In a free economy, supply and demand are supposed to determine price. That doesn’t seem to be happening right now as the woodworking industry evolves from primarily manual to more technical, automated processes. As we continue to replace cabinetmakers with CNCs and robotics, and consequently use our hands less, woodshops are not paying the new generation of ‘woodworkers’ at the same rate that other, competing industries pay skilled, high tech employees. Is this a problem?
What the government says
One of the lesser known reports published by the U.S. Department of Labor’s Bureau of Labor Statistics (BLS) is on industry by industry productivity, which measures output per hour. Despite almost full employment in the U.S., there was a widespread decline in manufacturing labor productivity in 2018. Woodshop owners might be surprised to learn that they were part of that. Productivity in the wood products sector fell a significant 4.6 percent in 2018. That’s a counterintuitive concept, because every shop owner in this industry watches robotics and automation grow daily.
If we have more machines and fewer people, then wouldn’t we have a higher output per employee? If the numbers are true, they might in some regard explain why the industry struggles to pay skilled people a competitive wage.
But the answer may also lie in another set of statistics. According to the BLS, there are now only 12,150 cabinetmakers left in the country! But there are some 50,860 machine operators in the woodworking sector alone, and another 38,500 sawyers. One might venture a guess that the statisticians don’t really understand the industry, or what its members do on a daily basis. And if they don’t define the parameters realistically, then there is reason to doubt their conclusions. The government seemingly paints everyone from foresters to finishers with the same brush.
There is one BLS statistic, however, that sounds like it might be somewhere in the ballpark of reality. Cabinetmakers and bench carpenters, according to BLS, earn $32,170 (median) and $34,460 (mean average) per annum. The median number is the middle (unweighted) number from a list of wages, while the mean is the average as most people understand it. That’s where one adds up all the wages and then divides by the number of woodworkers. So, cabinetmakers nationwide are averaging a mean of $17.23 an hour. Machine setters, operators and tenders (presumably, this includes people operating equipment such as CNCs, robots, edgebanders and beam saws) earn a little less, with a mean of $30,850 annually, or $15.43 an hour.
On Apr. 16, the BLS released its usual report on the earnings of wage and salary workers in the first quarter of this year, and the median wage of all of the nation’s 116.1 million full-time employees was $905 a week. That translates to $47,060 annually ($23.53 an hour), a statistic which says that woodworking pays only 73 percent of what the average employee in America makes. Just to give some perspective, Money magazine reported in May last year that the average salary for public school teachers, a sector that the majority of Americans feel is quite underpaid, was $58,353 in 2016.
Let’s face reality here. We’re not going to attract a lot of skilled or talented young people at a median wage of $17.23 an hour. And consider this: because of Industry 4.0, we’re now asking many of them to spend a large part of their workday either programming computers or maintaining robotics. According to the BLS, the median annual wage for computer programmers in May 2018 was $84,280, or 246 percent of what cabinetmakers made. If they’re smart enough or skilled enough to program, why would they settle for so much less? In fact, even those with no computer-based aspirations and only a willingness to work with their hands still earn less in a woodshop than even an average construction job pays ($38,890 in 2017).
It seems fairly obvious that the first step in finding (and keeping) skilled workers is to take a long, hard look at wages. If we’re replacing people with machines so that shops can maintain production with fewer employees, does that create some room in the payroll budget?
What does skilled mean?
Defining this in the woodshop industry is a bit of a challenge. Does somebody who can work magic in a CAD program have more skill than someone who can spray a perfect topcoat? Who is more valuable to the company, or the bottom line? As tasks in the shop become more refined and exclusive, custom woodworking is seeing an evolution toward the production line model. That is, people are becoming less interchangeable throughout the process. There was a time when the shop owner would draw plans on paper, and then move to the table saw. As robotics and other aspects of Industry 4.0 are increasingly integrated, we’re seeing more specialists and fewer unskilled, or strictly manually skilled jobs.
Training is one defining characteristic of skill. Employees who have a two- or perhaps four-year degree in various aspects of computers such as CAD, CAM or robotics are a completely different entity than somebody who arrives at the shop with a great attitude and physical abilities but needs to be trained in the shop. A big component here is that on-the-job training is no longer limited to subjects such as wood movement or staining. Now the new employee may also need to become well versed in such diverse skills as lean manufacturing practices, interactive screens and labeling software. This, of course, introduces an argument about the merits of skills derived from in-house training verses those purchased through college degrees. And, does somebody who was trained elsewhere bring more new skills to the shop than preconceived notions that might need to be tweaked?
As with any industry, a successful, long-term, skilled woodworker has a very specific core makeup. This is a person with a fairly unique combination of both intellectual and manual attributes, but there’s also something less quantifiable here. A long-term, or indeed lifetime woodworker, must have some aspects of the soul of a craftsman. And herein lies one key, other than money, to attracting skilled labor. These are the kind of people who revel in building, making, and then running their hands over something that they have created. Beyond simple pride, it’s almost an addiction. Yes, they are quite willing to spend a day reducing big sheets to smaller ones. But they will do so only with the promise of something better and more creative tomorrow. Training, and the opportunity to grow and learn – these will attract skilled people, or people with the talent to acquire advanced skills – even more than money can.
So, where are the candidates?
Finding qualified applicants has a lot to do with how a woodshop defines ‘qualified’. Are you looking for people who already have some cabinetmaking skills and experience? If so, running an ad in the local newspaper might still be the best way to go.
