Zsa Zsa Gabor was famous for noting that diamonds are a girl’s best friend, while a man’s best friend is just a dog.
Nowadays, a lot of woodworkers covet diamonds too, because they don’t dull easily and that reduces downtime. According to the German tooling manufacturer Leitz (leitztooling.com), “Diamond tools typically outrun carbide tools by more than 20 times and dramatically cut tooling and processing costs.” The company has North American headquarters in Grand Rapids, Mich. and its catalog includes a number of Diamaster brand cutting tools that use synthetic polycrystalline diamonds (PCDs) and nano diamonds (powder that is smaller than 1 micrometer) in its tool coatings, to deliver that high level of endurance. These bits can also feature complex engineering which offers options such as a positive twist for optimum chip removal, or a negative twist to support the clamping of small workpieces. Some are designed with both right- and left-hand rotation, without the need for a tool change, which delivers tear-free machining of coated workpieces. This combination of intelligent engineering and PCD is changing the way many manufacturers create CNC tooling.
Another global industry leader, GDP/GUHDO (guhdo.com) notes that polycrystalline diamond is now available in multiple quality grades, just like tungsten carbide. Most machine applications are supplied with standard quality grades with varying grain size, while more demanding applications may be supplied with either coarser grain or a ‘polished’ tip. Polished PCD helps prevent material buildup on the cutting face, which improves tool performance due to less heat generating in the cut. For woodworkers who are wondering whether diamonds are the answer to their prayers, Guhdo has an excellent article on its website blog titled, “Diamond v. Carbide: Weighing the Costs and Benefits”.
The bottom line seems to be that a shop that is milling the same material all day long will benefit, but if the CNC is switching from, say, melamine to hardwoods to MDF, even with the same profile, there may be a better solution using multiple carbide bits. It’s definitely worth talking over specific applications and addressing job specs such as feed rate, rotation (RPM), material, profile shape and so on with a qualified salesperson before making the switch from carbide to diamond. They do behave differently. For example, in hand tool sharpening, diamonds don’t always deliver the fine edge that a water stone can. In CNC tooling, that relative coarseness may not be an issue because of tool design, cut speed and material tolerances (MDF isn’t as picky as, say, hand-planed fir), but sharpening certainly is an issue worth exploring. Both the quality of the tool and the coating are subjective. Again, according to Guhdo, “you might be in for a surprise to find you were sold a ‘disposable’ tool that cannot be sharpened at all or can only be sharpened once. Or, you might think you are getting a bargain when you buy the tool, only to find you are going to be expected to pay 50 percent of the new tool cost to get it sharpened.”
So, buying from a reputable manufacturer is key. For example, LMT Onsrud LP (onsrud.com) in Waukegan, Ill. has been providing premium cutting tools for more than 70 years. The company offers a full range of CNC tooling, which include solid carbide and PCD coated up and down flutes, compression bits, chip-breakers, boring tools, roughers, slotting tools, trimmers and engraving tools.
And Freud Tools Inc. in High Point, N.C. has a special section on its website (freudtools.com) for CNC tooling. Currently the company offers 248 straight and spiral options, 74 edge treatment bits, 14 architectural millwork profiles, 36 joinery solutions and some 20 sets of tools.
We have options
As with diamonds, tungsten carbide isn’t a one-size-fits-all solution. According to Amana Tool Corp. (amanatool.com) in Farmingdale, N.Y., “there is no single grade of carbide that is suitable for every situation. For example, saw blades for ripping wood use softer grades such as C-1 or C-2. If C-4 grade were used, it would be too brittle for these materials.” The company also notes that CNC cutting tools can become overheated and dull from a number of causes that can often be ameliorated by woodworkers themselves. These might include improper and infrequent sharpening, incorrect feed-rates and RPM, excessive removal of material, inappropriate cutting tool selection for the type of material and machine, and inadequate horsepower. Amana offers a comprehensive catalog of both diamond (PCD) and carbide tooling that was designed specifically for CNCs.
Sometimes it’s hard to find a specific profile, more so in furniture than casework production. It helps to have a supplier who works with a broad spectrum of the industry, and if there isn’t a manufactured bit available, they can usually have one made. Like many other comprehensive suppliers, Connecticut Saw & Tool (ctsaw.com) in Stratford, Conn. can provide both design and production of custom-tailored carbide and PCD tooling. To get started, a woodshop just needs to email a drawing, fax a sketch or ship a wood sample to the company to start the conversation.
