Upgrading to a shaper or molder
How they work, what’s the difference, and why they’re a step up from a router table
There can be confusion about molders and shapers, and some of that comes from shops in Europe and the U.K. where they call a shaper a ‘spindle moulder’. In North America, telling the machines apart is a bit simpler. Most of the time, molders have horizontal shafts and shapers have vertical ones. That’s not exclusive, but it’s a handy rule of thumb.
Molders can be quite complex. Depending on the shop’s budget, they can address up to four faces of a board simultaneously and work on some very wide stock, while shapers primarily work on, or close to, solid wood edges. Both machines can raise a panel (within limits) or profile a molding, but each has strengths and weaknesses. For example, some molders and most shapers can be set up to do curved work for arches, bows, cathedral rails for cabinet doors, and the like. But some can’t, so if a shop is in the market for a molder or shaper and curves will be involved, it might be advisable to do a little research on aftermarket and shop-built jigs for curved work before buying.
Just to paint a visual, a four-sided molder is basically two horizontal molder heads (top and bottom) and two vertical shaper heads (sides) that are staggered so the knives don’t run into each other.
There’s also some discussion among woodworkers as to the quality of cut. In an informal and highly unscientific quick survey of discussion boards, most shop owners are of the opinion that a shaper delivers a finer cut, especially across grain, and that molders seem more susceptible to minor chatter that will need to be sanded out. That makes sense when one is talking about small or inexpensive machines where the knives are thin, and the power feed doesn’t have a lot of torque. But for professional machines, basic cut quality isn’t an issue.
Some small thickness planers can be set up with profiled knives, in effect converting them to simple molders that can work on one wide face of a board at a time.
Cut quality also depends on power delivery. For shops buying an older version of a small molder or shaper, a mild vibration might be attributable to worn bearings. But surprisingly, another likely cause is that the pulleys are actually out of round. And in some cases, the arbor hole in the pulley has become misshapen over time and no longer runs true. Out-of-round pulleys can be machined or replaced, but a segmented belt rather than a standard V-belt can often solve the problem, too.
The scale of work is more relevant when it comes to molders and shapers than it is with most other traditional machines. A small shop can meet many of its profiling needs with a single molder head and a thin shaper spindle – there are some as slim as 1/2", but 1-1/4" is probably as small as one should go for any level of production work. Medium-sized shops doing frequent tongue and groove or flooring runs are probably going to want a multi-head molder. And small shops moving up from a router table to a basic shaper will discover that the tooling is more expensive and needs more frequent sharpening. Molders and shapers also have a learning curve, especially regarding safety. These more powerful machines engage more surface area so they’re less forgiving than a router. Accessories such as power feeders and sleds can do a lot to protect fingers. On the other hand, belt-driven shapers tend to run a lot quieter than router tables, and they have the power to make deeper, wider and cleaner cuts, and plow through knots and dense species that might meet resistance on a router table.
Power struggles
The best answer is that a well-equipped shop has both a molder and a shaper. It’s all about the nature and volume of the work being done, and those considerations are also the reason that shops seek to upgrade from a router table.
A large table-mounted router can handle some sizeable bits, but their geometry is an important consideration. Some profiles are tall and thin, and they run the length of the bit, so they are vertical in nature and set into the fence. These are used to cut a design into the face of a part that is run on its edge along the fence, such as a picture frame or a small crown molding. Other profiles are quite wide, such as large round-over or panel-raising bits, and for these the part lies flat on the table and is guided by the fence or a bearing.
Both tall and wide router bits have limits, and those are imposed by a sensible assessment of the risk involved. The 1/2" diameter shaft on wide and tall router bits is quite adequate for the task, but the router itself is a significant parameter for the bit manufacturers. Bit makers know how far they can safely go in cutter width and height. Large cuts on a router table are taken at slower speeds and in incremental passes as a means to lower the risk and the stress on both the bit and the router. These practices facilitate the use of some quite large cutters, but they are in essence a compromise, an acknowledgement of the limits. But a shop that has already invested in high quality tall or wide router bits is ahead of the curve when adding a shaper, because these very large bits will behave perfectly in the larger machine.
