CNCs for growing shops
Woodshops expanding to higher levels of panel processing have a number of CNC options to consider including size and capability, the type of processing tools it is equipped with, and how reliable and user-friendly the software is.
A large industrial CNC can be quite a jump up from a standard 4’ x 8’ router with manual fixturing and loading. The initial investment is significantly higher, but money isn’t always the biggest concern. That would be getting the right machine.
The sales team at Stiles Machinery (stilesmachinery.com) knows a thing or two about volume processing. The company offers a range of Homag CNCs that are designed in Germany and assembled in the U.S., and its website notes that “there are a few common considerations when purchasing a CNC machine, such as the size and capabilities of the machine, the type of processing tools it is equipped with, and how reliable and user-friendly the software is.”
The first of those parameters, evaluating size and capabilities, begins with identifying the full range of parts that a machine will be asked to manufacture, not just now but over its lifetime. The CNC doesn’t just need to be able to mill curves and corners, cut to dimensions, or work well in the materials being used. It must also be up to handling projected volume and speed rates, and be ready for a new era of technology.
So, choosing a larger CNC begins with understanding what the shop’s needs are, rather than immediately trying to search through all the high-tech options available. Those are the fun part, and that comes later. First, let’s look at the basics.
What’s Essential
Manufacturers have numerous ways of describing larger equipment. A ‘CNC router’ is usually just that, a basic flat panel machine with a moving gantry. A ‘CNC wood processing center’ will have more options available such as the ability to turn, saw, mill, drill, sand or even glue. A ‘machining center’ can mean the same thing as a processing center, but the word machining is more often reserved for mills than routers. Mills are slower but highly accurate CNCs that generally move the part rather than the tool. They’re more often used to machine metals but can be employed to work in wood and similar materials when a high degree of definition or intricacy is required.
The ability to nest is pretty much a prerequisite on larger CNCs. Nesting means that the machine can cut in patterns and arrangements that reduce the amount of waste being produced. The goal is to use material in the most efficient manner, and the math for that can all be done by software. There are two ways to nest. Static nesting is employed when the shop needs to make lots of copies of a few parts, so it would be a good choice for a shop that’s building IKEA type cabinetry. Dynamic nesting is a little more complex and is used when the shop is doing lots of shorter, very custom runs. Both take advantage of simple geometry, such as being able to use one toolpath to create an edge for two separate parts. Nesting saves on material waste, tool edges and sharpening cost, power requirements, and employee time spent restacking, moving and clamping parts. If a woodshop is looking at CNCs to handle a higher volume of panels, nesting is an essential part of the picture.
Labeling is almost as critical. A larger CNC must be able to identify parts so that the assembly process goes without a hitch. Labeling can be done with printed stickers, direct ink printing, ink/dye stamps or laser engraving. The more automated the better. The machine software should be able to place labels in non-critical locations, such as the edge of a panel that will eventually be banded or buried in a groove or dado. Some smaller machines can’t reach sideways and can only label from the top. It can take a lot longer to remove a label than to place it.
Nesting software usually includes the ability to label automatically, and also to group parts either in sequence or affinity. The latter refers to keeping identical parts together as much as possible, and the former makes parts as they will be used (for example, an entire cabinet at a time so the assembler doesn’t need to wait for a specific part to be cut at the end of the day before the casework can be completed). Nesting software on larger machines often gives the operator the option to manually tweak a pattern and optimize so that, for example, a small part for the next job can be cut from the waste on the current job. Nesting software can also be integrated with inventory programs, so that whole sheets aren’t the only option. The software can determine that a previously labeled cut-off from another project can deliver a part, rather than using a full sheet.
Sometimes the introduction of a new machine can change the way the shop optimizes. If the bed is a different size or shape, the new machine can probably handle differently dimensioned sheet goods. That can open opportunities such as slightly redesigning established parts to take advantage of the new sizing. For example, a 5’ x 5’ sheet can deliver differently sized parts than a 4’ x 8’, so slightly changing a drawer opening or a door size might deliver more parts and less waste. If there are options for differing sheet good dimensions from the woodshop’s supplier, the bed shape and size might be a factor in choosing a new machine.
Integrating software becomes more important as the machines get larger. The woodshop owner or manager needs to discuss this with any potential CNC salesperson. If the shop is locked into a specific CAD design program, it’s critical that there is a streamlined relationship between that software and the CAM machining software for the new machine. Upgrading to a larger CNC may require changing the cabinet design package in the office computer. That can mean training downtime, or workflow challenges with other software such as project management, or even complicated transfers of libraries from parts and hardware vendors. It’s worth having the discussion up front.
