An aggregate head (or simply an aggregate) is an accessory for a CNC that lets the machine handle tasks that are more than just plunging a straight bit into the wood and then traveling across the top surface. Its most useful application is to bring many of the capabilities of a 5-axis machine to a 3-axis CNC.
The aggregate can be attached to the router spindle, using a standard tool-changer format such as HSK or ISO, to change the direction of the spindle shaft. Instead of pointing straight down, this new shaft extension can swivel and then lock at various angles to facilitate sawing, drilling and routing – either horizontally at 90 degrees (sideways, so it addresses the edges of the part), or at pretty much any incremental angle. For example, it might allow the bottom of a straight plunge bit to create the angled section of a traditional raised panel, rather than having to use a very large and wide-angled V-bit. One advantage then is that an aggregate can use a smaller, lighter tool and that’s significant where weight is an issue.
Remember that by adding an aggregate to the end of the spindle you’re now introducing sideways (shear) force as well as downward (vertical) force, along with the new head’s additional weight and length, so you’re asking the spindle and the gantry to do a lot more work.
Many standard tools can be modified to connect to an aggregate, so it’s a good idea to take an inventory of the shop’s available tooling before investing in a new aggregate that might require new tooling.
Some of the applications that an aggregate can add to a basic CNC are angled sawing such as removing excess material, trimming parts to length or creating slots and grooves at different angles; cutting compound angles; drilling for dowels and plastic or metal connectors on the edges of parts; milling mortises in edges and on the ends of stiles and rails; creating tenons without having to re-fixture between the top and bottom milling; milling for inset hardware such as hinges and locks; and sanding with either short belts or random orbit discs.
If a woodworker just attached a new aggregate to an existing spindle, it would obviously spin around. To keep it locked in position at the end of the spindle, various setups use anti-rotation rings or stop blocks, or a C-axis (fourth axis), if available.
If you’re not familiar with the C-axis, the easiest way to conceptualize it is to imagine a device that attaches between the spindle and the aggregate. It has a little motor on board that allows the aggregate to turn 360 degrees while the spindle stays in its normal position. So, if you have an aggregate with, say, two tools on it, there might be a large plunge bit sticking out of the left side and a much smaller straight bit chucked into the righthand side. Imagine an entry door fixtured to the table (well, vacuum clamped in place), and the mortise for the lock needs to be created in its edge. The large bit in the aggregate can move sideways into the wood and carve most of the mortise, and then the head is withdrawn so the C-axis can turn the aggregate 180 degrees and let the small head clean up the corners.
A C-axis also lets the tool follow curves and ellipses, adding even more abilities to the aggregate. That is, it can swivel slightly as the spindle travels along a curve so that the tool is always addressing the wood at the same angle.
Another great use of aggregates is to use a floating head that registers off the top of the work (rather than zeroing on the spoil-board), so the tool can stay parallel to uneven surfaces and always cut at exactly the same depth.
Adding an aggregate adds stress and weight, so keeping it cool is a huge concern. Most heads use grease lubing, while others offer an upgrade to an oil bath. An oil mister may be an option, but the best solution is to monitor the temperature and to set up cuts so the machine isn’t overworking. Many aggregates have a temperature gauge on the body. The best advice is to talk about speeds, bit diameters and chip load with the salesperson while keeping in mind that the machine needs to be powerful enough to handle the aggregate and the head needs to be cool enough to handle the load.
Depending on how far the tool in the aggregate needs to reach, a shop may be able to purchase different length heads. This can be an issue if the CNC will be milling slots and holes for, say, very specific connection hardware. So, it’s a good idea to have the hardware in hand, along with a sample of stock that has been milled, so that the aggregate salesperson can understand the exact parameters of the task. Another concern with dimensions is that the spindle is now in effect both wider and longer, so the operating space in all three directions (X, Y and Z) is going to be smaller. The shop’s CAD and CAM programs may need to reflect this in different ways so the head doesn’t contact the supports, table edges or gantry, or perhaps chew into the spoil-board or fixturing. If an aggregate is holding a long plunge bit sideways at 90 degrees, the distance from the tip of the tool to the center of the spindle is now a lot longer than it was when the same bit was just chucked in a vertical position. So, the distance the spindle can travel from one side of the CNC to the other is now shorter.
Available options
Precision Drive Systems (online at spindlerepair.com) is the exclusive distributor of Hiteco woodworking aggregates in the U.S. The catalog includes aggregates with retention rings and stop blocks, and also a variety of different aggregate configurations to use with various C-axis connections. Both the intermittent duty Fast Line and the company’s premium, continuous duty Master Line aggregates from Hiteco have bevel gears, so they can run at the higher speeds required in woodworking (as opposed to aggregates that are primarily designed to machine metals). PDS is based in Charlotte, N.C.
Some aggregates can handle different tool holders on a single unit. For example, Benz (benztooling.com) offers the Solidfix system so that quick tool changes are available even with the aggregate installed. Options here include fixed angle heads that turn the spindle direction 90 degrees; adjustable angle heads that can be either manually or automatically adjusted; multi-spindle heads that can, for example, drill several holes simultaneously; floating trimmers that can compensate for panel thickness tolerances; sanding units; mortising heads, and standard tool holders for single drilling, milling and sawing tools.
