A new year invites change
Upgrading the shop can include improvements to technology, machinery, processes, and the working environment
This is a great time to think about shop upgrades. It is the beginning of a new tax year for most woodshops, and doing returns for the past year can help bring things into focus. Sometimes we’re so busy filling orders that we don’t have the luxury of stepping back to see where the numbers are falling. The new year is the best time to create a budget and see what’spossible.
With a budget in mind, it’s important to identify what needs to be upgraded, and to have a very clear picture of the return on investment for new purchases. It’s easy to be tempted by baubles. For example, a shop owner who has a perfectly functional CNC might wonder whether it’s time to trade up to something with a larger spindle, a vacuum table, and perhaps another axis or two. But rather than replacing the entire machine along with its dust collection, pneumatics, wiring and all kinds of ancillary jigs and fixtures, it might make more sense to simply upgrade the existing machine in small steps. That way, extensive downtime can be avoided, and the bottom line should be significantly lower.
When looking for potential upgrades, it helps to think about where the bottlenecks happen. If breaking down sheet stock is slowing production, then a second saw or router might help. But if everything only slows to a crawl as it goes through the spray booth, a new CNC may aggravate the problem by improving passthrough at the front end.
Another tell worth monitoring is lunchroom chatter. If employees are frustrated with a tool or machine and talk about it a lot, or worse yet try to bypass it and use other machines to do the same work, that’s a red flag and a potential candidate for an upgrade. A good example would be if the shop has two table saws, and one rarely gets used. It may be time to trade the second one in for a better model, or perhaps a different type of machine altogether such as a vertical panel saw.
Technology
The phones in our pockets have become an integral part of life as they systematically replace cameras, encyclopedias, calculators, maps, alarm clocks, fax machines, radios, planners, libraries, and more. They also give woodworkers a wide range of apps for tracking how machines are working, where power tools are located, what maintenance is required, each machine’s output, job progress, employee hours, and expenses.
There are apps to work out cut lists, optimize sheet goods, add photos and videos to bids or planning sessions, convert measurements and dimensions, calculate board feet, and even compare the density and construction qualities of various wood species. Apps for CRM (customer relations management) let a woodworker keep tabs of sales calls, bids and clients.
Power tool manufacturers have created apps to help woodworkers enhance the performance and battery life of their portable tools, and countless manufacturers have created specific apps to help woodshops find exactly the right machine tooling, bits, cutters, knives, screws, hardware and other catalog items for every task. It pays to keep up with the new apps, but it doesn’t always pay to download and start using them. The idea of an app is to save time. If it isn’t doing that, then it’s time to delete it.
Most apps are available on the Apple or Android sites, but we’reall aware that browsing through the options and trying out programs can become a little addictive. While most apps are more amusing than useful, there are definitely some that can upgrade a shop’s performance and help bring order to chaos.
Beyond phones, other technologies are worth noting when it comes to shop upgrades. Battery power is beginning to take some significant steps, expanding into much higher voltage solutions that are now powering what have so far been stationary machines such as juice-thirsty table saws and dust collectors. There’s no magic here, no new energy source. What’s happening is that the manufacturers are adding more features to the circuit boards in the tools, batteries and chargers so the cells run cooler, store more energy, and deliver higher torque. And a corresponding improvement in brushless motors has fueled some significant advances.
Machinery
The number one and least expensive upgrade in a woodshop is to sharpen or replace dull tools. Poor edges force woodworkers to push harder on parts, and that’s when accidents happen. They also produce burn and chatter, which eat into profits because of all the time it takes to sand or redo affected parts.
Another way to reduce rejects and avoid sanding is to keep the jointer well-tuned. This is especially important in shops that use solid wood more than sheet stock, because boards that aren’ttrue will slow down every subsequent process. Step one is to install sharp knives or rotate the carbide inserts. Step two is to lay a straightedge along the beds and see how well they line up. Almost every jointer in America has a little sag on one or both tables, and many slump enough to impact results. Even a tiny drop in an outfield table can cause a bowed cut. It’s also important to place the straightedge at both edges of the tables (against the fence, and then away), so that any side-to-side tilt is revealed. That can usually be fixed by adjustments on the trunnions or adding thin shims to the sagging corner.