A shaper has far more mass than a router, and most also have a more robust shaft. That combination, in conjunction with a larger belt-drive motor, lets them safely spin much larger cutters. The added mass means they take a second or two longer to reach optimum momentum, and veteran woodworkers often need to remind novices to let the machine get up to speed before engaging the cutters. But that momentum also contributes to a deeper cut with a smoother surface. So, the shaper saves time in terms of having to make fewer passes and having less sanding to do.
The motor in most table routers is a universal commutating brushed motor, which doesn’t cost a lot and doesn’t take up much space. But it’s also not made for long and arduous production runs. A universal motor starts up and gets to full torque quickly, but it also runs at high speed so the brushes can wear out. Cordless brushless motors are just beginning to reach the performance levels required in an all-day router table.
The single-phase AC induction motors in small- to medium-sized shapers and molders have a rotor that spins inside a stationary cylinder called a stator. That movement creates a rotating magnetic field because the rotor is basically an axle covered in magnets which are attracted to the stator’s magnetic field. They spin as they hit the poles, being dragged from positive to negative and experiencing attraction and repulsion in turn. The rotor needs to get up to speed on start-up, but once there it’s quite powerful. Larger shapers and molders have 3-phase induction motors that can deliver a lot of torque. These types of motors are uncomplicated, tough and energy efficient.
Making the cut
There are some quirks with shapers, such as the opportunity to stack cutters (the number depends on the length of the shaft), and the machine’s ability to run in reverse with the cutters turned upside-down. That can really help with difficult grain. For example, on a round tabletop with the grain running in a single direction, the edge grain could be shaped in forward, and then the end grain in reverse or some combination of the two, depending on whether contact is being made with or against the grain. With most projects the workpiece can simply be flipped over, but there’s always that day when the grain runs wild and it’s nice to have another option. It’s a bit like climb-cutting on a router table but without the potential kickback.
A woodworker can run router bits in most shapers, but the reverse isn’t true. That means the shaper can run a lot of tools (it will probably need an adaptor) that the shop already owns. Be aware that shapers usually spin at about half the speed of a router, so running a test board is good practice. At such slow speeds, large bits might tear out in difficult grain.
In general, the larger the shaper’s motor, the thicker the spindle and the more adjustment it will have in Z (up and down). That can be a critical dimension in wider parts on a shaper, but molders don’t have the same issue. They resemble thickness planers in configuration, so they can handle much wider boards. But because of that width, they meet far more resistance, so cuts need to be made in slow increments, especially on smaller machines. Molders are perfect for tasks such as paneling, flooring, architectural trim (especially Victorian reproductions), and making wide and flat T&G panels. Some versatile molders such as the Williams & Hussey machines can make arched window trim all day long, cutting out many steps that need to be completed by shops using edge-glued laminated strips and routers on trammel jigs.
That underscores the main reason for upgrading to a shaper or molder: they shorten the workday. That efficiency can release some profit, but it also lets shops offer more options to clients. There’s good money in running a few feet of wide or fancy trim for renovation contractors, or high-end homes. And unlike building cabinets, there’s usually no assembly required.
Going shopping? Here’s a list of resources that may help.
Molders
Casadei-Busellato America casadeibusellato.com
Castaly/Lobo Machine lobomachine.com
Global Sales Group globalsalesgroupinc.com
Leadermac USA leadermacusa.com
Mikron Woodworking Machinery mikronmachinery.com
Northtech Machine northtechmachine.com
SCM Group NA scmgroup.com
Stiles Machinery stilesmachinery.com
US Concepts usconceptsinc.com
Weinig weinigusa.com
Williams & Hussey williamsnhussey.com
Wood-Mizer woodmizer.com
Shapers
Atlantic Machinery atlanticmach.com
Baleigh Industrial baileigh.com
Cantek America cantekamerica.com
Felder Group USA felder-group.com
Grizzly Industrial/Shop Fox grizzly.com
Ideal Machine idealmanufacturingllc.com
Ironwood Machinery ironwoodmachinery.com
JET Tools jettools.com
JKL Machinery jklmachinery.us
Laguna Tools lagunatools.com
Larick Machinery, Inc. pillarmachine.com
Northfield Machinery northfieldwoodworking.com
Northtech Machine northtechmachine.com
Oliver Machinery olivermachinery.net
Powermatic powermatic.com
SCM Group NA scmgroup.com
South Bend Tools southbendtools.com
Stiles Machinery stilesmachinery.com
Originally published in the December 2024 issue of Woodshop News.
