Buying a bit for nesting has become complicated over the years. While there are still traditional straight and plunge bits, there are also upcut and down-cut helix bits and a new generation of compression bits. These different geometries can play a huge part in the quality of the cut edge.
Upcut bits are all about chip extraction. An upcut spiral bit funnels waste up out of the groove and leaves a good edge on the bottom and a decent edge on the top of the cut, although it can fray a little in some species of solid wood. Upcut geometry works extremely well on large sheets, but the torsion can partially lift small or lightweight parts up off the bed. That can minutely distort a toolpath by moving the part, or causing minor chatter, or even letting a little dust lodge under the workpiece.
One big strength of a down spiral or down-cut bit is that it forces the workpiece down against the table, and that helps it deliver a smoothly cut edge. The waste is forced down but then out into the channel that has just been cut, so the bit isn't constantly recutting the same material. The downward action means that secured parts rarely move, but it can be a dusty environment if proper extraction isn't in place. And if the shop needs to cut plastics or Plexiglas, a down-cut can sometimes melt and meld the cut waste into clumps that cool and harden and then need to be removed manually.
The spirals on a compression bit are an engineered combination of both up-cut and down-cut helices. The tip area is up-cut and the rest is down-cut, so the chips are moved to the center of the cut before being evacuated into the channel that is being made, or through the wake of an exposed edge cut. This two-direction action delivers cleaner edges top and bottom, so these bits are great choices for double-faced laminate, veneer and melamine sheet goods. These are not usually plunge bits, so the up-cut section needs to address the edge of the bottom face of the panel while the down-cut touches the top face. If the bit is set too low in Z, it just delivers the results of a down spiral and the bottom face can have some blow-out. So, parts need to be suspended above most spoil boards with fixturing or pods to get the bestaccess.
Straight bits without a spiral (helix) are less expensive, and these are also the tools of choice for many 5-axis CNC operations because they reduce vibration. But the cut isn't as clean as it can be with up and down spiral cuts. A simple straight bit is the go-to solution for making small parts on a small CNC but is not the best choice for large work. That's because with a spiral CNC tool, some part of the cutting edge is always touching the perimeter of the cut. With a straight bit, only the flutes are in contact, and these are in a straight and vertical or slightly shear orientation. The constant contact offered by a spiral bit delivers less vibration or chatter, and even though this is minimal, it can affect the quality of the edge. A handy rule of thumb is that for smaller parts (up to maybe the size of a small drawer face), down spiral or straight bits work best. For anything bigger, most shops go with an up spiral.
Buying CNC tools
Cheap tools deliver cheap results. There's just no getting around that. Sometimes the shafts are a little oversized so they jam in the collet, or undersized so they slip and even work loose. Sometimes they're not exactly straight and the further one gets from the collet, the more erratic the action as they wobble.
Cheap grades of carbide can be too hard, so they're brittle. If they're too soft or the grain of the carbide is too coarse, they won't hold an edge. The carbide is often too thin for sharpening, and sometimes the brazing is so uneven that the insert has beeninstalled at an unintended angle. If the bit comes from a manufacturer who cares more about quantity than quality, odds are the brazing has been done at the wrong temperature. Too cold causes the joint to fail over time, and too hot draws the temper out of the carbide and makes it too brittle.
If possible, the experts say, always go with a thicker shank. That's not always a choice for tooling on a small CNC where the spindle and toolholders can have limits. Some of the smallest machines use a portable router motor that can handle 1/4" or 1/2" shanks, but others use a laminate trimmer that restricts the choice to just 1/4" bits. Large diameter bits have a larger heat sink, and they are far less prone to flex under shearing stress (pressure from the side).
Another shop adage is to buy the shortest bit that will do the job. The longer the bit, the bigger chance there is of it flexing or vibrating. But one should also buy bits with shanks that are long enough to seat properly and deeply enough in the collet, and not just hang on by their fingertips.