Shops can also find good people through contacts made as members of trade organizations such as the Architectural Woodworking Institute, Cabinet Makers Association or Stairbuilders and Manufacturers Association. These groups have mechanisms in place that help shop owners and managers meet and talk with each other. In larger cities, a shop can often find a branch of a labor organization such as the United Brotherhood of Carpenters and Joiners that may have some viable candidates available.
Are you looking for people with CAD/CAM and operator training who know their way around a tablet and also have some industrial parts making or assembly skills? Then you may want to connect with local community colleges and universities. Many third-level schools in the hardwood belts (the Appalachians, New England, and several states along the Canadian border) or those associated with the furniture industry (the Carolinas, Georgia, Pennsylvania and California, for example) have strong wood programs that teach people traditional woodshop basics along with Industry 4.0 skills.
There are some private schools, both for-profit and non-profit, that teach short but intense courses in various aspects of woodworking, and these might be a fast track way to get somebody with an IT degree and no woodshop experience up to speed. These include the Center for Furniture Craftsmanship in Maine, William Ng School of Fine Woodworking in California, and the North Bennett Street School in Boston – all of which might have recent graduates who are looking for a job.
And conversely, there are ways to get a woodworker up to date on computer-related skills. Community colleges and universities, and even some CNC machine and software manufacturers, offer classes in CNC and related topics online. Offering to pay for a new employee’s continuing education is often a smart decision from both the woodworker’s and the woodshod’s point of view.
There’s a state-by-state listing of classes and schools at woodezine.com/education.
This article originally appeared in the July 2019 issue.
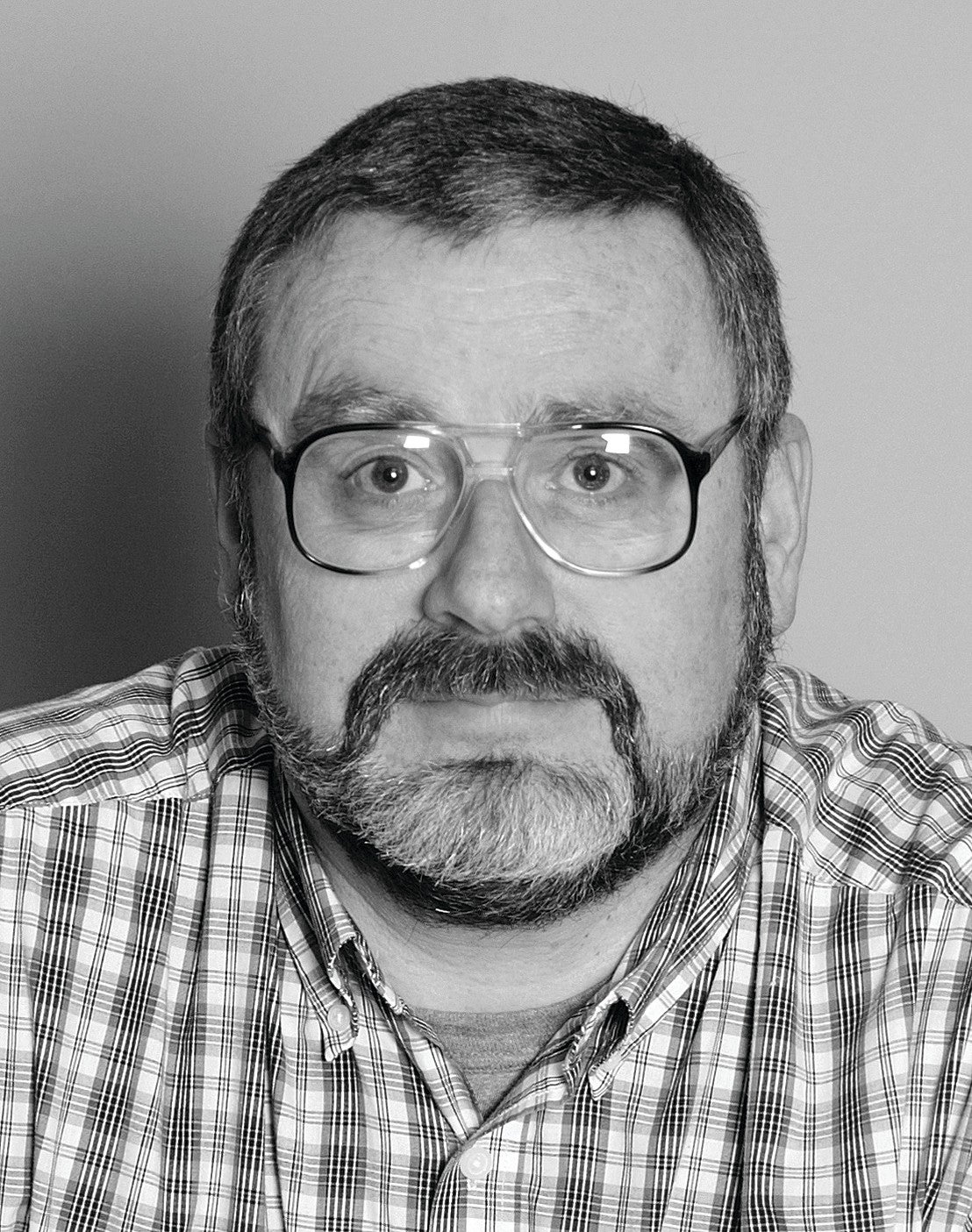