Thirty-some years ago, being broke but ambitious, I bought a used Craftsman table saw and started a small woodshop. Before the saw was even plugged in, the fence was replaced with a far better aftermarket upgrade that cost more than the machine. We were gifted a Forrest blade, and the shop was up and running. Over the years it graduated through cabinet saws and sliders, but that old Craftsman still holds some special memories.
We kept the core and added better.
The leap from router tables and cabinet saws to CNCs can be a little daunting, but it’s a similar routine. A smaller woodshop can start with a basic machine and allow it to evolve as budgets allow. The important thing to keep in mind is that the choice of machine should be firmly rooted in the shop’s needs, rather than being influenced by technical bells and whistles. The buying process involves a little introspection and soul-searching, and it’s not always based solely on cold, hard facts.
Some questions to ask
“Should the first CNC be new or used?”
There are arguments either way, the most obvious being that a used machine costs less. But a new machine usually comes with the latest software and controller, a factory warranty, free phone and/or online support, and no worn-out parts. On the other hand, the price of a used machine might include the other shop’s fixturing and clamps, dust collection add-ons, feed and offloading tables, and so on. There’s no rule of thumb other than this: what does your gut says.
The decision will be a lot easier if the used machine is a respected brand, or the seller is someone familiar and trusted. It also helps that nowadays a woodworker can visit online chats and discover a great deal about other shops’ experiences with specific machines.
“Can the CNC grow as the shop does?”
Entry-level CNCs are often targeted at skilled (or well-heeled) amateurs who want to play with the technology and learn new skills. But a small professional shop needs the machine to pay its way. It needs to be big and robust enough to complete daily tasks such as milling stiles and rails, flattening floating panels, or completing other production-line tasks when needed. Most shops are looking at a first CNC to increase output without adding payroll. If it does that, then the shop will experience some growth. Can the new machine keep pace with that? There’s not much point in investing in a CNC that can only turn out as much work as the traditional machines are already handling.
“What are the critical parameters?”
A work envelope describes the cubic area of the maximum sized part that a machine can process. The length and width of the table are going to be the most pivotal dimensions here for smaller shops. For example, a very small CNC won’t be able to process panels for wide drawers or pantry cabinets. The work area needs to be bigger than anything the shop intends to machine. There are some workarounds, such as splitting large panels and using a muntin, but such compromises will only satisfy for a while. At some point, frustration will set in. The best advice here is to buy a large enough table, and one that can handle thick parts. The travel in Z (up and down) isn’t always as grand as the specs say because it can be compromised if the shop needs to use longer bits or spindle attachments such as a dust diverter or an aggregate.
Think about pendulum processing. This is a term that describes a series of actions where one group of parts is being unloaded while others are being machined or loaded. It can happen effectively if the table is large enough and the automation is advanced enough (or the woodworker is agile enough!).
With robotics becoming more widespread and affordable, pendulum processing is a concept to be considered – maybe nottoday, but down the road a little. If it seems viable soon, that may affect how large a CNC table the smaller shop should buy now.
Precision is crucial. Rework and rejects are very costly, in both time and materials. If the gantry or frame is underbuilt on a desktop or small floor model CNC, it might bow a little under stress. If the spindle is underpowered, the tool can bog down as it leans into the work and cause chatter, or even deviate from the toolpath. Overbuilt is best.
How many axes?
Agility is a prime concern. Does the shop need 2, 2.5, 3, 4 or 5 axes? Almost every new CNC sold to small cabinet shops has 3 axes, and many of those can also handle an aggregate head. A 2.5 axis machine is actually a 3-axis model that can only move in two axes simultaneously. It works well for drilling and many simple milling tasks. A fourth axis rotates work around one of the three main axes, X, Y and Z. In the X plane (side to side) the fourth axis, called A, acts much like a lathe at high speed, but it can also rotate work very slowly such as just a quarter turn so that a different face can be milled. Rotation in the Y plane (back and forth) is called the B axis, and it’s similar to A. The C axis rotates in the Z plane (around the up and down axis).
How many axes a CNC needs to have in a small shop depends on the type of work being done. The more unique, shaped, and intricate the work, the more axes come into play. If the shop only builds casework with traditional flat rectangular doors, where the most intricate shape is a simple cathedral arch, then three axes will most likely be enough. If there’s an occasional need to execute a complex, multi-faceted part, it may be less expensive to outsource that than to upgrade from 3 to 5 axes.
A 5-axis machine cuts down on set-up time. It allows the spindle to do different operations with different tools without changing the fixturing. Clamp the work once, and then work on it from the top and all sides (except the bottom). A 3-axis machine often requires that the part be moved to reveal a new face after each machining task, and that can lead to inaccuracy. The more times a workpiece is handled, the more likely something such as dust accumulation or operator error can affect realignment.
Some CNCs offer the option of adding a second spindle and while that’s probably not a budget option for most small shops just entering the field, it might be an upgrade to be considered in the future, and that can be planned for now. Two tables rather than (or as well as) two spindles is also an option with some CNCs, and this can increase the volume and size of parts that can be machined. Some dual tables can be locked together so that very large object such as live edge tabletops can be processed.
The ability to add aggregate heads can transform the agility of a 3-axis machine because the spindle is no longer just pointing straight down. An aggregate can work at any angle up to 90degrees, so it can do things such as slot the edges of mitered cuts or chamfer at angles other than 45 degrees. Aggregates can hold drills, milling tools, saws, texturing brushes, sanders and a host of other tools, but they extend the point of contact farther from the gantry so there is more stress and a higher degree of lateral torque at the spindle. Slower speeds and smaller tools can help, but there are limits. Ask before buying.
Controlling costs
Running a successful business is as much about reducing costsas it is making sales. In a smaller woodshop, the margin for allowable waste is very slim. So, it may be important to invest more funding initially in the table and spindle, rather than to spend the budget on convenience upgrades. A heavier duty T-slot or vacuum table with bigger X, Y and Z capabilities and a larger, continuous duty spindle may well contribute more to the bottom line than immediately upgrading the cooling system, the speed of the travel motors, adding a chip conveyor, spending more on a fancier automatic tool changer (ATC), or automating infeed and outfeed operations. All of those upgrades can be added as needed, but the core strengths of the machine are the table, gantry and spindle. If these are undersized, add-ons won’thelp much. The idea here is to put your money where it will deliver the biggest ROI (return on investment).
On the other hand, tool changers aren’t just convenient. They can pay for themselves because they reduce the number of set-ups, which cuts downtime. But it’s easy to overdo. Adding a 24-tool changer to a shop that just does short kitchen runs is probably a waste of resources.
