Banded together
Exploring the options, capabilities and materials used in the edge bander category
It seems like it should be a simple process — sticking tape to the edge of a board. So, why are there so many options? For a start, there’s the machinery: everything from jobsite tools to a fully automated, high production unit that can apply banding, trim for perfect edges, scrape the glue excess, and keep up with the flow of production. For smaller shops, there’s also a choice between pre-applied adhesive with heat guns or using glue pots. And as the machines get more sophisticated, there are plenty of optional add-ons. Then there are different types of banding, with varying degrees of durability and flexibility, and different machines to apply them.
But volume is the primary factor in deciding which type of edge bander to buy.
If a one-man shop occasionally bands the edges of a few shelves, the owner is probably going to use a heat source with pre-glued tape, a scalpel, some fine sandpaper, and lots of time. But woodshops that are building kitchens or baths will generally opt for a stationary machine, so step one is figuring out how much work will be done, both now and down the road. When that’s known, the next parameters to explore include processing speed (how many doors per hour?), the size of parts (does the shop sometimes make countertops, or large and cumbersome panels?), and both the width and thickness restrictions for the banding.
Two other important considerations are the ability of the machine to handle surfaces other than a straight edge (contours and corners), and the kinds of tape it will handle.
Capabilities count
Let’s take a quick look at options, starting with pre-milling. This is a process that smooths out the surface of the substrate (plywood, MDF etc.) so that the banding lies flat, and a better bond is achieved. Both carbide and diamond pre-mill cutters are options, and both can be serviced. Without pre-milling, the reject rate in production runs can be higher because gaps, bumps and troughs might exceed the ability of the adhesive to fill and correct problems.
While there are edge banders that only work with pre-glued tape, and others that only coat one surface (tape or substrate) from a glue pot, some machines will apply an even amount of adhesive to both faces and this averts the possibility of gaps or small areas with less, or even no adhesion.
While most banders can trim, it’s important to understand that process and know whether there are restrictions about the thickness of the banding. For example, some knives find thin material challenging, while others can chip hard or brittle tape. The ideal solution is computer driven servo motors that control both top and bottom knife positions for trimming. These can adjust as the finished thickness of panels varies.
Not all machines will work with all types of banding, so the shop needs to establish whether its material of choice is going to be PVC, ABS, melamine, HP laminate, PMMA, real wood veneer, or some combination of these. That decision is based on cost, availability, traditional construction methods in the region, and the need for various properties such as hardness and color or pattern retention. It’s a choice best made with the help of experts in the supply chain.
PVC (polyvinyl chloride) is a synthetic thermoplastic polymer. It’s essentially made by adding color to resin and spiking the mix with additives that balance properties such as hardness and bendability. This is the least expensive and most popular option for edge banding, but it’s not very ‘green’. PVC is valued for its durability, flexibility and easy maintenance.
ABS (acrylonitrile butadiene styrene) is more environmentally apt, and the waste product can even be burned. Because of its resistant nature, this is a thermoplastic polymer that is most often used where impact is possible.
Melamine is a polymer (a synthetic substance made up of very large molecules) that is most often applied to a rigid backer such as plywood, but it is also available as an edge band. The process of making it begins with urea, which is broken down to become cyanuric acid, and that in turn becomes the melamine resin. It can be susceptible to chipping, but it’s cost-effective and durable.
HPL (high pressure laminate) is plastic that is bonded to a backer such as a woven fabric, and it is made up of several layers that are melded together during a process that uses high heat and pressure. It is dense, hard, and once formed can retain a shape.
PMMA (polymethyl methacrylate, also known as acrylic) is another plastic that can have a transparent appearance, and that can blend seamlessly with the neighboring surface material. In fact, PMMA and ABS bands are often used to make laser joints. Larger shops that do a lot of edge banding are increasingly turning to lasers to make seamless joints, or at least ones that are not immediately visible to the naked eye. The technology is more expensive, so volume is key. High volume means a lower price per panel over the life of the machine. A lasered joint is generally more moisture resistant than hot melt or hot air banding.
Solid wood veneer lets shops make stable, flat panels with man-made substrates, and some tapes even come with grain running across their width, so the tops and bottoms of doors look like end-grain. Most natural edge banding comes with a heat-sensitive adhesive already applied, so that will determine what machine can be used to process it. Veneer comes in many species, widths, thicknesses, cuts and grain patterns. That thickness spec is very important, as very thin banding prohibits sanding before coatings are applied, while too much glue can leave a small, discolored reveal along the edges.
Another potential issue with pre-applied heat-sensitive adhesive on veneer is that is can be reactivated by new sources of heat, so it’s not the best choice around fireplaces, direct sunlight, radiators and the like. Aliphatic resin (yellow wood glue) is a better choice there, so a hybrid solution might be appropriate where most of the veneer is hot-melt glued and pieces in sensitive areas are hand-glued with resin.
Edge banding is also available in various types of metal tape, including aluminum and stainless steel.
Automation issues
Other functions to ask about are scraping, polishing, and slot cutting. Any option that reduces the hands-on clean-up time required of employees will directly contribute to reducing the cost per unit of edge banded products. As employees are increasingly expensive to train and retain, woodshop owners are turning to automation to pick up the slack.
While CNC routing is the most automated process, edge banding is a close second. These machines can be fully manual, partially automated, or fully computer controlled. Trends in the market seem to suggest that cabinet design will continue to lean more toward minimal maintenance, man-made, colorful materials (as opposed to natural wood), so edge banding seems to have a bright future. That’s a factor to consider when weighing the cost of a machine against its potential payback. And when shops lean toward edge-banded over natural wood doors there are other cost savings involved, such as the fact that plastic panels don’t require employee time to be stained and coated.
Automation options include add-ons such as feeding and unloading, robotic picking and inventory management, alignment and fixturing, and waste management. But the edge banders themselves can also harbor on-board functions such as heavy-duty roller feeding for thicker panels, or perhaps servo-grooving. This latter means that the machine can cut slots, rather than the shop owner having to take a stack of banded parts to another machine such as a CNC router to plow grooves for hardware or assembly connectors. Servo-grooving avoids those additional set-ups, which can include having to install and program an aggregate head.
Tilting tables and platens on edge banders can accommodate angled edges, but this is not always an option on less expensive machines.
Interchangeable trays let an operator switch colors and glue types quickly. Machines so equipped can also cater to the different temperatures and warm-up times required.
Processing can be speeded up and rejects can be reduced or eliminated with comprehensive digital readouts and sophisticated control panels that let the operator see a problem before it shuts down the line.
Some manufacturers offer a kit for banding really tight inside corners. For hardwood banding and other difficult materials, ask if there is a more powerful guillotine and tougher blades. For shops that make large panels, enquire about vacuum pods and other fixturing options. And that brings up another option: sometimes a small portable edge bander might be a better option for very large parts, where the tool moves so that the part doesn’t need to.
Some machines have adjustable pressure which can be used to snug up the edges of joints. Adjustable trim knives are offered on many models, and some use separate feelers to automatically make perfect end cuts. End trimming can usually be adjusted manually, pneumatically using the control panel, or fully automatically using robotics and AI.
Many of these options are available through edge bander aggregates, such as a polishing unit that has cotton pads or brushes and is often paired with a liquid sprayer that emits a cleaning and buffing solution. A surface scraping aggregate can clean up bigger glue residue spots. Some machines come with a heat lamp that runs on quartz infrared energy and pre-heats the substrate before the glue is applied, for better adhesion and a slightly longer open time.
These are just some of the questions to ask when beginning the search for a new edge bander. That quest can begin with visits to other woodshops to see what they’re doing, or checking in with a supplier that carries more than one model or line. Trade shows such as AWFS and IWF are invaluable resources when it comes to investing in edge banders because a shop owner can physically see all the latest models and question the factory reps in person.
