Drive motors are the muscle behind CNC
Though the software side of CNC is the brains of digital fabrication, the muscle side is the drive motors and the related hardware that provide electronic signals and electrical power…
Though the software side of CNC is the brains of digital fabrication, the muscle side is the drive motors and the related hardware that provide electronic signals and electrical power to the drive motors.
Though there are many types of drive motors, the easiest to understand are direct-current stepper motors. A stepper motor is different than an electrical motor on a woodworking power tool as it receives the electricity driving it in pulses rather than continuously. The electrical pulses come from the motor driver that is like a switch that is turned on and off by the software controller, sometimes called an indexer, based on directions given by G-code. Stepper motors also have no brushes as the armature/shaft is turned by electromagnets placed within the motor frame.
A stepper motor operates only one step at a time — hence the name — and each step is exact. Because of this, a stepper motor can reverse quickly and easily. These characteristics, coupled with the software controller and the hardware motor driver, are what make CNC machining possible.
Stepper motors generally turn 1.8 degrees for each pulse of electricity they receive from the motor driver and it takes 200 turns for a full rotation. As the frequency of the pulses from the motor driver increase, the stepper motor will begin to turn continuously like an electrical motor on a power tool and the CNC machine will move faster.
Open and closed systems
A typical stepper motor operates in what is known as an open-loop system, which means there is no feedback between the stepper motor and the software controller. Once the CNC machine is “homed” [set to and x="0," y="0" z="0"], the software controller assumes the motor has and will move in the correct direction and distance based on the number of pulses the software controller has sent to the motor driver. While this might seem a heroic assumption, stepper motors and stepper motor drivers have evolved through several decades into extraordinarily dependable pieces of equipment.
Mechanically, a stepper motor is very simple and rugged, especially when operating in an adverse environment like a dusty shop. Generally, what limits the life of a stepper motor is the quality of the bearings that support the drive armature/shaft. With the increasing quality of the seal bearings available, the dependability and life of stepper motors have increased significantly.
Though stepper motors make a CNC machine move, it is the stepper motor drivers that have brought digital fabrication within the reach, both financially and operationally, of smaller woodworking operations. As mentioned earlier, a stepper motor driver is like an on/off switch that delivers pulses of electricity to cause the stepper motor to turn and, though this is a good initial description, as with all things electrical and electronic, it is a bit simplified.
A hardware motor driver is a type of amplifier that takes very low voltage signals from the software controller and higher voltage from a direct-current power supply and sends DC electrical pulses to a DC stepper motor. A typical hardware motor driver can adjust the duration of an electrical pulse so a DC stepper motor will turn less than 1.8 degrees.
There are closed-loop systems, which use a servomotor drive system to provide control of a desired operation through the use of feedback. A common such device is the cruise control on a car or truck. A closed-loop drive system includes a motor, an encoder and a method of feedback from the encoder to the software controller to provide speed and location information to the software controller. Because of the more complex and sophisticated mechanical and software systems, the cost of the servomotor drive system is much higher than a stepper motor drive system. Hence, this type of system is used on higher-cost CNC machines that will log long hours in a factory setting.
There are also hybrid stepper motors that have the mechanical and operation characteristics of a plain stepper motor, but with an encoder functionally similar to that found on a servomotor. The software controller and the hardware driver will also have many of the functional characteristics of a servomotor closed-loop system.
Help me decide
So now you’re probably wondering: should I buy an open- or closed-loop system?
For many small-to-medium-sized woodworking shops, where the jobs are unique and the requirement is more for efficiency rather than for high-production rates, a stepper motor drive system will more than likely meet its current and future needs. The reasoning behind this is that the stepper motors and the hardware drivers have evolved and are quite competent and dependable.
This article originally appeared in the July 2014 issue.
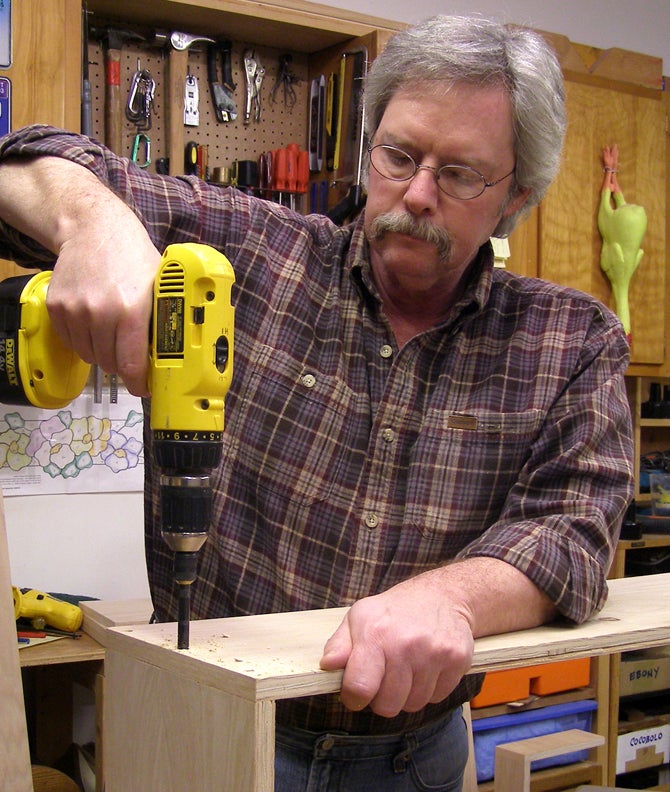
A.J. Hamler is the former editor of Woodshop News and Woodcraft Magazine. He's currently a freelance woodworking writer/editor, which is another way of stating self-employed. When he's not writing or in the shop, he enjoys science fiction, gourmet cooking and Civil War reenacting, but not at the same time.