Cheap tools don’t cost less. After buying a new CNC, it’simportant to make sure that it’s allowed to do its best work. Inexpensive tooling is far more prone to overheating, gets dull quickly, and can cause undue stress on the spindle and motors. Worse, dull tools deliver parts with burned and inaccurate edges, and tear-out.
Most shop owners will caution that one shouldn’t buy a machine without first ensuring that spare parts are not just available, but readily so. Downtime is expensive and demoralizing. It also creates bottlenecks through the rest of the shop. Before buying a CNC, and especially a used one, know where parts can be found and just as importantly locate experts who can complete any repairs.
A shop owner should give serious thought to the location of a new CNC. As with any machine, it will need physical space around it to load and unload materials, and that can be a serious challenge in a smaller woodshop. The new machine will also need room for dust collection ducting, and access to both electrical power and compressed air. If there’s a tool changer and a vacuum table, it’s probably time to buy a bigger compressor.
One item often overlooked is the need for more carts and lifts.Where will they be stored, and is there enough floor space for them to access the machine?
This may seem obvious, but CNC manufacturers caution that the shop owner should check to make sure the floor is strong enough to hold all the new weight. Wood floors on joists might not be. One of the ways that CNCs avoid vibration is to bulk up on mass, and some of them are surprisingly heavy.
A CNC may require true 3-phase rather than an auxiliary phase converter, so check with an electrician and also ask about total amperage coming into the building. The added draw of extra dust collection and a vacuum table might exceed the available load.
