Take a load off: Use machines for moving
Man and machine — these are two areas of concern when handling materials in the woodshop. First, a manager needs to train people to lift properly so they avoid injury….
Man and machine — these are two areas of concern when handling materials in the woodshop. First, a manager needs to train people to lift properly so they avoid injury. Once that’s done, he or she can take a look at various machines and mechanical aids that help an employee lift and move parts or projects around the shop.
When it comes to people, it’s a good idea to include proper stance and lifting technique in a shop orientation session. Back problems account for more than one-third of workplace injuries each year (there are about 400,000 accidents nationwide) and, once they happen, a lot of them tend to linger on for years. The first step, according to most training programs, is to convince your people to think before they grab. They need to take a few seconds to figure out a path, find a good grip and decide whether or not they’ll need help. If more than one person is involved, they also need to make sure everyone is on the same page before anything leaves the ground.
The key to avoiding injury is to keep the weight close to your body. If you have to reach out, your stance will be less stable. Feet should line up with shoulders: if they’re too close together you’ll have to take a step under the load to correct your balance and if they are too far apart you won’t be able to take that step. Speaking of steps, take small ones when carrying something heavy.
Here’s the most important rule: bend your knees to raise and lower the object and keep your back as straight and vertical as possible. The muscles in your legs are far, far stronger than those along your spine, so just let them do the heavy lifting. And don’t twist at the waist. If you need to turn, do it with your feet and not your vertebrae.
There is a very good guide to workplace lifting techniques on the OSHA website (www.osha.gov, Pub. No. 2236). It’s basic common sense, but can help a shop manager really think about how his or her employees are exposing themselves to injury during simple tasks such as loading plywood onto a CNC bed or placing a cabinet on a cart. Spending a few minutes training is better than spending months or years paying for an injury or having to watch somebody on your team suffer through pain that could have been avoided.
Mechanical solutions
If a machine can take the risk, let it.
Machines don’t need to see a chiropractor too often. They also don’t need to cost a fortune. Most lifting in a woodworking shop is more awkward than heavy. A forklift can handle big items such as bunks of hardwood and pallets of plywood and those are generally not the problem areas. Moving materials between workstations or loading them for delivery tend to be the high-risk zones for injury. When it comes to pallet jacks and platform carts, OSHA says that “pushing is generally preferable to pulling. Pushing allows the employee to use large muscle groups and apply more force to the load. Pulling carries a greater risk of strain and injury.”
Good staging is important, too. This includes placing materials as close as possible to where they will be needed and storing materials at ideal heights to minimize bending and awkward lifting. OSHA also advises that task rotation can be an effective way to limit each employee’s exposure to risk, so don’t let the same guy do all the lifting.
Manual scissor-lift carts are relatively inexpensive (ranging from roughly $300 to $1,300) and can remove much of the lifting from material handling. They reduce it to turning a crank or working a foot pump and then sliding the object onto a machine or workbench once it is high enough. Baileigh Industrial offers a single-arm hydraulic lift cart with 660 lb. capacity and 30” maximum height for $295 (item No. 1000578). The table size is 32.2” x 20.4” and that larger dimension will work for a base cabinet carcass. A 48”-high option (item No. 1000579) sells for $495. And U-line offers a 36” x 20” platform (model H-1784) for $619 that can lift up to 770 lbs. and has a hydraulic foot pump and polyurethane casters.
If you’re searching online, other manual scissor-lift cart manufacturers include Dayton, Southworth, Dandy Lift, Bishamon and Wesco.
Motorized carts cost a lot more than manual ones. A battery-operated Vestil brand cart from Grainger (item No. 3EB99) runs $2,775 and will handle 1,000 lbs., which is the equivalent of about a dozen sheets of 3/4” MDF. The only problem is that the bed is only 24” x 48”, so the load needs to be centered on that. The battery raises and lowers the platform up to 42-1/2”, but moving the cart is still done by manually pushing it along on its casters.
Vestil offers a motorized material-handling cart (not a scissors lift) with a 24” x 60” deck and an electric power plant. Model EMHC-2460 is listed at $1,999 and can handle 1,100 lbs. of cargo. There’s also a folding-table cart made by Sandusky (item No. DO102172TA-02) that can handle sheet goods, selling for less than $200.
Vestil also makes a tilting work truck (item No. TWT-2448-M) that holds up to 500 lbs. and can really save stress on a worker’s back. The platform is 2’ x 4’ and comes in either a mesh or a solid-steel version ($198 and $225, respectively). The large, solid-foam wheels can make a journey across the shop a little easier to push. It’s less bumpy than casters and the tires won’t ever go flat.
For jobs where a small number of different parts need to be moved from one workstation to the next, a nesting utility cart might be a good solution. These are basically platform carts with more than one platform and, while their original function was to simply save floor space, they are ideal for separating similar parts such as drawer sides and ends. A good example of a nester is the Model 33R from VersaCart, which is actually a manufacturer of retail store shopping carts. The 33R’s retractable upper shelves offer four different cart configurations and it can carry up to 470 lbs. The cart folds and nests in a 7.87” deep space when not in use and can also be outfitted with a bin container system instead of flat shelves. And its large, 5” diameter heavy-duty wheels with steel roller bearings make for great maneuverability in tight areas between machines and workbenches.
