Leading the charge
Portable power tool innovation continues with better batteries, brushless motors and improved ergonomics
When it comes to portable power, everything is going cordless – from simple screwdrivers to high-tech table saws. It’s happening because advances in Lithium-ion storage cells have occurred in conjunction with a move to brushless motors.
Smaller and more powerful batteries, smaller and more efficient motors, better ergonomics, LEDs, and faster recharging have delivered an avalanche of new tools over the past few years. Most of the major manufacturers now advertise product lines that include hundreds of tools that all use the same battery. A few are branching into new voltages (40 and 60) as the portable tools they make are getting bigger, and some tools use flexible voltage batteries that supply different levels of power depending on demand. The Amp hour (Ah) ratings are getting a lot higher, too. A single Amp hour is the amount of energy in a battery that lets one Ampere of current flow for one full hour. Most tool batteries are rated between 2 and 12 Ah, but that’s moving up fast.
Another trend in power tools is based on the emergence of phone apps. Several major manufacturers now offer devices that can be attached to a tool, along with a corresponding app that will trace the tool’s past and present locations, usage, and even its battery charge level. This makes it easier for a shop manager to find tools in various toolboxes, jobsites, work trucks and modular storage systems, and it also makes sure an installer or builder has exactly what they need. Some apps also let the shop customize tools to pre-defined settings such as controlling torque and speed, so when the new guy uses a driver for the first time, the screws don’t get stripped.
Battery basics
Lithium-ion is the chemistry that is driving most portable power tool innovation. Lithium (Li) is found in Group 1 on the periodic table, in the alkali metals. In its ionized form, it is used to build batteries for everything from cellphones to electric cars.
A battery is either a single cell that usually takes the form of a small cylinder (the least expensive shape to build), or more often it’s a group of cells that are all connected in series. They become a battery when they’re popped into a housing with a circuit board, which controls the top and bottom end of the charge and discharge. Each of the individual cells has a cathode (positive end) separated from an anode (negative end) by a liquid called electrolyte, and there’s a little metal cap at each end of the battery that is an electrical terminal (one positive and one negative). Juice runs from the anode to the cathode when you pull a drill’s trigger, and from the cathode to the anode when you plug the battery into a charger. That movement is current. What’s happening when the drill is running is that lithium atoms in the anode are being ionized, which means they are being separated from their electrons. Ionizing is radiation that has so much energy it can pull the electrons out of atoms.
The Public Health Department in Los Angeles says: “While any exposure to ionizing radiation can be potentially dangerous, it’s believed that the body is able to successfully defend itself against and repair the damaging effects of low-level exposures.” The levels in power tool batteries are extremely low and at this time don’t seem to be regarded by anyone as a health hazard. But batteries are getting bigger.
So, every time a trigger is pressed there’s a stream of positive ions and negative electrons being formed. Ions are miniscule chunks of an element (in this case, lithium) that are either positively or negatively charged; they can’t exist in a neutral state. A positive ion is a ‘cation’ and a negative one is an ‘anion’, and that’s where we get the names cathode and anode.
Lithium is the lightest of all metals and it has become the element of choice for batteries because it charges faster, lasts longer and delivers more power in a smaller package (because of its light weight) than any other known element. It also has no ‘memory’, so there’s no need to fully discharge the cells before recharging, or to schedule regular charging.
The largest looming problem with Lithium-ion technology is that the batteries eventually age and inevitably fail. To delay that, new chemical combinations are constantly being introduced that continue to shrink the overall physical size while steadily increasing the amount of power. (In the woodshop, the best way to make them last longer is to store them at about 60 degrees Fahrenheit with a 40 precent charge.)
The future of cordless tools might be something called a fluoride battery. So far that option is proving elusive because, even though it can last many times longer than lithium, fluoride is an anion (a negatively charged ion) and currently there’s a problem with stabilizing it. Other potential solutions are sodium, magnesium, and ammonia, but these are all decades away from being commercially viable.
Currently, most of our lithium comes from Australia or salt deserts (called ‘salars’) in several countries in South America. In the latter, drilled wells and natural conduits bring up salt water from underground lakes. The water contains lithium, so it is poured across the desert into huge basins and evaporated, then harvested. It’s a finite resource, and with the switch to electric cars, there are concerns about dwindling supplies.
Brushless motors
Rotary motors do one simple thing. They cause an electrical current to make one part rotate inside another. Remember playing with magnets as a kid? Turn one end-for-end and it either attracts or repels the other magnet. Basically, that’s what makes a motor spin. It turns electrical energy into mechanical energy.
The big difference between the older brushed motors and the new generation of brushless motors is that the former is comprised of three parts that are mechanically driven, and the latter has just two parts that are electronically controlled. And because there are fewer parts, a brushless motor can be smaller. They also avoid physical friction, so they are more efficient, run cooler and quieter, and are quicker at starting and stopping.
The smaller size of brushless motors means they give up a little bit of torque, but it’s not enough to cause a problem. Brushless motors are also a little more expensive to produce, but they have much better and more precise speed control. And they’re also better suited to long days at work because, beyond their smaller size and lighter weight, the lack of physical contact with brushes and the resulting lack of friction means they don’t build up heat.
Improving ergonomics
Ergonomics is essentially the study of how people physically fit and move in their working environment. As the decades roll by, we continually accumulate more and better information about how the human body and brain can best make it through a 40-hour week. In the shop, that can include considerations such as bench heights, adequate lighting, or even the placement of controls on a CNC. It also covers how we hold and use portable power tools. The challenge is this: Not all human bodies are alike, so how do you design a one-space-fits-all workshop?
