Adding axes
The decision to upgrade to a 4- or 5-axis CNC starts with answering a fundamental question.
What do you want to do with your CNC?
That’s the core question when considering an upgrade to more axes. Going to a 5-axis machine won’t necessarily speed up production, although it can. If the shop just needs to make more flat doors and boxes, or make them faster, adding another 3-axis machine might actually make more sense. If, on the other hand, a shop needs to increase accuracy, versatility, and the ability to machine complex shapes, then an upgrade may be the answer.
There’s a perception in the industry that 4- and 5-axis machines are only necessary for carving, sculpting and shaping, but that’s no longer true. Software has made those limits obsolete. But before we get into the capabilities of added axes, let’s lay a little groundwork.
Understanding axes
A standard 3-axis machine will operate in three directions: X (left-right), Y (back-forward) and Z (up-down). Despite that, it’s essentially only capable of creating parts in 2D, and that’s the first confusing issue for new CNC owners. The parts aren’t two-dimensional, but the machine’s movement is. A cabinet door obviously has three dimensions – width, length and thickness. But a 3-axis CNC cuts from above, so it can only move in two planes. Travel in X and Y is all on one lateral plane, and Z is in a second, vertical dimension.
Even though it’s limited to vertical and horizontal travel, and is itself locked in a vertical orientation, the spindle on a 3-axis machine can handle an amazing number of tasks. Depending on the tooling (cutters), it can move sideways into a part and then travel up and down to cut recesses such as biscuit hardware slots or mortises. It can even undercut cantilevered parts, and when an aggregate head is added, it can work at angles between zero and 90. Those kinds of operations can involve quite a bit of set-up time and some imaginative fixturing (clamping). The alternative is to mill all the parts in standard 2D, and then rotate them and mill a second face. Unfortunately, accuracy becomes an issue when parts are moved and re-set. Even a tiny bit of residual dust or a rough surface, burr, or uneven face can throw off alignments.
That’s where a fourth axis (called the A-axis, which rotates around the X) can come in handy. It rotates parts, most often doing so slowly to position a new face for routing, but sometimes quickly to address the part to a cutter, where the A-axis can replicate the action of a wood lathe. So, a 4-axis CNC can make 3D parts easier than a 3-axis machine, and can do so with less set-up, fewer tool changes, and often without an aggregate head.
When used to position a part, the 4-axis CNC can save a lot of time and money on fixturing, as the part only needs to be locked in place once for multiple processes. It also cuts down on rework and rejects, as the repositioning is mechanical so it’s very precise. It allows no possibility of human error or debris throwing off the alignment. A fourth axis also lets a router create more complex curves than a 3-axis machine, as the part can revolve while the cutter travels along its length. Think cabriole (Queen Anne) legs here, or spiral (helix, or helical) shapes. But the most practical uses for an A-axis are simply to rotate parts so they can be milled for assembly hardware pockets, recessed for decorative hardware such as lock bores or cabinet connectors, or spun between centers to make round parts such as balusters, spindles, and newel posts.
A 5-axis CNC is even more precise, and although it sounds quite complex, it’s really just an extension of the fourth axis concept. The fifth axis rotates either around an imaginary line on the Y (where it is called a B-axis), or else around the Z (which makes it a C-axis). Those rotations can be achieved by either rotating the part or the spindle. So, in the case of a baluster, the wood can spin, or the wood can be stationary, and the router travels around it, or both can move simultaneously.
With all those action choices available, a 5-axis machine can mill, shape or form any face of an object except one – the facet that is used to secure the part. Well, except for parts between centers, where there are two unavailable faces (usually the ends of a wooden turning).
This versatility makes it ideal for creating decorative furniture elements and complex wooden parts for jobs such as, say, RV or boat consoles and controls, or perhaps intricately carved corbels. A 5-axis CNC can cut anywhere in the 360 degrees around a part, while also moving up and down as it travels – and the part can be moving, too.
