CNC upgrades and add-ons
A CNC router can be a big investment, so one of the prime concerns for buyers must be to avoid premature obsolescence.
A CNC router can be a big investment, so one of the prime concerns for buyers must be to avoid premature obsolescence. There’s not much point in purchasing a machine that can’t keep pace with the shop’s growth, and to do that it needs to be able to take advantage of both existing and future upgrades.
Fortunately, most CNCs from small desktop models to full 5-axis machines can be updated, and a phone call to the machine supplier will usually result in a salesperson pointing out way too many options. Among those might be fixturing upgrades from screws and clamps to a vacuum table or pods; adding or replacing an automatic tool-changer; acquiring one or more aggregate heads; installing a larger or better spindle; adding safety and dust enclosures; installing the latest software; adding automated loading and/or unloading; upgrading to parts labeling; or even just enhancing dust control with a simple AirPro or similar device.
Some machines can accommodate non-routing heads such as lasers, additive 3D printers or scoring knives. Others let the woodworker add a larger table, or perhaps a taller gantry with more Z room. There may even be an option to add a second spindle to save floorspace.
Whatever the size of the machine, the best place to start upgrading is to give it a thorough cleaning and then replace any wearing or worn parts. After its body gets in good shape, work on its mind. Most larger machines will have automatic software upgrades, but smaller machines are often being run on aging control programs and need a manual update. With those basics taken care of, it’s time to look at upgrades and add-ons.
Retrofits and controllers
Anyone who has ever owned an older vehicle has probably thought about fixing a few rattles and getting another year out of it. If the body and engine are sound, maybe all it needs is shocks and a tune-up.
When it comes to 5-axis units, it can be a little more complicated. Fanuc America (fanicamerica.com) defines a CNC retrofit as “a process that upgrades the control system, the servo and spindle motors, the motor amplifiers, cables, and I/O units including the operator’s panel”. The company says that older, large machines are usually made with ‘good iron’ but may begin to fail due to aging electronics. Because of their large size, it may not be cost effective to replace the entire machine, so a CNC retrofit can be an excellent option. The process costs significantly less than a new machine, especially when taking into consideration the hidden costs such as tooling, fixturing and rigging. Additionally, new machines may require time-consuming training for the operators and maintenance personnel who are very familiar with the existing one.
To get the most out of a CNC retrofit, upgrading the servo and spindle system to a high-speed, digital interface is critical. If the servo and spindle system can’t keep up with the CNC block processing rate, the tool path will not be accurate. And if an older machine is still communicating through an analog interface to the servo and spindle system, this will impact the speed and accuracy of the system.
For shops that own an older and overworked CNC router, MachMotion has a few things to keep in mind when considering a controller upgrade. Some of the benefits of a retrofit over replacement include staying with machines with which the skilled and unskilled operators are familiar, while being able to enjoy all the technology benefits of a new machine. Then there’s the fact that the shop won’t need to rearrange other machines or dust collection to get the old machine out and a new one in. A shop may even have to disassemble both to get through doors or onto loading docks.
Avoiding all that heavy lifting, a mechanical, electrical, or software modification can really simplify future machine upgrades. And the minimal downtime that switching to plug-and-play offers can allow production to ramp up with little interruption. As with Fanuc, MachMotion also notes that upgrading a CNC can cost just a small fraction of the cost of a new machine.
That same theme is echoed by Thermwood, which suggests replacing an obsolete CNC control with a high performance one, and replacing the servo drives with state-of-the-art brushless digital AC servo drives. Additional tooling can be added such as 32mm drill banks, horizontal drills, and new vacuum tables. The company notes that much of the original cost of a CNC router is in the basic mechanics such as the machine base, table, gantry, drive screws, ways, and bearings. These have changed little over the years, and the real value of a CNC router is in the control, the servo drives, the machining heads, and parts holding. To a large extent, these determine what you can produce, how fast you can produce it and what the quality will be. If the basic mechanics of an existing CNC router are in good, serviceable condition and the configuration, table size and axes travels are adequate, then it might be more cost effective to keep the basic mechanics and upgrade the technical components which have become obsolete. If the basic mechanics also need to be rebuilt, then it might be more cost efficient to purchase a new machine.
Spindles are the heart and soul of a CNC, and one of the most updated parts of the machine. Shops can usually retrofit a new spindle that offers more torque, a wider speed range, or enough heft to handle aggregates well. Spindles are also the elements that do the most work, and on smaller machines they usually require manual tool changing. Upgrading to a quick-release spindle and an automatic tool changer can save a lot of time. HSD also offers wireless temperature monitoring on some spindle upgrades.
Needs and wants
Beyond controllers and servos, there are several upgrades and add-ons that are not just designed to keep the machine running, but rather to get more out of it. These can be as basic as adding Bluetooth wireless controls or importing collision-avoiding simulation programs that help avoid situations such as running a new aggregate head into the machine frame.
The most obvious but often overlooked upgrade involves the actual tools. There have been several significant advances in both tool geometry and materials over the past few years, and these run the gamut from combining up and down spirals into a single shaft (there’s a whole new generation of compression bits) to some very complex cutterheads with insert knives.
For example, the new LEUCO t3-System cutter can be used on CNCs for chip-free spiral plunge-cutting, rabbeting and chamfering, and Leitz’s family of WhisperCut jointing heads keeps adding new options. Benz now offers a one-stroke head that it has developed with Leuco for drilling parts for Cabineo connectors, and GDP Industrial Tooling has created oscillating sanding heads for CNCs. And CNC Factory offers the Deluche parts stamp as an alternative to peel and stick labeling.