Many of the larger machine manufacturers have created their own software bundles for monitoring performance, maintenance, safety and heat issues. Some of these new packages include programs that tie machines together from the same manufacturer (and in some cases from other factories) in a web that becomes systemic across the woodshop. This is intended to take advantage of options such as automatic loading and unloading, tool changes and fixturing (holding parts in place). An operator can use a tablet or even a phone to monitor several machines at once, and spot glitches before they become downtime.
As AI (artificial intelligence) advances in the woodshop, machines are learning to handle the monitoring, too. The impact of AI will be massive in all aspects of industry and production over the next decade, as more shops and factories switch to robots and cobots to replace humans. With larger CNCs, AI is going to be more of an issue with peripherals than basic programs (loading, monitoring, aggregates and so on), so it’s another area for discussion with the machine supplier. Ask about what’s in the pipeline, what’s available now, and how the machine will be compatible with advances in technology.
Axes, Tables and more
Nesting machines are the perfect option for routing and drilling. That lets them cut parts to size that are ready to edge band, and to mill edges and faces for connectors and other assembly devices. They can also mortise and drill for functional hardware such as slides, pulls and hinges. As more and more connection systems evolve, the ability of a machine to work in more than one plane comes into focus. Even though a CNC that can only mill in Z can’t easily place a slot in a 45-degree miter, aggregate heads and pods that raise parts for edge work have come to the rescue. Because of innovative solutions like those, most standard casework shops can get by admirably with a 3-axis machine.
And your basic 3-axis isn’t so basic anymore. For example, the Talent T5D is a 3-axis, high-performance nesting machine from NewCNC (newcnc.com) that has 1.5 KW servo motors, a 16-hp spindle and Delta CNC controls. Good travel speed and a standard 12-position carousel tool changer cut processing times, but the T5 also offers a 10-position boring block, a panel sweep, automatic panel alignment, and pre-configuration for auto-load and unload as standard features. It comes with 10-hp vacuum pumps and CNC controlled vacuum gates. In fact, all NewCNC routers are pre-configured with automatic load and unload devices, automatic panel alignment, a table sweep, and optional label printing, so a single operator can keep the machine in continuous production.
Grizzly (grizzly.com) has recently added two large-shop models to its line-up – a 4’ x 8’ table with 4-axis capability (G0933), and a 5’ x 10’ model (G0934) with a vacuum table and an eight-position ATC. The smaller model is a unique machine with a spindle that turns 90 degrees left or right, which gives it the ability to cut in 3D. The larger CNC has six independently controlled vacuum zones and a two-stage air vacuum pump.
While these kinds of versatile 3-axis machines can meet most needs, sometimes a shop needs to do work in more than X, Y and Z. For example, among the offerings from SCM (scmgroup.com) are machining centers that are specifically touted for the manufacture of chair and desk components. The company’s new 5-axis Balestrini Power machining centers use Smart Pro software for CAD/CAM that lets a woodworker draw parts on the computer and automatically optimize them. Then it visually simulates the machine’s operations on the screen before any cuts are performed, which helps avoid collisions with fixturing or the gantry when a shop is making complex, shaped parts. The Balestrini also has some very innovative parts-holding options, and it can operate with a single spindle or a 5-axis revolving toolholder.
Versatility is key when ordering a machine, and most of the big toys can be ordered to fit a shop’s basic needs and budget. Anderson America (andersonamerica.com) says it offers “the most comprehensive CNC router line up in the industry from 5-axis to 3-axis, fixed bridge moving table to moving gantry, pod & rail or flat table”. The line-up includes sixteen machines including the Stratos Pro XL, which is a large format 3-axis machine. When it comes to options, the table sizes on this machine range from 7’ x 12’ to 10’ x 30’, and a couple of different spindle sizes can be ordered with optional water cooling. The shop can opt for 10-, 12- or 16-unit tool changers, and a Z travel (up and down) anywhere from 350 mm (13.7”) to 600 mm (23.6”). Anderson offers vac pumps in 10-, 25- or 40-hp versions for this machine, and a list of other options that includes bar code reading, a touchscreen, a C-axis for turning, reverse airflow for the vacuum table, a mister for cutting tools, and automated materials handling. Additional options include workpiece dimension probing, both single and dual zone capabilities, and custom configurations.