To add a little to tool life, shops with automatic tool changers can cut profiles in several steps using different tools. For CNC owners who don't have this upgrade, it's important to make deep cuts incrementally, over several passes, rather than forcing the action. That’s because heat is the enemy, and plowing a deep groove at fast travel speeds can be devastating for a tool's cutting edge. It's not great for the spindle, either.
How they’re made
High-speed steel doesn't usually pass muster for industrial tooling, so either tungsten carbide or polycrystalline diamond (PCD) are used for both brazed bits and insert tools.
There are two ways to make diamond dust for a CNC tool. The first is a high temperature and high pressure sintered coagulate of minute diamond particles in a cobalt base. The result is called HPHT, which stands for 'high pressure high temperature' diamonds. The other process is named chemical vapor deposition (CVD), and the sequence is interesting. A seed synthetic diamond is placed in a vacuum chamber, and then gasses that one might have found around primordial natural furnaces (such as hydrogen and methane) are introduced before heat is applied – lots of heat, more than 1,600F. That causes the gasses to break down and leave a thin carbon residue on the seed, which is like a diamond skin. This replicates the way Mother Nature baked her diamonds, and the results are impressive: it takes specialized equipment to tell CVD diamonds from natural ones.
While diamonds may still be a girl’s best friend, they’re no longer the hardest substance on the planet. Carbon nanotubes have a greater degree of hardness at a microscopic level. And in 2023, a combined research team from Lawrence Berkeley and Oak Ridge National Laboratory identified a metal alloy of chromium, nickel and cobalt as being tougher than diamonds. So, metallurgy marches onward and we may soon see that concoction in our woodshops. But for now, PCD seems to be the best impact material for production tooling on a CNC.
Technicolor dreamcoats
CNC tool coatings are a non-liquid lubrication that helps resist resin build-up and excessive heat. It has become fashionable to showcase the coating by using bright colors.
Coatings can behave differently in manmade sheet stock than they do in solid wood. Sheet stock contains particles that are oriented in every direction, while wood grain is orderly and relatively linear. Those haphazard particles are also embedded in, or layered between, resins that behave differently during shear impact than wood cells do.
Manufacturers say that coatings can make the cutter cooler and therefore more durable, which means that it lasts longer between sharpenings. Anecdotal evidence seems to support that claim. Sharpening removes the coating on the face or edge being ground, so some sharpeners offer their own coatings after the factory ones are gone. Some woodworkers use coated tools onceand then discard them, rather than sharpen and recoat. Some say it’s because the sharpening process changes the shape of the tool, so their CNC then needs to be recalibrated. But that's true of new tooling, too. No two new bits are absolutely identical.
Sharp edges produce less friction, and less heat. In fact, everything about CNC tooling comes back to that one abiding factor, heat. This causes both chemical and physical deterioration. And that's interesting because commercial (manmade) diamonds are grown that way, with either physical or chemical vapor deposition. So, there's a similarity between the ways that CNC tools are born, and the way they die.
The coatings on CNC tools are usually made with dust from natural diamonds (harvested from processing for jewelry and other uses), or zirconium nitride, or titanium nitride.
Feed and travel speeds have a lot to do with heat build-up, too. That means the CNC operator has quite a bit of control over the deterioration rate of the cutting edges. And if a coating is working in the material being cut, then the bit won't get as hot. So, it can travel and cut faster.
It's always a good business decision to track wear on CNC tooling. Some machines do that automatically, and some software packages can keep track of changeovers plus bit inventories and costs. But for many shops, a simple clipboard may be the answer. Tracking can be as basic as noting which bit is being used, and then how many feet of cutting, grooving or profiling was done, or how many holes were drilled. The numbers don't need to be impeccable, but what they can reveal is which bits work best, and how often they need to be changed, sharpened and replaced. That can also tell the shop owner what percentage of his budget is being spent on CNC tooling, and whether it's time to research new options.
Originally published in the November 2024 issue of Woodshop News.
