Can it pay to mill your own lumber?
They trickle through the mail every few months: glossy brochures for portable saw mills that leave a woodworker wondering. Ironically, the appeal of harvesting one’s own lumber has little to do with economics.
They trickle through the mail every few months: glossy brochures for portable saw mills that leave a woodworker wondering. Ironically, the appeal of harvesting one’s own lumber has little to do with economics.
Access to new species and cuts (quartersawn, rift) is probably No. 1 on most woodworkers’ lists. And then there’s the Yankee in all of us that hates to watch a healthy log go to a landfill. There can be symmetry to saving urban lumber: a piece of furniture made for a grandchild could well incorporate the branch that held his father’s tire swing. And there are always environmental issues.
But the bottom line is raw greed: we all just want to own some 12/4 walnut or elm or perhaps a giant slab of diagonally sawn cedar. Or maybe even just a few blanks for turning bowls.
One doesn’t need to own a sawmill to save a tree (although it’s definitely an enticing option). That part of the process can be hired. But one does need to know enough to decide which trees are worth harvesting and to be able to tell the sawyer how to mill each log.
Some rough-sawn arithmetic
Let’s imagine that a crew has just removed several trees for a new parking lot at the new high school in town. It’s obviously too late to be involved in the felling, but the job supervisor says you’re welcome to the logs if you clean up the rest of the debris. Is it worth it?
The primary consideration is species. In general, the financial return on softwoods is a lot less than hardwoods. But there are exceptions. For example, some coastal cedars and new-growth redwood can bring more per board foot than even the clearest slow-growing northern red oak from Minnesota. Geography plays a role.
Coming up with an average price for harvested lumber is almost impossible because there are so many variables. The quality of the log, the species and the dimensions all play a part, as does how it is sawn and dried. Retail prices on most of the familiar domestic species (red oak, maple, poplar) vary widely depending on grade, cut and dimensions, but they average somewhere in the range of $3 a board foot. A log measuring 30” in diameter by a little more than 8’ in length can yield about 400 board feet after milling. Given the rough average above, it could be worth perhaps $1,200 after milling and drying. Double that for furniture-grade cherry and triple it for clear walnut.
If a professional sawyer with a mobile band mill and skid steer is hired to come on site, he/she will charge between $50 and $80 an hour to reduce the log to usable rough-sawn boards. Some smaller operators will do the job for a percentage of the lumber. Assuming that no blades need to be replaced because of hidden metal that has grown into the tree — and that the log is sound — the other costs involved are hauling the wood to a drying shed, sealing the ends of the boards, stickering (the small spacers that allow air to circulate across all six surfaces of a board) and then buying dinner for your brother-in-law, who provided the flatbed trailer. You know he’s going to order the sirloin.
Again using wild numbers, let’s say the total cost is in the neighborhood of $500 (don’t forget the cleanup that you agreed to earlier). That’s still less than half the retail value of the lumber. If there is more than one log, costs can go down per board foot because the mill is already on site, the flatbed will hold more than 400 bf and the brother-in-law still only gets one steak.
Milling one’s own lumber really starts to pay dividends when the species is unusual for the locale (for example, a healthy American chestnut in Manhattan) or the cut is something other than plain sawn (a white oak log that can be cut to deliver mostly quartersawn boards). And if you find a black walnut with 8’ or more of straight trunk devoid of branches, call a veneer mill before you buy gas for the chainsaw. It might just be worth half the cost of a new car (stick shift, manual windows and no AC — but still).
What to watch for
The biggest downside to harvesting urban hardwoods (trees that grew on city lots or even in the yard or the fence line of a remote farm) is metal. People have a habit of attaching things to trees — everything from yard-sale signs to hammocks, clotheslines, even steps for a tree house. Trees grow by adding new layers every year, so all that metal can be hidden well below the bark and can even be buried several inches inside the trunk. If he hits a chunk of metal with a band mill blade, the sawyer will ask you to pay for a new blade.
Professional metal detectors are available (the beachcomber variety just doesn’t have enough range). For example, the Probe 2100 model from MDI in Eugene, Ore., will detect an 8d nail buried 15” into any type of log. It runs around $1,200, but blades cost up to $170 and more apiece depending on the model, length, teeth and tips. You will also enjoy the privilege of paying for the sawyer’s downtime while he changes blades. Renting a detector is a cost-effective alternative, and many sawyers already own one that they will bring to the site.
For smaller logs, there is a much more affordable option than a trailer-mounted, hired band mill. For anyone familiar with chain saws, the Alaskan model G776-36 mill (above) from Northern Tool and Equipment in Burnsville, Minn., runs about $220. This is a 36” heavy-duty, portable mill that hooks onto a chain saw to convert rough logs into slabs from 1/2” to 12” thick.
Before calling the sawyer, try to establish what the core of the tree looks like. If it’s hollow, you’re going to mill some very expensive firewood. If the tree is standing dead, it might have been struck by lightning and it could have cracks running the length of the trunk. If it was lying on the ground, rot is an issue.
