How to buy hardwoods
The process begins by learning the grading rules and sawmill jargon.
Custom woodshops generally buy hardwood inventory by the job, while furniture manufacturers purchase by the truck, or even by the trainload. The difference in scale affects aspects of the transaction such as discounts and delivery charges. But both buyers share a number of guidelines related to the condition, cut and grade of the wood.
A woodshop owner who is considering a move from lumberyards (or perhaps a small local mill) to buying from a distributor might first want to spend a few hours learning those guidelines. That’s easily done online by visiting some of the organizations that set the rules and practices that govern the industry.
Industry groups
Based in Memphis, Tenn., the National Hardwood Lumber Association (NHLA) publishes its “Rules for the Measurement & Inspection of Hardwood & Cypress” every four years. This is the industry handbook, and it can be previewed at nhla.com/industry-services/rules. It tells a buyer how the distributor grades, cuts and sells hardwoods.
The Cabinet Makers Association (cabinetmakers.org) includes hundreds of small- to medium-sized cabinet shops, millworkers and furniture makers and suppliers. In the Materials & Supplies section of its membership directory page, a shop owner can find some of the national hardwood suppliers and contact them to find local distributors. And as a member, you can contact other shops and learn from their buying experiences.
The National Wood Flooring Association, online at nwfa.org, is a must visit for any woodshop owner who is buying hardwoods to mill solid wood floors. The site offers education and marketing resources, as well as ways to connect with other shops already buying hardwoods.
Another solid resource, especially for shops building casework, is the Architectural Woodwork Institute (awinet.org). This body publishes industry standards that are intended to give installers, manufacturers, and suppliers some guidelines regarding materials selection and use. This is a good time to stop by the site, as new standards were published on Mar. 15.
The Woodwork Institute (woodworkinstitute.com) is a similar organization that also publishes guidelines in its book, “North American Architectural Woodwork Standards”.
The Furniture Society (furnsoc.org) is a great way to network with other hardwood buyers, especially for smaller shops. And the Forest Products Society (forestprod.org) is the world’s largest network of wood professionals. Shops using imported wood might also want to visit the International Wood Products Association (iwpawood.org).
Choosing hardwood species
This choice involves aesthetics (color and grain patterns), durability and workability. The aesthetic factors are essentially subjective: everybody has their own favorite species and cut, and your customer will probably make the choice for you anyway. You can, of course, influence that choice by showing only samples of hardwood that you would like to use or buy. Be aware that shops buying from a different geographical location through an online distributor can be surprised by the effect that minerals in soil, or the length of the growing season, can have on hardwood. Red oak can run the gamut from almost pale to scarlet or brown, and the grain patterns can be quite different between, say, trees that grew in Canada and Georgia. So, the sample you show the client may need updating.
The most durable (physically hard) domestic species, according to the USDA, are hickory, pecan, hard maple, white oak, beech, red oak, yellow birch, green ash, black walnut, soft maple, cherry, hackberry, gum, elm, sycamore, alder, yellow poplar, cottonwood, basswood and aspen, in that order.
Wood density is measured as weight per cubic foot, and it has a strong relationship to the hardness of the stock. In the industry, this is expressed in terms of specific gravity, which measures how the weight of a cubic area of a certain wood species compares to the same volume of water. If water has a specific gravity of 1.0, then wood with a rating of less than 1.0 will float, and more than 1.0 will sink. But density is only one characteristic of many to keep in mind when considering the workability of a species. Ask the supplier, and other woodworkers, how the local variety sands, cuts, planes and shapes. And it’s always a good idea to visit local sawmills and talk about what’s popular in your region, and why. The sawyer will often know more about the characteristics of the species that pass through his mill than most of the experienced woodworkers around, simply because they see and cut more species.
Straight boards with uniform grain patterns are easier to work with. But windblown, burled trunks can deliver lots of figure, and this can be used in smaller areas (panels, drawer fronts) to enliven the boring, reliable, well-behaved wood. Some species are prized for their natural defects such as burls, insect damage, water damage and so on. Irregular grains such as fiddle-back or bird’s-eye are beautiful to look at but can be rather difficult to work. The key is perhaps to progress from straight grain to figured stock at the same rate that your woodworking skills evolve. If you’re buying burl hardwood from a sawmill, do some research on how to dry it as the errant grain patterns can do some serious cracking and moving once the confined internal strains are released. Woodturners seem to know most about burls, and their organization is the American Association of Woodturners (woodturner.org).