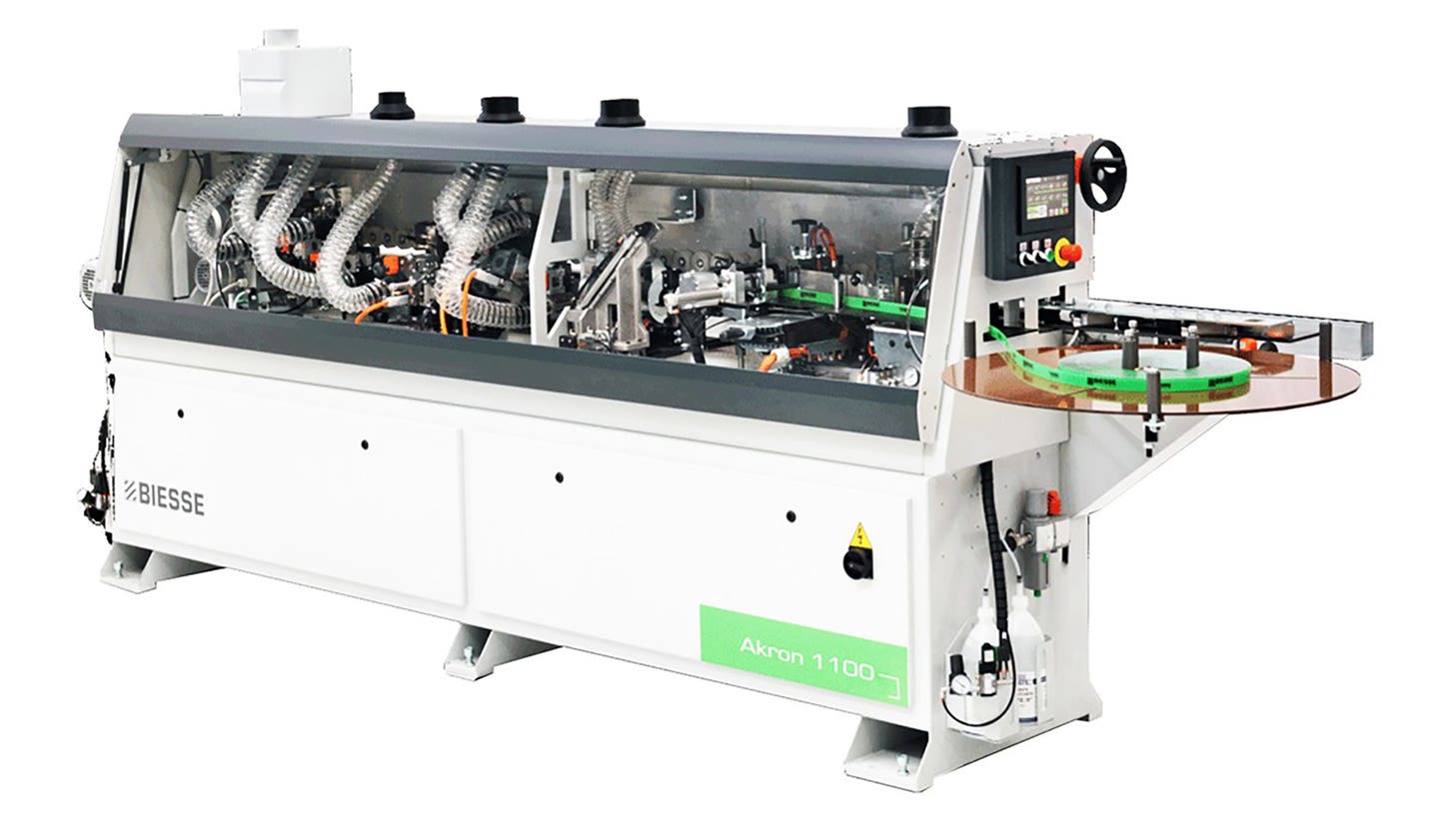
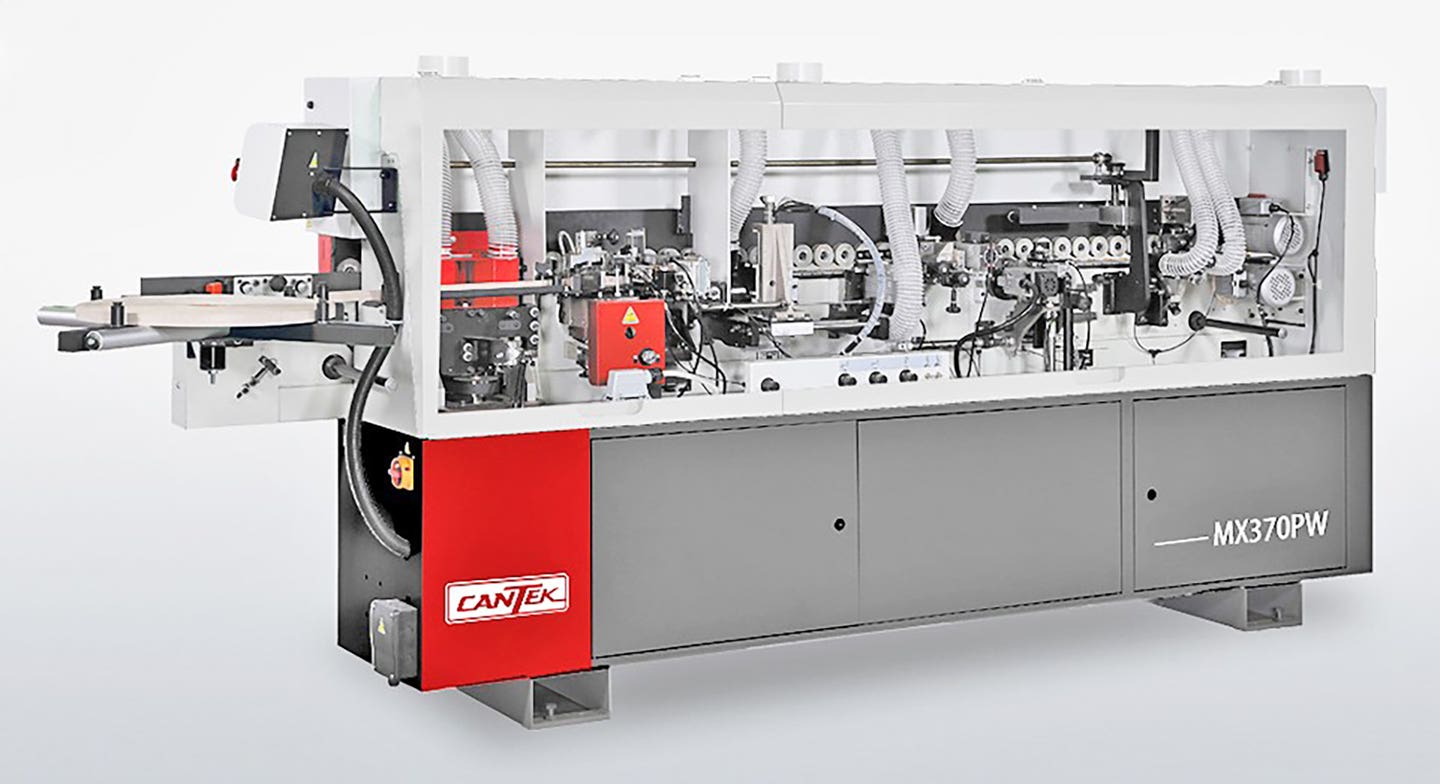
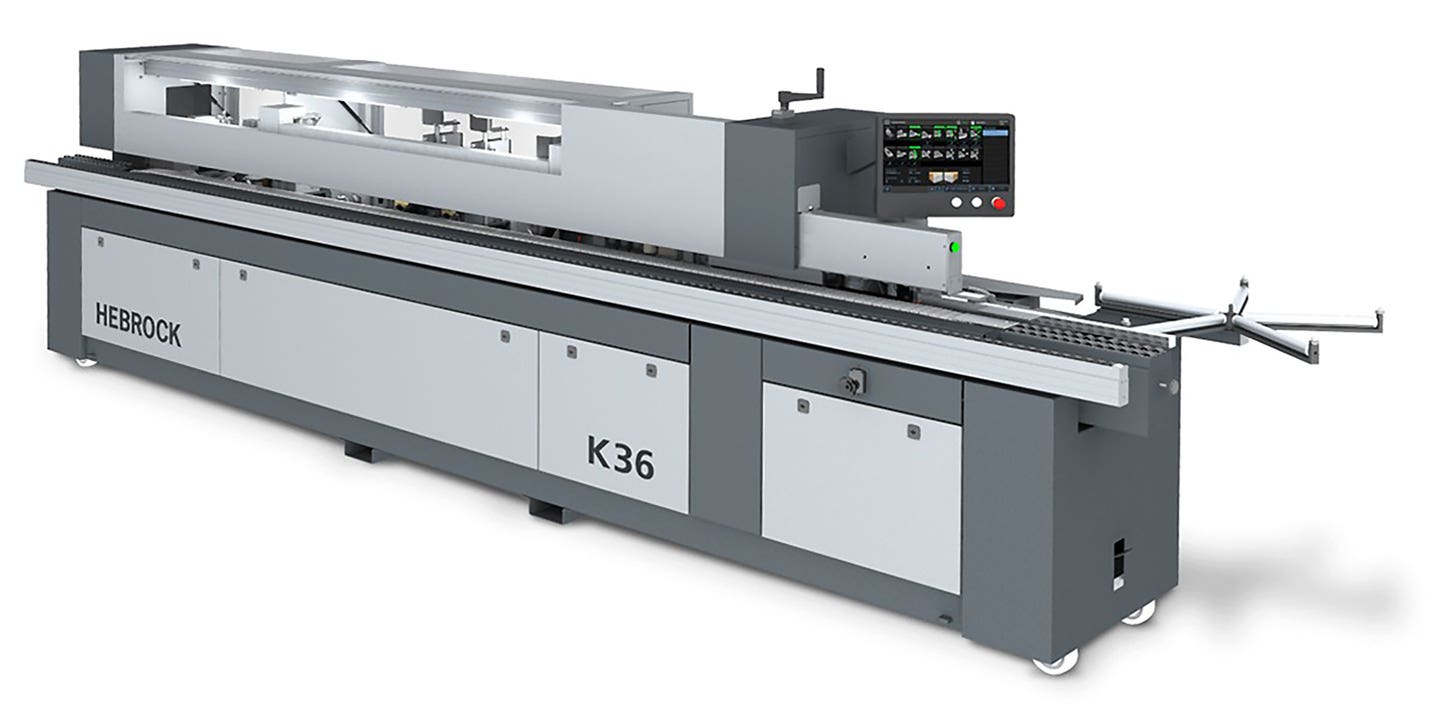
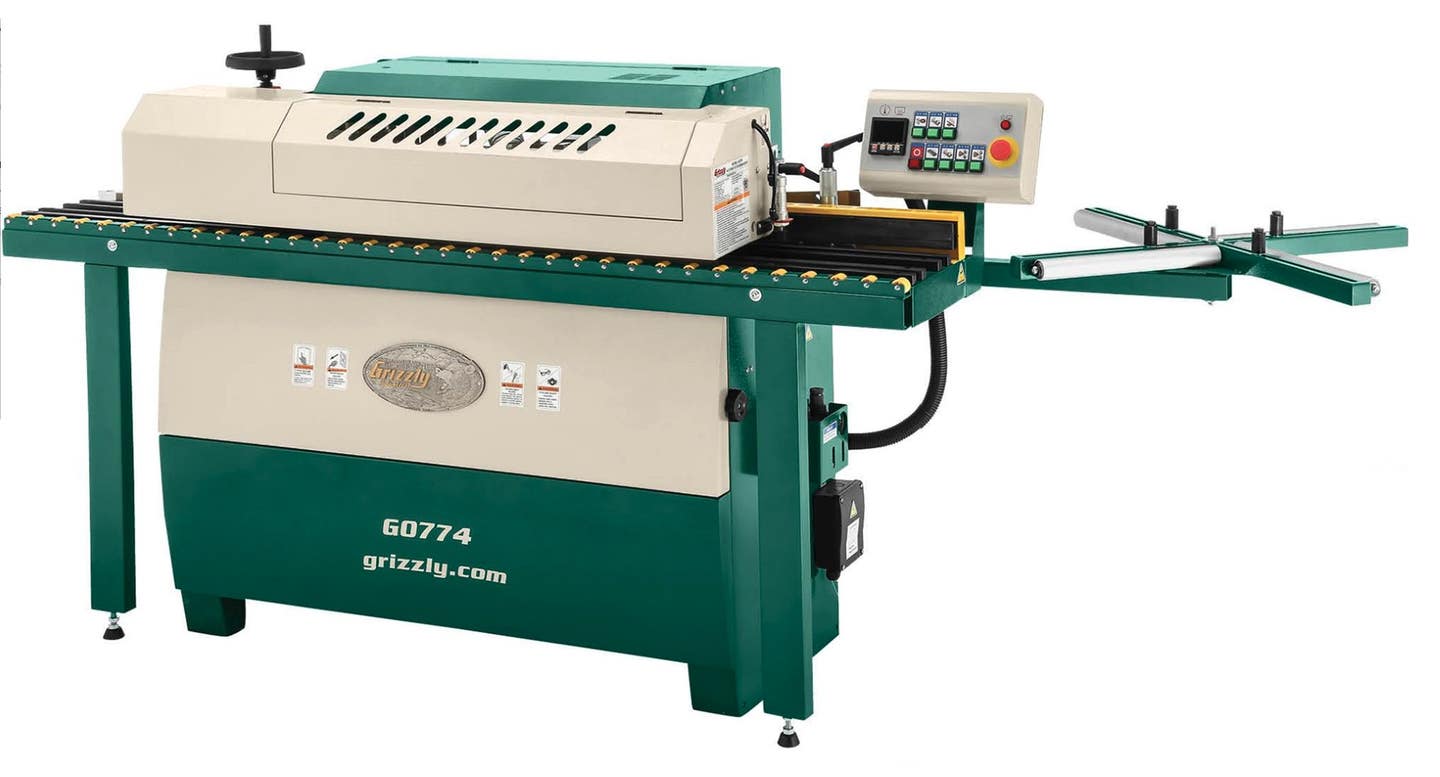
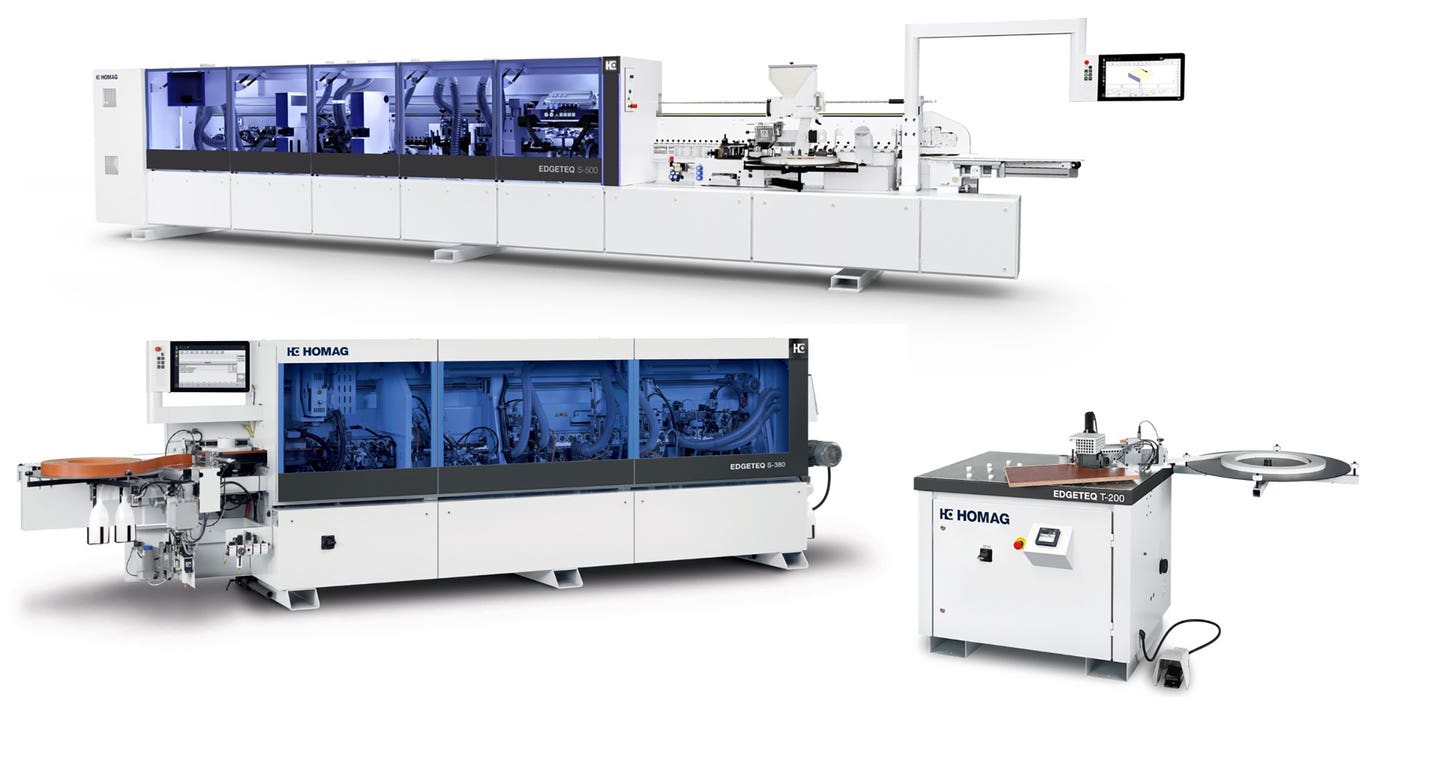
