Hand-held sanders get better with age
It’s hard to believe, but hand sanders have been around for more than 90 years. The first one, which looked remarkably like a modern belt sander, was invented in 1926 by Art Emmons at the Porter-Cable factory in Syracuse, N.Y. Before his ‘Take About Sander’, according to the company, “workers
It’s hard to believe, but hand sanders have been around for more than 90 years. The first one, which looked remarkably like a modern belt sander, was invented in 1926 by Art Emmons at the Porter-Cable factory in Syracuse, N.Y. Before his ‘Take About Sander’, according to the company, “workers had to take the work to the tool, which proved to be laborious and time-consuming.” Despite hard times over the next decade as the country suffered through the Great Depression, “sales continued to grow as this portable unit helped carpenters, craftsmen and boat builders shorten month-long projects into just days.”
Mr. Emmons probably wouldn’t find it hard to believe that his invention is still going strong, but he might be a bit surprised at some of the turns it has taken.
Tool types
Among the latest evolutions in sanders is a tendency among manufacturers to make it easier to load sheets on partial sheet orbital finishing sanders (those are the ones with rectangular bases that take less than a full sheet of paper). Many of the latest models feature large, tool-free clamping, so it isn’t as big an effort to change paper as it used to be. Several models also come with through-the-pad dust collection, so they include a plastic punch plate that pops holes in the paper to facilitate collection. Orbital finish sanders are also getting less tall and that keeps a woodworker’s hand closer to the work, which offers more control and a better feel. Woodworkers sorting through the various options here should also look for a model with a reduced body size that is smaller than the pad, so the tool can sand right up against edges on projects such as flat panel five-piece doors. Also ask if various handles can be removed temporarily, to facilitate better access.
Orbital finish sander manufacturers are also including extra counterweights nowadays, and various other devices that reduce vibration through the handle. Less vibration, of course, lets us work longer without fatigue, especially overhead or on vertical planes. And the handles themselves are getting a lot more ergonomical, and softer, too. But it’s still a good idea to pick up several at the store and see what fits your hand. Some models also feature speed control, and this can be a real boon – especially on delicate surfaces when you’re using extra fine paper.
Speed control is also available on some random orbit sanders (those are the ones with round discs, which many of us just call palm sanders), and the no-load speed range can be anywhere from 4,000 to 12,000 or more orbits per minute (OPM). The actual orbit size varies, too. There’s quite a bit of difference in the swirl size from a 1/4” to a 1/8” orbit (smaller is finer).
Both types of sanders are generally available in either pressure sensitive (PSA, or stick-on) paper, or hook and loop versions, and some models come with both options. You can change the paper on the hook and loop ones faster, which is handy when you’re re-using grits. But be aware that on some less expensive models the H&L paper can move a hair, and that can effect control and also swirl marks. On highly critical jobs, PSA might be a better choice on cheaper tools.
Circular pads on random orbit sanders can’t reach in and clean up inside corners, so they’re not a complete solution to your sanding needs – but they come very close. Smaller discs can obviously handle more detail, while larger ones work well on wide surfaces. A 5” diameter model seems like a good compromise if you’re only looking at buying one type of random orbit sander so they all use the same size paper. You can then back it up with an oscillating/orbital tool. There are a number of manufacturers that offer sanders with pads that resemble the shape of the base of a clothes iron. These tools can reach into small places, and they can also sand a wider flat surface in a pinch, so they’re a great choice for the jobsite. Most are fairly narrow, so they’re also quite well suited to sanding face frames.
There are also some linear (in-line, also called stroke) handheld pad sanders on the market and these are ideal for working along the grain. But they can be a nightmare if the new guy doesn’t know that and sands across the grain.
Belt sanders also work best along the grain, and they are a great choice for removing a lot of stock very quickly. Some of the newer models offer windows, cut-outs or transparent covers so you can see whether the belt is tracking well. The better models offer one edge that can sand right up against a wall, with the dust collector on the other edge and well out of the way. Larger belts are not just wider, they’re usually longer, too. That means they sit better on a flat surface: there is more platen/support to stop any slight tipping. However, the trade-off is weight. Hauling a larger machine up flights of stairs on a jobsite, or holding onto it for long periods of time, can be wearying. You might also consider a variable or two-speed model, as that can also help enhance the operator’s control.
Several manufacturers offer long, thin belt sanders (3/8” or 1-18” wide), and some have a pivoting arm that can reach into all kinds of very tight spots. They’re generally variable speed and very lightweight, and the pulley at the tip acts as a platen so the end of the belt can be used to sand inside curves and irregular profiles.
Accessories
When you buy a hand-held random orbit or orbital finish sander, look into purchasing at least one foam or felt platen (backing) pad, too. Unfortunately, manufacturers sometimes discontinue models and it can become impossible to find a replacement for a worn pad. The aftermarket ones are sometimes of lesser quality, fit poorly, and are either less or more dense. If they’re softer, the edges of the pad will compress and wear quickly while the center stays ‘fat’. If they’re harder, they can cause a little burning and also wear through the edges of the paper. Having a couple of inexpensive spare pads on hand can add years to the life of the tool.
It’s a simple thing, but look for a sander with a rubber boot over the switch: it keeps dust out and helps the switch last longer.
Dust canisters on many models have improved, too, and several now feature a small filter that scrubs the exhaust air before returning it to the shop. The old bag with a zipper seems to be on its way out. Some canisters are see-through (finally!), so one can instantly check on how full they are. Many can be removed and replaced with a shop vacuum hose for better dust collection.