Adding a sliding auxiliary table to a cabinet saw could be a great upgrade for a smaller shop. Several manufacturers make these, including Harvey (harveywoodworking.com), SawStop(sawstop.com) and Powermatic (powermatic.com) . This is a separate but attached table, rather than just a table saw sled. Unlike a sled, the slider stays in place all the time and it improves processing speeds and accuracy, reduces set-ups, and adds another level of safety. That’s especially true if the add-on is large enough to handle whole sheets. Woodsmith has published plans (woodsmithplans.com) for building a slider for small shops.
Some cabinet saws have enough room in the body for a larger motor, which might allow the shop to upgrade to 3-phase without having to replace the whole saw and all its jigs. The trunnions may need to be evaluated if the new motor is significantly heavier, but other than that this can be a relatively inexpensive upgrade if the shop already has a phase converter, or there’s 3-phase in the building. The extra power produces cleaner cuts, less burn, a lower chance of kickback, and perhaps even a lower electric bill.
Beyond the table saw, is it time to add 3-phase machines throughout the shop? More torque means fewer passes, and a shop can get a lot more 3-phase machine for the same price as a comparable single-phase unit. Plus, those big old iron dinosaurs usually have plenty of tabletop and mass, which makes it easier to move parts and reduces vibration.
Doubling up machines might be an upgrade option, too. For example, selling a small jointer and planer and buying a larger combination machine may give the shop wider cut capacity andreclaim some floor space.
For shops with new employees or tired veterans, a saw with one of the new safety shutdowns might be worth considering. This may look like a big investment, but it pales when compared to the cost of a few fingers. Beyond SawStop, several of the large machine manufacturers are offering new saws with reaction technology, including the Hand Guard from Altendorf(altendorfgroup.com), PCS from Felder Group (felder-group.com), and Blade Off from SCM Group (scmgroup.com).The advantage here is that all four manufacturers build very high-quality saws, so the woodshop can gain a number of other advantages beyond enhanced safety. Cut quality, material handling capacity, and various degrees of automation are possibilities.
Adding a CNC can be a huge upgrade for a small shop, but it is important to think long and hard about what the woodworker wants to make before taking the leap. CNCs are getting quite specialized, and there are models out there that come with all kinds of advantages such as a rotary axis, or perhaps more room to work on tall and thick parts (higher Z), or adaptability that opens the door to lasers, scoring knives, sign-making and more. Some CNCs are portable and can be hauled to a jobsite and set up in minutes. Other portable units are almost manual, and as the woodworker guides them, they automatically make small corrections to maintain a toolpath. Many shops only need a CNC to make doors or panels, so they may want to look at benchtop units rather than full-sheet processors. And that works the other way, too. A benchtop CNC probably won’t work well for a case goods manufacturer.
For shops wondering if they’re outgrowing their full-sheet CNC and thinking of the advantages of a 5-axis, an aggregate head could be a much less expensive option. The payback could be months, rather than years.
Sharpening is the easiest upgrade, but there’s not much point in sharpening tools that won’t hold an edge. So, a close second here is to upgrade the bits, blades, knives and cutters in the shop to the best that the budget will support. Diamonds are the most expensive tools, but surprisingly they may not be a bigger upgrade than some high-quality carbide solutions because tungsten can hold a finer edge. Insert tooling rather than solid carbide bits can be less expensive over time, but that’s a call that needs to be made on a job-by-job basis.
Processes
Anything that reduces sanding is a good idea. Better and sharper tools can make a big difference, but so can some basic shoptechniques. The simplest of these is to make the last pass a light cut to avoid burn or chatter. Slowing down a bit on that final pass can also help (but not too much!). A pocketful of new router bit pilot guide bearings is an inexpensive shop upgrade that can pay immediate dividends. It’s surprising how many bearings are loose, worn, off-center, damaged, or coated in gummy resin or some other forgotten residue. Many are not truly sealed and wood dust fines can work their way into the voids. That makes bearings stick or heat up.