Speaking of the C-axis, some machines have evolved with specific woodshop tasks in mind, such as the Maverick CNCs from Legacy Woodworking (lwmcnc.com) that pays special attention to turning. Built in Springville, Utah, the top-of-the-line Maverick comes with a 4’x 8’ horizontal table plus a 7″ x 20″ vertical table and a 79″ 4-axis turning center. Its three workstations are designed to handle standard panel flatwork, solid wood joinery, and turning. It’s an interesting combination of rotating the part and cutting with a router that is difficult to replicate even on a manual wood lathe.
Thermwood (thermwood.com) also offers several machines with an optional rotary axis, including the Multipurpose 45. This is a heavy-duty 3-axis base model with either single or dual spindles that was designed for wood and nested based panels among other materials. The table sizes run up to 7x12, and the standard ATC is a 4-tool holder but a seven-position unit is available. The optional rotary axis will work parts up to 8” in diameter and 56” long. The table is set up for an optional pod system, and that’s something that woodshops moving up to larger machines will want to ask about (see below).
Castaly (castaly-cncmachine.com) makes a rotary axis lathe for CNCs that will look quite familiar to anyone who has turned on a standard wood lathe. The relatively inexpensive upgrade offers quick and easy set-up for the standard 8” diameter and 48” long unit, and custom sizes are available. For larger shops doing more than occasional turning, the company offers an automated free-standing wood lathe and several 5-axis CNC options.
Pods, Rails and Fixed Bridges
Even though it can be a little slower, a pod and rail fixturing system offers one huge advantage over a flat table: it elevates parts so the edges can be worked either by a horizontal tool or aggregate heads. Instead of a large flat table with mechanical clamping, or holes for vacuum holding, it is a series of bars (consoles) that clamp across the table and can be moved from side to side. On top of the bars are pods, which are small manifolds or suction cups that can slide back and forth along the bars. The net effect is that the pods can be placed almost anywhere in X or Y and suck the part down using vacuum power. Sometimes the vacuum pods are replaced with mechanical clamps that can be moved around and swiveled to grip the edges of irregularly shaped parts. For repeat manual set-ups the pod systems can use LEDs or laser guides to mark locations, and some systems are robotic: software will move the pods into position automatically. The downside is that sometimes the pods get in the way of an aggregate head like an angled trim saw, plus there might not be much support for a large flat workpiece, especially where cut-outs that fall through (like sinks) are involved. Pods can be a challenge with narrow parts, too.
The Felder Group (felder-group.com) has advanced pod positioning to an artform with its lightPos system. This elegant solution lets a shop quickly and very precisely position pods in a larger production environment. On the company’s Format 4 CNCs, more than 6000 LEDs can indicate the suction cup size, position and orientation as the console positions the placement within a millimeter’s tolerance. A sophisticated management system means that each vacuum type and its orientation is displayed in well-defined and specific colors. LEDs on the X-axis give information about the processing status, while lights along the X and Y axes indicate both the position and the dimensions of the workpiece. The net effect is remarkably fast setups and accurate repeatability.
Flat vacuum tables are more numerous than pod & rail arrangements, but some of those use their bridge and table in a similar way. Their spindle moves left and right along the bridge for X, while the table moves back and forth to simulate the Y axis. One advantage of a fixed bridge in larger machines is that there can be two tables and multiple spindles. That layout can really speed up flat panel production. A good example is the LIME series from Machine Tool Camp (machinetoolcamp.com). The standard 01 unit delivers 5,700 inches per minute (ipm) of travel, and 1,600 ipm for cutting. There’s 14” of clearance for Z under the bridge, and two higher bridge options offer 31” and 48”. But what’s impressive is that the machine can be equipped with two tables, dual cutting heads, ATCs, drilling units, 5-axis machining, multiple table sizes, and either left/right or forward/back orientation for better access, depending on the type of work being done.
Sometimes an existing 3-axis CNC is more than adequate for a woodshop’s flat panel volume, but the shop is seeing a need for more advanced machining on some jobs. The answer may not be to upgrade to a full 5-axis machine, but rather to look at solutions such as the ELEV8 from ProEdge Technology (proedgetechnology.com). This is a boring and doweling CNC that creates all kinds of solid wood and composite joinery, and offers glue and dowl insertion. It has both horizontal and vertical routing capabilities and uses three electro-spindles and 3-axis CNC control. That means it can handle joinery and connector milling for Rafix, Minifix, Maxifix, Confirmat, dog bones, Domino slots, rear panel notching for undermount drawer slides, Soss hinges, and more. The parametric programming can deliver machined louvered doors and Shaker door stiles and rails, plus dadoes and blind dadoes can be programmed to automatically change size and length as the panel sizes change.