In the simplest terms, a 3-axis machine is an excellent choice for relief carving, while a 5-axis CNC is the best option for 3D sculpture, and a 4-axis machine is a good choice for making rotational parts such as spindles, finials and the like. These descriptors suggest possible usage: they don’t define the capabilities or limits of each type of machine, because a little inspired fixturing can change all the rules.
What’s to gain by upgrading?
A 5-axis CNC is not just more expensive, but generally it will have a larger footprint and require more infrastructure requirements such as 3-phase power, dust collection, compressed air, and vacuum draw. However, it will also reduce set-ups and production steps, so there can be a substantial saving in the time used to process parts. The more complex the part, the truer this becomes.
Five-axis spindles are generally heftier than 3-axis versions, and because of enhanced versatility and reach, the larger machine can remove more waste and reveal more of the final shape in a shorter period of time. It can also work in an equalized mode for parts that are not balanced for weight, removing waste in a synchronized sequence that helps to support the safety and rigidity of the fixturing.
Shops that move up to a 5-axis CNC tend to discover that they use far fewer fixturing and clamping jigs. Shop time to design/build and test new jigs is rarely required with a 5-axis machine, as the tools can reach into so many previously unreachable areas.
Because of its high degree of precision, parts made on a 5-axis CNC generally require less sanding and post-processing handwork or further machining. And its agility can move a woodshop into production choices that were once out of reach. It can do things that 3-axis machines simply can’t negotiate, so it may open the door to new markets, new clients, new products, and new processes.
As with all high-level technologies, input is critical. Owning the machine means nothing if the woodshop’s design and operating personnel don’t understand how to take advantage of its advanced features. Training the existing staff, or hiring somebody who understands the technology and its possibilities, is part of the package. There’s no point in buying a sports car if you never learned how to drive.
Is there a downside?
The machine isn’t the only thing that’s more expensive. So are the accessories, installation, operating cost, staffing, and software. The code can be more complex and harder to grasp, too, so most operators find themselves relying more on the software to self-proof, rather than on their own experience and knowledge. In some situations, more machine means a bigger chance of collision. On the other hand, the fact that the machine is doing due diligence and handling the more complex simulation data means that overall, 5-axis machines are becoming easier to operate.
There is the option of adding two axes to an existing 3-axis machine, and performing what the industry calls 3+2 machining. It’s not quite the same as true simultaneous 5-axis machining, but it’s close. The additional axes can take the form of rotating tables or trunnions that can both tilt and rotate, so that new facets of the part can be presented to the vertical spindle on a 3-axis CNC. The two new axes aren’t necessarily operational: they are used to position the part and then lock it in place for 3-axis machining. The 3+2 option lets the operator access all parts of a workpiece except the face being held. It reduces set-up times and the number of positional changes and jigs. It also allows the spindle to operate with shorter tools, which can reduce run-out and vibration to deliver a cleaner cut.
On the other hand, a 5-axis CNC can maintain continuous contact between the tool and workpiece by simultaneously moving the part as well as the tool. And it, too, can use shorter tool lengths for greater accuracy.
So, while they require a higher investment and usually cost more to operate, 5-axis machines can be faster, more accurate, and a whole lot more versatile than a 3- or 4-axis machine. Plus, a new machine will probably have faster travel times and tool changes, and perhaps better vacuum holding and dust collection, too. There’s even the possibility of saving on materials, as the acrobatics of a 5-axis machine may need a smaller blank to start with, and in some cases may be able to save material that might otherwise have been turned into sawdust.
Shopping for a new machine might be a good time to think about table sizes other than 4x8 or 5x10. Many manufacturers can build a custom-sized table and provide customized vacuum sectioning. For woodshops that supply components to another industry such as aerospace, marine, or audio-visual manufacturers, parts don’t always fit the traditional nesting dimensions. Depending on optimization, another few inches in one or both directions might save a lot of material over the years.
