Upgrading to a 5-axis CNC (June 2023)
Adding the capabilities of a machine that can approach work from more directions can help a shop sustain growth and open new markets, but there’s much to consider
This current inflation and interest rate cycle is creating some challenging labor costs. One way to cope is to adopt a more automated environment that either uses fewer man hours or employs less skilled labor where possible.
Although that doesn’t seem to favor employees, automation may in fact be the best way to keep a woodshop’s doors open and protect existing jobs. It also provides an opportunity for employees to enhance their technical skills by learning how to program and maintain robotics and more complex processing machines, such as 5-axis CNC routers.
Not so long ago, even shop owners who were very comfortable with 3-axis machines would shy away from 5-axis behemoths because of the cost and complexity. But new software and controls have made these flagship machines a lot easier to operate, and keen competition has helped keep costs under control. Woodshops are also trending toward outsourcing the mundane (boxes and drawers), while they keep more challenging work such as odd shapes and curves in-house. For that kind of custom work, a CNC often needs to be more versatile than the one-directional spindle on a 3-axis router.
Some shops go as far as they can on the 3-axis machine and then complete the part using traditional woodshop equipment, but that eats up hours and resources. Others use aggregate heads and those can certainly provide unique solutions, but they often work best in short runs and with custom pieces. That’s because they can cause stress on both the machine and the tool during production runs. Not only does the point of contact for the tool move farther away from the body of the spindle when an aggregate is added between the two, but heat build-up can become an issue. Heat usually isn’t an issue for 5-axis machines, which can reduce sheets to panels and parts all day long. And because the toolholder is attached to the spindle (without the need for an aggregate between them), they’re steady enough to make hefty angled, shear and cross cuts in solid wood.
Shops that produce items such as windows, entry doors, stair parts or furniture can find that a one-directional spindle is quite limiting. But a machine with the ability to attack work from almost any angle can significantly shorten setup times, and it can also take full advantage of tools and their various profiles. A 5-axis machine can work on five faces (the sides, ends and top) of a part without moving the workpiece, so the only time an operator needs to tear down a setup and rotate the part is to expose the bottom face, if it needs machining. Not having to make lots of adjustments eliminates a lot of man hours. It also reduces errors in repetitive work.
A 5-axis machine can eliminate any imperceptible ‘wobble’ that might occur with an aggregate head, and the direct drive nature of its acrobatic spindle will generally produce a cleaner finish cut. The reduced strain will also extend tooling life between sharpenings.
If a shop’s existing 3-axis machine, with or without aggregate heads, isn’t keeping up with production quotas, or can’t perform tasks at an angle, there are three basic paths forward. The shop can replace the router with a larger 3-axis machine that can handle bigger aggregates that accommodate saws and large profile bits. Or it can add a second machine – not necessarily a 5-axis, but perhaps something with rotary abilities such as a Legacy. If neither of those choices solve the issue, then it’s probably time to take the plunge and upgrade to something that has true five axes.
What to consider
If a woodworker is looking at an existing machine and wondering whether this is the time to upgrade to five axes, here are a few thoughts to consider. First off, does the CNC seem like it’s slowing down? It may be almost imperceptible at first, but if jobs seem like they’re taking longer than they used to, it may be time to check the travel and milling speeds. A telltale sign that parts are wearing out on the machine is a little bit of a slip in accuracy – nothing dramatic, but a few more rejects or tight fits, or panels that are just a hint out of square. When changing the tool for a sharp one doesn’t fix it, then it might be time to look at gears, bolts, collets, motors, and so on. Keep in mind that some mechanical failures can put employees at risk, so doing the diligent thing may have more benefits than just better or faster work.
Is this a good time to make a major purchase? Interest rates are high, so a lot depends on how much the old machine will bring on the used market or as a trade-in, and how much of the balance the shop needs to borrow. Money is expensive right now, but so is downtime. It looks like shops will be busy enough for the next year or two, and that may be long enough to recoup most of an investment that is made this spring or summer. Keep in mind that fixing the old 3-axis is going to cost more as time goes by, and parts may get harder to source. Plus, prices from some manufacturers are quite reasonable. Some 5-axis machines now cost about what a shop paid for a decent 3-axis unit a decade ago, in real terms.
The main issue may be, can the shop afford not to upgrade? If the jobs coming in require working with new materials, new tooling, new employees, and new architectural forms and norms, then the decision may already have been made with no input from the woodworker. Progress sometimes drags us along for her own amusement.
If a 3-axis machine is showing severe signs of age and needs to be replaced, maybe a 5-axis is a better solution – even if the shop doesn’t currently need those extra A and B axes. If the volume of work at the shop has grown steadily over the years, perhaps the added capabilities of a machine that can approach work from more directions can help sustain that growth by fueling some new market niches. Perhaps it’s time to contact all those other shops still running with an outdated 3-axis, or even no CNC at all, and offer to make table or island legs, fancy range hoods, or carved panels. A 5-axis machine can turn competition into customers.
