Aggregate advantage
Aggregate heads (also known as angle heads) are a relatively easy way to add a new dimension to most CNC spindles. They essentially enhance horizontal capabilities to include vertical options….
Aggregate heads (also known as angle heads) are a relatively easy way to add a new dimension to most CNC spindles. They essentially enhance horizontal capabilities to include vertical options. That is, they allow the operator to change the direction of the spindle. They can also change its function because they allow a woodshop to add new tooling that won’t always work on a vertical spindle.
Aggregate heads are available for virtually any CNC machine, but they do eat up power. The minimum spindle rating is usually 5 hp, but many manufacturers will recommend something with more “umph.” Heads will work with either HSK or ISO connections and some will accept BT, too.
Many aggregate heads will work with automatic tool changers, but talk to both the head supplier and the CNC manufacturer before committing. Some options will require manual mounting. There might also be physical size and weight restrictions and questions about configuration, too. You might end up sacrificing some tool-holder positioning. And you have to be sure the head can maneuver inside the confines of your CNC without bumping into anything, before you actually run parts. The new head substantially increases the tooling footprint. You’re also switching from vertical to horizontal positioning and that can have limiting implications for paths.
Aggregate heads also come is variable versions, so you’re not always looking at 0- or 90-degree applications. Many are infinitely variable between those angles (and sometimes slightly beyond them), so they can perform beveling or chamfering functions.
There are other advantages to aggregate heads. Adding one to a C axis pretty much converts the CNC to four axes. And a floating aggregate head can handle workpieces that are not entirely flat. They will register off the top face of the panel, rather than the bed of the CNC so they can mill a uniform depth below the surface even if the workpiece is tapered — usually up to a tolerance of about 10mm — so they’re engraving in much the way a laser would (although not as finely).
A big selection
Most major manufacturers provide a complete array of aggregate heads to handle a variety of woodshop operations. For example, Techniks (www.techniksusa.com) has aggregate heads in stock that perform routing, drilling, sawing, mortising, sanding and many other operations. These heads let a shop combine functions and thereby increase productivity. The company has stock aggregates for just about any application and it can build custom models to meet a woodshop’s requirements, usually at no additional cost.
That brings up a good point. Aggregate heads are often quite customized and that can be labor-intensive. When Techniks creates one, it is test-run it for 30 minutes and completely disassembled for a quality check. The company offers a “Never Down” program that ensures a shop will always have an aggregate head up and running.
The very nature of these heads invites constant innovation. For example, Benz Inc. (www.benz-inc.com) recently introduced a new floating version. It comes with a 360-degree integral dust hood that directs chips straight up and into a shop’s dust collection system. It requires no C axis and there’s no need to steer the unit because the dust hood is concentric. The Benz Floating Aggregate is easily adjustable for depth of cut and has large, easy-to-read gradations (for us older, more seasoned woodworkers). It’ll fit all brands of machinery, too. Benz also repairs all makes of aggregates.
The company’s Undersurface Trimming Unit is an aggregate head that will machine an elevated workpiece from underneath, up to 6” in from the edge. Benz also offers a Corner Notching Unit that mills square corners with a round tool. (Well, it actually plunges a small rotary cutter head from the top, which squares the corner.) The company introduced several new aggregate heads at IWF 2014, including its HF103 Solidfix spindle motor, which allows for quick and easy tool changes. It uses adapters that hold a variety of tools, instead of requir ing a manual tool change or adding an automatic tool changer. It’s more flexible than a collet shaft and has a brushless motor.
Precision Drive Systems (www.pdsspindles.com) describes the need for aggregates this way: “Users of CNC machines and robots often find it necessary to perform operations that cannot be accomplished with a spindle alone. Some of these instances include changing the angle or plane of machining and fitting into tight spaces.”