The existing dust collector may not be powerful enough, so it’s a good idea to check the velocity and volume requirements of the new machine.
If there’s a choice in control systems for the new CNC, odds are that one of them is easier to use while the other offers more features. This will be a very subjective choice: each woodshop has different requirements. Somewhere in there, the owner also needs to assess the skills of the employees and decide whether the shop is best served by either simple or more control. Part of that decision is also tied to the seller. A used machine won’tusually come with much or any training, but the price of a new machine might include employee training. That might be onsite at the shop, or in a training facility that uses the manufacturer’s machines, or even at a different shop that has a similar machine. The more training, the faster the CNC will start paying for itself. Learning by trial and error can be expensive.
Know what you’re getting
The spindle is the heart and soul of a CNC and for smaller shops buying their first machine, it’s very important to do due diligence. It’s good advice to buy a trusted brand name that offers great support and solid history.
Spindles are often evaluated on their speed and power. After that, check on what buyers online say about precision, tolerance, and longevity. The materials being processed will play a part in choosing the most appropriate spindle. Woodshops tend to process plastic laminates, solid hardwoods and softwoods, and a range of panel products such as Baltic birch, MDF, HDF, and other composites. It’s important to quantify these and understand how much of each will be presented to the new machine. Some composites behave better with low torque and high speeds, while other materials prefer the opposite. A slow spindle may not be able to reach the optimum chip load for different tooling/material combinations. That means the tool will be cutting the material more than once.