Another custom manufacturer, Charles G.G. Schmidt & Co. (cggschmidt.net) in Montvale, N.J. offers a wide choice of materials used in tips for custom cutting tools. These include diamonds and tungsten carbide, but also S-alloy which is recommended for solid wood and provides less resistance, plus it can be sharpened to a finer edge than carbide. It’s especially effective on cross-grain cuts. And Schmidt also offers high speed steel (HSS) that is hardened to Rockwell C60-62, and T1 grade HSS that is rich in tungsten and meets the needs of both long runs and grinding ease. T1 is only available in corrugated back knives, thin knives and Terminus knives.
One reason carbide’s edge wears down is that dust removal isn’t always efficient, so the bit has to cut the same material more than once. FS Tool Corp. (fstoolcorp.com) is headquartered in Markham, Ontario and has a U.S. presence in Lewiston, N.Y. The manufacturer will be demonstrating its tried and true Aerotech dust-free nesting technology at the Ligna woodworking show in Hanover, Germany this May. FS Tool notes that it invented this technology and says its system will remove 98.4 percent of CNC dust. And IMS USA (imsusanc.com) in Wilmington, N.C. is now carrying both the ER32 and ER40 models of the Twister, another smartly engineered device for removing chips and residual dust. Another dust management option worth a look comes from Peak Toolworks (peaktoolworks.com) in Jasper, Ind., which offers the Sand-Free series of tools that are designed to reduce manual sanding by as much as 70 percent.
H3D Tool Corp. (h3dtool.com) in Newcomerstown, Ohio offers a wide array of diamond, carbide and insert tooling. Among its newer offerings is Extreme Shear, which the company bills as “the most advanced tooling possible for chip and sand free cutting in solid wood and manmade materials for profiling, jointing, and chamfering.”
Hold on…
For shops looking to upgrade tool handling, Benz Inc. (benztooling.com) in Grand Rapids, Mich. has developed the Hybrix. This is a rotating tool carrier system with a fixed housing, and its main components are one or more stationary motor spindles with an automatic tool exchange system. It combines the characteristics of both a magazine and a turret.
Another tool holding solution comes from T-Tool (t-toolusa.com) in Weston, Fla.. The company now offers Lamello compact holders where cutters can be clamped safely, and with high precision. With this solution, there’s no need to switch between collet or hydro chucks.
New from Leuco (leuco.com) is the Smartjointer, which is a cutterhead where tooling can be exchanged quickly and easily, and thanks to three-point support, there’s no subsequent balancing required. The cutting edges and the gullets are replaced together.
ComSurge Tooling (comsurge.com) in Poway, Calif. offers a range of carbide inserts that includes two- and four-sided knives plus radius, face and back groove inserts, all in a variety of sizes. The company’s services include onsite quality control and monitoring order progress. The catalog is restricted to industrial-quality tool manufacturers (no DIY or contractor-quality tools), and the engineering department also caters to shops that need custom-made or rare tools.
CMT Tools (cmtorangetools.com) makes an adjustable chamfering CNC cutter, (item No. 663.201.11) that has two reversible, replaceable, carbide knives that are held in swiveling blade carriers. They cut along three edges (the periphery and both sides), and they can be set from zero to 45 degrees upwards, or all the way to 90 degrees downwards. The settings are infinitely variable with positive stops every 7.5 degrees. The bit will cut chamfers, rabbets and other joints.
Freeborn Tool Co. (freeborntool.com) in Spokane, Wash. offers brazed shaper cutters, insert cutters, spiral surfacing cutters, router bits, custom tooling, and options for CNC tooling that are all made in the USA. The company has just launched a new website that makes finding the right tooling a lot easier, and its entire stock catalog is now online.
Eagle America (eagleamerica.com) in Huntingdon Valley, Pa. offers a number of CNC tooling solutions, especially for small shop machines. Among them is a set of the company’s most popular eight router bits in either 1/4” (item No. 106-1010) or 1/2” shank (106-1015).
And speaking of small shops, calculating tool feed rates can be a challenge for someone new to CNC routers (or even for an old hand who is using new cutters or new material). The Cutter Shop (cutter-shop.com) has a free calculator on its website that gives pretty good guidelines here. And if you are new to CNC tooling, you might want to stop by the All3DP website (all3dp.com) and check out an article by Brian Obudho titled, “Simple Guide to CNC Router Bits”. It’s an excellent primer on the basic essentials such as up, down and compression spirals, selecting flutes and lengths, and working out speed and feed rates.
Woodworkers looking for a tool to cut thin materials on a CNC might want to visit the Donek Drag Knife site (donektools.com). This is a tool that fits into a CNC router or spindle collet and uses a special utility knife blade.