Some variable speed sanders that offer a very low speed range are set up so that the abrasive head can be changed out for a polishing head. That’s usually reserved for metalwork, but wood-turners also like to polish some oily species such as African blackwood, and the lathe speed combined with the polisher can deliver quite a sheen.
For most handheld sanders, but especially the cordless models, you might want to see if the manufacturer offers a case or bag that will hold the tool, batteries, charger and paper.
Power sources
Electric razors came out a long time ago with a combined hardwire and battery setup, where you could plug it in or go cordless. The sander manufacturers are finally getting to that point. The delay was battery technology: it takes a lot more juice and time to sand a board than to shave a chin. And we also had to wait until the batteries were small enough (weight-wise) to hold and carry them all day, yet strong enough to last at least an hour between charges. 18-volt packs are the stepping off point here and some manufacturers already offer larger power packs. It’s pretty obvious that larger, longer-lasting batteries will become the trend. Brushless motors also help, as there is less resistance. Look for a power pack that lasts longer than it takes to charge, so that just two batteries will carry you through a full day of work. With hybrids (corded and cordless) that isn’t an issue, but we often find ourselves on jobsites without power, and that’s a consideration.
In the workshop, pneumatic sanders are a viable option if there is a large volume of compressed air available. They’re usually not a great option on jobsites, as most models will drain a small portable compressor very quickly. There are a few small detail sanders that work well: check out automobile finishing catalogs for a lot more variety in air tools than woodshop suppliers tend to offer.
This article originally appeared in the October 2017 issue.
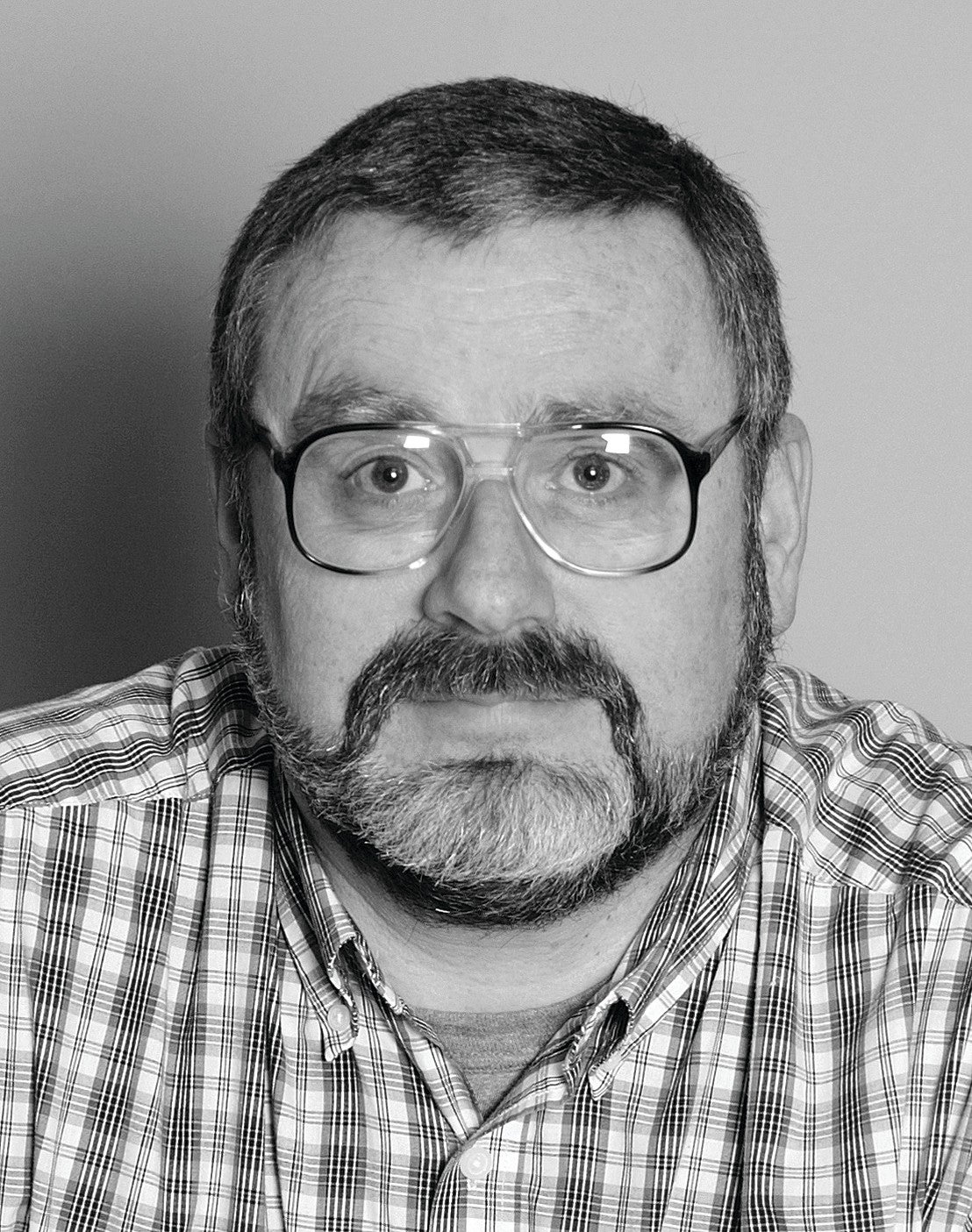