A host of companies including LestaUSA, Fanuc, Biesse, RobotIQ and Universal Robots are fine-tuning everything from parts sanding to automated loading/unloading by using robotics. Most of these add-ons are cobots (collaborative robots) than can sense the presence of a human worker and avoid contact, and some of them can hook right into the CNC controller.
For medium-sized machines with limited axes, aggregate heads can add functions and abilities that resemble those of a multi-axis machine and do so at a fraction of the cost.
Aggregate heads can change the direction of the router bit or other tooling including drills and sawblades. There’s a downside: they can lose some strength, speed and accuracy when compared to a straight tool, and they usually need to travel at slower speeds. But for shops that occasionally need to reach around a part to do some special machining on a surface other than the top face or vertical sides, they can be the perfect add-on.
Some machines will allow the addition of a fourth (rotary) axis that essentially turns the router into a fully automated wood lathe. This can be a great add-on for shops building stair or deck columns, balusters and posts.
It may be possible to add audio and visual alarms to an automated CNC, where klaxons or flashing lights can alert an employee to a problem that might otherwise only show up on a touchscreen. Not having to stand by the controls means that an operator can multitask, and adequate warning can help avoid problems such as collisions or thermal overloads.
Data monitoring is increasingly becoming available for mainstream CNC models, where operators can make more informed decisions about maintenance issues and automation, or they can deflect declining performance due perhaps to dull or overheated tools that are causing changes in the chip rate. Some monitoring systems incorporate artificial intelligence (AI), so they can learn as they go.
Keep in mind that many upgrades will also require a corresponding increase in electrical power and dust collection, along with time spent training. Even so, upgrading the basics or adding some options can often increase production, and the lower risk of failure and shutdown will usually deliver a little peace of mind.
This article was originally published in the July 2022 issue.
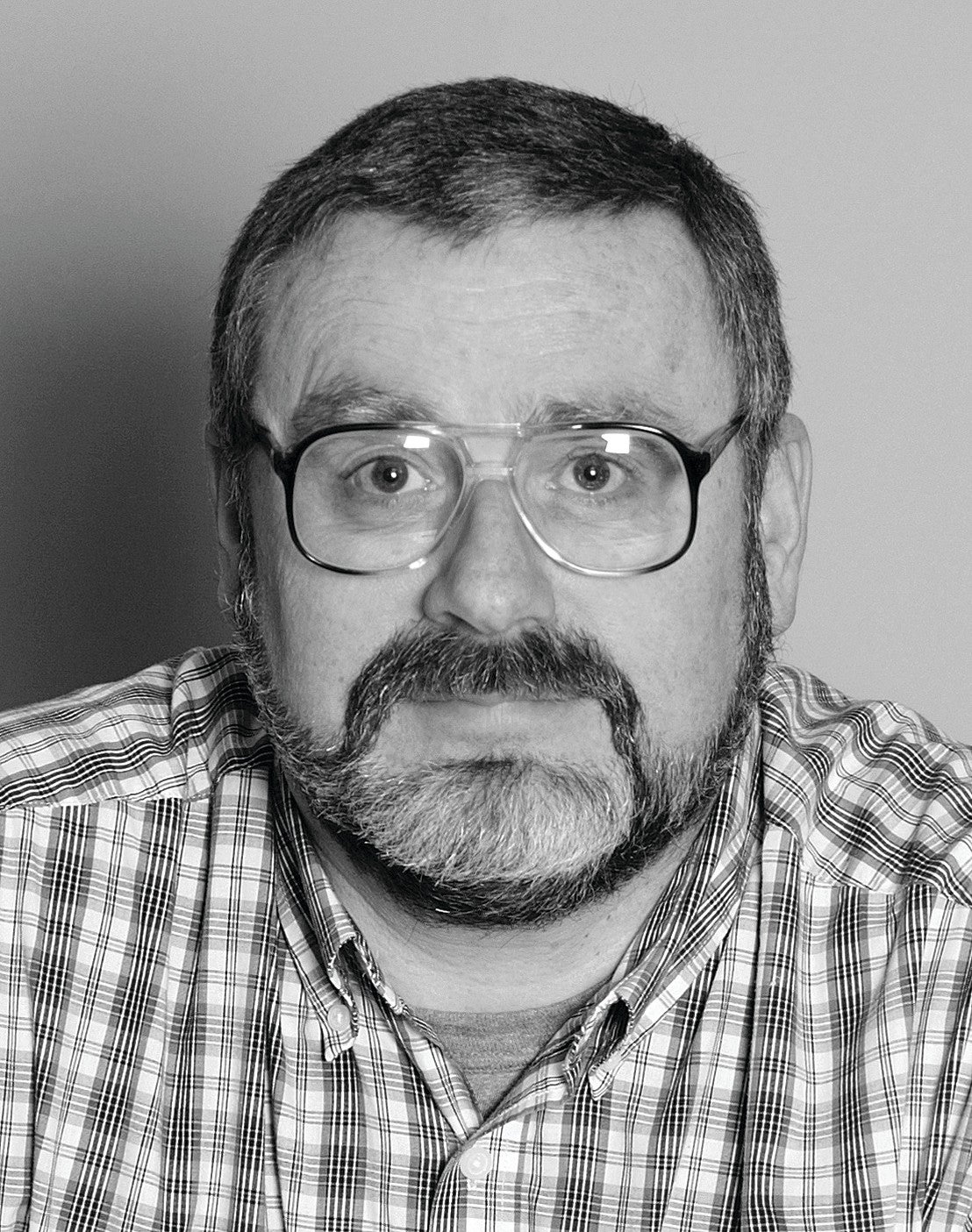