Building a safer saw
He was in a hurry. About six years ago Thomas Skaggs, a studio furniture maker in Champaign, Ill., was cutting stock on his cabinet saw and hadn’t realized that he’d…
He was in a hurry. About six years ago Thomas Skaggs, a studio furniture maker in Champaign, Ill., was cutting stock on his cabinet saw and hadn't realized that he'd started the cut without locking down the fence securely.
"As I was pushing the stock through, I noticed that the kerf was drifting," he recalled. "I looked down at the fence, and at that point realized that the fence was moving. But it was too late and the cut had gone through. The waste side of the cut caught the blade and kicked back."
The waste side Skaggs referred to was a narrow, tapered piece of cherry he described as "spear-like."
"It happened in an instant, and there was no time to react or do anything. I felt a huge kick to my abdomen, and without looking down I kind of just moved my hand there and realized a piece of wood had impaled me. Without even thinking I pulled on the stick, and that was when it really clicked that, 'Hey, this was inside me.' "
Skaggs' wife — by chance a registered nurse — was in the house and she rushed him to the emergency room where he underwent two hours of trauma surgery. Afterward, the doctor told Skaggs that the piece of wood, which had thrust 5" deep into his abdomen, had missed his liver by a fraction of an inch.
At this point, you're probably wondering: Was he using the guard and splitter?
"No," he admitted. "I wasn't.
Like the guard and splitter arrangements of many stationary machines at the time, Skaggs' guard system wasn't easy to use, easy to see through or easy to remove and re-attach. And, like many woodworkers (few of whom ever admit it), he took it off. This issue, and the danger it imposes, isn't exactly an industry secret.
"There are two reasons why people don't use their barrier guards," said Jason Feldner, product manager for Bosch. "One is that they can't see what they're doing. The other is that they're just two darned hard to get on and off. Once it gets taken off, it stays off."
Responding to the problem
No manufacturer of power woodworking machinery can force customers to practice safety in the shop, but are there things they can do to make safety easier for the end-user to achieve? Judging by the appearance of new technology in the woodworking machinery industry, mandates from government and other bodies for safer equipment, and the efforts of the manufacturers themselves as evidenced by the features on their latest tools, the answer appears to be a solid yes. The first of these is to make saw safety equipment easier to use, particularly at times when guarding has to be removed temporarily for special cuts.
"We have to make it very easy to make a non-through cut," said Scott Box, vice president of Steel City Tool Works. This new company designed the guard on their saws to be more accessible from the beginning. "All you have to do is loosen a wing nut on the back, and you can flip the guard up and out of the way. When you put it back in, it registers in the same position again and it's very rigid. That's the kind of thing we have to do as manufacturers, and make it user-friendly to the point that it doesn't become a pain to take off and get back on. You can readily go back to using that guard again as you change your setups."
For Bosch, Feldner noted that the guard on the company's new model 4100 job-site table saw addresses both vision difficulties and ease-of-use.
"Our whole goal in this design is to eliminate the two issues and give people a reason to actually want to keep it on," he said. "The blade guard is a split-guard design, using a top fork and two side barrier guards that prevent you from touching the blade. The fork design means that there are two prongs, so there's nothing that blocks your line of sight of where the wood touches the blade. The barrier guards can be locked in the upward position if you need to make adjustments on the blade, so you don't have to take the guard off to make accurate adjustments."
The main purpose of guarding is to keep hands from coming into contact with blades, but that covers only one of the table saw's two main dangers. While the guard itself may help to deflect a sudden kickback — the other main danger — their design doesn't prevent kickback from happening. For that, you need to keep the wood on the waste side of the cut from coming into contact with the blade.
Splitters, common on table saws for decades, help prevent kickback. However, because splitters attach rigidly in place to the saw their height is constant, usually several inches above the table. For that reason they can't be used for non-through cuts like dados and rabbets, and must be removed. European saws, however, have had a workable solution for that for a long time.
Riving knives, like splitters, mount behind the blade and prevent offcuts from drifting into the back of the blade. However, riving knives don't extend above the blade. In fact, they raise and fall with blade changes, always remaining just below the crest of the blade and making non-through cuts possible. U.S. manufacturers are now recognizing their value.
"We're incorporating riving knives with detachable blade guards into all of our newer saws," said Grizzly Industrial's Bill Crofutt. In addition, Grizzly's system gives the user more than one option on the knife. "Depending on the saw, some of the guards are attached directly to the riving knife. On others, the guard can be removed from the splitter, and leave that in place; and then the splitter can be removed and a riving knife dropped in. So, there are a couple different ways we're approaching it."
Machine mandates
If riving knives are such a good idea — and if European use is any indication, they are — why are they only now coming to U.S. manufacturers' offerings?
"The only reason riving knives are here is because of SawStop," said Steve Gass, president of SawStop. "Manufacturers did that in response to the pressure that SawStop was putting on them — and by that I don't mean us directly calling and bugging them, but the existence of that technology pressured them to do something to address safety. In large part the developments that have happened over the last couple of years with table saw safety and the riving knife standard were quite literally a direct result of the development of the SawStop technology."