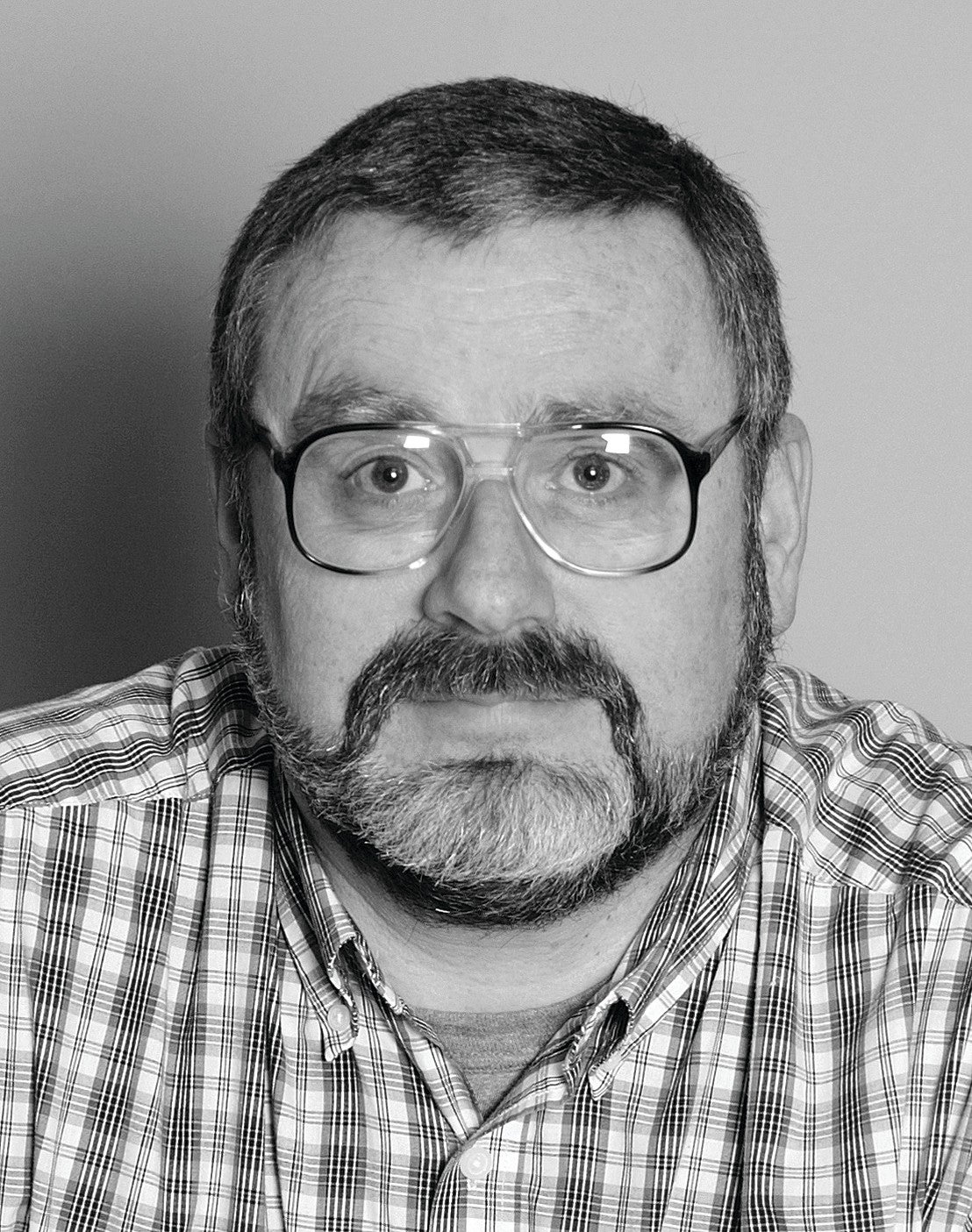