Drive systems are vital to CNC router operations
Moving the router or spindle over the table is the primary function of a CNC router’s software, hardware and motors. To get this motion means changing the rotary motion of…
Moving the router or spindle over the table is the primary function of a CNC router’s software, hardware and motors. To get this motion means changing the rotary motion of the motors into linear motion to move the router’s cutter along the X, Y and Z axes and constraining that motion in a straight line in the case of a three-axis CNC router.
There are two systems used in the moving of the CNC router’s axes in a straight line. The first is the drive system and the second is the constraint system. Together these are known as linear motion systems. This article describes the drive systems. Next month’s article will describe the constraint systems.
Though there are many variations, the two primary drive systems are:
• Translation screws; specifically square thread screws, Acme screws, or ball-bearing screws and
• Gear trains; specifically a rack-and-pinion system
Like everything else in life, there are tradeoffs with each of these drive systems that move the router’s axes in an accurate and repeatable manner. But you shouldn’t confuse the concepts of accuracy and repeatability. The worst drive system can have excellent repeatability, but if a CNC router’s accuracy is poor, meaning the axes do not move as called for by the G-code, high repeatability means nothing more than making very expensive firewood and sawdust at a rapid pace.
Broadly described, a linear constraint system consists of a platform, called a truck, riding on a fixed rail. The fence on a table saw is a perfect analogy, though in the case of a CNC machine, there are two rails for each axis.
Translation screws
Translation screws, also known as power screws, are part of a broad category of drive systems that translate rotary motion into linear motion based on a screw thread. The thread is attached to some sort of nut, which is attached to the CNC machine’s axes to be moved. The axes’ movement is further constrained and directed linearly by the rails and trucks.
Translation screws and friction nuts have been around for centuries in metal working machines and are classified by thread types. Square threads, as the name suggests, have square threads. Acme threads have threads cut at a 29-degree angle. Square threads are the more efficient of the two, requiring the least amount of power to turn with a given load. But square threads are more expensive to manufacture.
Ball-bearing screws are a type of translation screw that uses a ball-bearing nut to translate motion from rotary to linear instead of a friction nut. The threads of a ball-bearing screw and nut are ground to create a raceway, eliminating friction between the screw and the nut. Ball-bearing screws and nuts come as a single component.
Ball-bearing screws are generally 90 percent efficient, compared to a broad average of 50 percent efficiency for square and Acme threads. But they are the most expensive to manufacture. This is offset by their durability and precision characteristics.
Though translation screws are common and continued to be successfully and economically used in all types of metalworking and woodworking tools, they have two negative characteristics in a CNC machine application.
The first is whiplash. A translation screw starts as a metal rod and, as any rod gets longer, irrespective of its diameter, it tends to bend toward the ground. Fixed to a motor, a longer rod will flex perpendicular to its length as the speed is increased. To envision this, think of putting a fishing pole in a drill. At top speed, the fishing pole will end up looking like a skipping rope.
The second is backlash, which is lost motion between mating components because of clearance or slackness when movement is reversed and contact is re-established. To envision backlash, think of a stopped train that begins to move forward. The couplers on the cars will bang into each other as they are pulled apart by engine’s forward motion.
Whiplash and backlash can be managed though design considerations. For instance, the diameter of the lead screw can be increased to limit whiplash. Other solutions include increasing the length of the friction nut or limiting motor speed.
One of the most straightforward methods to reduce backlash is to place a tensioning spring between two friction nuts. This creates a static loading force known as preload. However, if the motor is powerful enough, the spring could compress and the preloading would be diminished. Another method is to cut the friction nut across its diameter and reassemble with screws so one side of the nut rides on one face of the thread and the other side rides on the opposite face of the thread. This method allows for easier adjustment to compensate for wear though use.
With today’s CNC machines that use translation screws, backlash isn’t a big problem. Electronic controllers and laser calibration in the manufacturing process have made it minimal.
Gear train drives
Gear train drives in a three-axis CNC router are based on a rack-and-pinion system, which consists of two parts:
The rack, which can be thought of as a gear that can be unrolled to any length, and the pinion, a circular gear attached to the drive motor, either directly or through a belt-driven gearing system or a gear box.
A rack-and-pinion drive system is quite simple compared to a translation screw drive system. The pinion and motor are held firmly into the rack though a spring-tensioning system and the rack is fastened securely to a structural element of the CNC machine frame. With everything held firmly, there is little chance of backlash or whiplash.
As three-axis routers are powered by stepper or servo motors, they require gearing between the motor and the pinion gear to cut at a high speed, since the motors have to run at a lower speed to achieve the most torque. Rack-and-pinion systems deliver very fast speeds — as much as 1,000 inches per minute in a non-cutting movement — and have stood the test of time. For use in a dusty woodshop there are enclosures for rack-and-pinion drive systems, which are a great help in minimizing, though not eliminating, cleaning and lubrication.
This article originally appeared in the September 2014 issue.
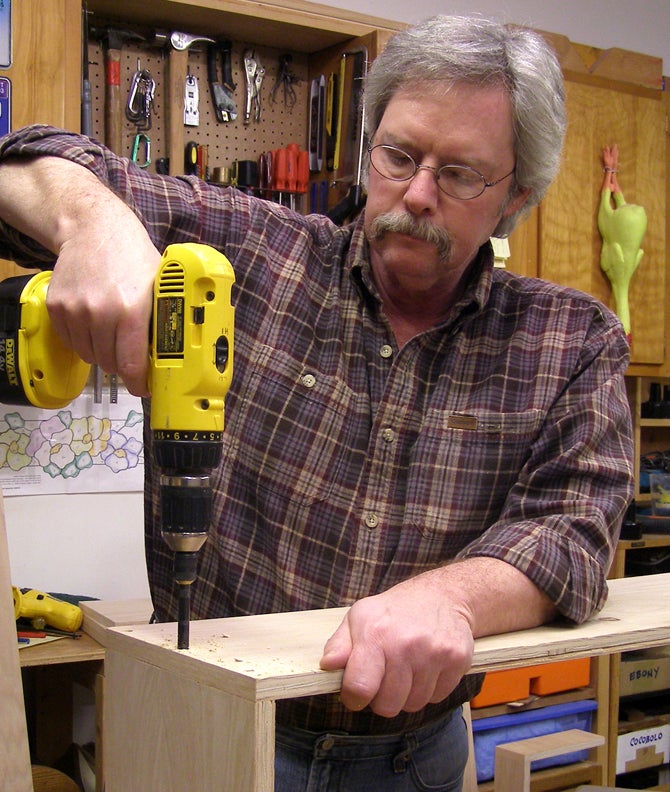
A.J. Hamler is the former editor of Woodshop News and Woodcraft Magazine. He's currently a freelance woodworking writer/editor, which is another way of stating self-employed. When he's not writing or in the shop, he enjoys science fiction, gourmet cooking and Civil War reenacting, but not at the same time.