How to avoid those ever-lingering VOCs
We’re hearing a lot in our industry lately about volatile organic compounds, commonly called VOCs. The Environmental Protection Agency says they “include a variety of chemicals, some of which may…
We’re hearing a lot in our industry lately about volatile organic compounds, commonly called VOCs. The Environmental Protection Agency says they “include a variety of chemicals, some of which may have short- and long-term adverse health effects.”
In the woodshop, common sources for these potentially dangerous chemicals are paint, lacquer, paint stripper, cleaning solvents, sheet goods, glues and adhesives. All of these can release organic compounds while you are using them and, to some degree, when they are made into furniture and cabinetry and installed in a client’s home or office. That is, the volatility often continues past the manufacturing phase in a product’s life cycle. That means there’s a potential danger for both your employees and your customers, especially as the government notes that concentrations of many VOCs are consistently higher indoors (up to 10 times higher) than outdoors. And, of course, that’s where most cabinets and furniture are built and used.
It’s a complicated topic. For example, the EPA defines a VOC as “any compound of carbon, excluding carbon monoxide, carbon dioxide, carbonic acid, metallic carbides or carbonates, and ammonium carbonate, which participates in atmospheric photochemical reactions, except those designated by EPA as having negligible photochemical reactivity.”
Huh? Speaking as an average woodworker (and one without a degree in chemistry), I have to admit that their definition went way over my head. So let’s take a quick look at the problem in layman’s terms.
These are compounds. That is, they all have more than one element from the periodic table. One of the elements always seems to be carbon, hence the “organic” part of the name. And volatile just means that these chemicals evaporate (enter the shop’s air) at very low temperatures. Well, low for chemicals in general. Room temperature, if you will. They also break down at normal levels of atmospheric pressure, which means they can bleed some of their elements into your workshop’s breathable air year-round. In fact, the lower a compound’s boiling point (the temperature at which it turns from a solid or liquid to a gas), the higher its volatility or ability to break down. The U.S. government talks about VOCs in those terms — rating them according to their volatility. In Europe, however, the government defines VOCs simply by their boiling point, which is much easier to determine and understand. According to the European Union, a VOC is essentially “any organic compound having an initial boiling point less than or equal to 250 degrees C.”
However, just to add to our confusion, the World Health Organization categorizes indoor organic pollutants in amazingly simple terms as “very volatile, volatile and semi-volatile.”
Local governments in the U.S. seem to have a better handle on the whole concept than any of these larger bodies. The Air Quality Management District is the air pollution control agency for Orange County and the urban portions of Los Angeles, Riverside and San Bernardino counties, which the agency itself describes as “the smoggiest region of the U.S”. People in those parts of Southern California have a special interest in VOCs, because the chemicals are an important source of smog. According to the district website (www.aqmd.gov), “VOCs, or solvents, are one of the key ingredients in coatings that contribute to ozone formation. VOCs are emitted from coatings from the containers themselves, as the coating is applied, and as the coating dries on the surface. The VOC emissions from the coatings can then mix in the air with other ground-level pollutants (nitrogen oxide, carbon monoxide, sulfur dioxide, hydrocarbons …) and the energy from the sun acts upon this mixture to form the brown gunk in the air known as photochemical smog.”
Ugh! For most woodshops, thankfully, the VOCs don’t show up as visible “brown gunk” in the shop’s air. But, nonetheless, they are present.
What’s available?
So what’s the best way for a woodshop to avoid VOCs in coatings? That’s easy: just switch to low- or no-VOC finishes.
While international giants such as Akzo Nobel, Henkel, Britain’s ICI Group, PPG and BASF are all serious players in this field, American companies are also taking this issue very seriously. That’s not surprising, because the EPA is leaning on states (and actually, in some cases, following state initiatives) in an effort to lower the country’s VOC emissions. Nowadays, local VOC regulations have to at least meet a level of stringency the feds call Reasonably Available Control Technology (RACT). That’s defined as “the lowest level of emissions that can be achieved, taking into account technical and economic considerations.” In other words, lawmakers and finish manufacturers are trying to find reasonable common ground on this issue that serves the best interests of both woodworkers and their customers.
With that in mind, Sherwin-Williams has developed a line of product called Sher-Wood LoVOC Lacquer that’s ideal for high-volume, high-speed finishing lines and offers a solution that not only satisfies current federal hazardous air pollutants (HAPs) regulations, but also meets proposed VOC limitations. The system is free of lead and chromate hazards, too.
DuPont has developed Capstone, which has allowed them to formulate both low-VOC and VOC-free paints and coating applications. They are also leading the charge in cleaners (Final Klean) and automotive finishes (ChromaSystem), that have low or no VOC emissions.
Valspar has developed Zenith Low-VOC wiping stain base and its Zenith Waterborne pre-catalyzed lacquer is low in VOC, HAPS-free, contains no formaldehyde or isocyanate, and is Greenguard-certified. (Greenguard is part of Underwriters Laboratories and helps manufacturers create interior products and materials that have low chemical emissions.)