Along with the investment in a larger CNC, a woodshop will need to deal with traffic flow, power requirements, vacuum issues, and of course software updates. Changing out or installing a new CNC also means downtime, so the whole process needs to be treated like any other project and managed as well as possible to avoid glitches. But once the right machine is in place, a new state-of-the-art CNC can revolutionize product levels and the quality of work.
This article was originally published in the September 2023 issue.
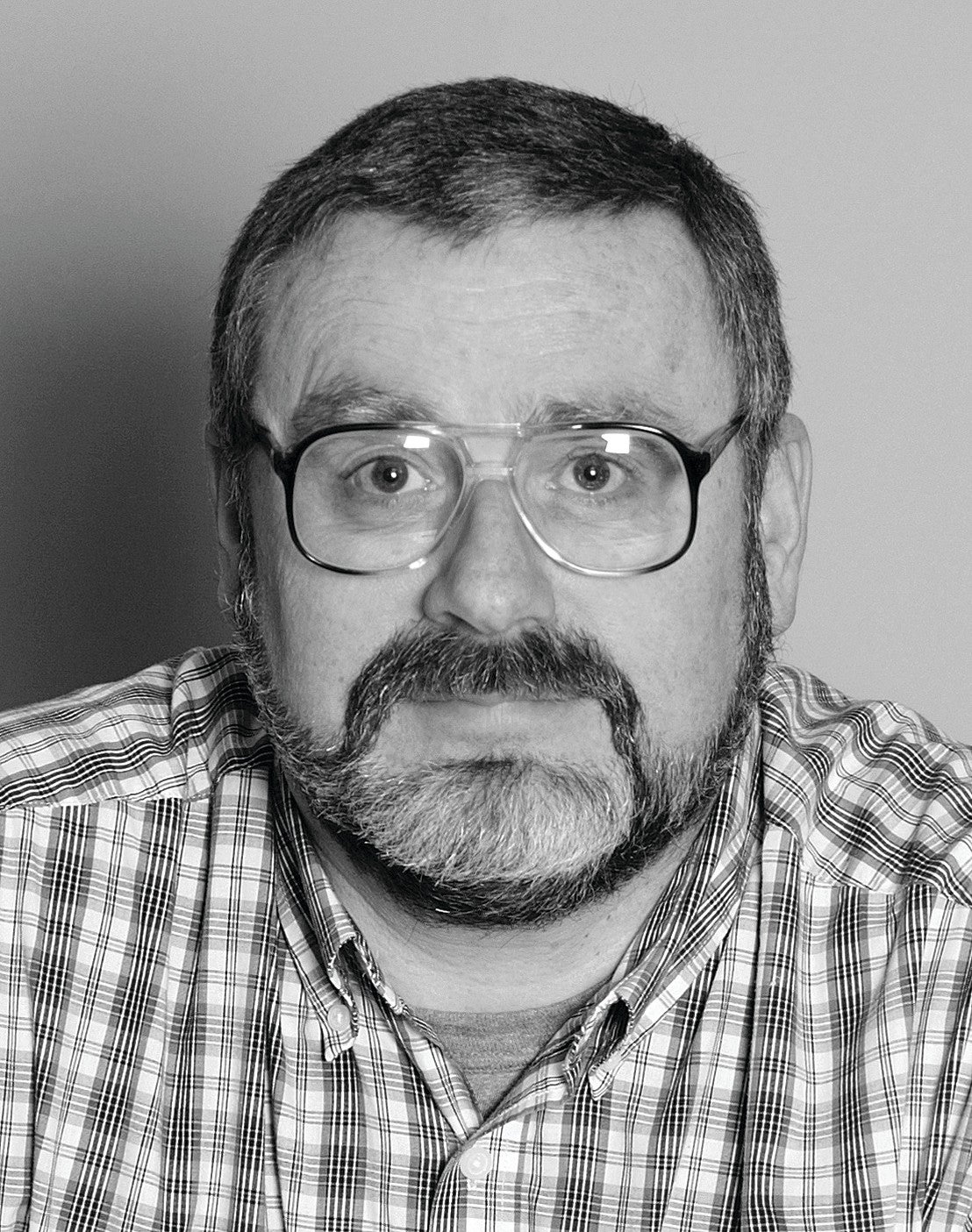