Again, it all boils down to that initial question: what will you ask your particular CNC to do?
Milling for numbers
A 5-axis machine combines the ability of the spindle to move in three directions with the option of rotating in two planes. A CNC isn’t limited to just five axes: there are metalworking machines that have as many as 12. But five axes is enough to mill virtually any shape in wood. And because of the agility those multiple approaches deliver, tools are constantly addressing material at different angles, depths and speeds. That variance means that the tools wear differently than those in a standard 3-axis machine, and they tend to retain their edge longer. The constant tilting of the tool or the table means that there are fewer tool changes, so there’s less downtime changing them and less cost in renewing or replacing them.
That is one part of the essential equation to consider when upgrading to a 4- or 5-axis machine. One needs to discover the optimum relationship between cost, time and quality. If the parts that a woodshop needs to make can be completed on either a 3-axis CNC with lots of fixturing, on a 4-axis machine with less human involvement, or on a 5-axis with virtually no set-up beyond the original clamping, then each of those processes needs to be subjected to cost-benefit analysis. The only true way to extract meaningful values is to physically run the parts on each of the three machines, and record time and material costs for each, along with overhead.
The CNC manufacturer or sales agency will most probably comply with such a request, as most of the larger suppliers have active models available, or they can access machines in operation at clients’ shops.
Batch sampling will be far more accurate than running a single piece. The woodshop could bring several parts in differing dimensions and complexity to the test, all the while acknowledging that even a large sample doesn’t replicate the norms in a day-to-day high production environment.
For more precise data, all aspects of the process should be recorded, from time spent designing and programing toolpaths to loading the CAM software, prepping and fixturing the part, milling, unloading, and post-machining. After the run, the quality of cuts and surfaces needs to be compared, and the time involved in taking down the set-up and restoring the machine for its next task is also a factor. The more aspects of each process that are timed and cost evaluated, the more accurate the picture will be. It’s impractical to achieve a complete comparison, but it’s imperative to get as close as possible, within reason. Even tangential factors can be weighed, such as the reduced time required to sand parts that are machined with cleaner surfaces, and the unrelated tasks that can be performed by employees who currently tend to the existing 3-axis machine, but will have extra time available with the new machine because of fewer tool changes, less fixturing, and so on.
This is also an ideal time to factor in further automation such as loading, placement, and unloading options that the shop has not yet put in place on the existing machine.
If the woodshop is making relatively simple parts, it will quickly become obvious if the 3-axis machine holds an investment cost advantage, and maybe even an operational one, too. However, as more and more parts are made and repositioning/fixturing becomes a cumulative activity, the chances of errors and inaccuracy increase, and the amount of downtime may become a bigger factor.
These are aspects that won’t become obvious in a limited test but will emerge in longer runs. So, it’s a good idea to also visit shops that have recently upgraded and talk things over with both the owners and the machine operators. Upgrading is a big decision with large numbers and heavy impacts on a business, and it’s worth taking every small step possible to paint a complete picture of exactly what is involved. Finding woodshops that have already walked down this road can be a matter of contacting fellow members of business or trade associations or asking machine suppliers for direct access to some of their existing clients.
Choosing a shop outside one’s own immediate geographical market is advisable: the close competition may be a little reluctant to reveal all aspects of their experience. The large trade shows are good places to start the quest for upgrade info, as are online forums. One can also visit the Resource Guide at woodshopnews.com and search under CNC Equipment & Services.
If a woodshop currently owns a specific brand of 3-axis machine and the operators are comfortable with its controls, mechanics and software, it might be worth checking to see what 4- and 5-axis options that manufacturer offers even if the prices are a bit higher than some new competitors’ offerings. The existing brand familiarity might shorten the learning curve on a new machine, and the shop’s personnel may already have established relationships with tool suppliers, spindle maintenance providers, and tech support options that can transfer to a new machine.
This article was originally published in the February 2024 issue.
