Woodshops use spray equipment for two obvious reasons. Guns apply finish quickly, and they apply it evenly. With a little practice, most woodworkers can spray a lot faster than they can brush a coating. A gun also takes advantage of fast-drying finishes to avoid runs and dust problems. Quicker drying lends itself to thicker coats, too, and more protection. Spray guns can be used to apply clear coats, stains, toned clear coats with stain added, and of course paints. In today’s market, fewer than half the kitchens being installed are natural wood, so paint is a factor.
Configurations
The guns and equipment are constantly changing, but they still stick to three basic configurations. They can have a gravity bottle (reservoir) on top, or a suction (siphon) bottle below. Or in most commercial situations, there’s a pressurized hose that runs between the gun and the drum of coating (no reservoir). There are two hoses when the gun is run on compressed air (one for air, one for product), and one hose plus a cord for electric guns. For now, most professional guns still use air, but advances in batteries are beginning to change that. There are many handheld units already on the market. In the trade, ‘handheld’ refers to a gun that is self-contained. The tool contains both the pump and the reservoir, so there are no hoses attached. And many of these smaller guns run on lithium ion batteries, so there’s no cord either. It’s a pretty good bet that commercial cordless spraying will be a lot more mainstream soon, as battery amp hours continue to increase. One major obstacle here is that batteries are heavy, so hand/arm fatigue becomes a factor when one includes the weight of the liquid coating in the reservoir, the electric pump and now the batteries. At this time, cordless isn’t really an all-day option but is certainly viable for one-off furniture builders.
There’s a learning curve with guns that includes avoiding runs and contamination, and that can be a little expensive. It takes a while to train somebody to produce an excellent finish. But a bigger problem with spray equipment has always been ongoing waste. High pressure traditional guns can overspray an enormous amount of product. A lot of the product going through the nozzle misses its target.
High volume low pressure (HVLP) guns have addressed that issue, but there is a little bit of a trade-off. HVLP describes the amount of air being moved – lots of it, but not a lot of pressure (pounds per square inch, or PSI). Conventional guns atomize the paint more efficiently (break the fluid down into a very fine mist), so they deliver a finer finish. HVLP spray guns have slightly larger mist droplets because of the lower air pressure, so they spread a thicker coat. However, the lower pressure also means that the gun can be held closer to the work, so the spray pattern is more accurate and controllable. That means a whole lot less waste.
HVLP systems often come as a complete outfit that includes the turbine, hose and gun. A turbine is essentially an electric fan in a confined space that creates air pressure. They are relatively inexpensive and are a great choice for small to medium sized woodshops. But HVLP spraying goes a little slower, too, and can clog quite easily on product that has some volume (thickness) to it, so larger industrial concerns generally find other solutions.
While HVLP is the method of choice for most small- to medium-sized custom shops, one-man operations and skilled amateurs might also want to take a look at LVLP guns. These low volume low pressure tools are generally inexpensive and uncomplicated, and even a small air compressor can keep up with them. However, they don’t have much oomph, so they’re quite slow and they also can’t push thick finishes such as un-thinned paint very well.
Those gravity bottles mentioned earlier have an obvious upside (no pun intended). With this configuration, the finish doesn’t have far to travel as there’s no hose, and the position of the bottle takes advantage of simple gravity. Liquid likes to flow downhill. Auto refinishers really like this set-up because there’s almost no waste and as long as you have the arm muscle, it can be very accurate. You wouldn’t want to do a whole hospital with this gun, or perhaps not even a large kitchen all at once, but if you pace yourself it can be a very satisfactory solution.
At the other end of the spectrum, there are robots. In the past, an automated painting system had a series of stationary guns and the parts were passed in front of them. We’ve come a long way in a short time. Now, robotic arms simulate the dexterity of a human hand, twisting and rotating in unimaginable ways at a high rate of speed to deliver even coats accurately. There are completely enclosed systems where parts are loaded in or pass through a large cabinet, and there are single arm solutions where the parts are hung on a rack and the collaborative robotic arm applies a coat using one or several nozzles. This latter option is surprisingly affordable and well worth a look for shops running more than about one job a week.
Going airless
Traditional high-volume systems are still widely used in large factories where the sheer scale of operations requires their power to keep up with demand. They deliver a superior finish (in the right hands) but are somewhat wasteful in terms of product, and quite expensive to purchase and set up. A large woodshop that does a lot of outsourced work for other shops may consider this option, but only after a detailed cost analysis. The guns, booth, exhaust system, compressor, and operator training are all serious cost considerations.
For on-site work and in many small shops, an airless spray system can make sense. This is an electric piston (pump) that has one hose going to the gun and another coming from a bucket of coating. The piston develops pressure that both sucks and pushes. It moves up and down inside a cylinder, sucking in air at one end and compressing it at the other by using one-way release valves. Depending on how it’s built, a piston can create an enormous amount of pressure that dramatically exceeds the performance of a standard air compressor. A good rule of thumb is that the bigger (and more expensive) the piston is, the better the finish will be because more pressure means better atomizing and a finer mist. And because they don’t depend on an external air compressor, airless systems are somewhat portable. They are also relatively simple mechanically, so they don’t often fail in the middle of a job.