Techniks (techniksusa.com) in Indianapolis has introduced several new aggregates over the last year or so. The company’s FunctionLine variable heads accomplish routing, boring, mortising and sawing operations, and they work at any angle from zero to 100 degrees. They can be fitted with an ER25 output, or a Combi saw output that’s compatible with 45mm or 52mm bolt circles, and they can also accept the modular system. Techniks’ UltraLine variable aggregates have the ability to pivot a full 200 degrees for the most difficult custom profiling while adding fourth axis capability to the CNC router. They are recommended for sawing when using blades larger than 7″ and for V-grooving, heavy routing operations, and cutting MDF or composite materials.
Located in Marietta, Ga., GDP Industrial Tooling (gdptooling.com) offers aggregate heads for drilling, routing, grooving, sawing, sanding and more. The company has partnered with the German manufacturer Atemag to provide aggregates that fit most CNC machining centers including Weeke, HolzHer, Homag, Onsrud, Felder, Biesse, Busellato, SCM and others, as well as point-to-point machines.
Komo Machine (komo.com) in Lakewood, N.J. works closely with a couple of the largest aggregate tooling manufacturers to provide solutions for its CNC customers. The company says that combining a head with a C axis can deliver machining capability and flexibility at a fraction of the cost of a dedicated 5-axis machine. Among the options offered by Komo is a side-mounted auxiliary tool changer that allows for increased tool capacity. This is aggregate compatible and can be installed on both left and right sides if the machine has two spindles with programmable head spacing.
HSD Mechatronics has its U.S. headquarters in Fort Lauderdale, Fla. The company’s Wood Line aggregates (HSK and ISO) are featured in a catalog, available at www.hsd.it.
This article was originally published in the July 2021 issue.
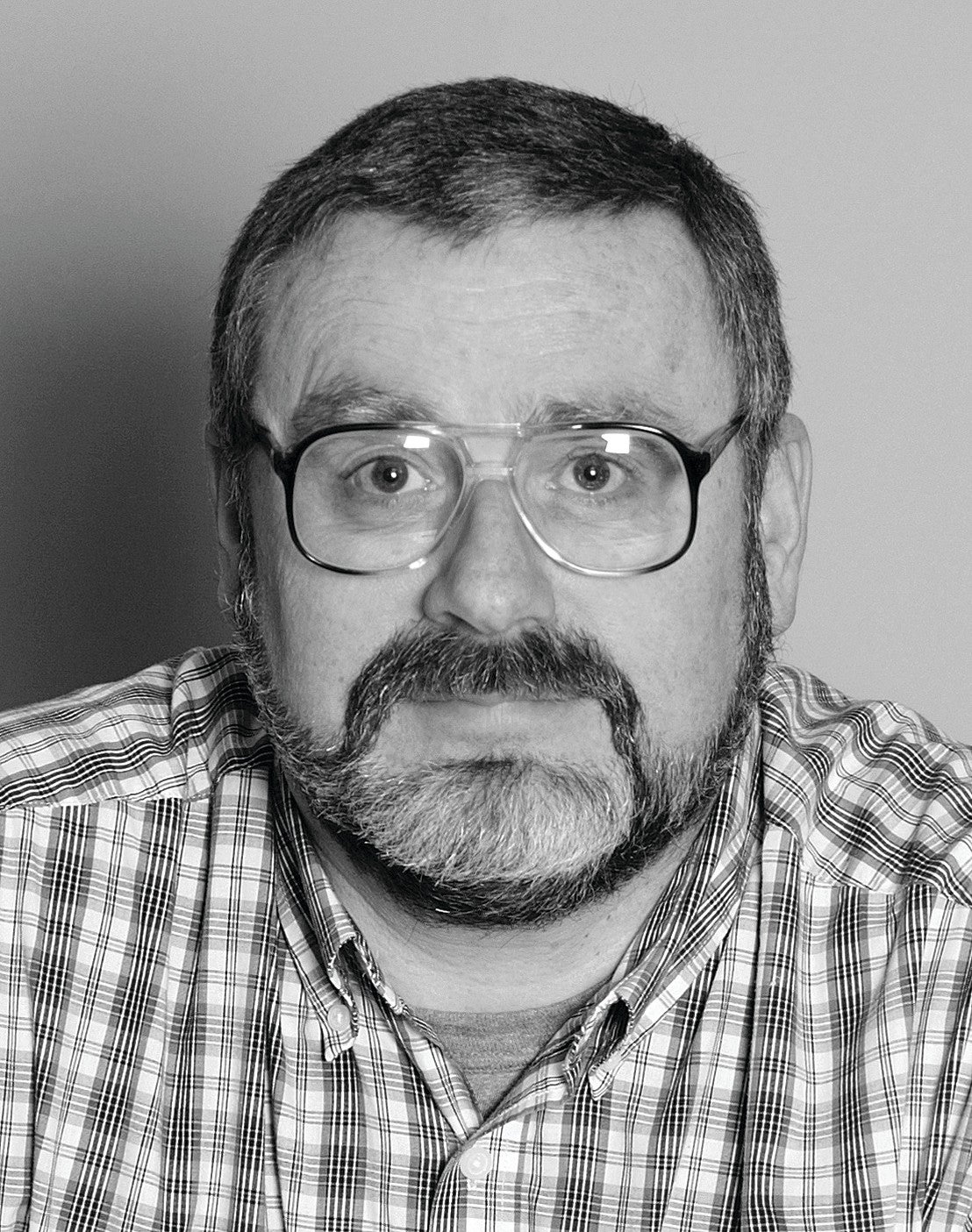