Beyond Basic Boxes
There are several design and detail options that won’t destroy budgets or disrupt production as they elevate the value of work. Those include outsourcing design elements, adding hi-tech accents such as controls and lighting, introducing materials other than wood-based products, and getting creative with hardware.
Chippendale, Stickley, the Greene brothers, and even Frank Lloyd Wright shared a common trait. They, along with numerous other noted woodworkers, were accomplished interior designers who created rooms and entire buildings specific to their furniture. Tables and cabinets became part of a larger environment – and one in which design elements were often reflected. Cloud lifts and Medieval pegs found their way into everything from entry doors and structural beams to the most infinite details of desks and dressers.
Today’s cabinet shops build basic boxes with openings, add doors or drawer fronts, imbue the surface with color through sprayed coatings or lamination, and complete the work with screwed-on hardware. The richness of a Hepplewhite or Sheraton room stands in stark contrast to the minimalism of modern design.
That’s not all bad. It’s an indication that wealth is more evenly distributed today, and a much larger segment of the population can enjoy products that are built in custom cabinet shops. It also reflects changing lifestyles and evolving values, but even so, the basic box is a bit boring. Minimalism also makes one wonder whether there is some hypocrisy in using the word “custom” to describe work. Perhaps we should question how bespoke a kitchen is, when a thousand other shops are using the same materials and processes. Sometimes, the only unique (custom) aspect that we offer is differing dimensions.
So, how does a woodshop remove listless ennui from its catalog? Is there a way to add zest without going gaudy? There are several design and detail options that won’t destroy budgets or disrupt production as they elevate the value of work. Those include outsourcing design elements, adding hi-tech accents such as controls and lighting, introducing materials other than wood-based products, and getting creative with hardware.
There are also ways in which new equipment such as an aggregate head or a vacuum press can augment current production processes, while allowing the woodworker to expand a catalog using in-house solutions. Equipment options invite the woodshop’s designer to think about the core kitchen value, door design, in more creative ways – perhaps using miters rather than butt joints, or horizontal openings instead of always going vertical. CNC upgrades can make new edge profiles possible, or they might allow the operator to make, say, relief panels that can interrupt the flat plane of a kitchen. For shops that don’t run CNCs, or are not ready to upgrade, those options can be outsourced and included at known costs, and that makes it easy to include them in an estimate.
Acquired embellishments
Decorative and functional elements such as supportive corbels, window and desk valances, on-lays, rosettes, split turnings, built-up moldings, or furniture feet and legs are widely available online, so it’s easy to download images and include those as part of the conversation with potential clients. Some design details are very easy to install, yet they can have quite an impact. For example, an on-lay is a thin relief that is simply glued and clamped to a flat surface to lend the illusion of hand carving.
Most woodworkers are familiar with traditional designs that include grapes, acanthus leaves, shells, scrollwork and even animal motifs. Contemporary versions espouse Art Deco, geometric designs, and other timely themes. The shift from natural wood coatings to painted doors and casework has made it easier to include on-lay accents because painting makes them a little more subtle, but still tactile and textural. Most are made of wood or resin/wood combinations and take paint well, but it’s a good idea to test the adhesion of the coating. And keep in mind that the on-lay can also be a different color: just paint it separately before applying it.
Instead of standard clear glass, using art or textured glass inserts allows a cabinetmaker to build doors that allow light to pass through, but block the views of clutter. Opaque glass panels can distort the contents of a cabinet interior to maintain privacy, but their translucence means that LED interior lighting can still be used as an accent. Art glass can also add drama and color at a low cost, as small amounts of these accents tend to have a big impact. Think about the effect of a little splash of brightly colored glass in a white kitchen. Sometimes designers pick up the color of the glass in the pulls and knobs, for a cohesive and more comprehensive design.
Woodshops have been installing thin wood and laminate appliance panels for decades. Some shops get more creative by transforming fridge doors with frame and panel inserts that maintain the stile and rail profiles of the surrounding doors but use a different species, material, or color in the field for dramatic effect. For example, the panel might match a backsplash or an existing wall covering. For this to work, the edge of the frame will need to be rabbeted to fit the appliance retainer molding, but this is an area where a shop can be quite creative without adding a lot of cost. It is, in essence, just another door to build.
