Lamp sheds light on wonders of veneer
A standard thickness for commercial veneer is 1/42 of an inch. At that thickness, many species of veneer are thin enough to be quite translucent. When light passes through such…
A standard thickness for commercial veneer is 1/42 of an inch. At that thickness, many species of veneer are thin enough to be quite translucent. When light passes through such veneers, their color and tone often change. Indeed, many veneers have a more brilliant, exciting look when light passes through than when the light is simply reflected off an opaque surface, such as when the veneer is glued to an opaque substrate.
The lamp shown in the accompanying images is an attempt to exploit the translucent properties of veneer. Both the top shade and the shank of the light can be illuminated from the inside allowing light to pass through and illuminate the veneer. Of course, the piece is functional; the top bulb provides indirect lighting for the space above the lamp as well.
The lamp's mechanics
The lamp is wired to be in one of four states: No light, light in the shank of the lamp, light in the top of the lamp, and light in both the top and the shank of the lamp. The state that the lamp is in is controlled by one push-button switch on the top of the base of the lamp. The lamp can be dissembled for shipping or for replacing bulbs. The top can be separated from the shank and the shank can be separated from the base. And the entire lamp comes off the table built specifically for it.
Happily, my interest in translucence resonates with a couple of other personal interests: marquetry and Judaica. If one is interested in how different veneers respond to the passage of light, then exploring that interest with the variety of veneers typically used in marquetry clearly moves the enterprise forward. Also, I have recently been dealing with Jewish themes in my work and marquetry provides an explicit way of incorporating such themes.
The focal images in the lamp bottom and the lamp top are Hebrew letters. Both the top and the bottom contain the Hebrew letter shin. The letter shin also stands for fire or flame. In the top of the lamp, it is the first letter of the word shalom, which is Hebrew for peace.
The shank of the lamp much more explicitly deals with light/translucence. Depicted is the lighting of Sabbath candles with images of candles, a sun-like halo around the flames of the candles and a woman's hands. Traditionally, the Sabbath candles are lit by women. The movement of their hands, in many traditions, is important to this ritual. The hands do a kind of dance winding around or circling the two lit candles three times. The specific meaning of these movements is obscure, but it looks as if the woman is trying to "take in" or incorporate the light.
The images in the four panels relate to one another in a circular fashion. Just as we think of the practice of religious ritual as part of something that has no beginning or end, there is no place in which the image begins or ends.
Construction of circular imagery takes some planning. I visualize the set of images I want. The sketch or cartoon is completed so there are objects that are cut off at the right margin of the drawing; these objects are then competed at the left margin of the drawing. Of course, one can think of it as having objects cut off at the left margin being completed on the right margin of the sketch. The sketch is then divided into four panels.
Technical issues
Naturally, there were a variety of technical problems that presented themselves. The veneer had to be attached to a material that would stiffen it sufficiently to maintain its integrity and still let light through. I used clear Lexan for the substrate because it is sufficiently stiff and is transparent. The glue also needed to be transparent and bond well with the Lucite. After some experimentation with a variety of adhesives, I settled on a 3M adhesive transfer tape (468MP) specifically made for high-energy substrates.
Light bulbs generate heat. The Lucite and the veneer have different coefficients of expansion with heat. To minimize the fluctuation in temperature caused by turning on the lights, the areas that house the bulbs are open at the top and the bottom. This permits air to move freely and vent the heat. The shank of the lamp is closed in more than the top of the lamp. Since florescent bulbs generate less heat than incandescent bulbs, florescent bulbs were used in the shank. An incandescent bulb is used in the completely open top.
Of course, different bulbs have different color temperature distributions. The incandescent bulb has a warmer spectrum than the fluorescent bulb. The difference in color temperature of the fluorescent and incandescent bulbs drives an interesting difference in the appearance of the veneer. For example, the incandescent bulb accentuates warmer colors like red.
Sculpting the solid parts
The glow of the lamp from within clearly steals the show, but there is another detail that woodworkers might find interesting. Everything is held together with solid oak legs and corners that are sculpted. Although they are not round and the sculpting is not symmetrical around each individual piece, they were made on a lathe.
The technique is a derivative of what is known as "inside-outside" turning. It involves temporarily gluing four spindle blanks together into a larger blank that is the same length, but twice the width and depth of each of the component spindles. The new (aggregate) blank is turned on the lathe. When finished with this stage, there is a single turned corner on each of the four constituent blanks. The aggregate blank is split or decomposed into the four original blanks. The four blanks are temporarily glued up a second time. This time a new corner is exposed. The reconstituted aggregate blank is put on the lathe and turned a second time. The third and fourth corners are sculpted on the lathe in the same way. When the blanks are finally separated for the fourth time and cleaned, four identical legs are the result.
Designing and building this lamp has been an instructive adventure. The visual drama of backlit veneer is difficult to match and very attractive. There are serious technical issues associated with achieving these results. I have discussed some of them and revealed my efforts at solving them. I look forward to more work in this realm, learning/developing more sophisticated solutions to technical problems and taking the design possibilities as far as I can.
Abraham Tesser is the principal of Tesser Furniture in Athens, Ga. To see more of his work, visit http://tesserfurniture.com.
This article originally appeared in the March 2011 issue.
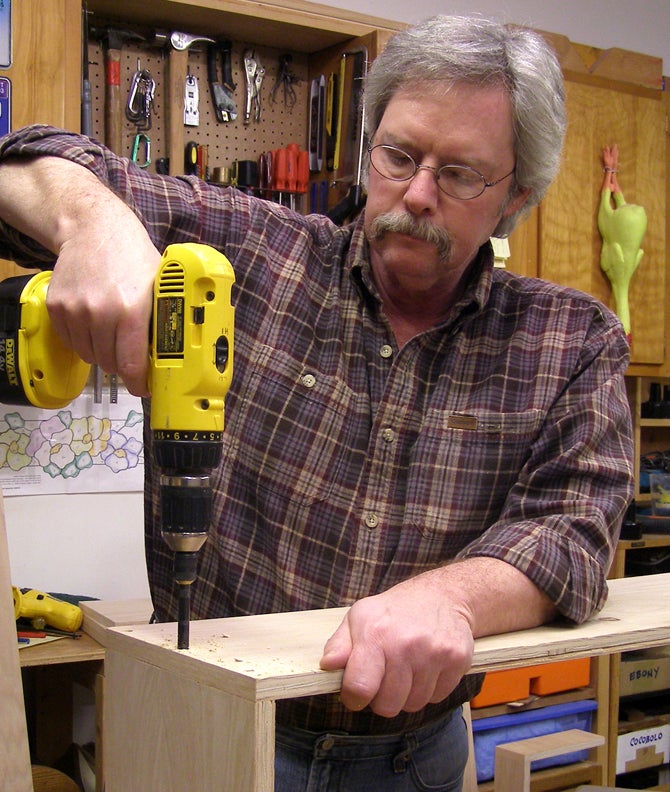
A.J. Hamler is the former editor of Woodshop News and Woodcraft Magazine. He's currently a freelance woodworking writer/editor, which is another way of stating self-employed. When he's not writing or in the shop, he enjoys science fiction, gourmet cooking and Civil War reenacting, but not at the same time.