On larger projects, it’s often possible to buy flitches, which describes the boards, or veneers, that make up a log. The word is actually more widely used to describe the dozens of layers of thin veneer that make up a log. Buying a flitch means that color and grain can be matched more easily, so that adjacent panels look similar. And it also opens the door to book-matching panels.
Anatomy of a board
At the center of the tree is the pith. This was once the sapling, and each year it wrapped itself in layers of new growth (the annual rings). Trees expand not by enlarging their cells, but by adding new ones. The rich heartwood at the center of a living tree is already dead, and the usually lighter colored sapwood at the edges is a conduit that brings water and nutrients from the ground to the leaves.
There is an area next to the sapwood called the cambium layer. It’s composed of phloem, cambium and xylum, and this is the part of the tree that grows. Phloem is a short-lived layer that passes large amounts of food to the rest of the tree. Cambium repairs injuries and creates new growth, and xylum circulates water and dissolved minerals. For natural (or ‘live’) edged hardwood furniture, this is usually the area where a woodworker wants to end up. Beyond it is the outer bark, which is difficult to keep intact and in place, so it is almost always discarded.
Annual rings are each made up of a wider area of earlywood (spring and summer growth), and a thin area of latewood (fall growth, that usually has a darker color).
There are three primary ways to saw a log – plain, quarter and rift – and each produces very different boards. Plain sawing is the most common, most economical and least stable cut. It’s what you see in the big box stores – cathedral grain with arcs in the middle and tighter lines along the edges. Quartering can yield very stable boards with tight, straight grain and minimal movement. It is, however, a little wasteful. In some species, most notably white oak, this cut also delivers a ribbon-like effect called flake that is a result of slicing through medullary rays that run between the pith and the bark, carrying small amounts of nutrients. Rift is an architectural cut that can cost a lot, and it’s difficult to find a sawyer who knows how to do it well. The advantage is stability with more interesting patterns than quartered stock.
Some species work better with different cuts, and that’s a conversation to have with your salesperson.
Hardwood rules
The NHLA has created guidelines for grading hardwood. But be aware that a lot of small suppliers make up their own grading system, and that’s actually legal because the NHLA isn’t a government body so it has guidelines, not laws.
You may still need to add some specs of your own when placing an order. For example, if you just ask for FAS cherry, you will get a mix of heart and sapwood in random widths. If you need all heartwood in 7” wide boards, you need to tell the supplier, and pay a premium. For details on the various grades, download the NHLA guidebook.
Hardwoods are measured sawn but not yet planed, and this is called “rough”.
The standard hardwood unit of volume is a board foot, which is 144 cubic inches. Multiply the three dimensions of any board (thickness by width by length, in inches) and then divide the result by 144, and you’ll know how many board feet you have.
Hardwood thickness is measured in quarters. There are four quarters in a 1” thick rough sawn board. That is described as 4/4, which is called “four quarter”. 5/4 is 1-1/4” thick in the rough, 8/4 is 2” thick, and so on.
The distributor will sell you hardwood that is rough, or completely dressed, or anywhere in between, depending on how much you want to spend. S2S means that a board is planed on two faces, but the edges are not straight. You can usually have the supplier rip one edge straight (straight-lining). The most expensive process is planing on both faces and both edges (S4S), but few professionals go this route as they need to sand or plane after gluing up panels. It’s best to have just one edge straight-lined and leave the other natural so that the boards are at random widths. That way, you can run boards against a fence back at the shop and cut them to custom widths.
After initial hit-and-miss planing, 4/4 stock is usually 13/16” thick. That is just right if you’re edge-gluing boards and want to plane them to 3/4” after the glue cures.
When you bring dried lumber back to the shop, let it sit for a few weeks if possible, to acclimate to the ambient humidity. This will reduce the amount of movement after your project has been assembled.
Some suppliers measure the board feet of straight-lined lumber and then add an allowance for the waste that they removed. This isn’t a labor charge, but a fee for wood you don’t receive. A more correct practice would be to sell a certain number of board feet in the rough, and then charge the customer for labor if he/she wants it straight-lined. And it can be very surprising to buyers how much a sawmill operator might slice off a board when straightening one edge: most woodworkers would perhaps be more conservative.