Vent hoods that match the casework are a longstanding upgrade. But that can be a challenge if the customer wants to go with the emerging trend of losing the upper (wall) cabinets in favor of flee-floating shelves or even empty expanses of wall. There are cooktops with almost invisible built-in vents, so nothing shows on the wall. And then there are hoods with oversized, exposed ductwork that runs all the way to the ceiling and suspends a glass, chrome, or copper hood above the stove. If you need to disguise a problem, sometimes the best way is to celebrate it. The large duct can deliver an interesting optic, but unfortunately it doesn’t deliver any revenue for the woodshop unless there are floating shelves to build.
Wine racks have always been popular accents, but they assume that either the homeowner only stocks a few bottles or else has a large cellar located elsewhere. Storing wine properly can help it keep for decades, but improper storage can quickly destroy it. Both reds and whites should be stored at constant humidity and at temperatures not exceeding 68 degrees Fahrenheit, so a wine fridge is a much better design option than an open wine rack. Like wood, traditional cork expands and contracts with temperature fluctuations and that can allow air in, so corked bottles should be stored on their sides, never vertically, to keep the cork moist. And no wine should ever be stored in direct sunlight. The darker the room the better, as UV rays can accelerate deterioration. That’s why French vineyards have ‘caves’, or cellars, where daylight is not invited. Wine fridges should also be installed away from vibration, so don’t pop one in next to a clothes dryer.
Another popular design element is using turned legs and half turnings on islands, outside corners, and in nooks, and that may present one of those build-a-whole-room opportunities. If the kitchen has enough space for dining, the woodworker might suggest carrying the cabinet’s leg design into a free-standing, custom built table. The top can match the kitchen countertops, the apron might pick up an existing molding profile, and the legs could be painted or stained to match the cabinet coating.
Electronics and lighting
With the shift from office to home office over the past two years, it’s no surprise that power strips and pop-ups have become mainstream design details. Beyond those plug-ins, many kitchens and home offices are using invisible phone and device chargers, LED strips inside base cabinets that turn on when the door opens, mechanisms that open doors or drawers with a light touch or tap, and other controls that operate with motion sensors. There are remote-controlled cabinet locks that keep toddlers out of toxins and teens out of tequila, and of course a whole range of new accent, task and ambient lighting options.
LEDs have blown the doors off lighting design because they’re small, flexible, cool (in both senses), come in different colors and beam shapes, and are relatively inexpensive to buy, install and run. They can be triggered by motion sensors and placed in toe-kicks, soffits, behind crown moldings, above countertops, inside cabinets, under or above floating shelves, under the edges of counters, and basically anywhere there’s a lip, reveal or rabbet. It may be a good idea to involve a lighting consultant early on in a casework project, rather than waiting until after the cabinets are in. Task lighting can be especially bright and intense, and LEDs that are over about 3000 on the Kelvin scale can be very stark and harsh because of the amount of blue light they emit. There is a possibility that this might affect circadian rhythms and sleep patterns in some people, so the color of LEDs is something to discuss with the lighting consultant.
There are lots of new ‘smart’ appliances that can be worked into kitchen designs, such as personal espresso machines and coffee grinders; Instant Pots that are controlled over Wi-Fi through apps (this is a slow cooker, pressure cooker, rice cooker and steamer all in one); separate bread, ice cream and pasta making machines; thermal immersion circulator machines that cook sous vide; Wi-Fi based hot air fryers; and even smart tea infusers. Some of these won’t store easily on standard shelving, so they may present an opportunity for the shop to offer a custom design – perhaps something like a mixer lifter (a hinged shelf that pops up out of a base cabinet), or even an old-fashioned appliance garage.
Homeowners may also request that the designer build in space for Bluetooth speakers and video screens, security system monitors, and even health-monitoring equipment for diabetes, heart conditions and other challenges. Staying abreast of the latest trends and fads in electronics lets a shop create custom solutions that may not be available through big-box stores or online cabinet sellers.
