Sanding head variations have their roles
There are four basic types of sanding heads and one major hybrid variation that can be applicable to any sanding head type that incorporates a polishing platen. Contract drum head…
There are four basic types of sanding heads and one major hybrid variation that can be applicable to any sanding head type that incorporates a polishing platen.
Contract drum head
Contact drum heads are generally incorporated in most widebelt sanders as the sanding head “type of choice.” They come in a range of diameters (4” to 18”) and a wide range of hardness (30 to 95 durometer in rubber, or even steel).
They are used for cut down and dimensioning, using 24- through 50-grit belts; intermediate sanding, using 50- through 80-grit belts; and in some applications, finish sanding, using 100- through 400-grit belts. They are one of the most critical components in a widebelt sander, but have a tendency to produce chatter marks if not properly constructed and maintained. They interface with the part being sanded with a line contact, exerting a high unit pressure.
Combination drum and platen head
Combination type sanding heads employ both a contact drum and a polishing platen within the same abrasive belt. They normally have adjustments so that sanding can be accomplished with the drum only, platen only, or with both drum and platen. A disadvantage to these types of sanding heads is that the distance between pinch rolls or hold-down shoes becomes extended so that minimum part lengths are longer. A second disadvantage to any platen-type sanding head is their greater tendency to create streaking. When using the platen, they interface with the part being sanded with a flat surface, exerting low unit pressure.
Platen head
Platen heads (smoothing bars) were developed to deal with the chatter marks and belt splice marks often produced by contact drum-type sanding heads. Polishing platens perform the exact function that their name implies. They impart a polishing-type finish that refines the scratch pattern or grit marks introduced by previous sanding heads. When an abrasive belt is run on a platen-type sanding head, its cutting and finishing characteristics are dramatically changed. This happens because instead of a line contact (obtained on contact drums), platens interface with the part being sanded with a large flat surface, keeping the abrasive in contact with the product for a period of time This fact results in:
• A longer scratch line because of greater dwell time.
• A smoother finish from any given grit belt because of the fact that as sanding dust is created, it is progressively trapped between the abrasive belt and the product and therefore the abrasive mineral is not able to penetrate as deep.
• No tendency to create chatter marks because the abrasive backup device [the platen] is non-rotating and also cushioned, it has no tendency to impart a chatter mark.
• Fewer tendencies to create belt splice marks because the abrasive belt entry and exit to the platen is relatively flat and it will not impart a mark from a stiff or out-of-specification belt splice. Its cushioned construction, low-unit-pressure sanding force due to the large surface area of the platen and long scratch line all help to eliminate the possibility of belt splice marks.
• However, platen type heads have a greater tendency to create streaking because dust does become trapped between the abrasive belt and the product and the tendency for streaking is increased, particularly if excessive pressures are applied. Also, the graphite pad cover and the pad itself are susceptible to buildup or grooving that then imparts its own streaking pattern.
Crossbelt platen head
Crossbelt platen heads employ a relatively narrow (6” to 12” wide) abrasive belt running transversely (at a right angle) across a piece part. Originally, these were one-piece solid platens, but in today’s modern machines they are always segmented platens. Crossbelt heads will cut more aggressively with any given grit belt then a conventional widebelt platen head — because cutting is at right angles to the grain — and are normally used for tape removal on veneered parts. They are also required if you’re sanding long parts with the grain running at right angles to the parts length, such as on desk front panels.
Segmented platen sanding head variation
Segmented platens can be provided on any of the above sanding head types that employ a platen. Approximately 30 years ago, the concept of a yielding segmented platen sanding head was developed. With this concept, yield is achieved within the sanding head so it can accommodate not only panel thickness variations, but also variations within the face being sanded. This type sanding head is ideally suited for seal sanding, lacquer sanding and veneers. It can also be used when sanding solid wood parts. It is an undesirable characteristic if thickness dimensioning is required.
For help with sanding problems, contact: Howard Grivna, Sanding Systems Consulting Inc. Tel: 218-678-2929. www.sandingsystemsinc.com
This article originally appeared in the November 2012 issue.
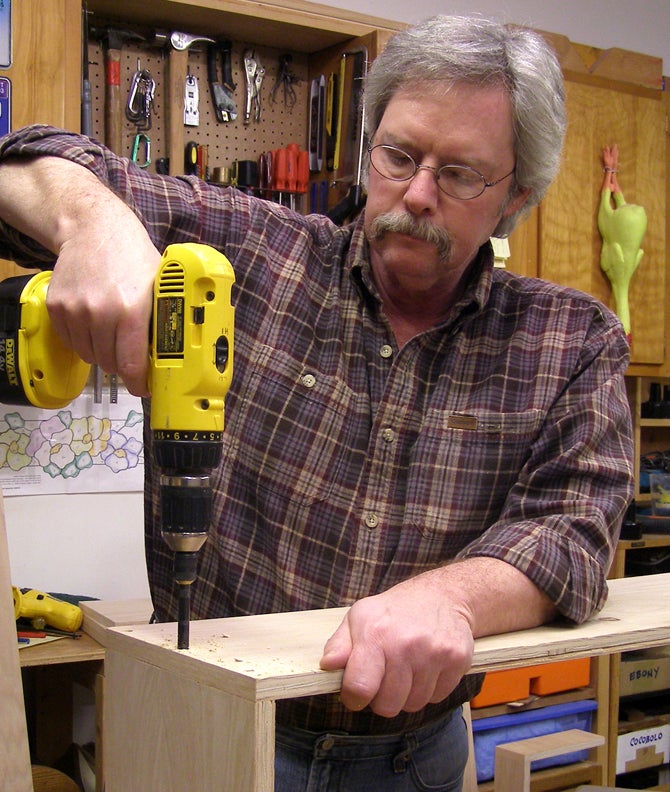
A.J. Hamler is the former editor of Woodshop News and Woodcraft Magazine. He's currently a freelance woodworking writer/editor, which is another way of stating self-employed. When he's not writing or in the shop, he enjoys science fiction, gourmet cooking and Civil War reenacting, but not at the same time.