A Growing Palette of Choices
Options for countertop materials have never been greater, including wood, epoxy, porcelain, and a faux metal finish.
While woodworkers might think of solid surface countertops when they hear the phrase ‘surface materials’, it actually describes every visible and hidden facet of cabinetry from vertical doors to horizontal shelves and counters. The category encompasses materials such as veneer and solid wood, plastics, metals, and stone.
We drag everything across our countertops, from school backpacks to frozen food, dishes, keys, computers and even the occasional pants seat. And toughness is only half the equation. Counters also need to look good while they perform architectural functions such as separating white base cabinets and colorful wall units, or underscoring a bank of windows, making a galley out of a hallway, improving the convenience of an island, or simply adding drama where it is lacking. Much of that visual impact depends on the material being used. Counters run the gamut from traditional plastic laminate to stones such as Travertine, marble, soapstone and granite. Or they can be metals including copper and stainless-steel, or cast and tiled ceramics, edge-glued butcherblock or live-edge slabs, to name a few.
One of the trending materials right now is a very old product in new guises. Porcelain is made with a fine-grained clay called kaolin, which is fired at a higher temperature and longer than commercial ceramics. The result is a surface material that’s denser and more durable, and usually has a smoother glaze, and the color runs through.
Porcelain can be ordered as a slab from manufacturers such as Caeserstone (caesarstoneus.com), and the dimensions can be quite large. That company’s standard collection measures 61.5” x 124.5” and just under 1/2” thick, and that size can deliver a single slab for most islands or countertops. Even though porcelain evokes images of ancient bathroom fixtures, this is a very versatile surface material that nowadays can assume other identities. For example, the new 503 Circa porcelain countertop material from Caeserstone looks like marble.
Epoxy is another option that’s gaining ground as a surface material, and it has become especially popular with art furniture builders and skilled DIYers. We’re all familiar with ‘river tables’ that feature a blue stream of resin trapped by live edge wood. But as a pure kitchen countertop, epoxy can be quite inexpensive when compared to granite or marble, and experts can even make it look just like those or other stones. It can be seamless too, which can be a critical advantage on large jobs.
But there’s a downside. It can also absorb standing spills and allow them to become permanent stains, plus epoxy countertops are tricky and unforgiving to make, especially if they are poured in place. Bubbles, unevenness and spills are common for new practitioners. And the quality of epoxies isn’t ubiquitous – some are really brittle, or perhaps so fluid that they flow too fast. Epoxy can also be used to reface or recoat existing countertops, where a thin skin is poured over a treated and properly prepped surface. That can cut the cost dramatically, as standard thickness epoxy counters can absorb a lot of cubic inches of expensive resin.
Epoxy countertops can be purchased as pre-poured units and cut to size, custom manufactured, or ordered as kits from suppliers such as Epodex (epodex.us). There are lots of instructional videos online, and kits come with instructions. However, Woodshop News spoke with an epoxy installer who strongly suggested starting out with several projects for practice before offering the service to customers. There’s a learning curve.
Sustainable options
Combining workability with the potential for dramatic colors, Richlite (richlite.com) is a durable, sustainable and versatile material made from paper infused with a thermosetting resin. It is laid up by hand, and then pressed into a solid panel. This material can change and transform over time, growing deeper, darker and mottled while still withstanding the daily demands of kitchen use.
Another sustainable and familiar option, the live edge slab, is once again gaining popularity among designers who wish to add the warmth of natural wood to clean, stark, post-pandemic cabinetry that feels sterile without such a balance.
Stone Italiana (stoneitaliana.com) has been making waves this year with the launch of Cosmolite. Made from recycled minerals, this is a high-performance surface material that is made with different formulae for different collections and looks. The sheets contain mineral oxides in varying amounts and grain sizes that are linked by a common thread: their low crystalline silica content. (Also known as silica dust, it has been regulated recently by the U.S. Department of Labor.) The minerals in Cosmolite are sourced locally in Italy, which reduces energy consumption and transport costs at the manufacturing stage. The resin used to bind the grains together is made using plant-based ingredients, and the company says that Cosmolite is “a bright new opportunity for designers who, whether following their own consciences or because they know it enhances the value of a product, seek out green solutions.”
Sometimes a shop needs a surface material that can follow a curve, and Kerfkore (kerfkore.com) offers backers that can bend down to 10”, 8”, 5” and even 3.5” radii. Thicknesses range from 1/4” to 3/4” and some panels are available in sizes up to 120” x 48”. The company’s Timberflex flexible panel combines a base layer with a 1/8″ imported Italian poplar plywood face to create a flexible and stable structure that allows the attachment of high-pressure laminates, veneers, metals and many other semirigid materials.
Custom solutions
One of the challenges in design is to find a manufacturer that can provide the same surface pattern across several surface materials so that vertical, horizontal, damp and dry applications can match or complement each other. Omnova (omnova.com) supplies a broad portfolio of 3D, 2D and paper laminates that lets cabinetmakers use different materials to fabricate products in a more cost-effective way. The 3D laminates are used on cabinet fronts, while 2D and paper-based versions can be used on both interior and exterior surfaces.