A tally will often be rounded off to a full board foot (7.9 becomes 8, for example). Be wary of a supplier that always rounds up. You deserve to have equal treatment: if the fraction is less than half, they should be rounding down. A gross tally is rough lumber before milling, and a net tally is what you actually get after processing.
The bottom line on buying hardwood is that the vast majority of suppliers are far more concerned with making a customer than a single sale. It’s in their interests to treat you well. And it’s in your interest to know their rules before you buy.
John English is the author of “Harvest Your Own Lumber”, available at www.woodworkerslibrary.com.
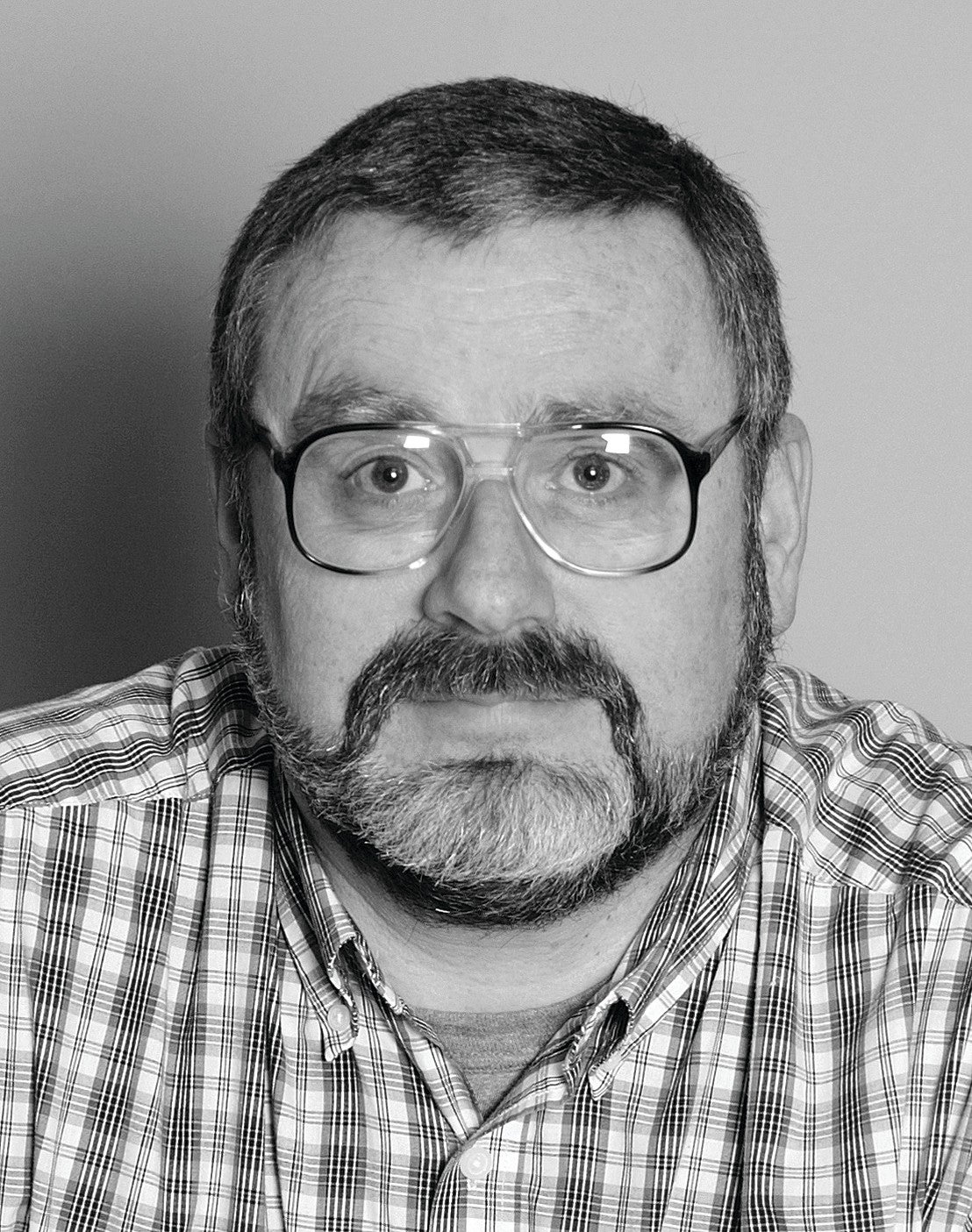