Non-wood materials
In an age of impressive technology, why are almost all cabinets still made with wood or wood-based products? It’s not just because of the warmth of natural surfaces, because most casework is now coated with either foil or paint. So, is it perhaps because the industry has developed machinery and tools to work this wonderful renewable resource, and doesn’t wish to change? Or perhaps because our species has a natural aversion to the aesthetics of plastic? Whatever the reason, and there are probably many, we have stuck with wood as our core medium for casework, despite the evolution of complementary materials.
That doesn’t mean we can’t use other materials to augment the wood, especially in doors. Several suppliers offer decorative metal grilles to replace plywood door panels. Some designers are using contrasting interiors in cabinets with see-through glass or grille doors, and they’re not just painting the interiors. They are adding texture with rusty corrugated tin, used brick slices and even recycled plastic and glass. The theme is salvage or recycled based, which designers are labeling as ‘elegant repurposing’.
Perhaps it was the pandemic that focused consumer attention on non-porous, easily cleaned surfaces. The past couple of years have seen a big jump in the use of commercial kitchen materials in residences, such as copper and stainless-steel cabinets. Adding other metal design details (moldings, edging, soffits) can be a challenge as they are hard to make in-house, so they need to be outsourced. But using flat metal sheet-stock in 5-part door panels and drawer fronts can be an affordable in-house option if there’s no bending, shaping, or forming to be done, and they just need to be cut to size. Another challenge is the different expansion rates of wood and metal, so shops need to design for movement when they mix media.
Re-using building materials is more in vogue than ever before, and it has become a distinct selling point for woodshop designers. Take, for example, paint. Nobody has ever completely used up a can of paint, and that presents an opportunity. PaintCare (paintcare.org) is a non-profit organization that helps coatings manufacturers plan and operate leftover paint stewardship across the country. There are currently programs in nine states and Washington D.C. where homeowners and businesses can take unwanted, leftover paint to a PaintCare drop-off site. So far, more than 60 million gallons of paint have been donated, and much of that has already been recycled by coatings manufacturers. Letting customers know that their design includes recycled or reused materials used to be a bad thing, but that’s not necessarily true anymore.
Sometimes a simple and inexpensive idea can have a surprising impact. Foil (vinyl) decals are trending right now, where a door or drawer receives, well, stickers, that add some flair. Companies such as Cabinet Accents (cabinetdecals.com) sell packages of themed decals that a woodshop, and often a homeowner, can apply to woodgrain or painted doors to add some pizzazz. The themes include diamonds, fleur-de-lys, barbs, hearts, pineapples, seashore items and waves.
Hardware and high spaces
One very custom aspect of residential design is that it can be tweaked to better suit a homeowner’s physical attributes, such as raising or lowering countertops, widening passageways for wheelchairs, or using retractable (flipper) doors on hard-to-reach cabinets. And one of the more positive ways to augment a kitchen or bath design is to add convenience and usability by including task-specific hardware. Specialty drawer organizers and sliding cabinet hardware are widely available, as are item-specific storage units that can add a custom feel to a job. Those include anything from tie or shoe racks to alternatives for lazy susan corner solutions.
One less obvious option is using the toekick space under cabinets for storage drawers. With the advent of motion-sensing slides, these can be opened by passing a foot in front of them, obviating the need to bend down and search for a drawer pull. If a slightly taller drawer is needed, the height of the cabinet can be reduced a little, so the countertop remains at an ideal height.
Hardware can also make a drab design dance. Custom and handmade art knobs and handles are available from a huge number of suppliers and often at prices that surprise. Many are American made, and some use found objects such as seashells, rocks, or even railroad spikes to add some authenticity and once again hit on that recycling theme. High impact hardware can become a dramatic design detail in a minimalist, monochrome kitchen.
If a home has high ceilings, that soffit space above the wall cabinets can hold a whole other row of cabinets. Adding a library ladder can make them easily and safely accessible. That kind of design detail returns us to the original theme where woodworkers create rooms specific to their furniture. Beyond ladders, a designer might consider the idea of breaking up solid walls of cabinets by building separate, moveable pieces that carry the same design details but allow for change. By building, say, a free-standing dish/glassware cabinet along with a secretary desk with the same dimensions (especially width), the two units can be switched at will by the homeowner to give the room an air of change, or to alter its function. Using furniture feet and a different paint color on these units can add some impact, too.
