Vacuum Pressing
Vacuum pressing is a scalable skill that can help a shop offer flat, curved, and decorative options.
The best way to make a sheet of veneer or thermofoil lie flat, expel air, and conform to curves and profiles is to use a vacuum bag or a press. This method can deliver about the same pressure on a cabinet door as parking your pickup truck on it. And getting set up to do that can be surprisingly inexpensive for a small shop that has time to do one door at a time. As the numbers expand, there are automated solutions that can vacuum press multiple doors or panels simultaneously.
Vacuum pressing is a scalable skill that can help a shop offer flat, curved, and decorative options that can quickly upgrade its catalog.
Darryl Keil, the president of VacuPress (Vacuum Pressing Systems, vacupress.com), shop-built his first vacuum press in response to a client’s request for a large veneering job. After studying the options and considering the expense of purchasing a large industrial press that might never justify its cost, he built his own. It performed far beyond his expectations.
“Not only could the press do flat work,” he says, “but curves and shapes were almost as easy and allowed us to offer our clients a whole new level of design choices.”
Keil’s website describes the process of vacuum pressing in a concise and informative manner: “When air is removed from a closed vacuum bag containing a veneering or laminating project, two things happen. First, as the vacuum is created, atmospheric pressure bears down on the work inside the bag with perfect uniformity and enormous pressure. Second, as air is drawn out of the cells in the surface structure of the wood, glue is sucked into these cells.”
There’s an adage that says a shop can never have enough clamps, but a vacuum press may be the exception that proves the rule. This single tool can do a better job in many cases than a whole rack of clamps and cauls. For a start it’s fast, so the woodworker doesn’t need to worry so much about the glue’s open time. Second, the pressure is applied far more evenly than a series of clamps could ever achieve. And it’s not just for veneering. The same system can be used to hold all kinds of shaped or flat parts together while the adhesive sets and begins to cure. For example, it can be used to laminate thin layers of contrasting species to form architectural accents, musical instrument parts, marquetry, or curved cabinet doors.
Small and medium options
Vacuum forming is relatively simple and requires a clear plastic bag, a vacuum pump, some tubes, and a control valve. Taking that to the next level, in a vacuum press the bag is replaced by a sheet of flexible plastic (a membrane) that is secured in a rectangular frame and hinged to a table. The edges of the frame are sealed with a gasket. A woodworker creates a sandwich that contains the substrate plus the veneer or other lamination, an adhesive between the two, and sometimes a pair of platens if the assembly is flat. The platens are usually plywood or even MDF with a gridwork of saw kerf grooves cut into one surface that allow the air to be sucked out more efficiently.
The difference between the bag and press methods is that the bag surrounds the entire ‘sandwich’, while with the hinged press (also called a table or frame), pressure is applied to the top surface and the table provides resistance The table method can be physically easier to handle for an operator if the bottom face of the sandwich is flat, as in cabinet doors.
Keil’s company, VacuPress, offers pumps, bags, table presses, glue, supplies, tools, and – most important for anyone just getting into vacuum pressing – lots of information.
For small shops that only occasionally need to veneer, the wood veneer source can often supply everything that’s needed. For example, Veneer Supplies (veneersupplies.com) in Forest Hill, Md. is a small family-operated business that has the simple goal of getting “vacuum pressing parts and exotic wood veneer into the hands of hobbyist woodworkers and small-shop craftsmen”. In addition to press parts, plans and supplies, the company offers more than a quarter of a million square feet of veneer through its website, plus a free DIY vacuum press plan.
Quality Vakuum Products (qualityvak.com) in Hudson, Mass. provides woodshops with free-standing and wall-mounted frame presses, bags, tape, hose, vacuum pumps (both pneumatic and electric powered), glue, worktables, and a selection of accessories such as rollers and spreaders. The catalog also includes a variety of clamping jigs and vacuum line connectors.
Highland Woodworking (highlandwoodworking.com) supplies a variety of pumps, tools, bags and even a tint for laminating glue that helps make glue lines less noticeable.
Veneer Systems (veneersystems.com) is a full-service supplier of veneering supplies, tools, and presses. The company also offers the Zig Zag splicer that obviates the need for veneer tape. The splicer applies a glue thread to the back face of the veneer.
Rockler (rockler.com) carries the Roarockit 26” x 28 Thin Air Press Vacuum Bag with a hand pump for $65.95. Rockler also sells an adapter that lets a shop attach an electric pump.
Smartech International (smartechonline.com) brings “the precision of German design” to its reusable industrial vacuum bags. The company points out that bags must be able to withstand normal handling at layup and not wrinkle. They need to provide a complete seal and conform to the deepest channels in a part, so Smartech uses silicone materials that can sustain perfect negative pressure and withstand temperatures of nearly 400 degrees Fahrenheit.
Bags are critical, but so are pumps. For woodshops exploring medium or high-volume solutions, a good place to visit is Busch Vacuum Solutions (buschvacuum.com). To give some idea of their expertise in this field, the company supplies six different kinds of vacuum pumps. The headquarters in Virginia is home to a state-of-the-art vacuum pump manufacturing and system building facility, along with a service center that provides pump repair and remanufacturing.
Castaly (castaly-cncmachine.com) offers a range of single- and double-stage vacuum pumps, plus a dry rotary vane vacuum pump.
Industrial solutions
Vacuum pressing isn’t just for thin veneers. By adding heat to the vacuuming process, all kinds of plastic materials can be shaped and formed. For example, SchultzForming (schultzform.com) in Carlsbad, Calif. offers a pair of solid surface vacuum formers. These machines can form materials such as Corian into many different shapes. The larger model, the SSVF12, can handle a full sheet, and its frame opens up to 28” to accommodate tall projects.
