That extra touch
New materials and accommodating suppliers open up new opportunities for woodshops installing decorative panels and countertops.
The first impression a potential client has on walking into a custom shop’s showroom is one of color. Whether the casework is wood grain or foil, paint or laminate, one’s other senses initially play second fiddle to sight. But as people walk closer to new cabinets, almost everyone does the same thing.
They reach out a hand. They brush the surfaces.
They need to touch, to physically feel, before the experience is real.
That tactile aspect has always been a part of natural products, where grain patterns subtly telegraph through lacquer. Fingertips trace the crown of plainsawn grain such as red oak or hickory, or perhaps follow the fumed formality of quarter-sawn white in a Stickley piece.
They feel the wood.
Today, fewer than half the cabinets being built are wood grain. And when one looks at the new walls of color in kitchens, there is often a very brief hesitation before those fingertips reach out. But when they do, customers are almost universally pleased – albeit quite often subconsciously – to learn that there is still a tactile reward. In fact, some of the newer panel products available to custom shops deliver this sensation with gusto.
Textured panels
Roücke HD from the Denver-based manufacturer Premier EuroCase (premiereurocase.com) is a high-definition panel made with the deepest structured melamine, so it has the decorative texture and appearance of real wood grain. But it also has the strength and endurance required by today’s high-end consumers, according to the company. Roücke HD panels are ideal for residential use in cabinets and furniture, and they’re also strong enough for store fixtures and displays. The panels come in 12 woodgrain patterns and three solid colors, with perfectly matched laser edge-banding and no glue lines. Full sheets (4’ x 8’) are available in 1/4” MDF and 3/4” particleboard, and finished door and drawer components are also offered.
Premier EuroCase also provides matching vinyl material in most colors. With one of the industry’s fastest lead times (just five days for standard orders with no minimums), the company stocks more than 90 surface products including in-house lines such as the high gloss Reflekt plus a decorative high-gloss film called Ion that has the stylish appearance of brushed metal, and the most scratch resistant acrylic on the market, UltraMatte.
For shops that are searching for GreenGuard compliance in a textured panel, StevensWood has just added three new surfaces to its Legno collection. This is a family of dual-sided, elegant materials with texture matched grains that already come in a wide range of wood-like finishes. The new arrivals are Walnut Pittoni, Mezzo Cherry and Trento Oak, and they share standard Legno characteristics such as a high impact surface, the textured feel of three-dimensional vinyl, and matching edgebanding, moldings (including crown), and availability as five-piece flat, raised panel or Shaker-style butt or miter frame doors, one-piece slabs and three-piece doors. Two-sided panels are available in 5’ x 8’ sheets from 1/4” to 1-1/4” thickness. The company, online at stevens-wood.com, only uses materials that are 100-percent recycled and recovered, or GRN+ non-added formaldehyde core materials. For a more dramatic texture, take a minute to look at the Artika & Rain collection, too.
Also GreenGuard certified, the catalog of panel products from Decotone Surfaces (decotonesurfaces.com) offers woodshops a huge palette of texture, color and design. Among its offerings are solid color, wood grain, stone and pearlescent decorative laminates, with more than 250 designs to choose from. There are also more than 90 metallic choices plus over 50 translucent options, and even 30-some wood veneers. Decotone even offers aluminum tile in a custom design created by Fabrice Covelli. And for those specialty projects, where a shop needs sheet stock for very specific installations, the company carries chemical resistant, solid core, antibacterial, custom digitally printed, thick partition and even chalk and marker-board laminates.
Speaking of veneer, GL Veneer (glveneer.com) in Huntington Park, Calif., supplies some 200 species from afromosia to zircote as flexible veneer sheets or architectural plywood panels. For accents, or perhaps as a dramatic countertop to complement veneer panels, GL also stocks about two dozen species of live-edge slabs in species such as Claro walnut, willow and acacia. And here’s something that any designer looking at panels will love – Wallwood, which is literally wallpaper made of wood!
