Green in the finishing mix
Whether it’s a reaction to government regulations or consumer demand for greener finishes, manufacturers have increased their offerings in recent years to include waterborne, low VOC and formaldehyde-free products. “We…
Whether it’s a reaction to government regulations or consumer demand for greener finishes, manufacturers have increased their offerings in recent years to include waterborne, low VOC and formaldehyde-free products.
“We are well-positioned for various environmental regulations,” says Bob Deiter, category director at M.L. Campbell. “We have high VOC products, which is typically the preferred product in the industry. We can offer our customers options for formaldehyde-free conversion varnishes, precats that are acid-free cure, which is extremely new technology, waterborne low-VOC and low-VOC solvent-borne products.
“In roughly 1990 we started spending a tremendous amount of research and development time formulating our products to be solvent HAPs-free. It was all about having safer solvent blends and focusing on worker health safety. We were the first coatings company to be Greenguard-certified. It’s something we feel strongly about. We try to be a good steward and leader in environmental safety and emissions.”
The diverse offerings are mostly a response to regional air quality regulations. There are stricter laws in California than the rest of the country, for example.
“A lot of the issues are different based on how someone is classified as a user. For example, there are some areas that consider low VOC being extremely important. California would be that state. The South Coast Air Quality Management District in Southern California pretty much set the VOC limit bar at a relatively low level. Most other states don’t have a consistent approach for VOCs,” says Deiter.
“Low VOC is a misnomer and let me tell you why,” says Erick Kasner, president of Hood Finishing Products. “Low VOC in California means 275 grams per liter. VOC in the New York City area is 672 grams per liter — a big difference — so almost any nitrocellulose lacquer qualifies as VOC compliant.
Kasner says other regions of the country are not following the Southern California standard. “Most major cities follow, but not to the strictest content of California.”
Pro and cons
The fundamental criterion for all “‘green technology” products from Hood Finishing is that they must be truly water-based, not just water reducible, according to the company’s website. Its major component must be water and its thinner or reducer must be water only. They cannot contain hazardous air pollutants such as xylene or toluene, nor can they contain any toxins or carcinogens such as lead, mercury, phthalates, toxic preservatives, fungicides or N-Methyl Pyrrolidone (NMP), a reproductive toxin causing birth defects as listed on California’s Proposition 65.
“There’s a distinction between a water-based and truly green. Water-based is fine — it’s going in the right direction,” says Kasner. “There’s nothing that is perfect. There’s always going to be something extremely good and extremely bad. Let’s look at lacquer as an example. It’s biggest plus is the way it reflects light, its extreme clarity and the warmth it gives wood. On the negative side, it’s hazardous to your health and it’s flammable.
“On the plus side for water-based, it’s environmentally-friendly, your safety is enhanced significantly and it’s non-flammable. On the negative side, it does not provide the warmth. It’s also very temperature-sensitive and very sensitive to slow-drying, oil-based stains.”
No end to trend
M.L. Campbell has 16 products with Greenguard certification, including EnviroVar formaldehyde-free acid cure conversion varnish, which won a Sequoia award for green/environmental leadership in wood coatings at the 2011 AWFS fair. The company has recently released a pre-cat version.
Acid cure products are predominantly used in the kitchen cabinet and architectural millwork markets. “It gives you very good application characteristics, a lot of flexibility for product use, dries fast and is priced relatively good,” says Deiter. “The acid that’s introduced creates a chemical crosslinking with the formaldehyde urea resin and, during this reaction, that’s what actually off-gasses formaldehyde. It’s becoming a bigger problem and that’s why we spent a tremendous amount of effort getting formaldehyde out of this product.”
Formaldehyde-free “is a significant price increase,” adds Deiter “It all revolves around raw materials. Most customers are trying to figure out how they want to position themselves, whether they want to offer a green product. No one has a crystal ball to understand regulatory timing. And it’s not just coatings — it’s particleboard, adhesives, MDF and plywood.
“The ideal scenario would be if every local government or municipality had the same regulatory restrictions. From a coating manufacturer’s perspective, that would make our job a lot easier.”
That’s probably never going to happen. While Europe has embraced waterborne finishes, the North American market is about 90 percent solvent, says Deiter. “While we consider our waterborne products to be very good — and I’m sure our competitors do, too — they are a little bit more difficult to get consistent results. I will say that over the last five years, waterborne products have greatly improved for durability. They almost mirror their solvent-based counterparts, but you’re challenged more with application.
“The majority of our research and development right now is tied to low VOC, waterborne and formaldehyde-free, acid-free acid cure coatings. And it’s been that way for quite some time.”
This article originally appeared in the May 2012 issue.
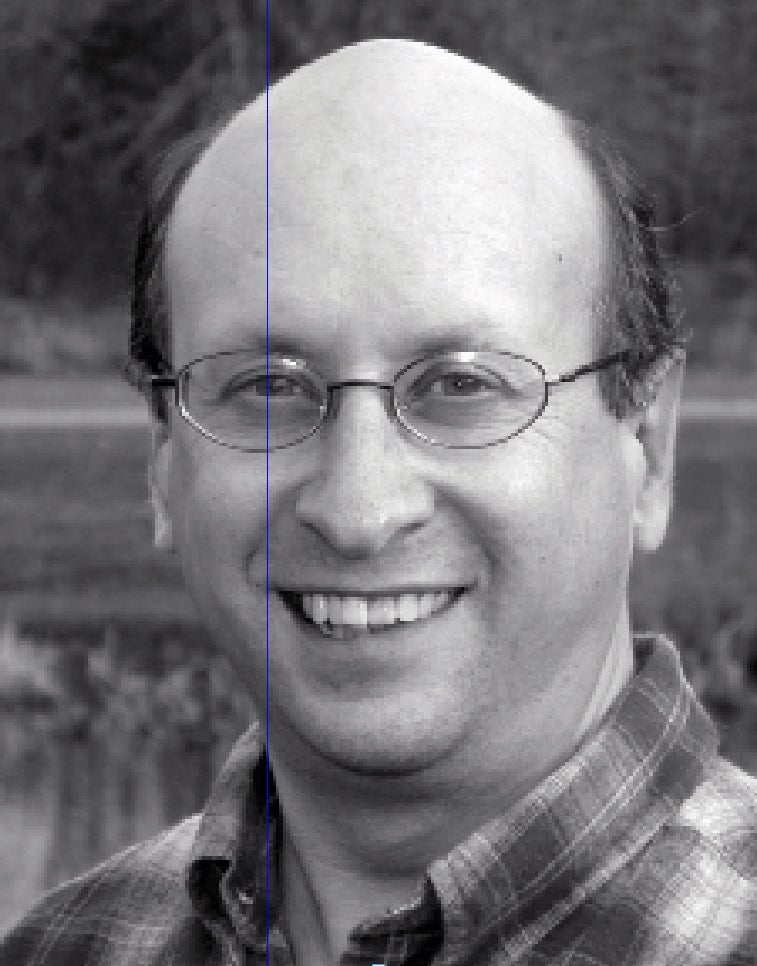