It’s not exactly Chippendale, but he’s a bit dated anyway.
This article was originally published in the January 2023 issue.
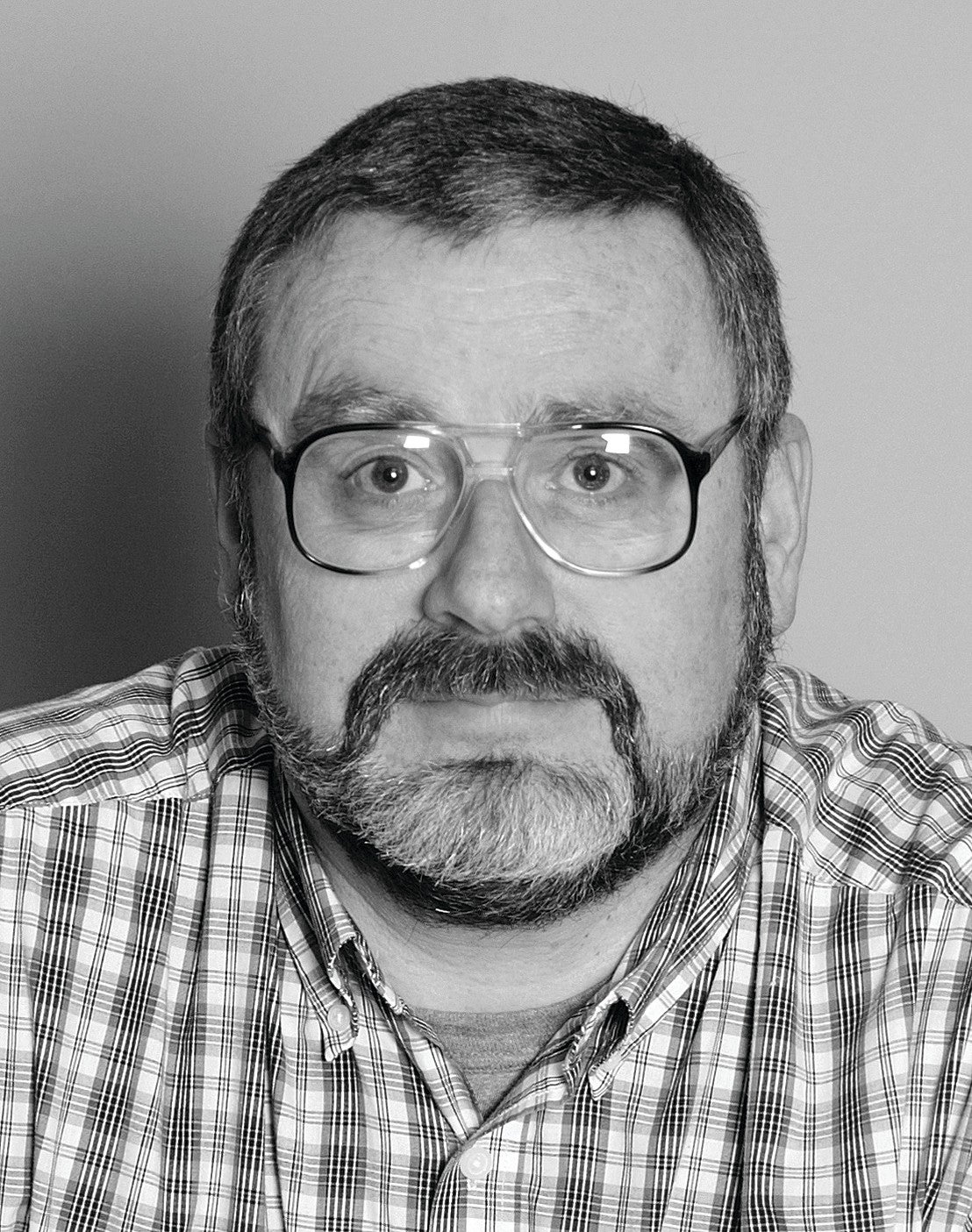