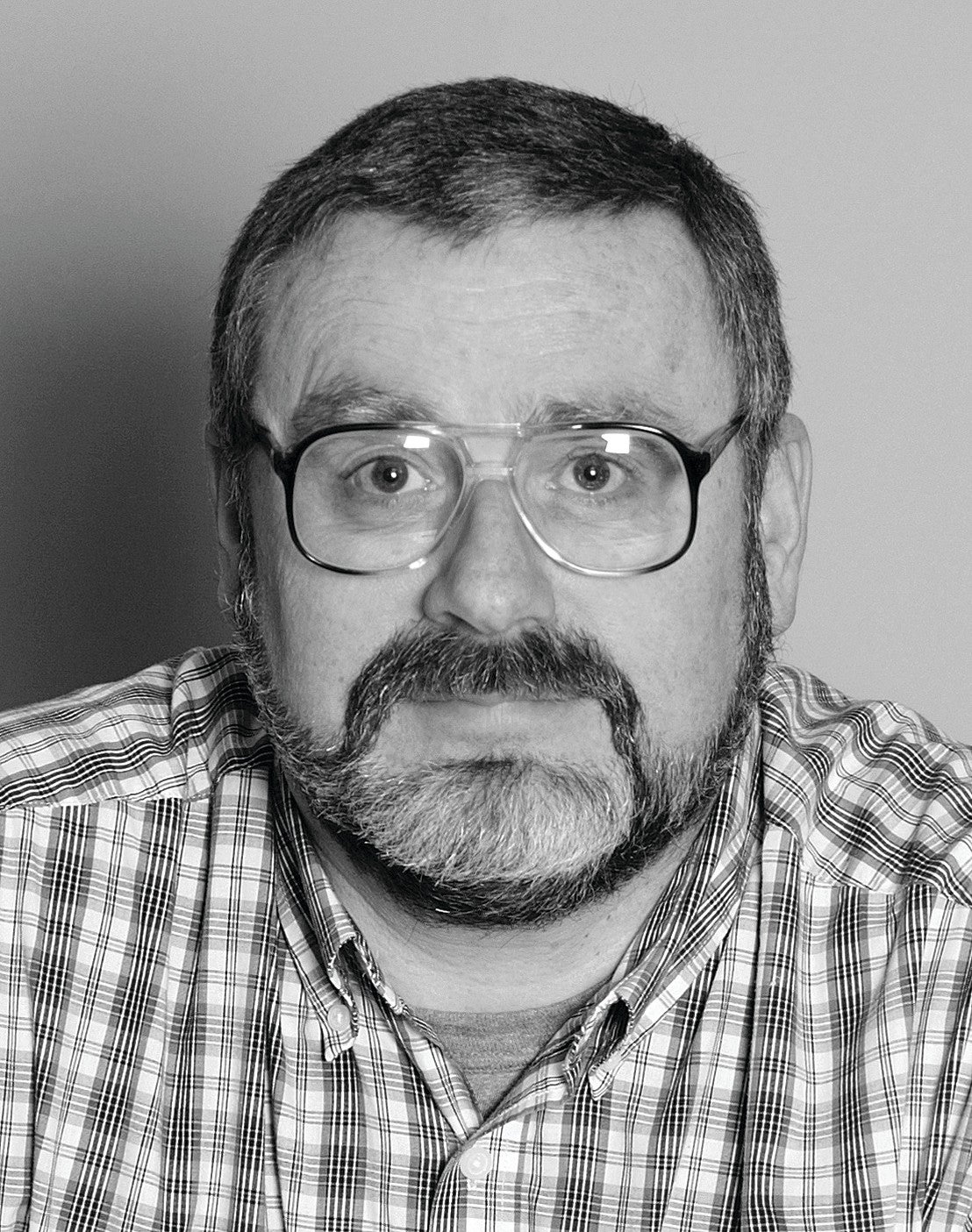