There are very small and very large airless systems available. At the lower end, homeowner versions may have a bottle instead of a direct feed from a drum of finish. At the higher end, factories automate them with robotics. A woodshop looking at this system needs to have a serious conversation with their salesperson about the type of liquid being sprayed, the available tips (nozzles), and the effects of different hose lengths. There is a relationship between tip size and pressure that takes a while to understand before one consistently achieves a good spray pattern. Also ask about flushing (a built-in cleaning option), which lets the shop switch products quickly, and whether the gun allows for reversing the tip to clear a clog.
There is another option for coating that is just beginning to gain traction in the cabinet industry. Electrostatic spray painting (powder coating) is offered by several door manufacturers and aftermarket shops. Here, the pigment/coating is in a powder rather than a liquid state, and the grains are electrically charged. Remember playing with magnets as a kid, where like poles would repel each other? That’s what happens here. The tiny paint particles try to get away from each other, so that by the time their energy is overcome by gravity, they have spread out very evenly across the door or drawer front. The surface of that component has also been charged with an opposite polarity or a ground, so the particles will stay in place (just as opposite ends of the magnets attract each other). Consequently, the amount of waste in powder-coating is very minimal. And those particles can reach in and around obstacles such as the profiles of moldings or hard-to-reach corners, so the paint gets excellent coverage even in places where liquid spraying has some challenges. The cabinet parts are then baked to melt and attach the paint properly. Powder-coating is expensive to get into, but not too costly when it’s outsourced. And the companies who coat MDF parts say that the finish is remarkably durable.
This article originally appeared in the July 2020 issue.
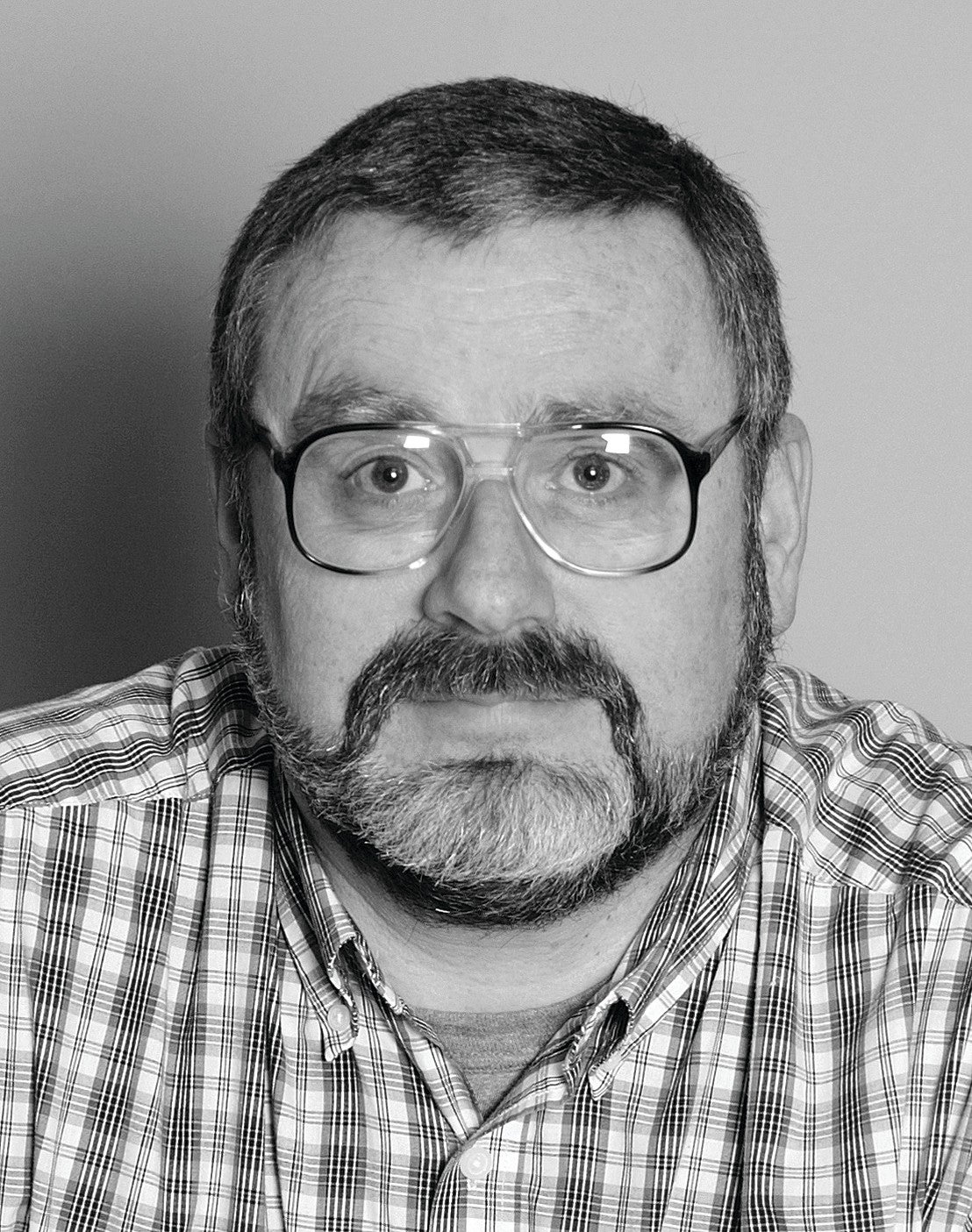