Among the ergonomic innovations to watch for when buying new tools are subtle changes such as smaller tools with bigger handles. The grips on tools have changed a lot lately, making them equally comfortable for larger male hands and smaller female hands as the workplace evolves. People are getting bigger, and more women are working on shop floors. Larger outsourcing suppliers employ a lot more women than smaller woodshops, but that, too, is changing. And the tool manufacturers are taking note.
LED lights are an ergonomic advance as they make it easier to use the tools to do the job.
Customized tool storage continues to improve with units that have more compartments, better linings, and easier mechanisms to let them lock together on a two-wheeled cart. Self-propelled carts are in the works, as is charge-as-you-go, so that a service person will always have fully charged batteries when they arrive at a jobsite. Storage modules are also getting more secure, with built-in locking and tracking devices. The very concept of offering several small, lightweight units that lock together into a large and portable whole is ergonomical.
As for further innovation, we’re going to see new ways to cordlessly charge batteries over the next few years. These are already popular as a way of charging the small Lithium-ion batteries in cellphones and tablets, and they will soon be more widely available for charging tool batteries. Another concept is to charge a large battery in the shop, which is used to charge smaller tool batteries at the jobsite.
The future looks good for woodworkers. Lithium-ion cells are getting bigger, and the batteries are getting larger and more efficient. Soon, there will be no tool that doesn’t have a cordless option. That means some machines that were traditionally stationary are soon going to be portable, such as dust collectors, lathes and shapers. We’ve already seen several manufacturers introduce portable CNCs such as the Shaper Origin, Goliath and Yeti. We’re going to see huge strides in that area over the next decade, where portable CNCs become as common on the jobsite as they are in the woodshop.
This article was originally published in the November 2022 issue.
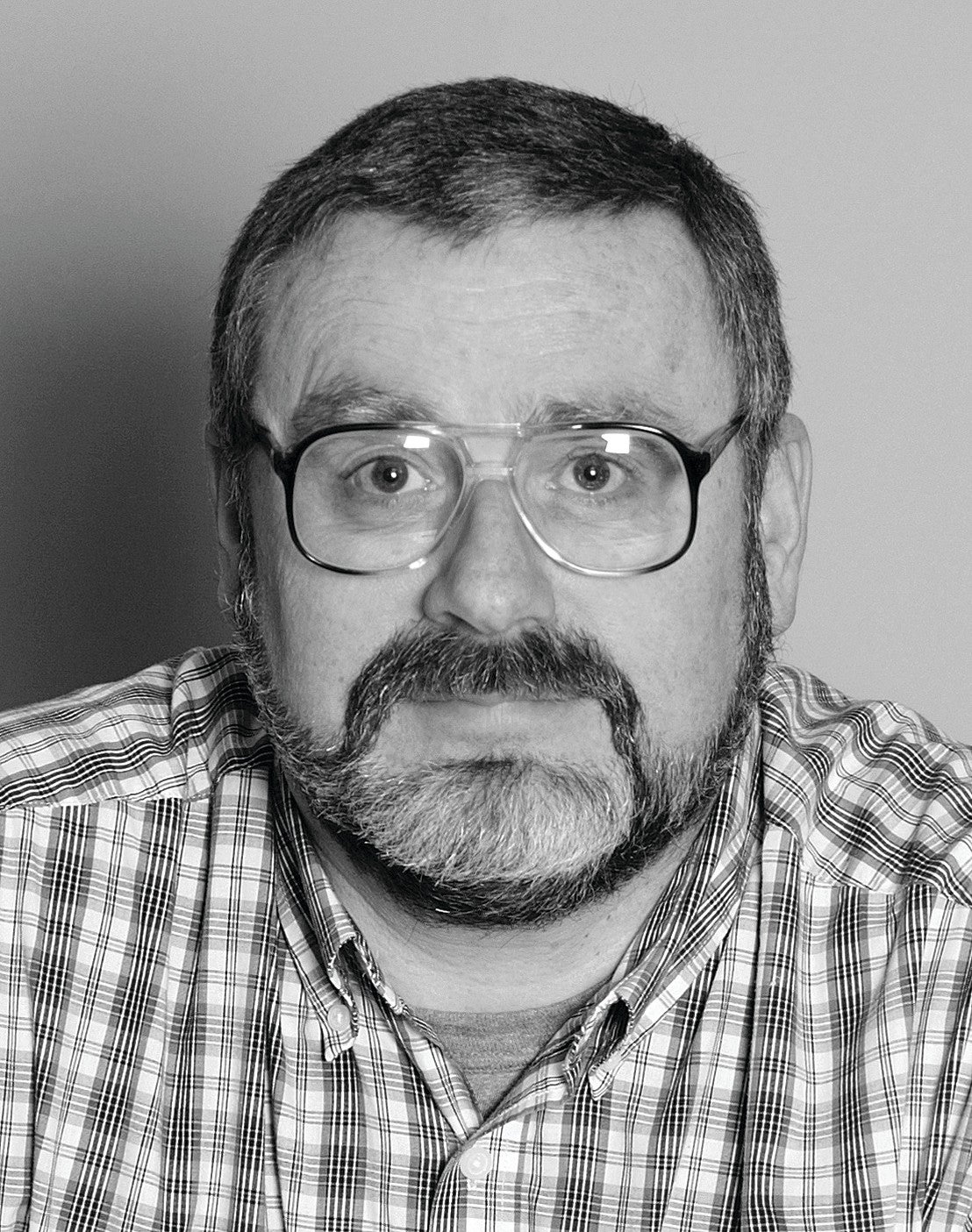