Once the decision is made to explore 5-axis options, the first parameter to consider is whether the new machine will fit well with existing equipment, infrastructure, and software. For example, will it physically fit into an existing cell that has automated loading and loading, and is the software compatible? How about ceiling height – does the shop need extensive Z clearance? If not, don’t pay for it. Is there enough power available for a much larger spindle or vacuum table? Can the existing dust collection system handle the increased volume?
It’s a good idea to start a list of physical considerations, and then keep updating it as new thoughts occur. Think about aisle space and material handling, and whether there will be enough room for traffic to flow around the new, bigger machine plus any newly automated loading or unloading, conveyors, carts, or people. Before hiring a delivery truck, check the dimensions of the loading dock door to be sure the largest component of a new 5-axis CNC will fit through it. And if the shop doesn’t have concrete floors, have a chat with a structural engineer.
Software
One of the biggest psychological hurdles for woodworkers to clear when moving up to five axes is getting their heads around the software. This is an area where the industry has made vast gains of late, and it has become a whole lot more intuitive. Take, for example, Maestro from SCM. Comparable in its abilities to packages from several other leading manufacturers, Maestro is a software package that includes and integrates all the designing and programming that the shop needs for all its woodworking operations. It’s a comprehensive, all-in-one solution, and this is an industry trend. The software delivers workpiece previews, machine simulation, tool management, and many other functions and utilities. It improves programming accuracy with 3D visualizations of the workpiece, the worktable, and the tools. Above all, it allows the user to concentrate on designing the part, and lets the software automatically handle issues such as tool paths and optimizing.
Ideally, the control software for the new machine will be compatible with exported files from the shop’s existing CAD system. While wires and memory sticks are still acceptable, any new software transfer is going to be wireless. Even if the woodshop is going to change its design software to accommodate the new work cell, compatibility with the existing design program is desirable because it means less duplication, and downtime, during the transition from one machine to the other. It wouldn’t make sense to have the shop’s next job designed in software that the new machine can’t understand or execute.
New software can also do some surprising things, such as suggesting the correct suction volume to hold a part (or several parts simultaneously). That can let the operator place vacuum cups in the optimum spots for maximum hold and clearance, especially on irregularly shaped parts. Many machines are equipped with laser guides to accommodate this, so no employee calculations are required. Lasers are handy because, after the part has been fixtured and it now obscures the view of the cups, a laser beam shining on the board can let the operator know exactly where the cups are located underneath it. For operators who don’t do their due diligence to avoid contact between the cutter and cups, this can be a handy reminder. Most new machine software will include simulation and collision avoidance programs, but these need to be used if they are to be of use.
Shopping
The sheer volume of choices in 5-axis machines can be a challenge. An initial survey of websites will reveal the physical abilities of various routers or machining centers. But trying to compare apples to apples when working through dozens of websites can be exhausting, and it’s easy to get confused. A woodworker pretty much needs to create a spreadsheet. The columns might list X, Y and Z capabilities; spindle power; cooling systems (liquid, air); worktable dimensions; acceleration; milling speeds; guide types (linear, servo); warranties; installation, and ongoing support (what’s included and what’s not) for each machine, and so on.
Each woodshop will have slightly different requirements, which means that no machine will ever answer every need. What’s important to the salesperson might not be critical to the woodshop, so it’s important to have a very detailed list of requirements before shopping. Even though they have five axes, some CNC routers are still primarily designed for nesting and casework. They certainly can produce unusual and prototypical work, but their strength is high speed and accuracy in processing panels and delivering details such as hardware mortises and shelf drilling. Other 5-axis machines (and these usually have smaller beds and taller gantries) are intended more for short runs and prototype work including carving, shaping, texturing, and sanding.
Some issues with a 5-axis machine will be new. For example, an existing 3-axis machine might have had a dozen or so tool positions, so the woodshop owner is comfortable and familiar with some basic tools and sees the new machine as a handy way to add a couple more. But many large 5-axis machines will offer far more. For example, the Epicon 7235 from Holz-Her can handle up to 97 tools. That opens a whole new world of programming and creative options. It allows the machine to use several tools to remove large amounts of waste in different ways and refine the cuts sequentially as they near completion (much in the way that a traditional woodworker begins with a saw and fine tunes with a chisel). This means the shop owner can reevaluate many existing processes and find new, faster, more efficient, and cleaner ways to do things. But it also means investing in more tooling.
Some larger machines offer a chip conveyor, which is a moving belt below the working head that moves waste to a dust collection port. Something you need?
Flexibility is a huge concern. The fact that the woodshop is looking at an upgrade now suggests that it will need to upgrade again in the future. When that need arises, the flexibility of the new 5-axis machine will be a core consideration. Can the spindle be upgraded to something more powerful? Can the shop add more tool capacity to the ATC? How about travel speed?
Every aspect of moving up to a larger machine involves that nagging question in the back of one’s mind: will we be able to train or hire somebody competent enough to run it? For example, how easy is it for unskilled employees to load? Are there programmable, adjustable stops? Can it all be automated?