Box agreed, noting that groups such as the Power Tool Institute, a consortium of tool manufacturers, were instrumental in getting the ball rolling.
"These guys got together to counter SawStop, and that was one of their solutions, to petition UL to come up with a different set of standards that they could achieve at a cost-effective manner and still promote safety," said Box.
Back in 2003 Gass' company filed a petition with the Consumer Product Safety Council, encouraging the production of safer equipment, with an eye toward the SawStop device technology. Manufacturers, reluctant to incorporate the device into their saws, pressured organizations such as Underwriter's Laboratory to revise standards to mandate safety measures they felt more achievable. The result was UL 987, a set of standards that includes a mandate for riving knives. As of Jan. 1, 2008, to garner UL approval all new table saws must include a riving knife. After a period of years, older equipment not equipped with the knives must be converted to receive approval, or phased out of production. In a few years it will be difficult to buy a saw that doesn't have a riving knife.
To clarify, UL sets standards for table saws (and a host of other industrial and consumer products) that are not legal requirements in the sense that a company can't sell a saw without them, but they do constitute a practical requirement. Few customers will buy equipment without the UL seal.
Mandates, although formed with the best of intentions, aren't always easy to implement. And, in some cases, may even be counter-productive.
"The danger there is that something may be mandated that's not possible or practical for everyday use, very difficult for the manufacturer to implement or even unproven designs that do not have long-term testing, thereby not improving the situation," said Grizzly's Crofutt. "And there could be mandates that would raise the price of the machines to the point of forcing people to keep their old one."
Further, Crofutt said that many mandates can sometimes be hard to comprehend. Wading through the thick stack of pages that make up UL 987, for example, one can quickly get lost.
"If you read the UL recommendation it's very confusing," he said. "As a matter of fact the CPSC letter to UL states that they don't even understand what UL is trying to say. From a manufacturer's standpoint, we want to comply, but if the mandates are confusing it makes it very difficult."
"I don't think anyone in the industry is going to argue with any legislative body against more or better safety features — safe equipment is in everyone's interest," added Norman Frampton of General International. "Research and development costs are a concern of course and no one wants to be forced to make changes that price them out of the market. But as long as the rule is the same for everyone and the playing field is level, in the long run everyone benefits. Being able to design affordable and retrofit-able versions of new safety features to fit previously built equipment is also a major concern and can be a challenge. We'd also like to see government-mandated training be more emphasized as well. Again, if the user doesn't understand how or why a safety features works and what it is protecting him/her from, then even safety features won't protect those who don't use them properly."
Other paths to safety
And then there's SawStop. By now, every woodworker has heard of the device that can detect when a blade comes into contact with human skin and instantly shut the machine down. While injury can still occur, it has been shown that the injury will usually be far less than without the device.
When the device was introduced at IWF in 2000 it was greeted with amazement, and easily won a Challenger Award for innovation at the show. It has since won numerous additional awards. At the time of its introduction, more than a few people predicted that it would be readily embraced by the industry.
It wasn't.
"We were all shocked at SawStop, because it seemed so obvious that this was the right answer," said Gass. "If you're a woodworker, and you know other woodworkers, you know somebody who's had an accident. The consequence of those accidents can be so devastating. If you had something that could prevent that and it was cost-
effective, why would you not do it? It seems like such an obvious answer, that of course you'd incorporate it. I wasn't thinking that they'd incorporate it because they had to, as much as because customers would want it. Users of table saws generally like their fingers, and like to keep them attached to the rest of their body. I thought customers would demand it from the manufacturers."
When no other manufacturer adopted the device for their lines, SawStop introduced its own cabinet saw with the device included. Sales have been brisk. Gass said that about half the sales have gone to industrial customers, with the other half split evenly between private individuals and schools. The safety issues of the SawStop device aside, the performance of the SawStop machine has garnered several good reviews from woodworking publications in its own right as a quality woodworking tool.
And, while no manufacturer has yet stepped forward to incorporate it into their machines, some admit that the technology is here to stay.
"I think it's going to be a long road of development to improve on what Mr. Gass has done," said Steel City's Scott Box. "I think that down the road that technology is probably going to become less expensive. I know of other ideas that are out there now that are being explored by other companies, and I think you're going to see some move toward that in the foreseeable future."
"There's no arguing that it has prevented some serious accidents but it is a mechanical device; and over time it has been proven that anything mechanical has the eventual potential to possibly fail. Then what happens?" Frampton asked. "Perhaps the real question is whether or not we want students and inexperienced users learning or working with a false sense of comfort or the presumption that they cannot be injured, rather than keeping that healthy respect for the equipment front and center in their minds. It takes time to develop good habits but it usually takes even longer to unlearn bad habits. In the meantime, what happens when the user goes to work on a different saw with that same 'I can't be injured' mentality? Again, we believe there's no one simple, easy solution. Good safety features in combination with good work habits formed from proper training will reduce personal injuries the most."
Of course, there are other types of safety features, some of which have been popping up on table saws for a few years now.
A left-tilt design is generally considered to be a safer arrangement than a right-tilt. Most new saws offer left-tilt, while some manufacturers have introduced left-tilt versions of venerable right-tilt machines.