Another inexpensive upgrade is to add battery-powered laser guides to older miter saws, drill presses and other tools that didn’t come with them. The added accuracy is akin to the way that marking knives can leave a better line than a pencil. These cheap little lasers can be temperamental and annoying to set up, but once in place they can speed up processes and reduce rejects. They also make it a lot easier to sneak up to the cutline.
One of the most impactful upgrades for most shops is adding a track system to the finishing booth. This allows a woodworker to hang parts, gain access to both faces simultaneously, and move work through the booth smoothly without having to touch it. PaintLine (paintline.com), Sprayfish (sprayfishinc.com),Fast Rack (fastrackequipment.com), and the PivotPoint and PivotLine systems from Guffey Systems (guffeysystems.com) all offer multiple solutions that cater to small and medium sized woodshops.
Loading and unloading processes are another area where shops can upgrade without breaking the budget. Carts that can be raised and lowered with a footswitch, crank, or electronic sensors will make a huge difference moving sheet goods. Another solution is a vacuum lift on wheels that picks up a sheet and lets the operator wheel it to the machine and drop it in place. Robot arms are also becoming less expensive, although units that can lift a full sheet are still quite an investment.
And labeling is a huge help here, where parts can be sorted and stacked according to when they will be used, and in the correct orientation. Upgrading to labeling can be as simple as a rubber stamp or printing labels in the office, or it can be fully automated and is often an add-on option for older CNCs.
Environment
Both wood products and employees will appreciate a shop owner who adds a dehumidifier. Humidity can cause material dimensions to change, and employees to tire. It can also rust every ferrous surface. If the shop doesn’t have air conditioning, a few dehumidifiers and fans can transform the workspace on a budget. Fans alone won’t work – they just move the moisture.
If you’re a cabinetmaker, storage is what you do. Which means you can transfer that set of skills to the workshop to store parts closer to benches, build specialized carts for parts such as drawer sides and slides, or just make routines more efficient by creating custom storage for every tool so there’s no more rummaging through the benchtop or buckets. The same skills can be applied to organizing plywood cut-offs and short boards. For ideas, spend a lunch hour on YouTube.
MDF slatwall is surprisingly inexpensive and it can be used on every bare wall and vertical surface in the shop, including the exteriors of storage cabinets and the sides of workbenches. There are countless hardware and hanger options for this store-fixture system that let the woodworker hang everything from saw blades to miter gauges in plain sight, and up off the workbench.
A very inexpensive shop upgrade is to suspend extension cords and pneumatic hoses from the ceiling. Simple cup hooks might work, or garage bicycle hooks. The advantage beyond removing a tripping hazard is that this makes it easy to drop cords and hoses right where they’re needed, rather than chasing them across the shop floor.
LEDs now offer countless ways for a woodworker to upgrade lighting, and subsequently the quality of work. LEDs are inexpensive both to buy and run, don’t get too hot, and come in so many shapes and sizes that they can be placed just about anywhere. In addition to improving both general and task lighting, they can also be tuned for color, so they deliver warm yellow or bright white light as needed. They can replicate the color of the light where the cabinets or furniture will be installed, so they offer a preview of the finish.
Better filter bags can be a huge upgrade for a shop’s dust collection system. The micron size in the weave can allow more volume or velocity, as can larger bags. This is an area where professional advice can really pay off, so it’s worth chatting with a filter bag manufacturer. Automated blast gates (or even manual ones) can greatly improve the efficiency of a dust collection system and do so at a relatively low cost. Even a one-man shop can benefit from gates that open and close as various machines are used or turned off.
For shops with concrete floors, an anti-fatigue floor can be a sensible upgrade. Horse stall mats are a wonderful solution as they’re heavy and durable, but they’re also expensive. Better Life Technology offers some other options at bltllc.com.
During all these improvements, it’s important to be aware of the domino effect. Upgrade this and you may have to upgrade that, so it’s a good idea to treat the process as much as another project management task. One could put it on a spreadsheet, create a schedule, design some evaluation tools, and figure out ways to measure success. Rather than having a staff meeting right away to garner opinion, it might be more profitable to speak quietly to key players and create a roadmap before inviting comments from the entire team. Or not. Each shop has its own culture, and that’s something you probably don’t want to upgrade.