Next steps
The cabinet and furniture markets seem healthy, despite a downturn in homebuying and building. The consensus among financial analysts seems to be that interest rates will continue to climb a bit through 2023, but inflation should probably rein in sometime during the year.
This may be a good time to pay special attention to American machine manufacturers, especially ones that don’t rely on imported parts.
That said, there are several prestigious manufacturers from overseas who have established a long-term presence in the U.S. or Canada, and who maintain large parts inventories and excellent service and support crews.
Among the 5-axis manufacturers’ websites to visit during a search for options are (alphabetically) Anderson America, Atlantic Machinery, Biesse America, C.R. Onsrud, Casadei-Busellato, Diversified Machine Systems, Felder USA, Hendrick Mfg., Holz-Her U.S., Komo Machine, Laguna Tools, Masterwood CNC, SCM Group, Stiles Machinery (its brands include Homag, Greda, and Heian), Techno CNC, and Thermwood.
And for further reading on 5-axis machines and how they work, visit woodshopnews.com/features/think-it-through.
This article was originally published in the June 2023 issue.
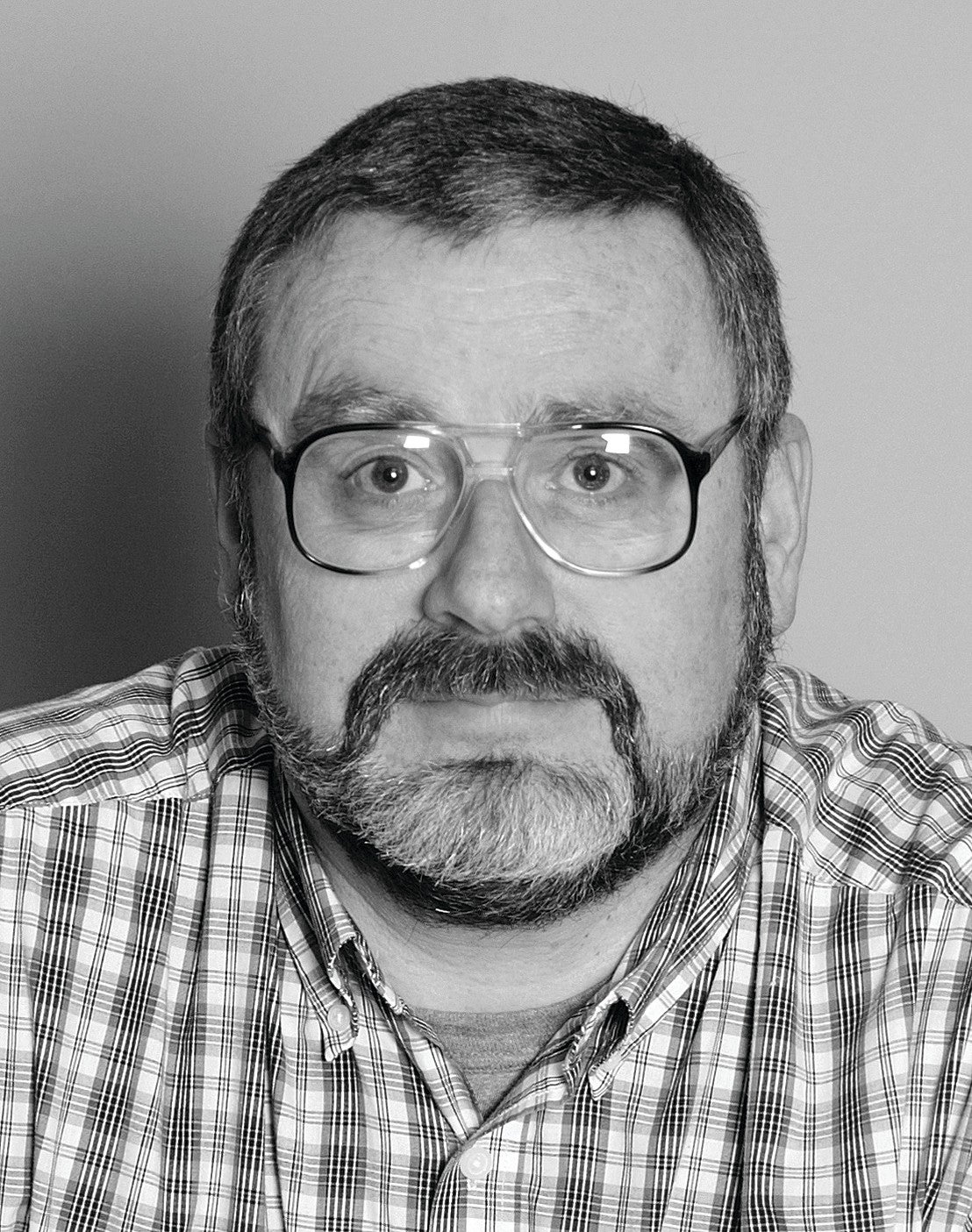