Need to build curved panels? Kerfkore (kerfkore.com) has been showing the industry how to do just that since the mid-1980s. Today, the company offers environmentally-friendly bendable substrates and lightweight structural composite panels for architectural needs, shelving, partitions, ceilings, columns, wall systems, signage, displays, theatre props, swing doors, elevators, kiosks, movable food carts, table tops, furniture, cabinets, motor homes, boats and virtually any other bentwood application a woodshop needs to address.
Another creative way to use panels is to surround them with cost-effective, architectural-grade aluminum trim. Shops looking for wall and panel options for commercial spaces might want to stop by the Monarch Metal website (monarchmetal.com) and check out the options. The company essentially offers panel fabricators the flexibility to manufacture their own wall panels, and then choose from a variety of off-the-shelf, popular aluminum trim options for 3/8” and 3/4” material.
Rock solid
New panel concepts such as these allow woodshops to meld the ancient art of woodworking with the color palette, endurance and workability of modern materials. They also allow cabinetmakers to employ looks that are distinctly not wood, such as the genuine but lightweight stone veneers made by EA-Stone Group (ea-stonegroup.com) in Wadsworth, Ohio.
The company makes granite, marble, travertine, slate, sandstone, onyx and even concrete veneers that can be worked in the woodshop and lend the architectural integrity of genuine stone to casework. The resulting hard, durable, stable surface resists impact, abrasion, temperature extremes and open flames. It comes in a wide variety of backing material, from paper-thin to a honeycomb, and can be used vertically or horizontally on almost any woodshop project from cabinets to doors, fireplace surrounds and backsplashes.
EA-Stone Group provides veneer in every format from raw material to fabricated products, cut to size material, and full stone product such as shower surrounds. The company offers fabrication services on a variety of millwork, steel, glass and other substrates, and has in-house CNC, waterjet, laser and large format printing capabilities.
When stone is harvested from quarries all over the world and brought to the EA-Stone Group facilities, it is split into thin book-matched sheets. The veneers range from 1mm to 4mm thick, before being applied to backers that keep the product lightweight, flexible, durable, and impact resistant. For example, Universal Stone Panels have 3mm of natural stone and a 3mm aluminum composite backer, creating sheets that come as large as 60” x 102” – and still only weigh an average of just 2.6 lbs./sq. ft. The stone veneer panels can be cut and fabricated dry with minimal tooling, making them an easy addition to any woodshop or they can be cut and fabricated wet with traditional diamond tooling.
Countertops
Outsourcing stone countertops on an install can be a painful experience, as woodshops watch a subcontractor collect those lucrative sales. That’s especially true for shop owners who once made all their preformed laminate and solid surface tops in the shop. And while the skills have always been available to keep this aspect of the business in-house, the tooling and machinery wasn’t there to accommodate the influx of stone. It’s hard to mill granite on a CNC that’s set up for MDF.
But times and tastes are changing, and a return to more malleable materials in counters is opening up some new possibilities. Unsightly edge treatments were one of the stumbling blocks that invited the masons into kitchens, and there have been some advances of late in that area. Take, for example, Northway Industries (northwayind.com) in Middleburg, Pa. The company offers an entire range of edging options including 3mm PVC, 3mm polypropylene, unfinished or pre-finished internal wood (where the edging is essentially a frame around the substrate, under the laminate), and pre-finished external wood which is a molding attached to the edge. Northway fabricates a large variety of tops and work surfaces with square or round corners and free-form shapes, and with fourteen CNCs, the latest robotics and a laminating line, the factory can accommodate custom finishing, tight joint seams, cut-outs and hardware mounting. Or it can lay up panels and let a woodshop do the detailed work.
Speaking of detail, there’s one more panel supplier that any creative shop owner or designer absolutely has to visit. Stop by the Art for Every Day website (artforeveryday.com) and click on products. Then scroll down to ‘Panels’ and let go. What greets you next is a mind-blowing display of architectural panels that… well, you’ll just have to go there.