Originally published in the December 2024 issue of Woodshop News.
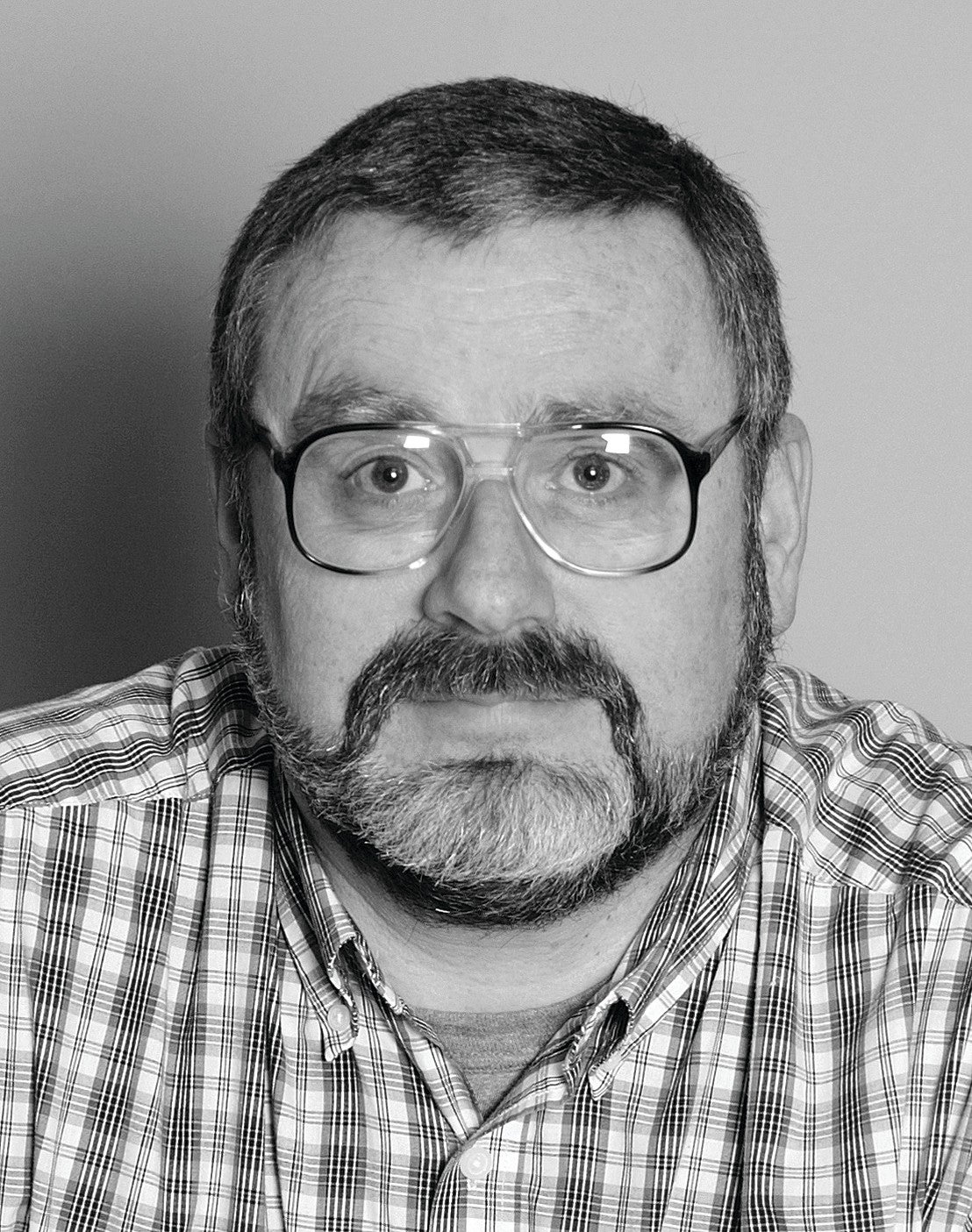