Dust, while it doesn't pose the same type of danger as blades and kickback, is also getting more attention. Shroud-type dust collection is improving dust control on contractor and hybrid saws, and collection shrouds on blade guards is becoming more prevalent.
And even when blades aren't turning, the sharp teeth can injure. For that reason blade arbor locks are being incorporated to make blade changing safer and easier.
Your current saw might not have these features, but it's a good bet that your next one will.
So, what's new?
Whether prompted by UL 987, by other forces in the industry, or by their own initiative, a number of new machines are being rolled out with a variety of improved safety features. Here's a small sampling:
Bosch's 4100 job-site saw has the distinction of being the first portable with a riving knife system. Its forked guard design offers an unobstructed view of the blade. The left-tilt machine has an arbor lock.
SawStop is finally ready to deliver its long-promised contractor's saw in the first quarter of the year. In addition to the SawStop device the machine will be a left-tilt unit featuring a riving knife and a shroud-based dust collection system.
Grizzly's new left-tilt 12" G06051 has a riving knife and magnetic switch. The company's G0623X sliding table saw features adjustable riving knife, magnetic switch and dust collection on both cabinet and guard.
General International's 50-460R and 50-450R 12" table saws come in left- and right-tilt versions, respectively. Both have arbor lock, riving knife, magnetic switch and dust collection ports on the cabinet and blade guard.
Delta offers a left-tilt version of its popular 10" Unisaw and has recently introduced a left-tilt contractor's saw, available with a 30" Biesemeyer fence.
Steel City Tool Works has introduced an industry first granite-top machine in their model 35915G. The left-tilter has magnet switch and riving knife.
Powermatic's left-tilt 14" PM3000 has many of the same features as the earlier 10" PM2000 machine, including push-button arbor lock, magnetic switch and riving knife.
Jet just recently introduced a left-tilting version of the company's long-available Xacta JTAS-12XL50 with magnetic switch.
The new Shop Fox W1761 from Woodstock International is a left-tilt 12" machine with riving knife and magnetic switch.
And new offerings from the European companies like Martin, Felder, Altendorf, Laguna Tools and others all include riving knives — but that's no surprise. With the shift in manufacturers' thinking in this country, it's clear they had the right idea all along.
The final responsibility
All of these safety developments are good news for the industry, and good news for woodworkers at large. Still, they mean nothing if the safety features aren't used, and mean even less if safe practices are not in force whenever the power switch of a table saw is turned on.
Manufacturers are moving in the right direction, but it's still up to the user to show personal responsibility for safety.
"Always use your guard," said Bosch's Feldner. "Use proper body position; you don't want to be standing right behind the blade, you want to stand to one side. Use push sticks. Make sure you're using a good fence and that it's locked in position."
"Most of the accidents I'm aware of or that we hear about are ones that were almost always preventable," said Crofutt. "Slowing down, taking a good look at the intended operation and asking yourself, 'Is this a good idea?' would, I believe, prevent most accidents."
"It's a pain in the keister to have a guard on there for some cuts, but in the long run it's going to be the best medicine to prevent accidents," said Box. "You just have to work smart."
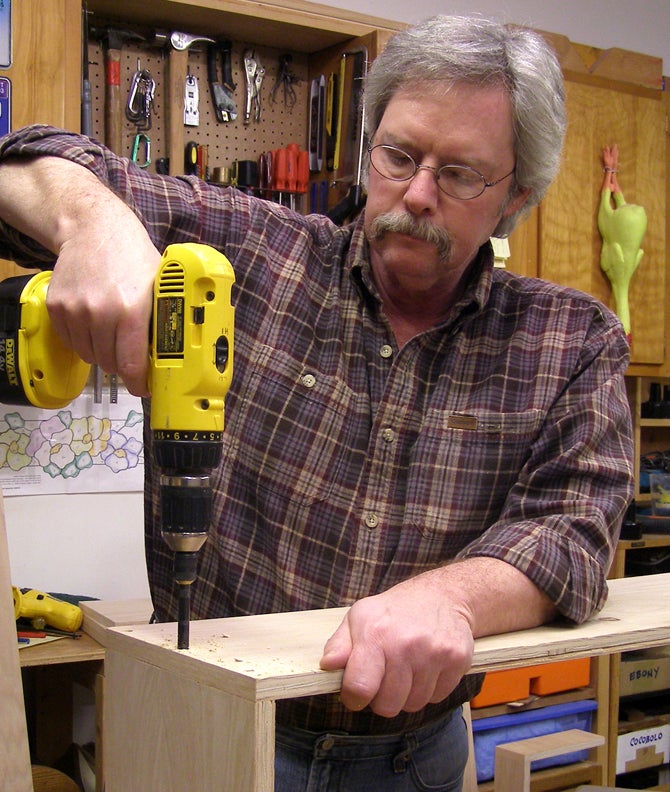
A.J. Hamler is the former editor of Woodshop News and Woodcraft Magazine. He's currently a freelance woodworking writer/editor, which is another way of stating self-employed. When he's not writing or in the shop, he enjoys science fiction, gourmet cooking and Civil War reenacting, but not at the same time.