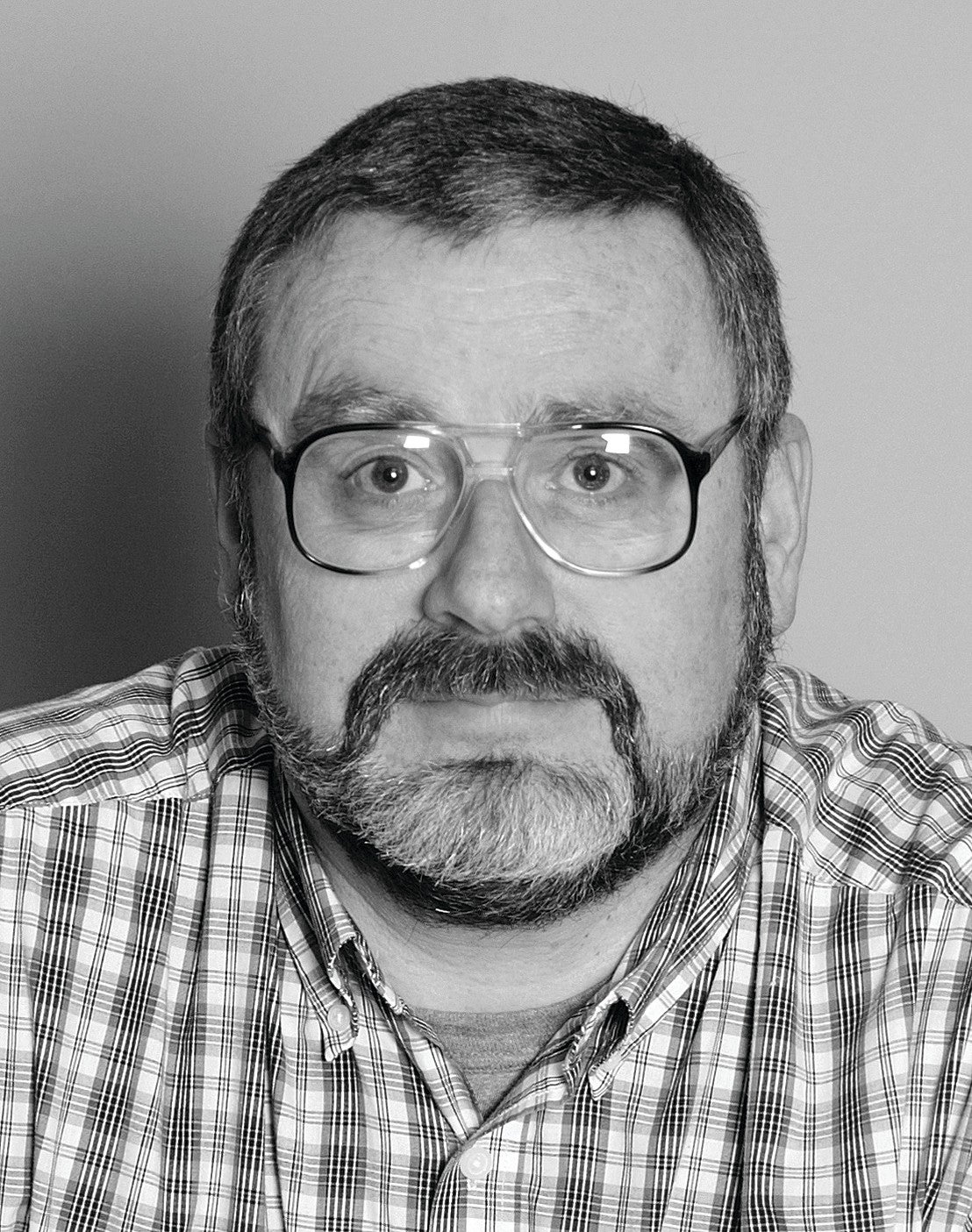