This article originally appeared in the April 2019 issue.
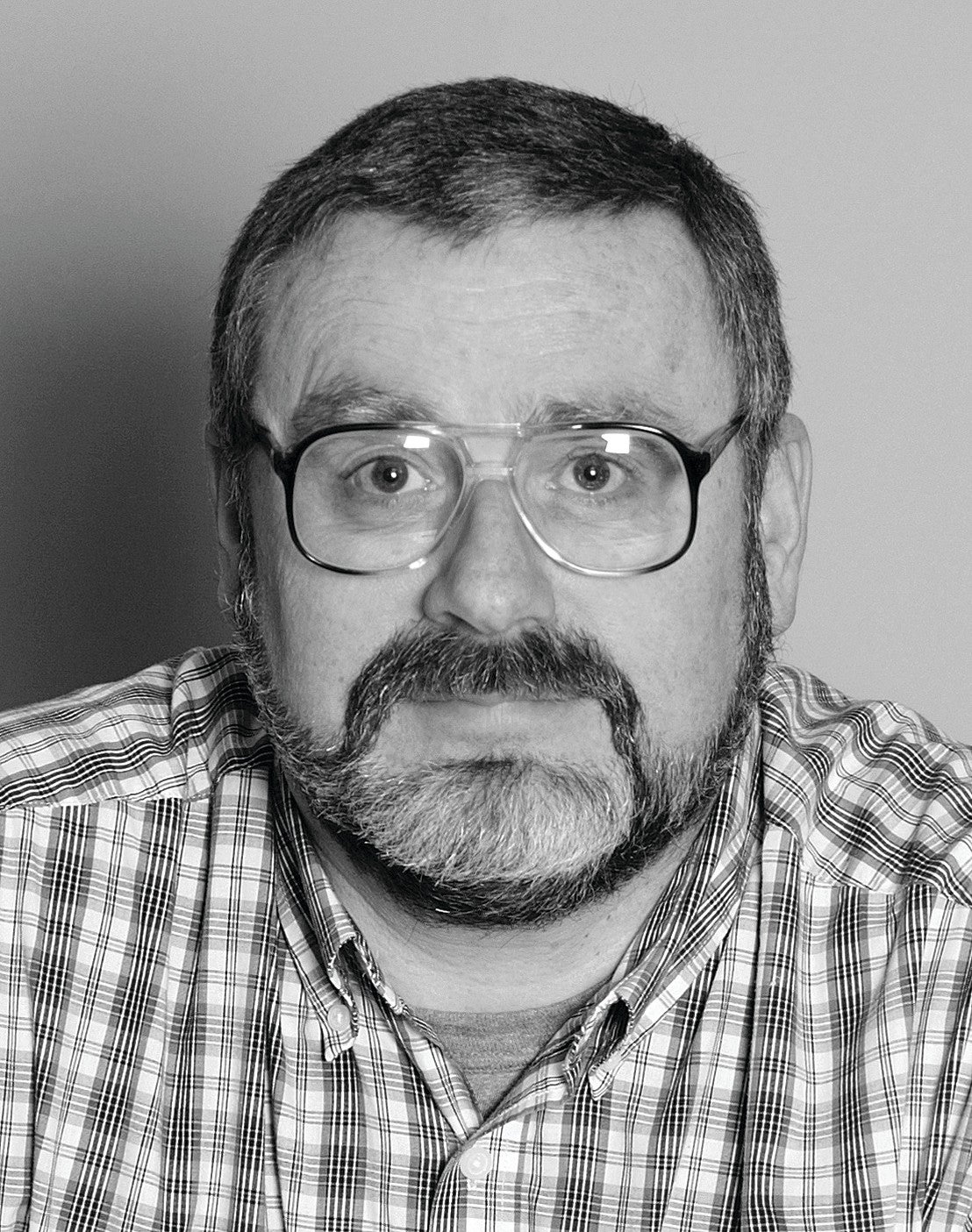