Live trees have very high moisture levels and this can double the weight of the lumber. That’s an issue when using utility trailers rather than a flatbed truck to transport the rough-sawn boards, as axle weight might decree that the lumber is moved in several loads. Gas or diesel costs then become part of the equation.
Drying is also a consideration. Boards need to be stacked in such a way that the air can circulate around all six surfaces. The ends need to be sealed, they must be protected from snow and rain and they should be kept out of direct sunlight to facilitate even drying. If possible the stickering (slats) that are used between boards in a stack should be of the same species as the boards themselves to avoid sticker lines. These are reactionary marks that develop over time when the chemicals in the sticker species change the color of the boards where they touch. Usually they are darker lines running across the board and, while most can be removed during planning, some run quite deep.
The bottom line on choosing whether or not to harvest a tree is often not the bottom line. That is, the decision isn’t always as simple as running the numbers. Sometimes the tree has subjective value. Perhaps it stirs personal memories or it’s a species that one doesn’t come across too often. Or maybe it’s so huge that it presents the possibility of making that Nakashima-style table you’ve dreamed about. Even if it just belonged to a good customer who would be thrilled to have a piece of furniture made from it, the value of harvesting a tree is rarely measured in dollars alone.
This article originally appeared in the February 2012 issue.
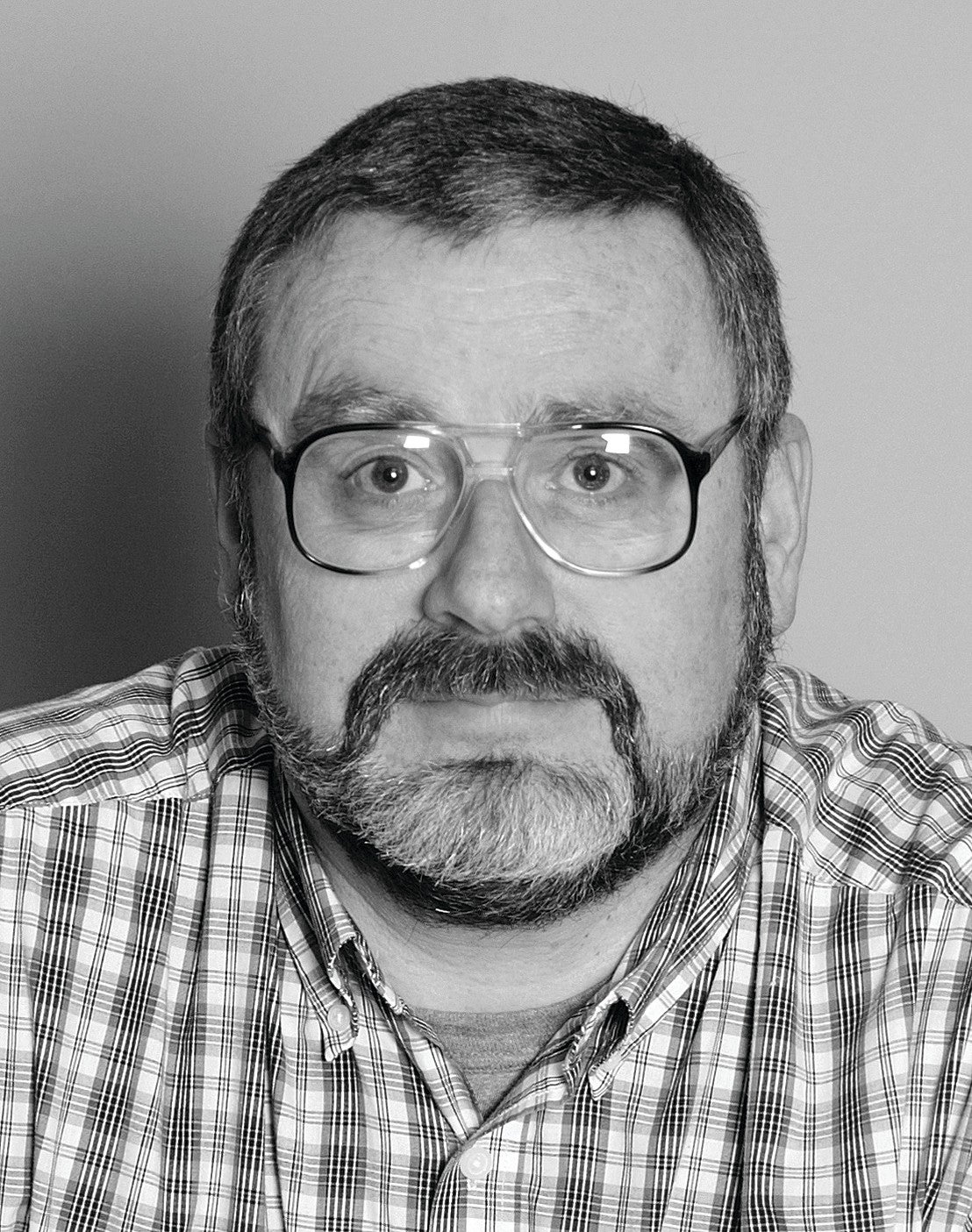