Innovative solutions
For high-volume woodshops and component suppliers, technological and pricing advances in the last decade have made material handling robots an option worth considering, especially when duplicates are being built such as hospital or school casework. A good place to start a search for these kinds of resources is the Robohub website (www.robohub.org). Based in Switzerland, Robohub is a non-profit site that brings together experts in robotics, business and education from across the globe. The organization is “dedicated to providing free high-quality information for the robotics community and the general public.”
For a much less technical solution to moving things around the shop, a small company based in Tustin, Calif., might have just what you need. Nimble Scooters makes the Nimble XL, which is a heavy-duty industrial warehouse scooter. For a shop that needs to run drawer slides or portable power tools around the facility, this will certainly speed up delivery times. It can also be converted to a handcart and sells for about $600.
A new cart from Handtrucksrus.com looks like it could be a real boon to casework installers. Called the Ground Glider (model R18RT), it sells for about $300. The cart transforms into any one of eight different configurations to move cabinets and components around the shop with ease. It has 3” wide x 8” diameter front casters with brakes and 3” x 10” rear wheels. The tubing on the cart is beefed up to carry larger loads (up to 700 lbs.). What is really nice about the cart is that it extends from 42” to 60” and weighs only 37 lbs.
This article originally appeared in the December 2015 issue.
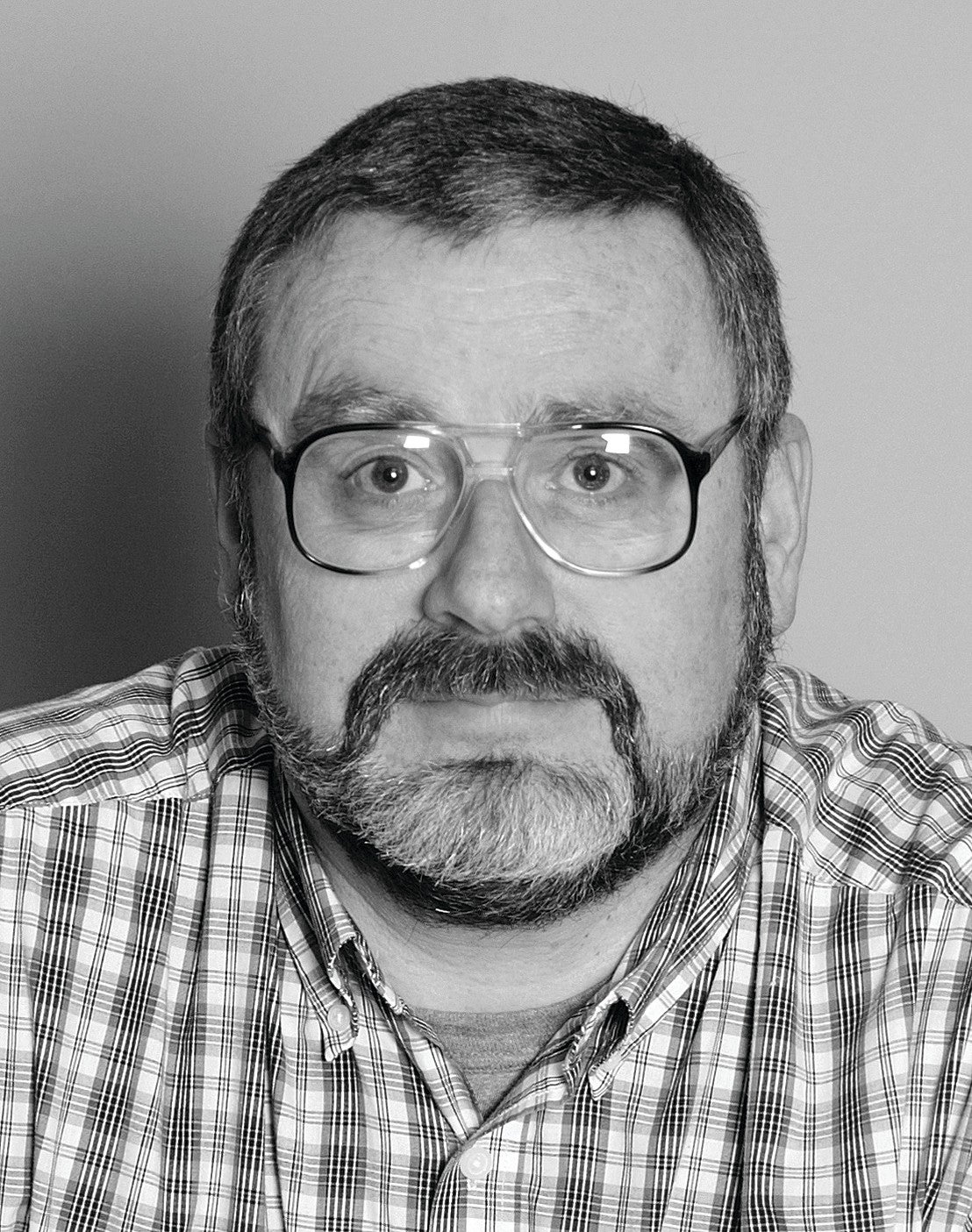