Precision Drive Systems repairs heads and spindles and builds custom solutions for woodshops. In 2008, the company began manufacturing its own line of high-speed spindles called the XLerator series. Today, Precision Drive Systems offers both fixed- and variable-angle aggregate heads for vertical CNC machine tools. Its aggregate heads are used for sawing, routing, boring and mortising and custom head designs are available. But aggregates are very versatile and not limited to those functions. For example, Precision Drive Systems also make heads that are designed for a broad range of automated sanding and polishing applications in wood and composites.
Printing, too
C.R. Onsrud Co. (www.cronsrud.com) offers the new InnoAgg labeling system, which allows a CNC to apply printed labels to parts before they are milled from the sheet stock or to print directly on the parts with either water-based (for easy cleanup) or permanent inks. This innovative labeling aggregate lets a woodshop label the sheet, do a quick tool change and cut the parts in one smooth transition. It’s perfect for a nested-based manufacturing setup and it also saves the space that would have been used by a dedicated offline printing station. There’s no wax ribbon or transfer paper involved and the heads feature wireless self-charging, so it’s powered by the spindle and requires no cord connections. Plus, when it’s idle it can reside in the tool changer.
Colombo USA (http://colombospindles.com) offers an entire family of aggregate heads — about 70 variations all told — with ISO, splined or HSK spindle inputs. They include models with fixed right angle (single or dual output) and heads with variable angles that can address work anywhere from 0 to 90 degrees. The company maintains inventory of the most popular items with stocking programs available to minimize lead times. All Colombo spindle repair work is guaranteed and completed using only OEM parts and factory specifications. The company has been designing and manufacturing spindles for nearly 60 years and can tailor heads to suit a specific woodshop application.
Another company with a long history in spindles is HSD USA Inc. (www.hsdusa.com). With a worldwide reach (it has branches in Europe and China), HSD is the leading Italian producer of aggregate heads. Its U.S. operations are based in Fort Lauderdale, Fla., and its aggregate heads cover milling, boring, drilling, floating, copying and cutting options. The company’s HSK and ISO aggregates are made of Avional aluminum (a high strength alloy that contains copper, magnesium and silicon), which is designed to deliver a high level of structural integrity and durability. HSD’s woodworking line is being constantly updated with the addition of new models, a recent example of which is an oil-lubricated head. As with all of these high-end suppliers, quality control is extremely important. Each mechanical, pneumatic and electronic component used in a HSD right angle head undergoes a double testing phase. The company’s catalog can be downloaded online.
Two more
GDP/Guhdo (www.guhdo.com) has been supplying industrial cutting tools in North America since 1986. Based in Marietta, Ga., most of its partner companies are ISO-certified and thus explicitly required to adhere to European safety and quality standards, which are usually higher than ours. The company provides custom tooling for CNC machinery, including HSK63F, SK30 and ISO30 aggregate heads that are made in Germany. They cover options such as drilling, routing, grooving and sawing. Gudho aggregates fit most CNC machining centers, including Weeke, HolzHer, Homag and point-to-point machines. The company also supplies a good range of aggregate head saw blades (Series 2062).
Integra Precision Tooling (www.ipgandm.com) offers 1-, 2-, 4- and variable-angle aggregate heads, plus a soft touch (floating) model. The company’s Ultra aggregates are lubricated in an oil bath and sealed from contaminants for extended use under heavy-duty conditions. Ultra models are recommended for saws with blades larger than 7”, V-grooving, heavy routing applications and cutting MDF or composites. Integra’s Function aggregate heads are grease-lubricated for standard duty operation and cover a large number of configurations and application-specific options. And the Integra’s Smart aggregate heads are smaller units for standard duty operations that are grease-lubricated and intended for smaller CNC routers.
The bottom line with aggregate heads is that they expand a shop’s options. A CNC can stay busier when it can do more things and by adding a relatively inexpensive head (or heads), a woodshop can tackle more functions than simple routing. Plus, with an adjustable head, the CNC can work at an angle.
This article originally appeared in the September 2015 issue.