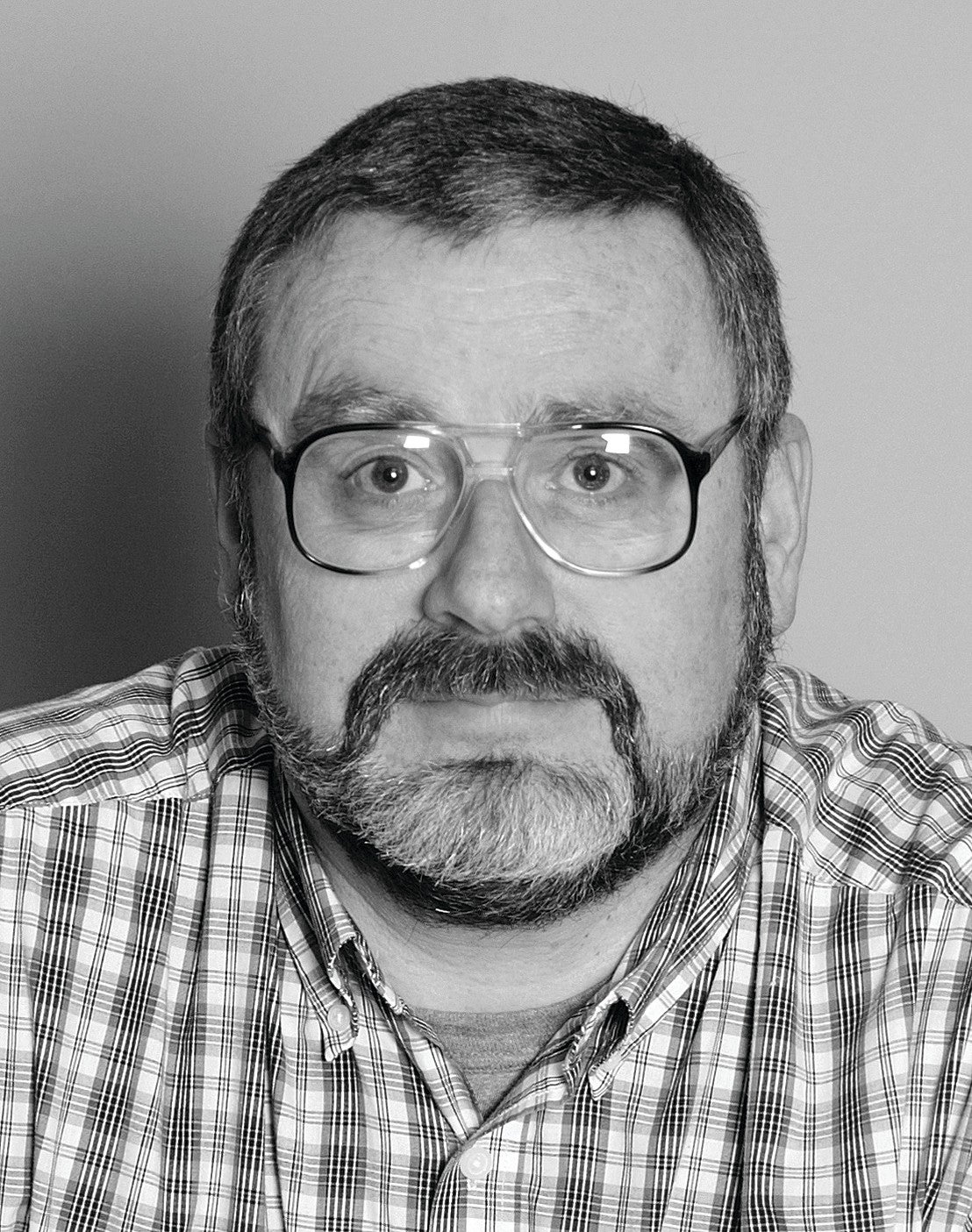