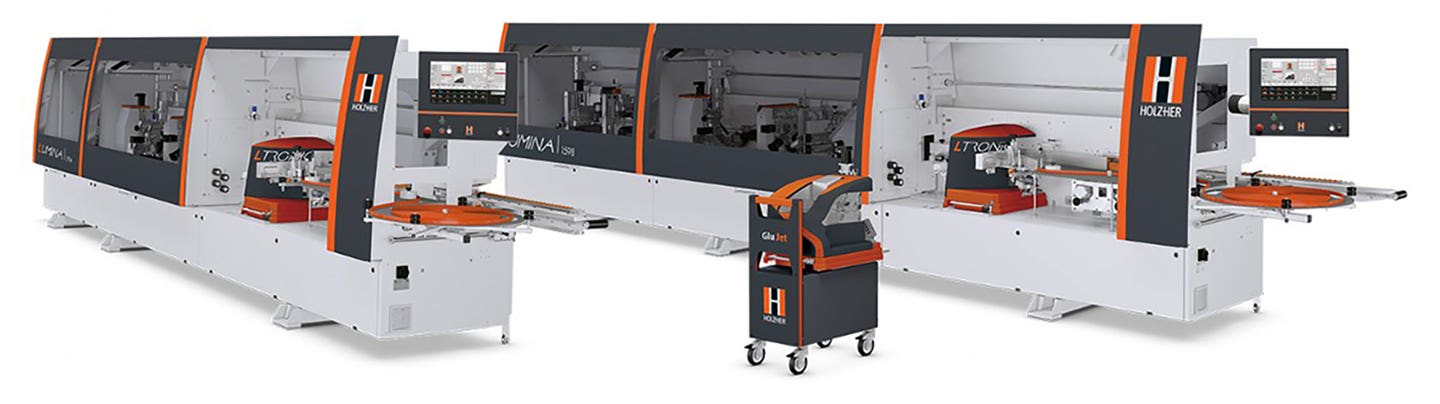
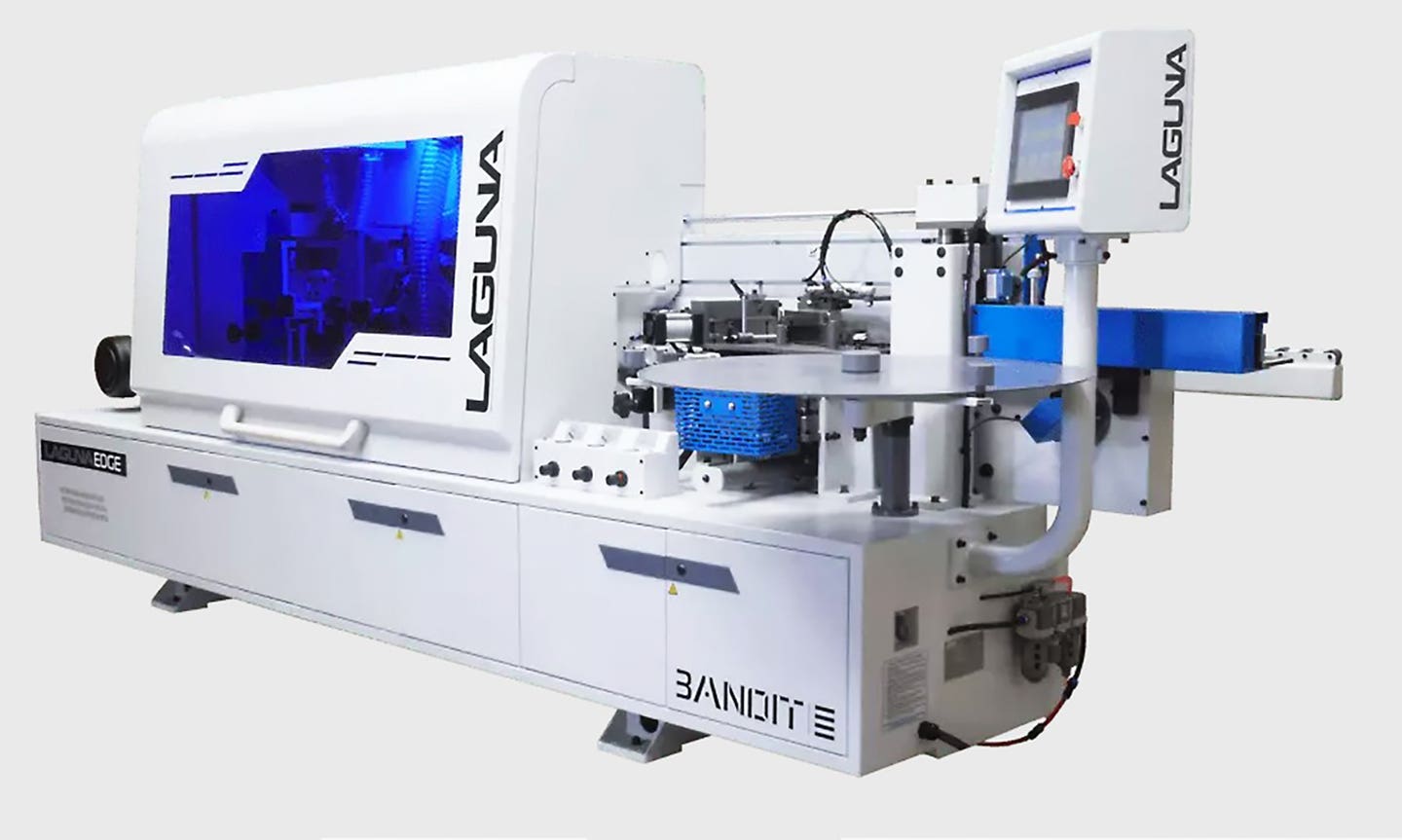
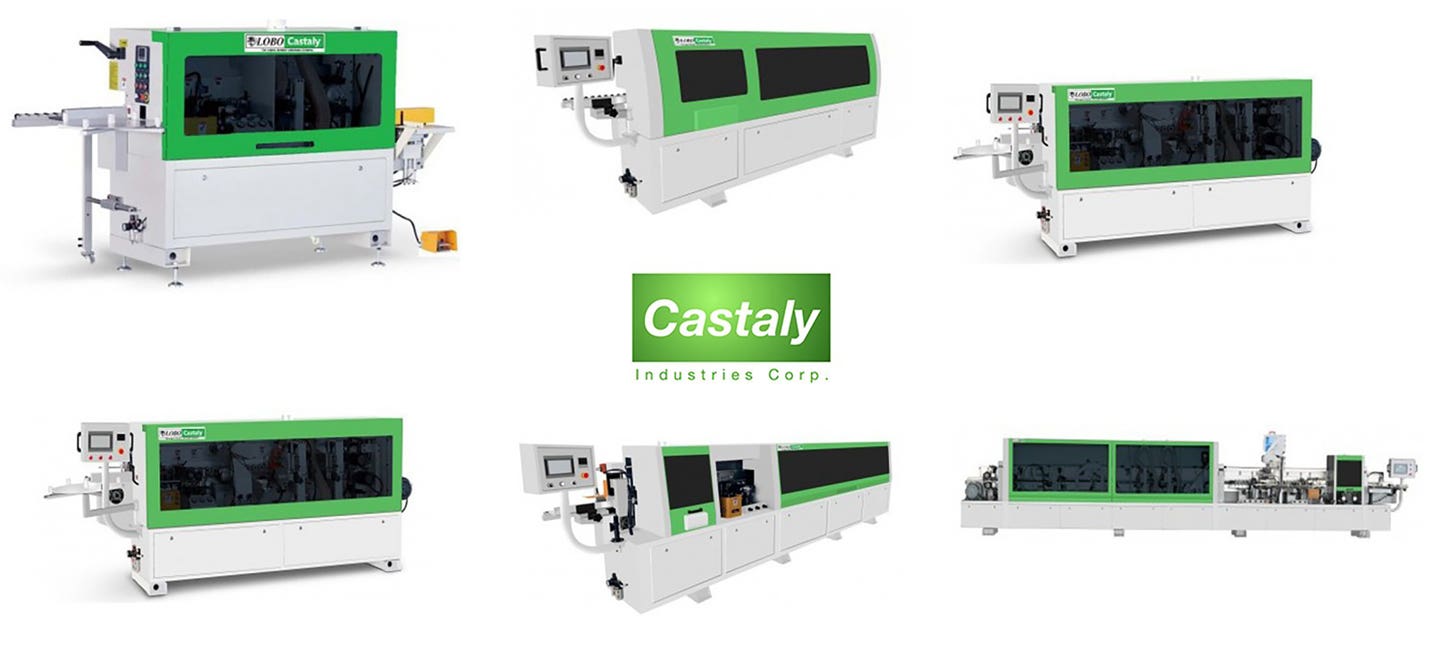
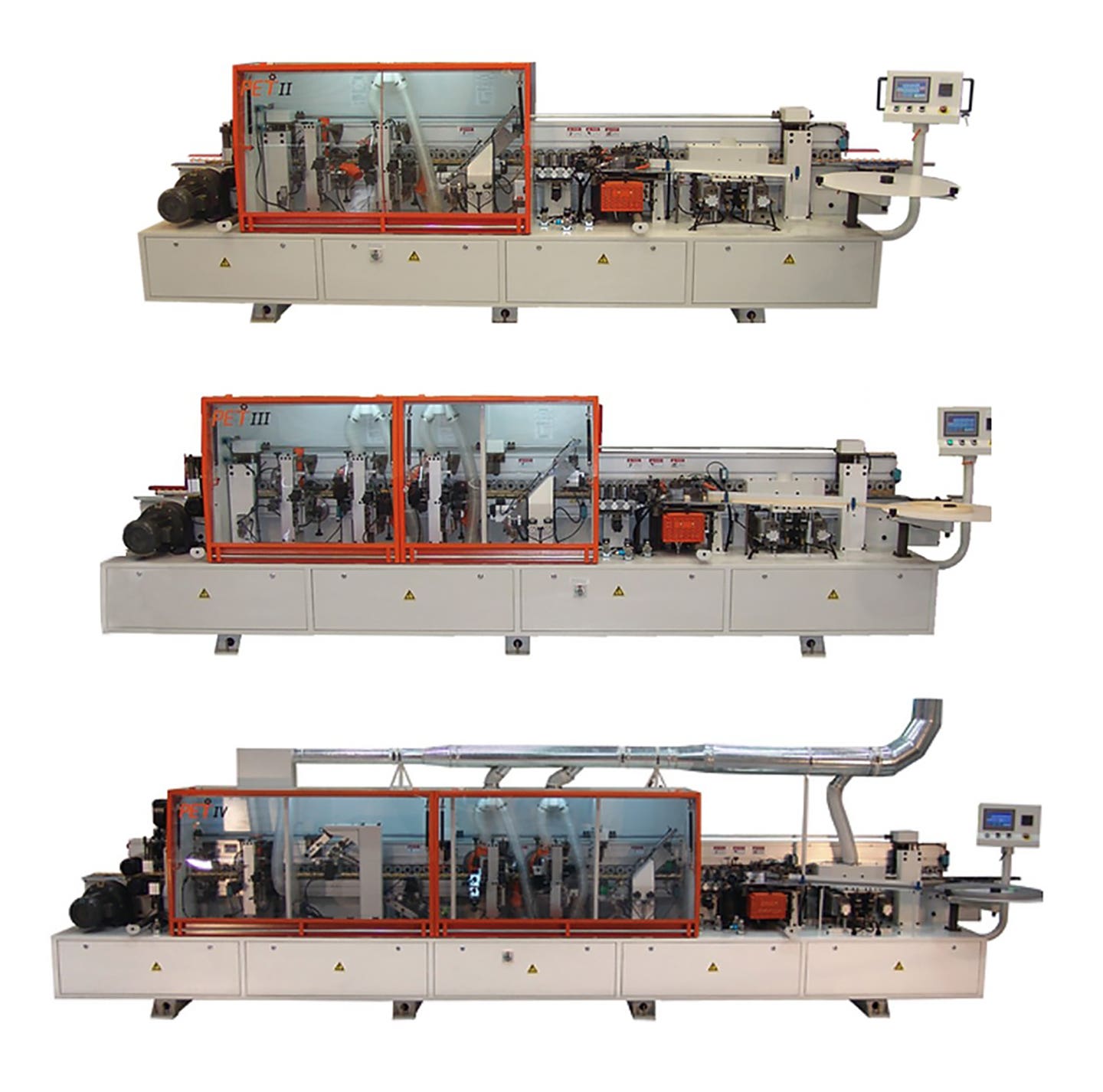
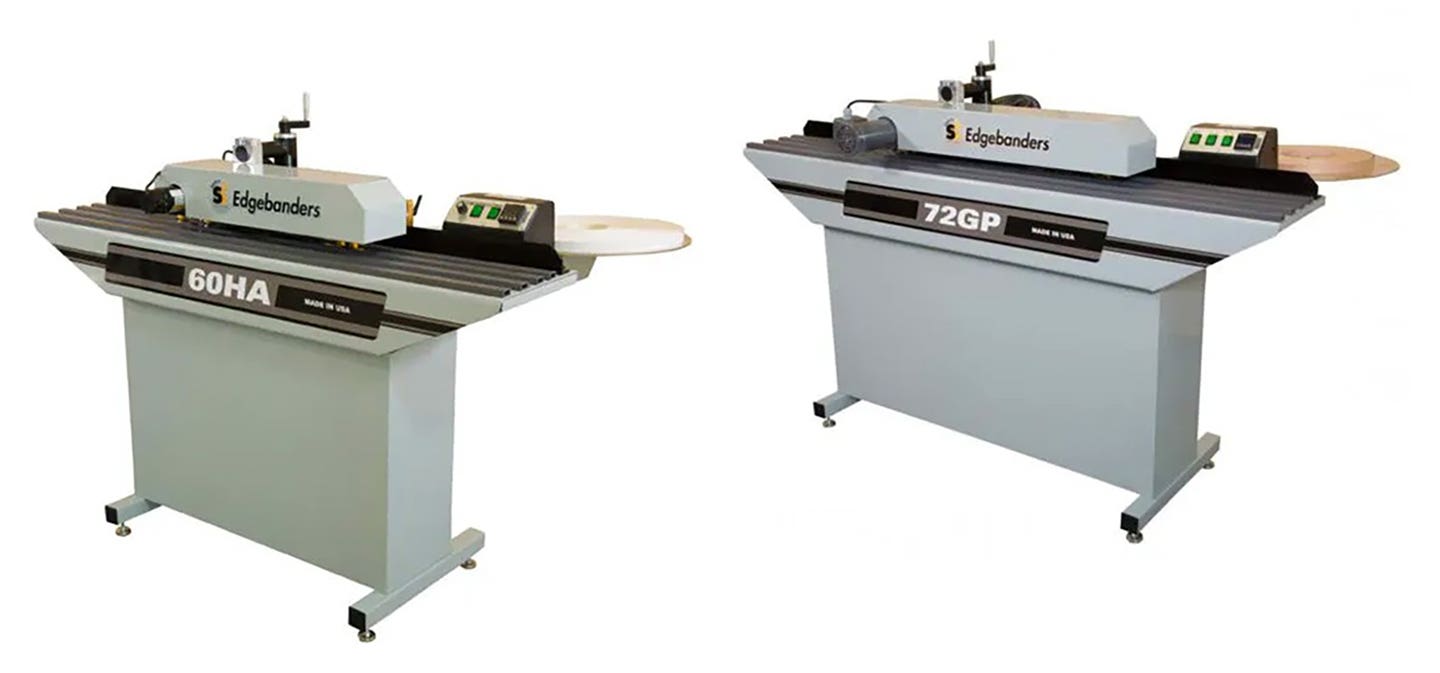