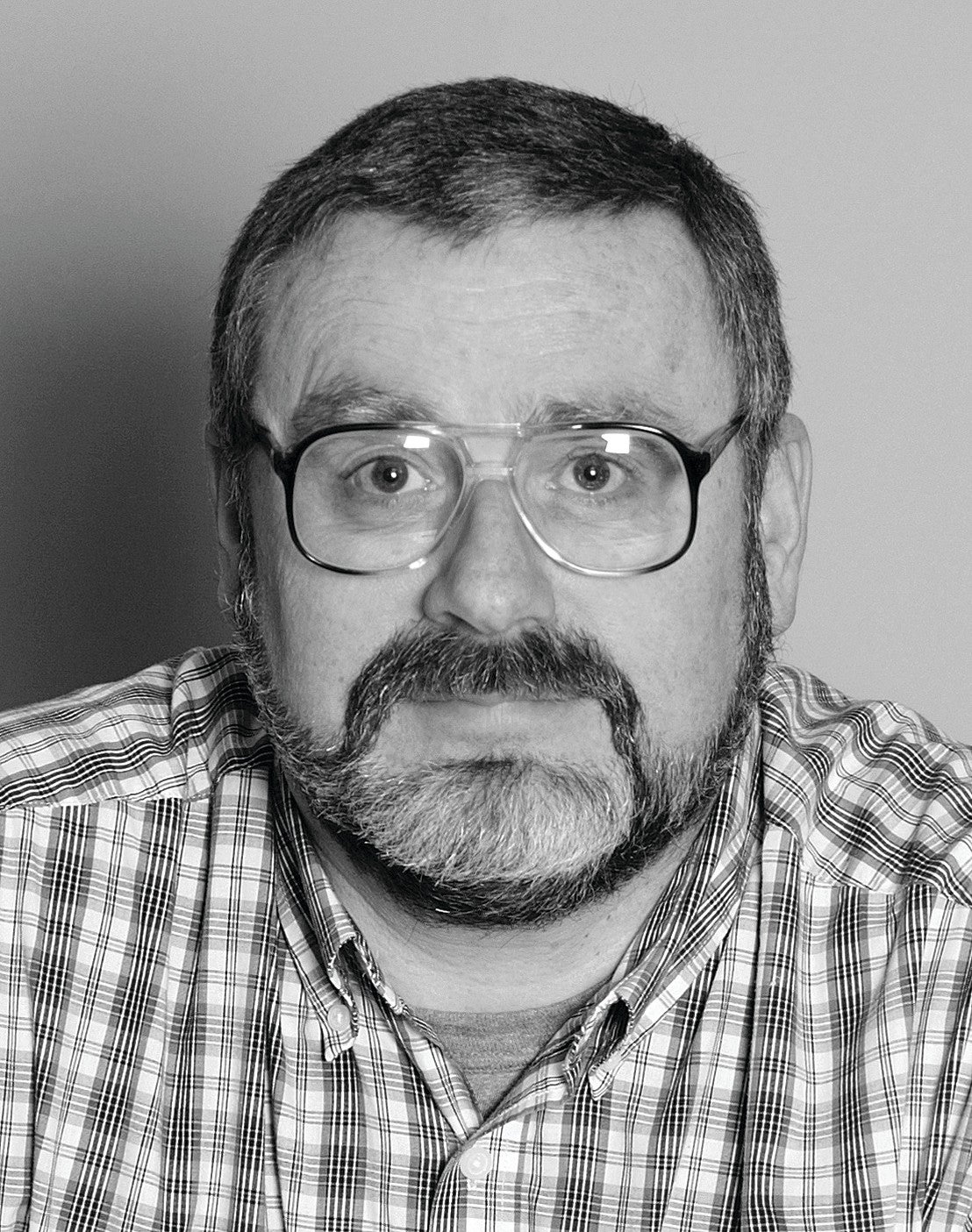