Another challenge is to find large panels that are stable enough to build sliding barn doors and floor-to-ceiling casework, for example. SingCore (singcore.com) in McCleary, Wash., provides custom, uncoated door and architectural panels, with no hardware or finishing options, that come with a 50-year structural and warp-free guarantee. They’re available in numerous surface materials including paint grade, wood veneer, metals (aluminum, steel and copper), ceramic laminate, Fiberglas, and high-pressure laminate (HPL).
Another supplier of panels, Talbert Architectural (talbertusa.com), supplies miter-folding edge products, sequenced (continuous grain) panels, and UV coated, cut-to-size elements. Talbert was the first veneer company in California to be FSC certified.
Superior Veneer (superiorveneer.com) in New Albany, Ind., offers 1/16” veneers for jobs that require real wood surfaces that are about twice the thickness of the industry standard. These ‘Artisan Thick’ veneers are available in a variety of species and layup options.
And for shops that need very specific surface materials, States Industries (statesind.com) is a custom manufacturer of hardwood plywood where every part of the panel can be customized to match precise specifications. Those include everything from the substrate to the veneer species, the color, and the unique properties of the finish. States can supply small quantities for a custom remodel or large quantities for use in commercial applications, and is also a prime source for rare species veneers and panels.
Finally, woodshops that need to magically turn wood-based parts into a wide variety of ‘metal’ materials might wish to visit Make It Metal (makeitmetal.com). This company uses liquid metal coatings on a variety of surfaces to create the look, texture, and feel of real metal.
This article was originally published in the November 2023 issue.
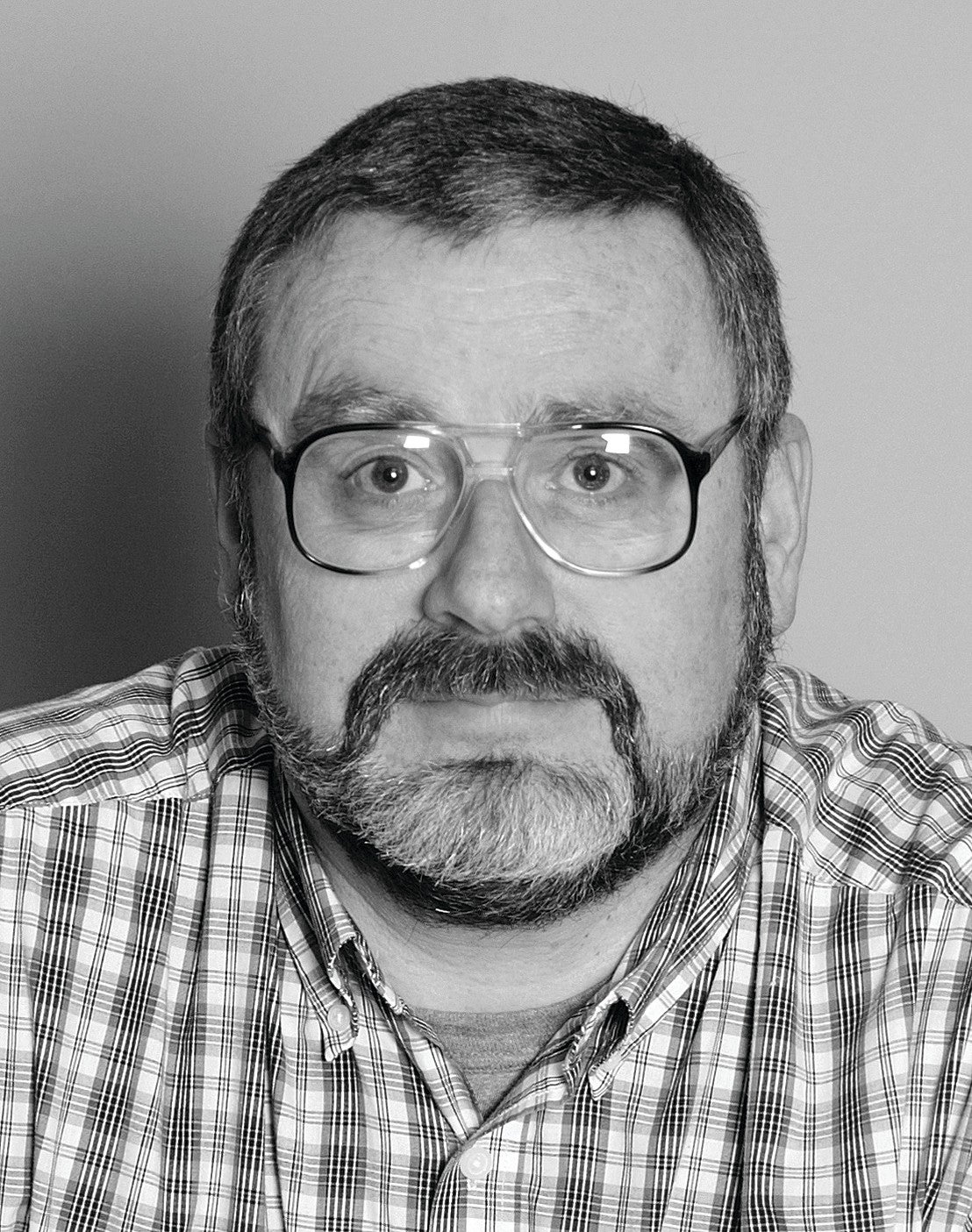