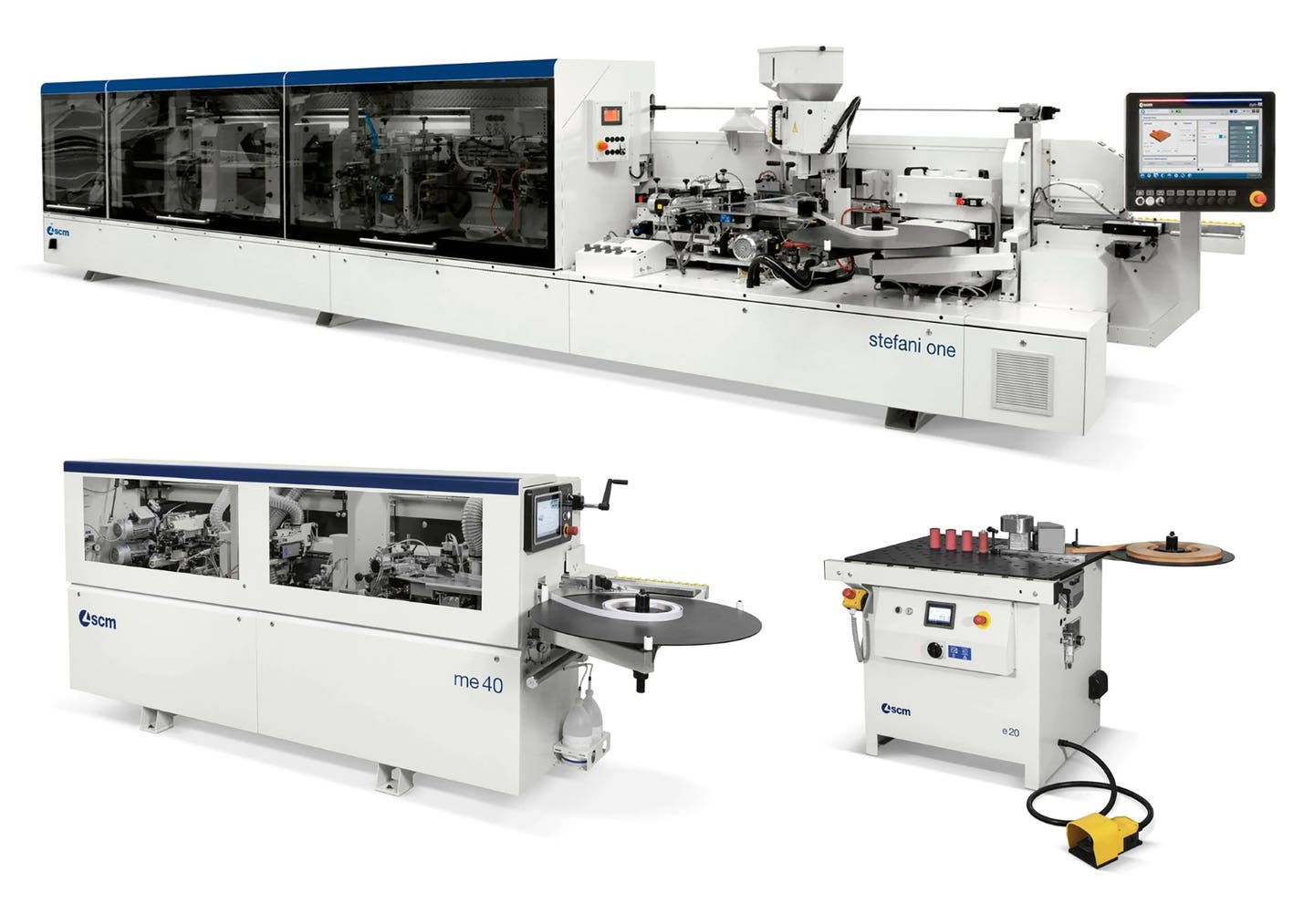
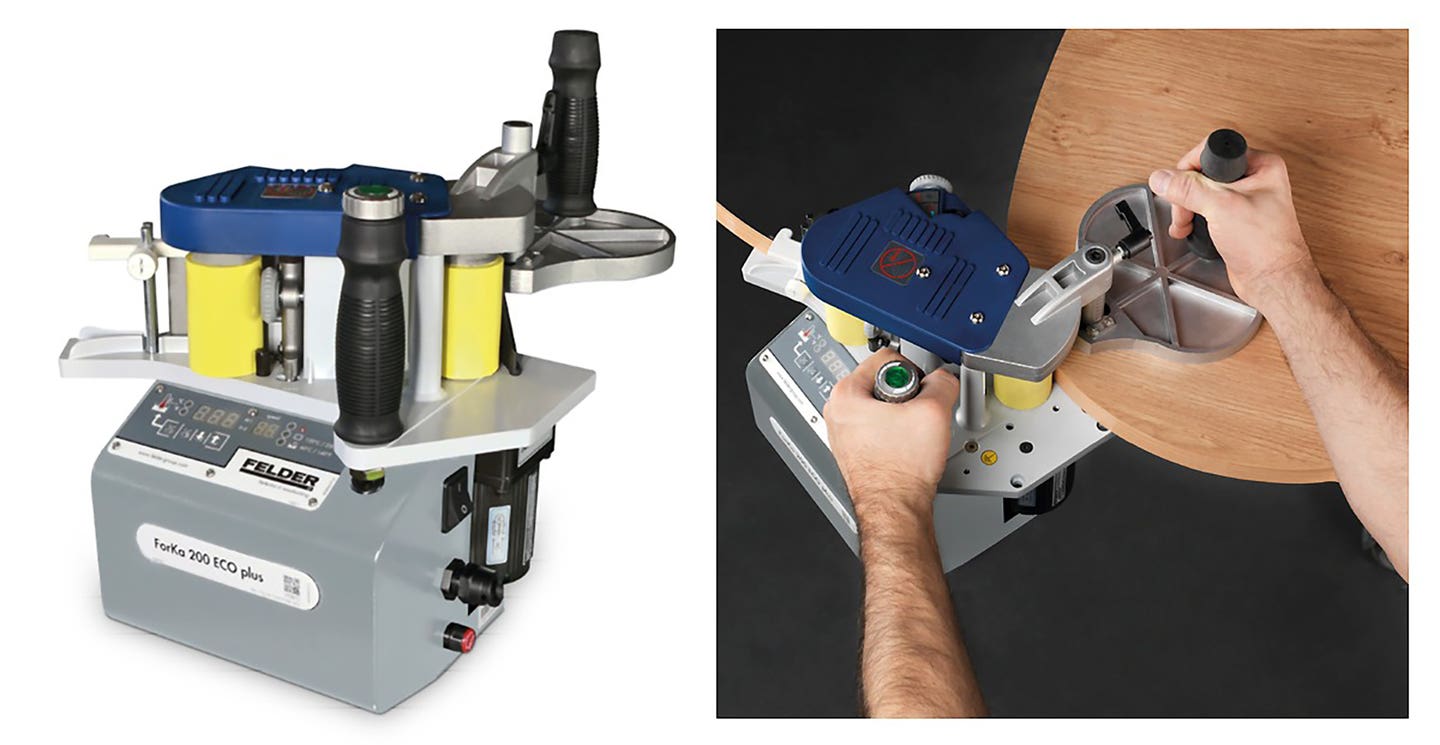
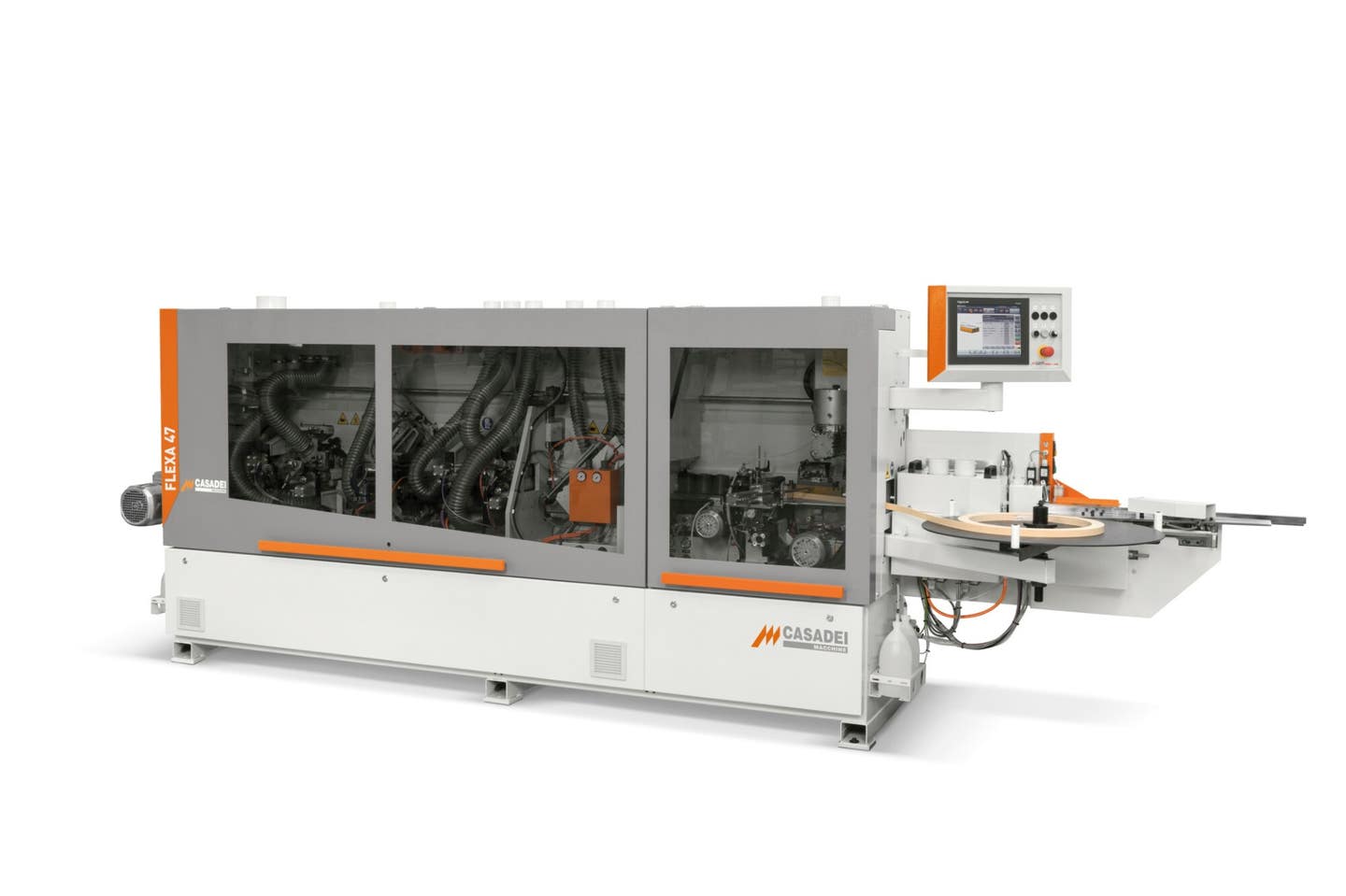
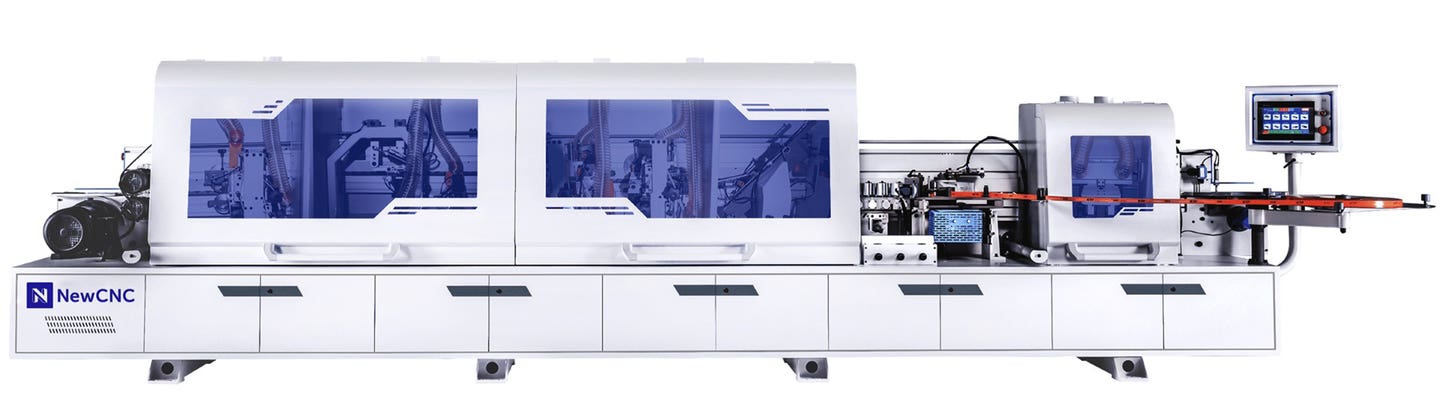
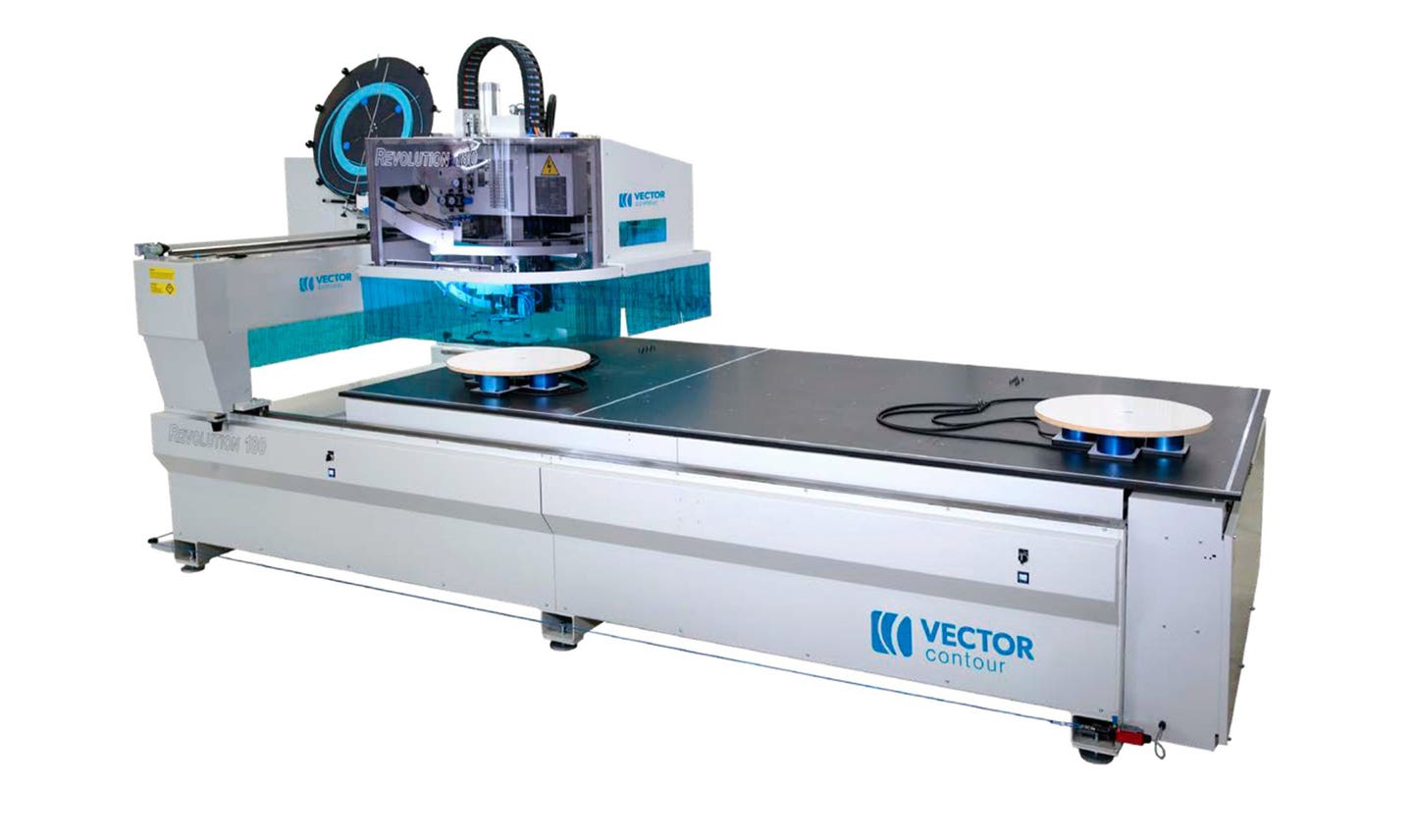