Finally, for shops using desktop or small CNCs, setting up bits is now a little easier with the Router Bit Vise from Infinity Tools in Oldsmar, Fla. (infinitytools.com, item RBV-001). It holds bits securely when removing or installing cutters, or when cleaning carbide with a wire brush. It has three unidirectional needle bearings that hold and lock a 1/2”, 8mm or 1/4” shank router bit securely in place, and rare earth magnets to attach the device to any steel surface on the CNC for safe storage.
We began with a quote, so let’s end on that note. William Makepeace Thackeray once said that “there are many sham diamonds in this life which pass for real, and vice versa.” Perhaps he’s telling us that shops upgrading to PCD might want to work with a reputable supplier who sells a proven brand.
This article originally appeared in the March 2020 issue.
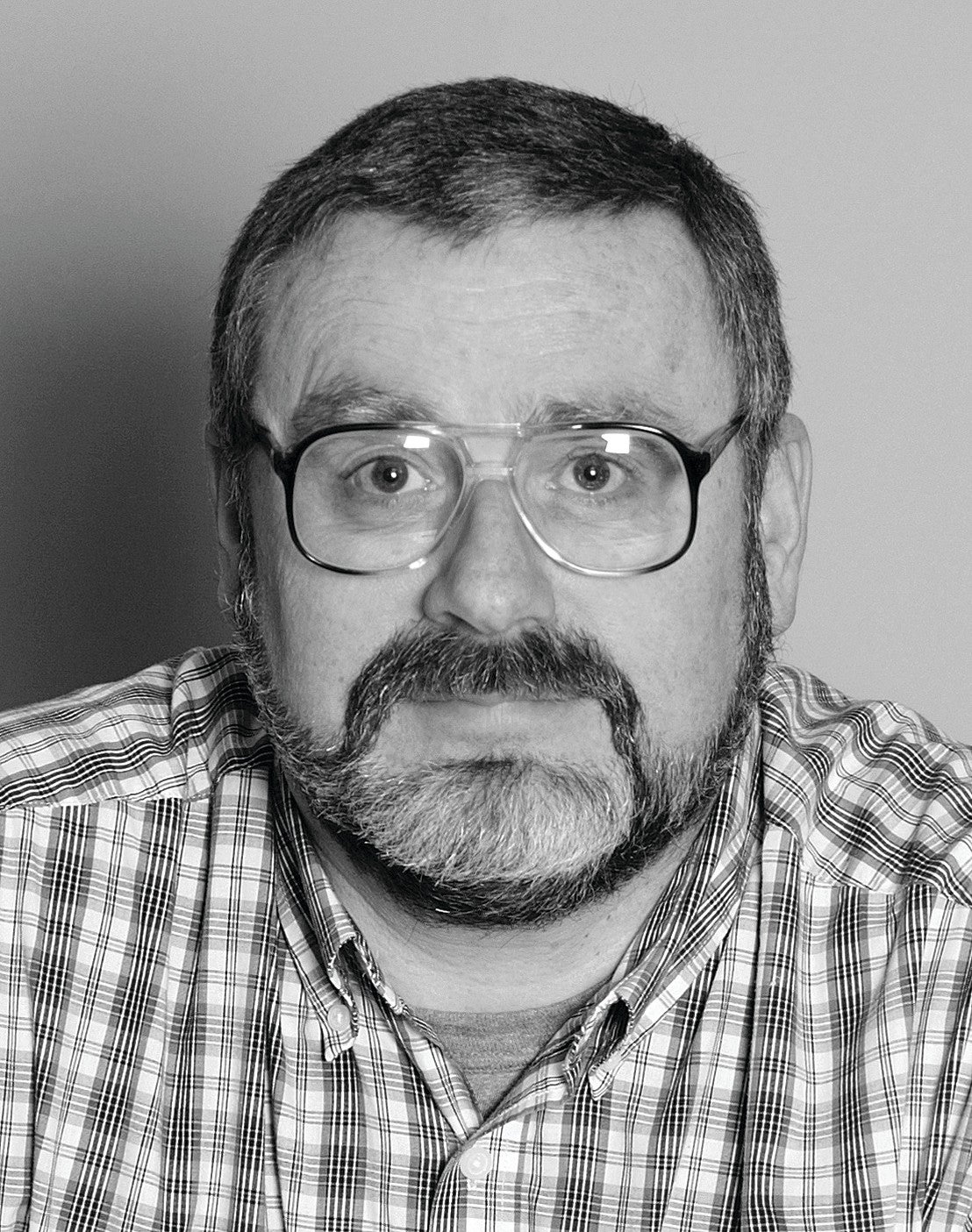