CNCs intended for woodworking generally have faster spindles than machines that process soft metals or similar products. So, a CNC with a high rpm spindle will most likely be better suited to woodshop work. What they give up in torque, high speed spindles make up in terms of process cycle time (how long it takes to make each part), the life of the tool’s cutting edge, and less wear on the spindle. A variable speed spindle with generous top and bottom limits may be the best choice for shops that process lots of different materials.
Is the machine compatible with the shop’s existing software? And will third-party software such as performance or maintenance tracking apps work well with the new machine?
CNCs require regular maintenance. The shop owner should ask whether the new machine has a required maintenance schedule, and if so, what’s the cost? Who performs various tasks – a factory rep or an in-house employee. Is there downtime involved, and if so, how much and how often?
The bottom line here is that buying a CNC for a smaller woodshop doesn’t necessarily mean buying a smaller machine. But it might mean buying a basic model that can be upgraded over time.
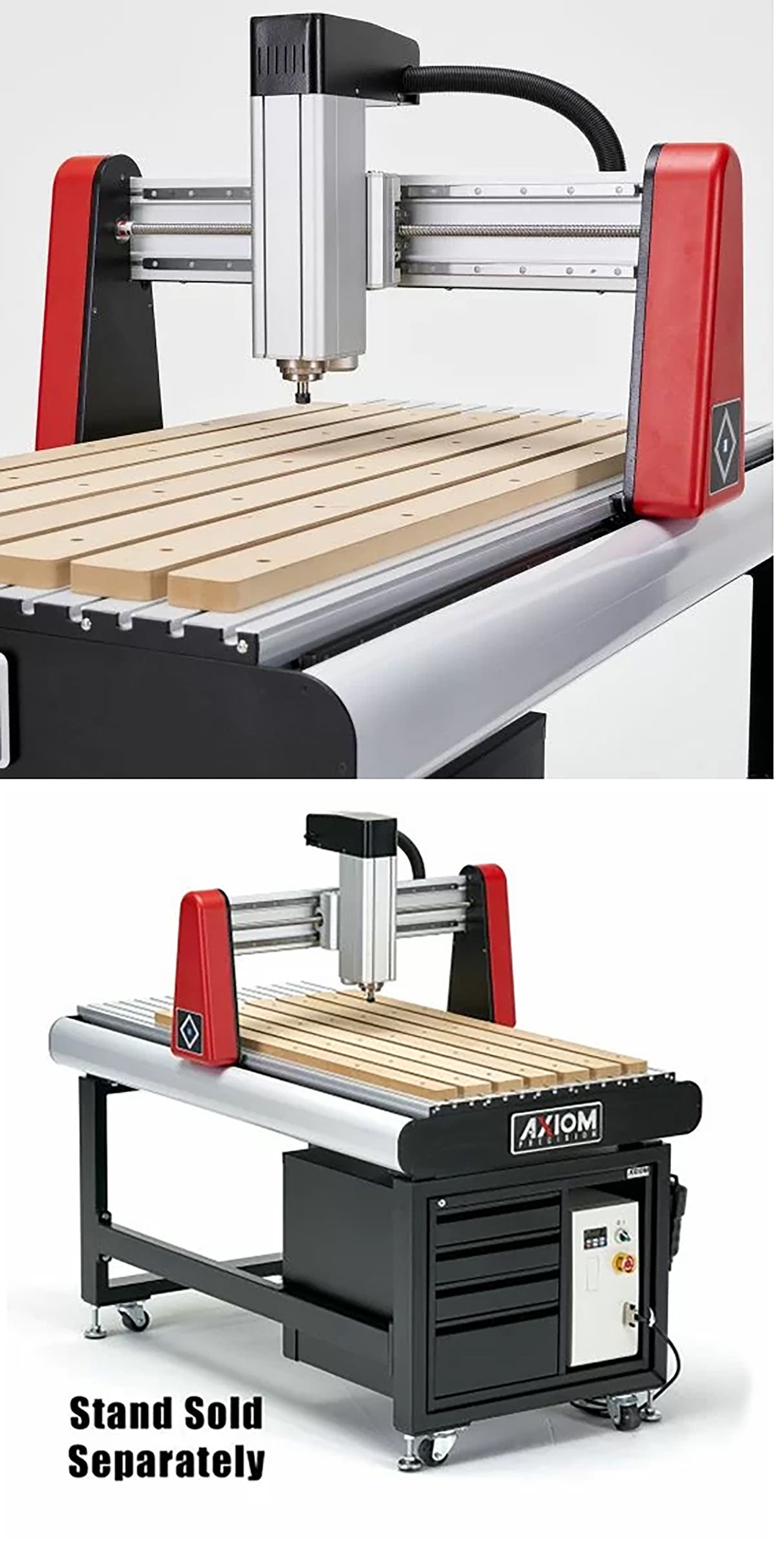
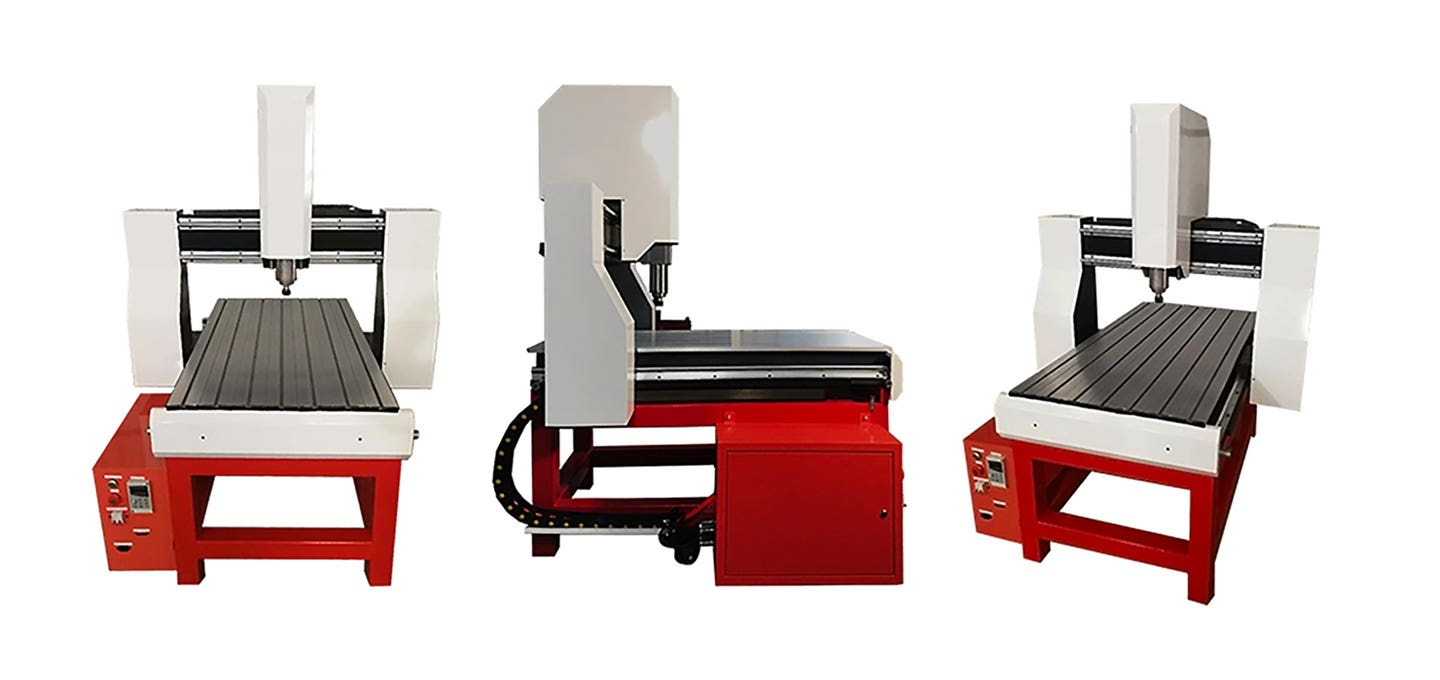
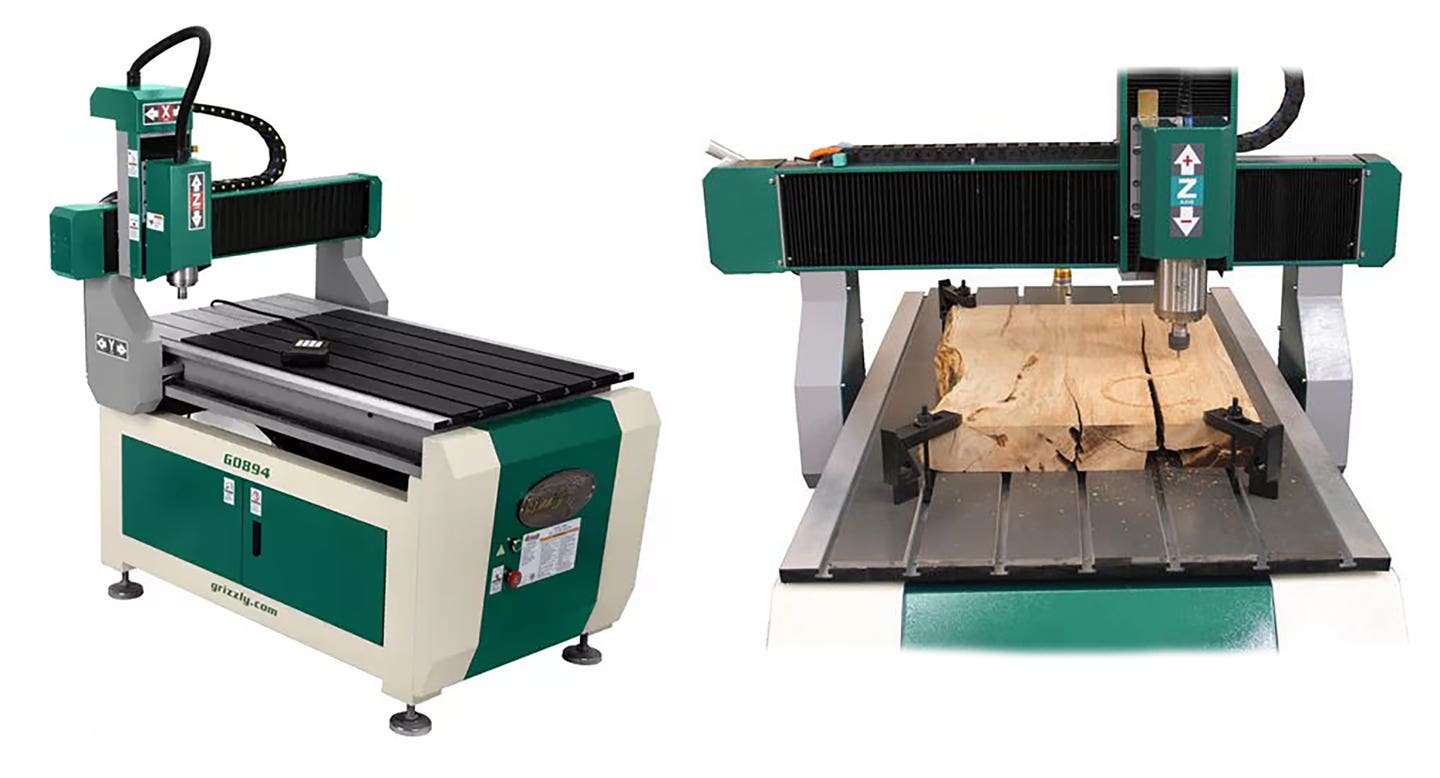
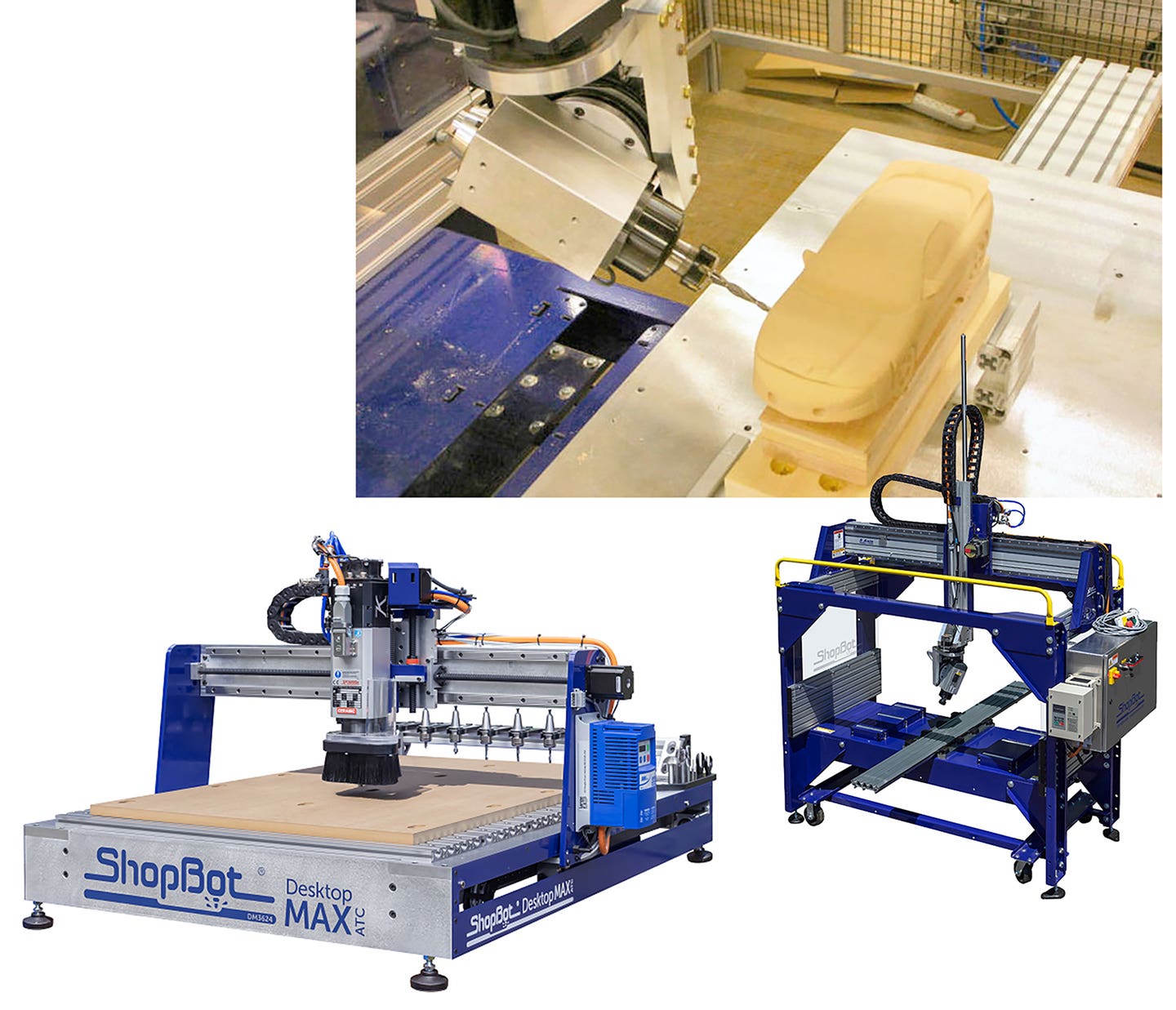
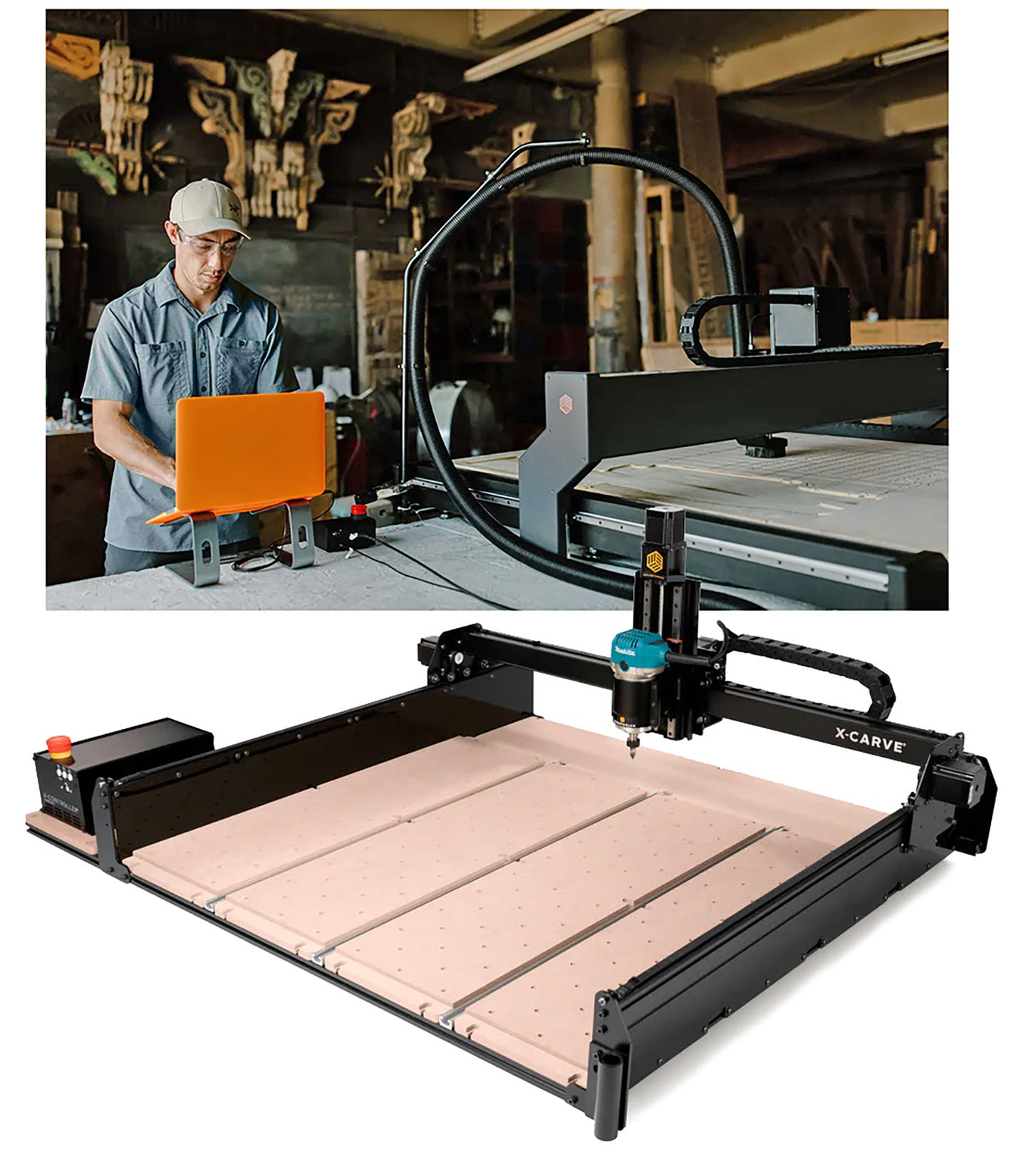
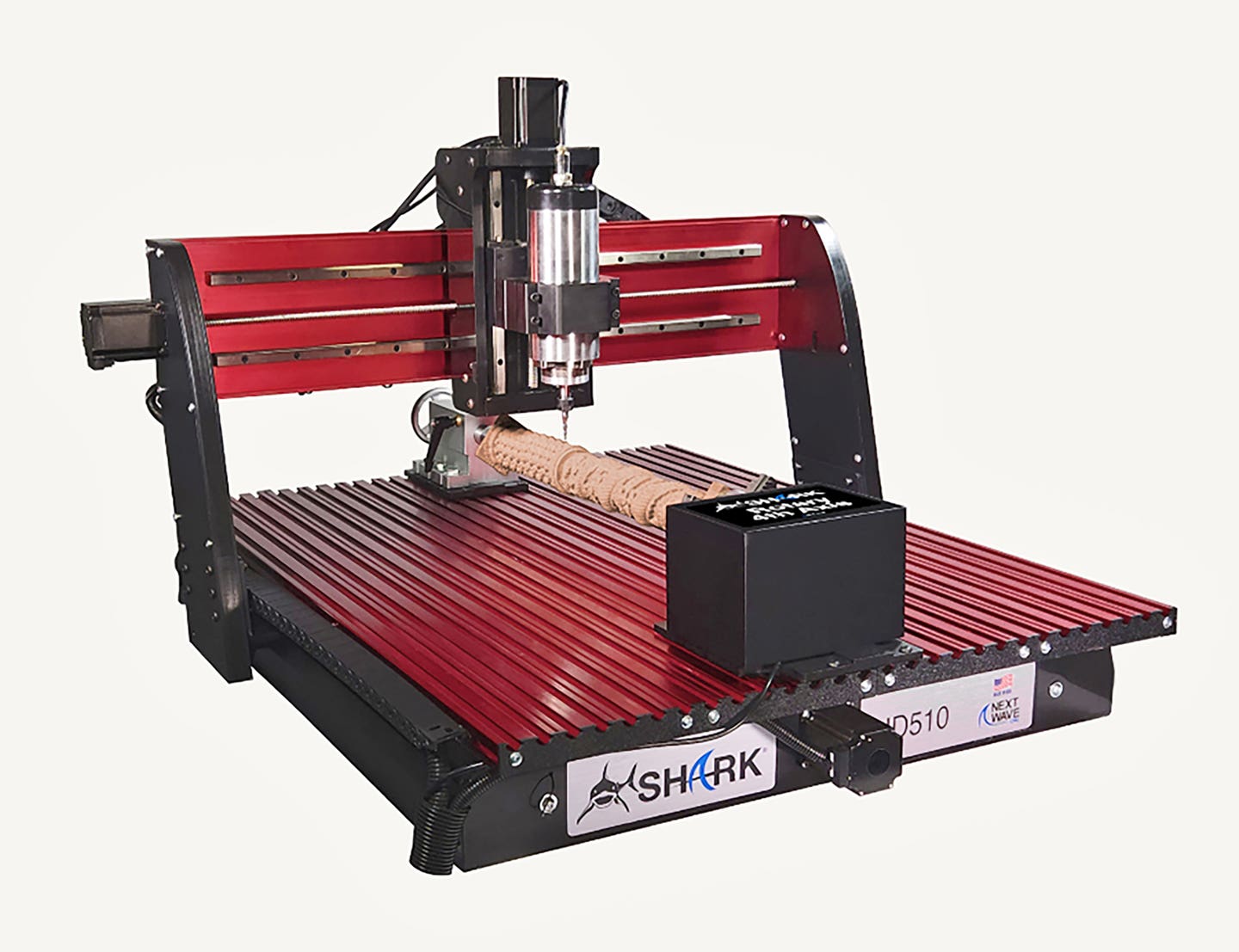
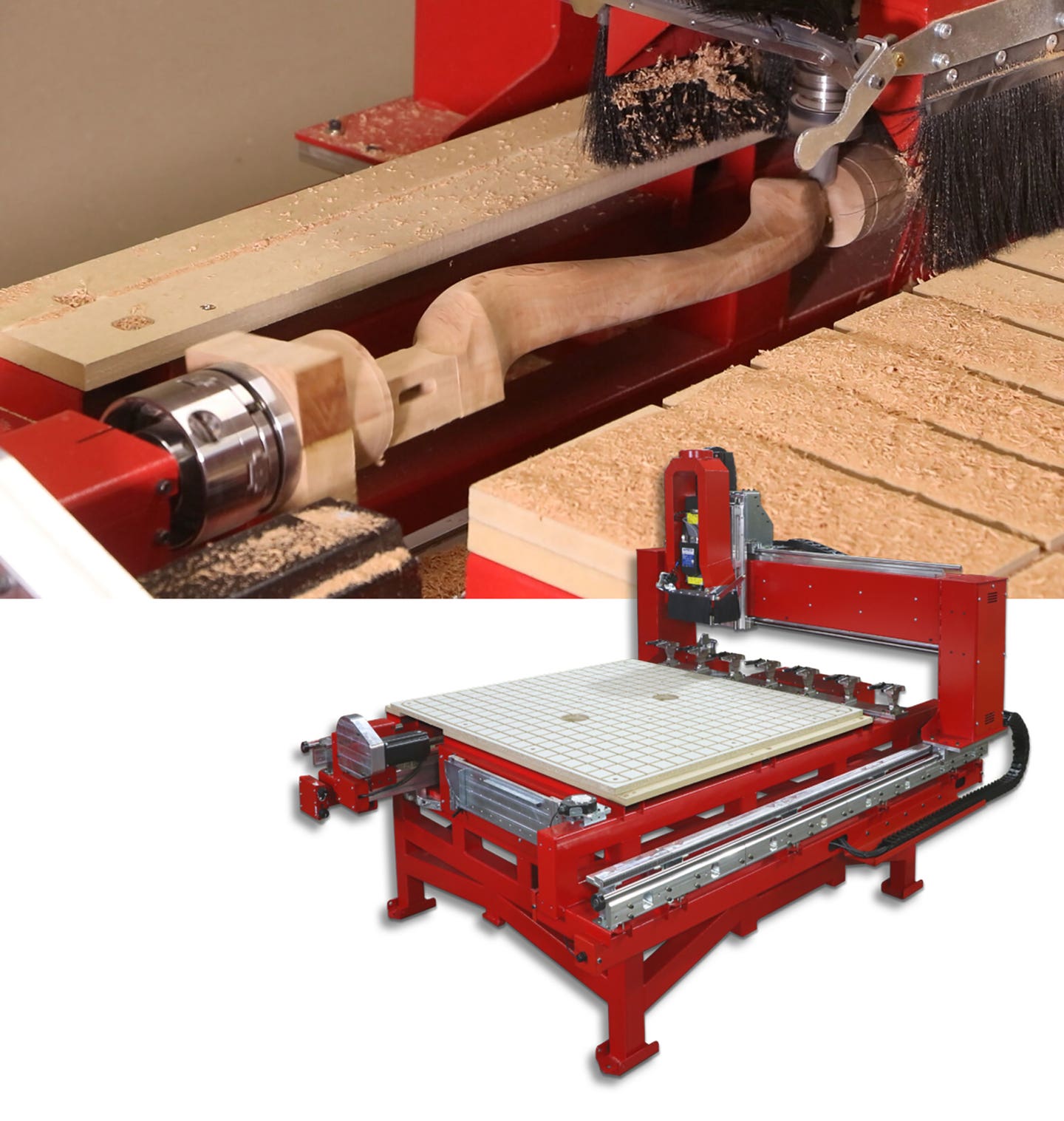
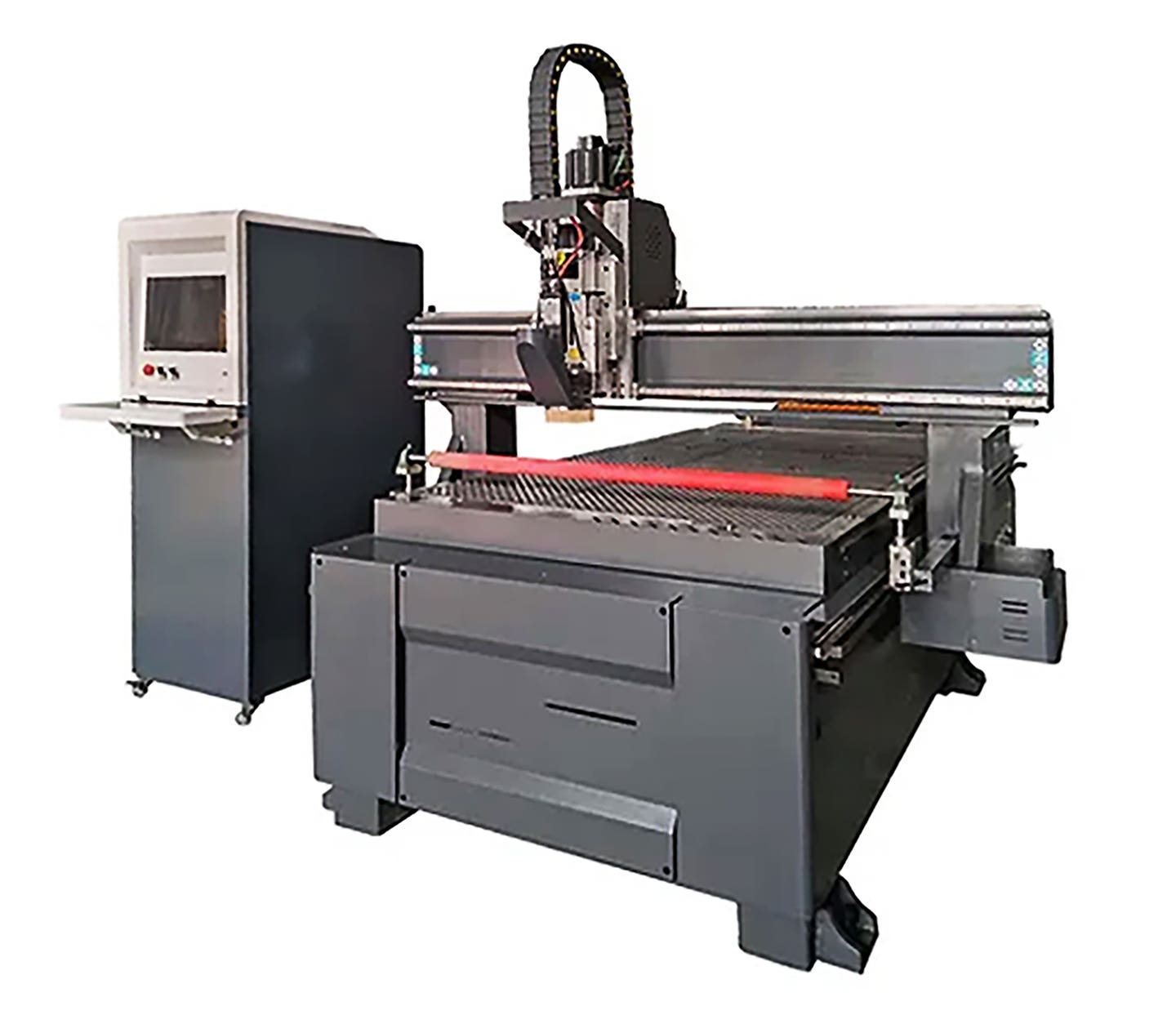
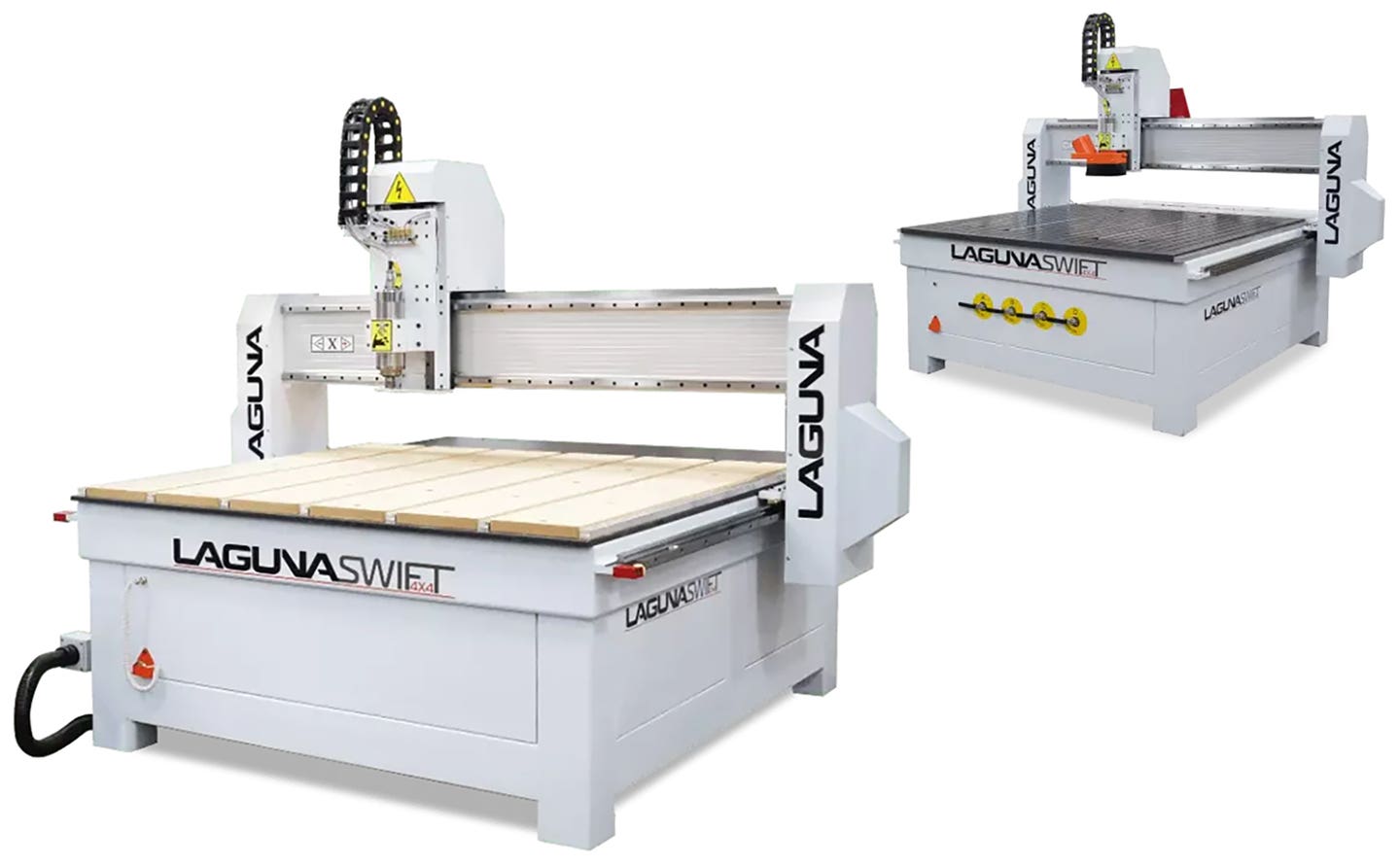
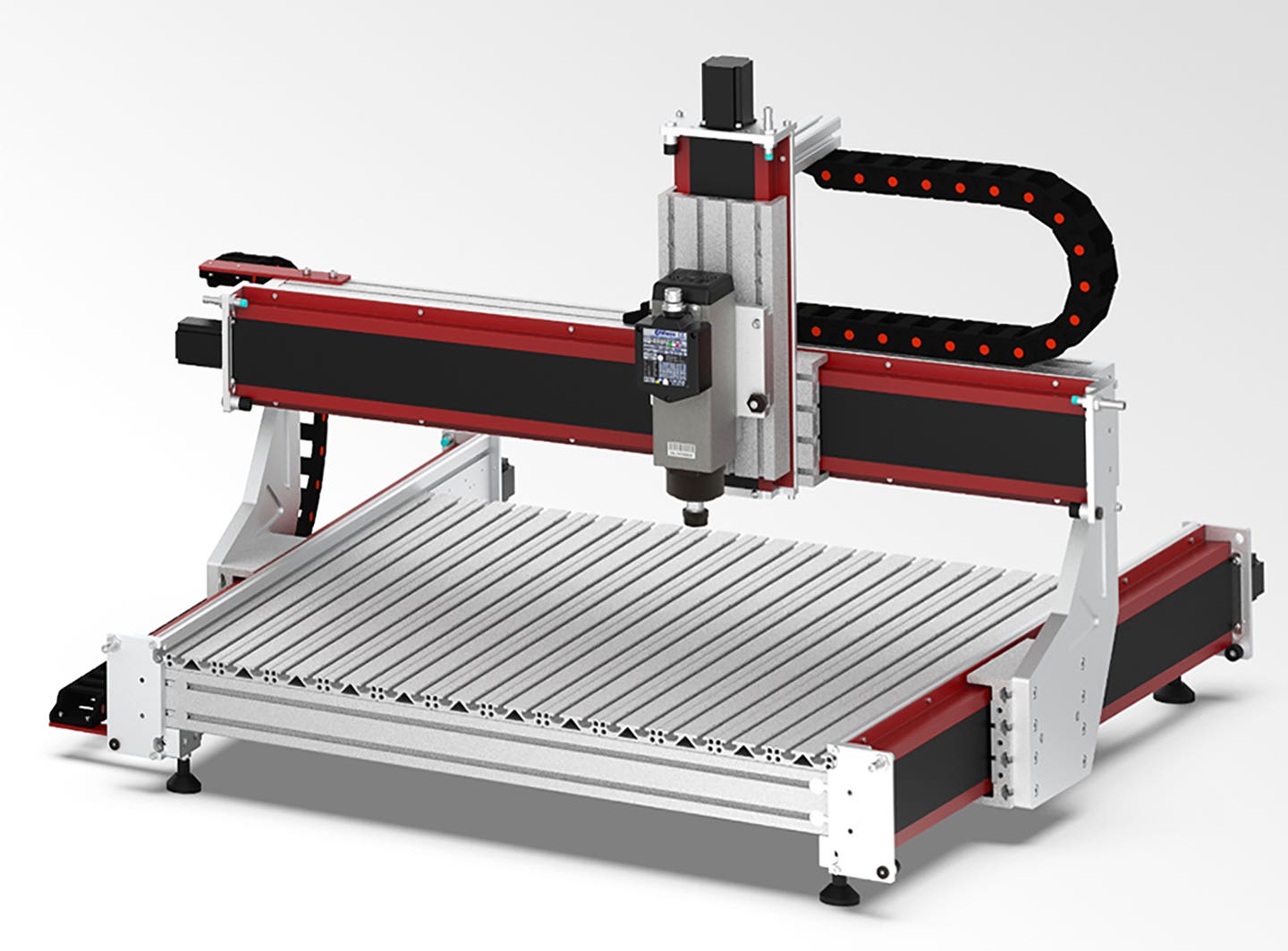
Resources
Anderson America andersonamerica.com
Atlantic Machinery atlanticmach.com
Avid CNC avidcnc.com
Axiom Tool Group axiomprecision.com
AXYZ axyz.com
Biesse biesse.com
C. R. Onsrud cronsrud.com
CAMaster camaster.com
Casasei-Busellato casadeibusellato.com