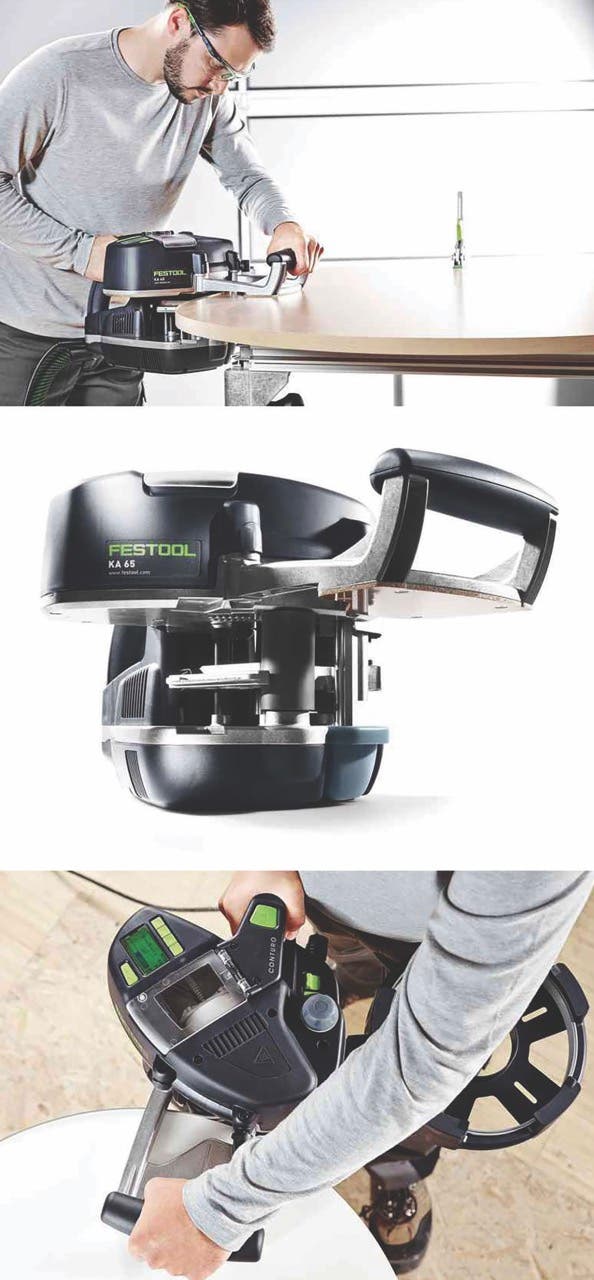
Sources for edge banders
• Altendorf (altendorfgroup.com) • Atlantic Machinery (atlanticmach.com) • Biesse (biesse.com) • Cantek (cantekamerica.com) • Casadei-Busellato (casadeibusellato.com) • Felder (felder-group.com) • Festool USA (festoolusa.com) • Grizzly Industrial (grizzly.com) • Hermance (hermance.com) • Holz-Her (holzherusa.com) • JKL Machinery (jklmachinery.us) • John G. Weber (johngweber.com) • Laguna Tools (lagunatools.com) • Lobo (lobomachine.com) • Maksiwa (maksiwa.com) • NewCNC.com (newcnc.com) • Panel Wood Machinery (panelwood.com) • Pro Edge Technology (proedgetechnology.com) • Safety Speed Mfg. (safetyspeed.com) • SCM (scmgroup.com) • Stiles Machinery/Homag (stilesmachinery.com)
Originally published in the June 2024 issue of Woodshop News.
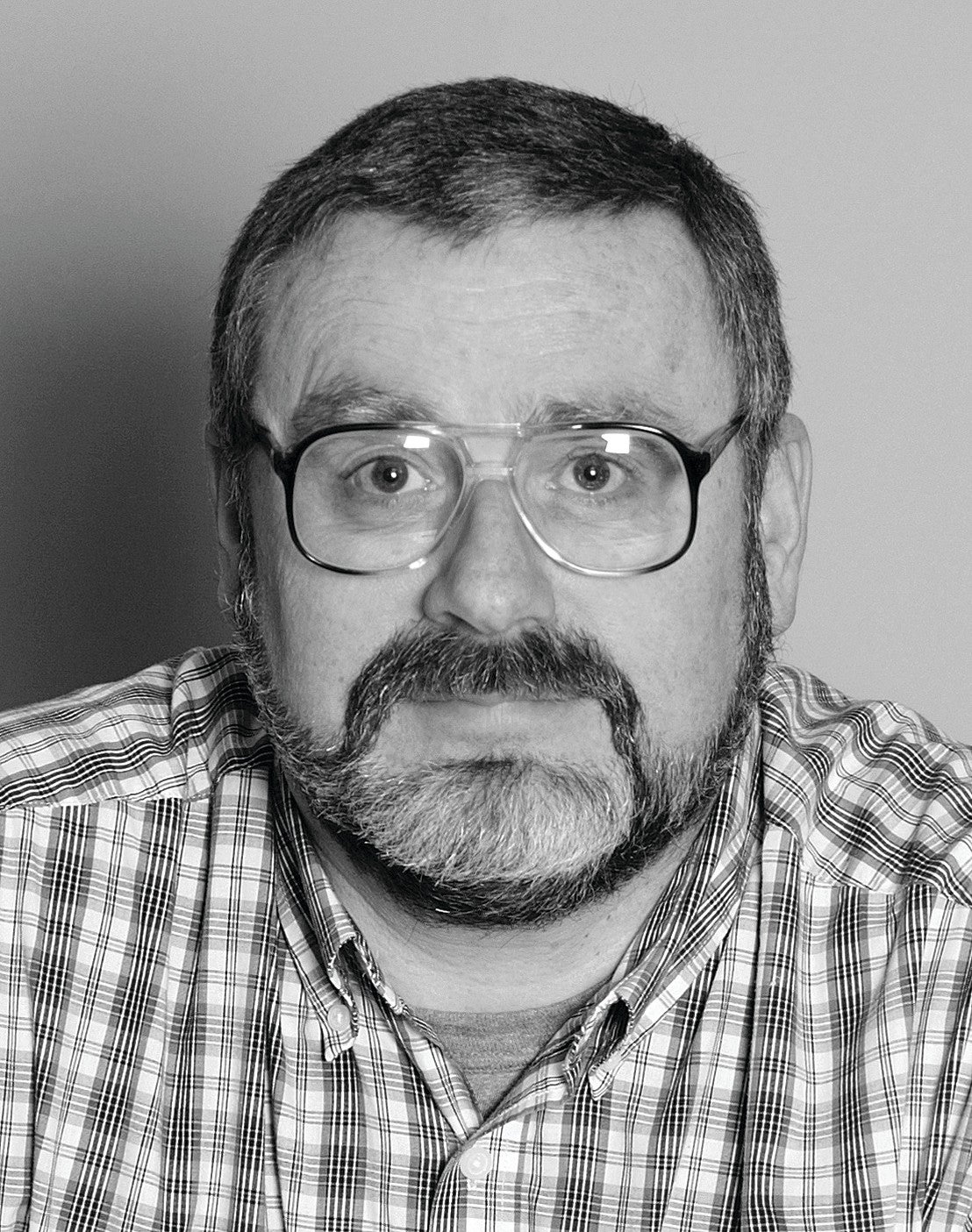