Mohawk’s Waterborne Pre-Catalyzed Lacquer is a water reducible, self-crosslinking, low-VOC-emitting technology that has good color retention and is suitable for cabinet, millwork, furniture and other high-traffic interior wooden surfaces. Mohawk Finishing Products is a division of RPM Wood Finishes Group and this lacquer is also Greenguard-certified.
Green Building Supply in Iowa sells Safecoat wood stains and sealers that are non-toxic and are low- or no-VOC. Some are food-grade for toys, countertops, salad bowls and kid’s furniture.
Minnesota-based 3M Co. offers a variety of low VOC products. For example, any woodworker who regularly applies printed patterns to wood is probably familiar with its low VOC Super 77 spray adhesive. The company has a great online resource at http://solutions.3m.com that can help shop owners and managers search their vast product lines for similar adhesives.
H.B. Fuller’s waterborne adhesives are an extremely versatile and logical choice for bonding many types of substrates. Some of their advantages include the absence of VOCs, and ease of cleanup after application. The company develops low-VOC content and VOC-free polymers for interior paints as well as high performance formaldehyde-free polymers for insulation fiberglass and wood composite applications.
Minwax’s 250 VOC Compliant Wood Finish is a penetrating oil-based wood stain, available in 22 wood tone colors. This stain has been matched to the standards of the company’s traditional Wood Finish line, so there are no surprises.
Other leading paint and finish manufacturers such as Rohm and Haas, Behr and Benjamin Moore offer low- or no-VOC products for various woodshop applications. For example, Monocoat has been around since 1906 and is now a division of Special Hardwood Products. The company says that its oil finish (without accelerator) contains no VOCs, nor does it contain other harmful chemicals. Its clear-color oil is a pigment-free, natural finish that adds a slight amber tone to wood. It’s expensive in small quantities (about $116 a liter, which delivers roughly 500 sq. ft. of coverage on hardwoods, less with color added), but when it comes to VOCs, it’s safe.
Wax, oil and water-based
It’s no surprise that the hardwood-flooring sector has played an important role in developing low- and zero-VOC finishes for the woodworking industry. One noted leader in this area is Stang-Lund, which produces its own brand of hard wax oil finish, which it say is an all natural, non-pollutant, non-toxic, no-VOC product with no biocides or preservatives and it’s also free of lead and benzene. The company’s hard wax oil finish is produced from natural materials such as vegetable oil and natural waxes made from purified renewable natural raw resources. The idea is that the oil penetrates the wood, while the wax stays on the surface. That wax and oil combination seems to be one key to the new generation of low- or no-VOC finishes.
Many water-based products, including latex finishes, are offered as low-VOC compounds and, in most cases, these have less than 250 grams per liter of volatile organic compounds. Similar oil-based products range up to 380 g/L. Products that the EPA considers as no-VOC are rated at less than 5 g/L, but those measurements are made by the manufacturer before pigment or any other additives are included and these can bump the VOC content a little.
Bottom line: Ask your current finish supplier what they offer in terms of no- or low-VOC finishes and, as soon as you switch, let your customers know that you have their best interests, and your employees’ best interests, at heart.
This article originally appeared in the May 2013 issue.
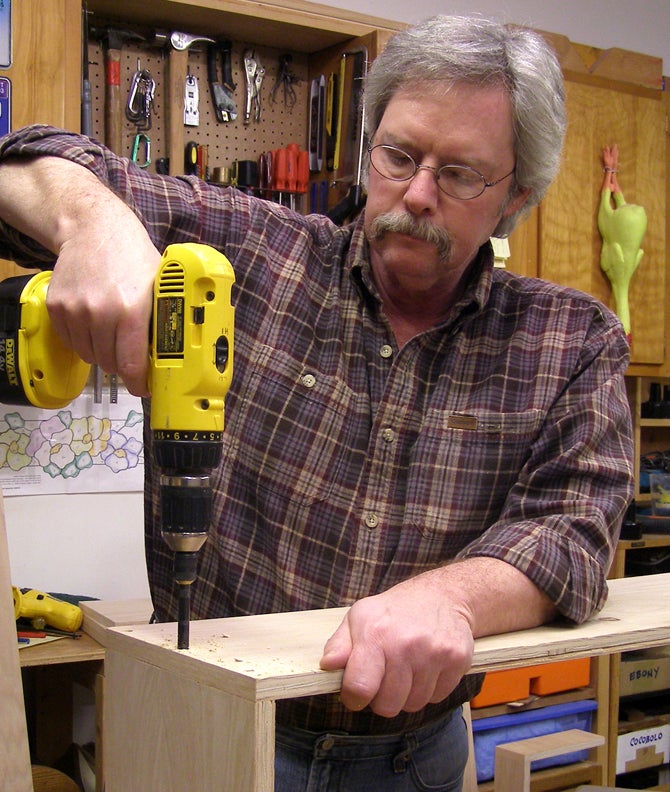
A.J. Hamler is the former editor of Woodshop News and Woodcraft Magazine. He's currently a freelance woodworking writer/editor, which is another way of stating self-employed. When he's not writing or in the shop, he enjoys science fiction, gourmet cooking and Civil War reenacting, but not at the same time.