Black Bros. Co. in Mendota, Ill. (blackbros.com) manufactures a complete line of laminating presses including the ThermoFormer, which is among its top-selling 3D laminating (thermofoil) presses. The company notes that a vacuum press is frequently the ideal solution for smaller companies because of its economical pricing and flexible productivity.
Burkle North America in Greensboro, N.C. (burkle.tech) offers a number of industrial volume vacuum pressing solutions including a high-performance through-feed press line for veneering furniture components, with an automatic board and veneer lay-up system.
Evans Midwest (evansmidwest.com) manufactures an industrial line of 3D shuttle and clamshell style laminating presses for a wide range of industries. Its products are also available through Choice Machinery (choicemachinerygroup.com) in Holland, Mich.
For large-scale production, Italpresse (italpresse.com) in Punta Gorda, Fla. makes presses for wood-based panels, doors, windows, and wood components.
Sometimes a woodshop has a production run of profiled parts that need to be veneered, and there isn’t enough time or money in the budget to set up a vacuum press in-house. There are some options for outsourcing, such as Accuwrap in Ontario (accuwrap.com), which offers custom profile wrapping.
In between large production lines and one-off door vacuum pressing is the Cyclone 4896 from CNC Factory (cncfactory.com). This thermofoil press is a mobile vacuum membrane machine that has an automated heating, vacuum forming, and cooling process, plus a small footprint so it doesn’t impede the shop’s workflow. The press has automated shell opening and closing, and there’s a full, unobstructed 48” x 96” working table and one-button digital PLC monitor.
This article was originally published in the July 2022 issue.
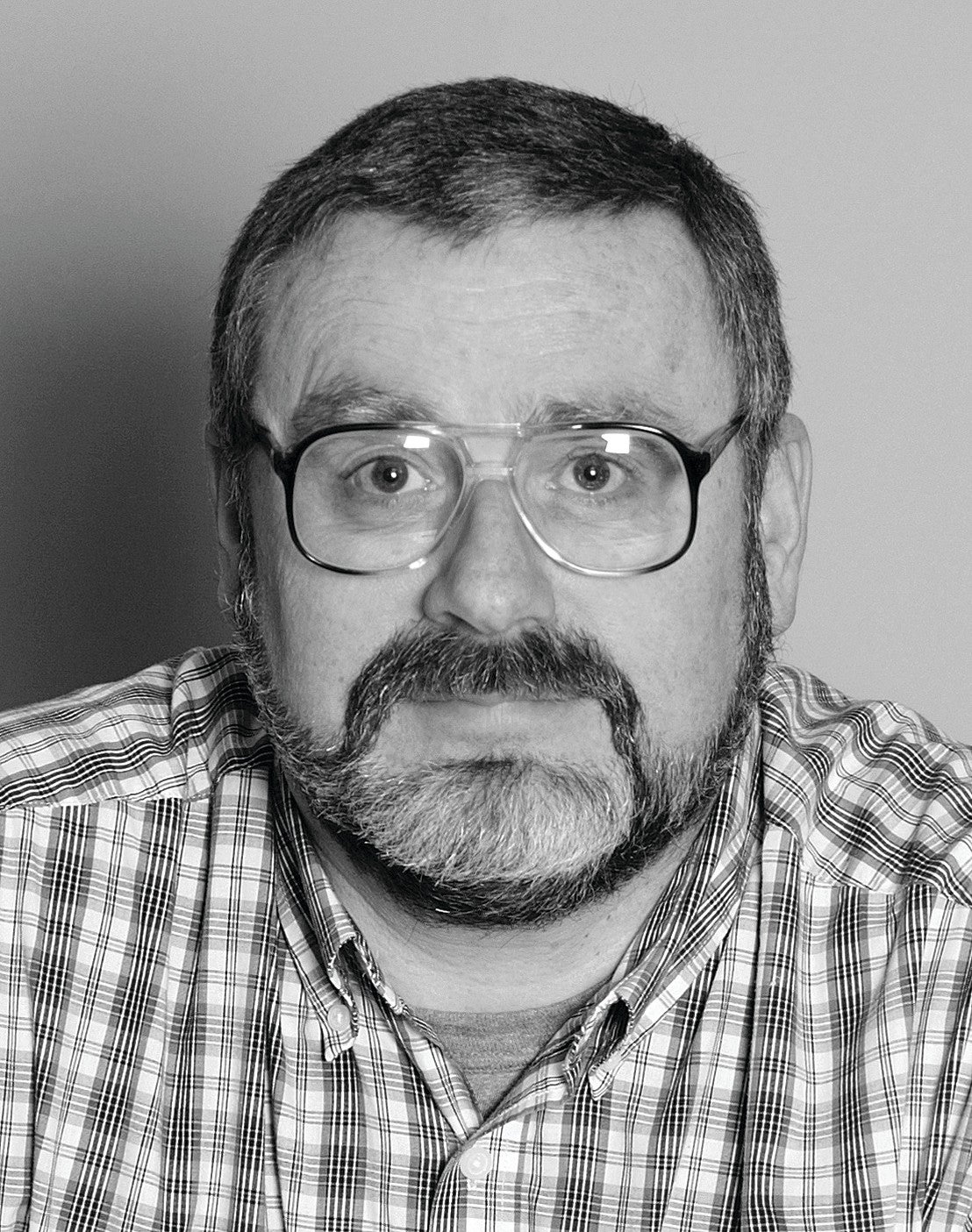