Castaly-Lobo Machine castalymachine.com
Felder Group felder-group.com
Hendrick Mfg. hendrickmanufacturing.com
Hermance Machine hermance.com
Holz-Her USA holzherusa.com
Industrial CNC industrialcnc.com
Inventables inventables.com
JKL Machiner jklmachinery.us
Komo Machine komo.com
Laguna Tools lagunatools.com
Legacy Woodworking legacywoodworking.com
Limtech Industries limtechindustries.com
Martin Woodworking martin-usa.com
Masterwood CNC masterwood.com
MultiCam multicam.com
NewCNC.com newcnc.com
NextWave nextwavecnc.com
Pro Edge Technology proedgetechnology.com
Rexmotion rexmotion.com
SCM Group scmgroup.com
Shaper Tools shapertools.com
ShopBot Tools shopbottools.com
Stiles Machinery stilesmachinery.com
Techno CNC technocnc.com
Thermwood Corp. thermwood.com
Vision Engraving visionengravers.com
Yeti SmartBench yetismartbench.com]
Originally published in the September 2024 issue of Woodshop News.
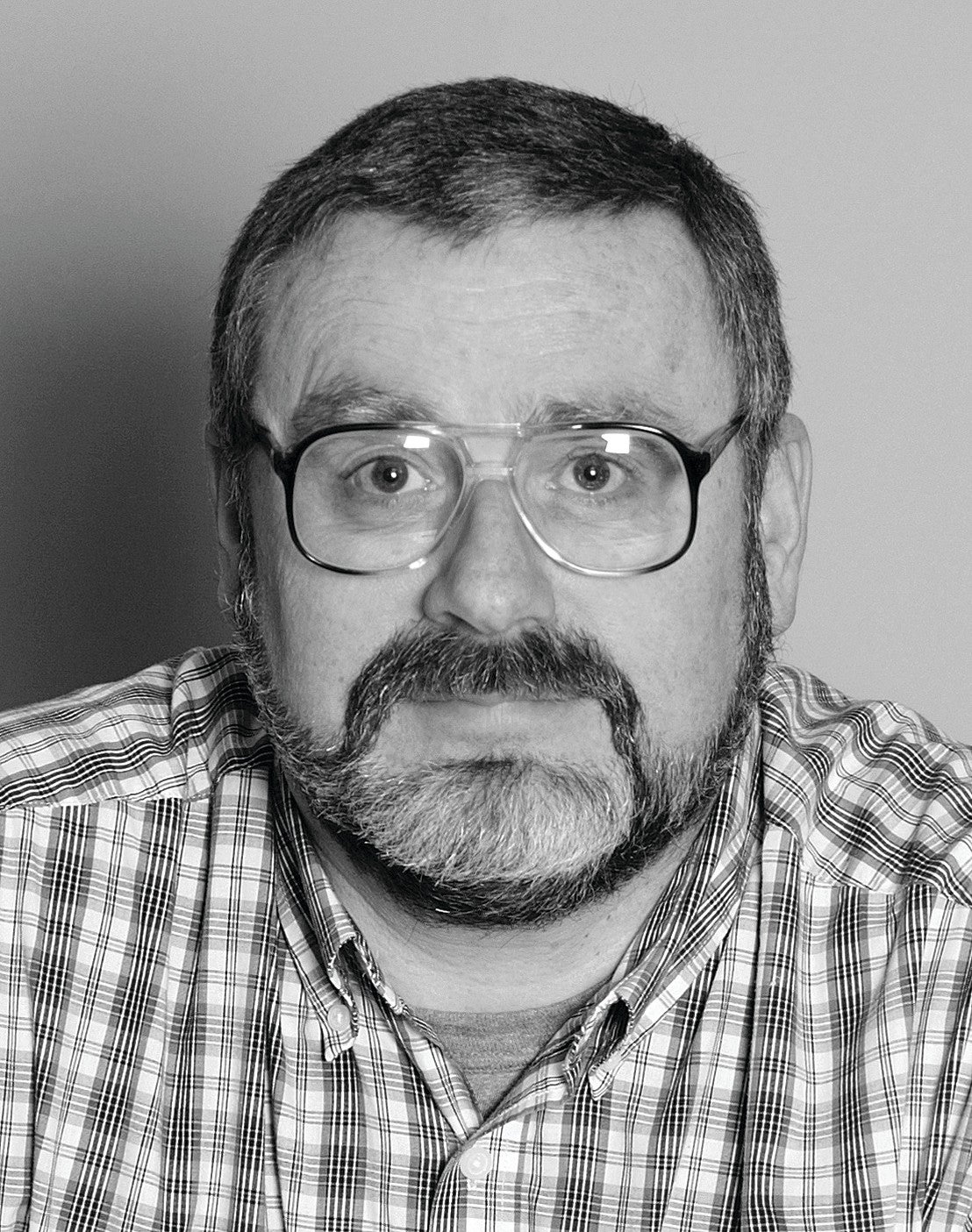