Controlling dust, spray and fumes: September 2022
The biggest environmental challenges to a woodshop are fine dust, spray booth exhaust, and chemical emissions from adhesives, but addressing them will almost always improve profitability.
The three biggest environmental challenges to a woodshop are fine dust, spray booth exhaust, and chemical emissions from adhesives, coatings, and other materials. Historically there has been a bit of reluctance to deal with these kinds of issues, especially in small shops, because they don’t seem to immediately affect the bottom line. That’s a misconception. Beyond the obvious health issues, all three of these contaminants cost money, and addressing them will almost always improve profitability.
Controlling dust
Beyond its impact on lungs and nasal passages, fine dust can play havoc with finishes and cause a lot of reworking. It can also become an explosive threat in high concentrations, and a fire hazard when it accumulates on heat ducts or near pilot flames and other spark sources. Plus, anyone who has ever worked in a shop with a hardwood, laminate or ceramic tile floor knows it can turn a gloss coating into an ice rink.
Catching larger dust particles is easy with a two-stage system, but fines are trickier. The problem is maintaining suspension. Dust collectors move a large volume of air at low pressure, and shop vacuums move small volumes at high pressure. Run a 2” diameter vacuum hose through the middle of a pile of dust on the floor and it will efficiently suck up a thin line of debris about the width of the nozzle, but it will also leave two banks behind, one on either side of its path. Run the same hose a few inches above the pile and it will barely grab anything. A shop vacuum can be very efficient right at the source of dust, but it’s almost useless if there’s any gap between the nozzle and the debris. That’s because there isn’t enough air volume to move the dust into suspension. There’s plenty of speed and pressure, but very little volume.
Now run a 4” hose connected to a 2-hp or bigger dust collector over the same pile, six inches off the floor, and as long as you move it slowly enough it will eventually collect everything. That’s because it’s sucking up about 1,500 cubic feet per minute (cfm) of shop air, so the principle of attrition is at work. The fine dust becomes suspended in the airflow, and if there’s no reduction in the speed or volume of air being moved, it will stay in suspension all the way to the bag. Things that slow down the airflow are long ducts, bends, open blast gates and clogged filters.
In large shops, the baghouse vibrates or uses air pulsing to keep the filter tubes clean, and the volume of air being moved is so large that it overcomes one or even several of those other reducing factors. But in smaller woodshops without central systems, the answer is to locate individual collectors as close as possible to machines, and then keep the filters clean. The key to controlling dust is to collect it at or as close as possible to its source, using a large enough volume of air to keep the particles in suspension. Where a collector hose just can’t keep up (think miter saw), try adding a shop vacuum and earplugs.
The next step is to scrub the shop air for fines using fan-powered filter boxes that are hung from the ceiling, or free-standing units such as Axiom’s Stratus. And here’s an idea that’s going to fall on a lot of deaf ears, but the whole shop should be vacuumed periodically including under machines and on top of HVAC ductwork, door and window casings, and wood or sheet stock storage racks. Blowing dust around with an air hose isn’t cleaning. It’s just dispersing, and it makes the problem worse.
Here are a couple of tricks that may help to control dust in a small shop. First, install a gently curved plastic plumbing elbow on the exhaust port of the shop vac to direct air up toward the ceiling, rather than across the floor where it will blow any settled fines into suspension. Use small magnets to hold the dust collection bag when it’s being replaced. They’ll keep the clean, new bag in position until you can snap the band back in place. Adapt an old funnel to the end of a shop vacuum hose to catch rooster tails on the router table or in grooves being made with a portable router. And always wear a dust mask when sanding. Even a cloth one (as opposed to a full canister version) will eliminate most unseen fines before they can cause nasal or lung issues over time.
Controlling spray
The most efficient way to control excess airborne finish in the spray booth is to spray less product! Anyone who is still using an old-fashioned high-pressure gun with transfer rates in the region of 30 percent is spending a lot of money on coatings that miss the target and land on the floor, or they bounce back and become airborne. Turning down the pressure can help, but a better idea is to switch to a high-volume, low-pressure (HVLP) system with a transfer rate in the 60-80 percent range. The spray pattern needs to be matched to the work, too. You shouldn’t use the same pattern to coat tabletops (wide) and stick moldings (narrow).
HVLP isn’t the only option. Low-volume, low-pressure (LVLP) systems can be used with small compressors, and they may be able to atomize difficult coatings such as higher viscosity or waterborne products better than HVLP guns. They can also create a little more overspray, but it’s marginal.
One issue for small shops in northern climates is makeup air. It doesn’t take long for a spray booth to cool down a small woodshop during the winter as it expels overspray. There are several manufacturers that make sealed, safe, gas or electric air makeup units that provide heated air directly to the booth. They can keep up with the exhaust fan, and some can even help bake the coatings for faster drying. If your spray booth door is hard to open or the booth is drafty, there may be negative air pressure where enough warm air is being exhausted and not replaced that it’s creating a vacuum. Air makeup units are not cheap, but they can last a long time and can help maintain a healthier, cleaner environment in the woodshop.
Portable spray booths have become more popular of late, both for small shops and for onsite touch-ups. Units such as the PJSB from The Paintline are inexpensive, and they can reduce contamination from fine sawdust as well as protecting the shop or jobsite from overspray.
Controlling fumes
Woodworkers tend to open lots of cans. We use everything from thinners and solvents to coatings and fillers, and almost anything in a can has some evaporative carrier or dilute that can become airborne, even in waterborne products. Not all chemicals are harmful, but many can cause nasal allergies, skin issues and pulmonary problems. Latex paints don’t have natural rubber latex in them, so they shouldn’t cause a latex allergy. However, water-based coatings can still have VOCs, even though they are far lower than solvent bases.
In a 2021 study of water-based products, the Los Angeles Society for Coatings Technology studied flat, low-gloss, semi-gloss, and gloss paints, plus wood stains, traffic paints, clear varnishes, sanding sealer, and water-reducible lacquer. Using direct gas chromatography, twenty-three different solvents were found in these 52 coatings in amounts greater than 0.1 percent.
Another potential threat is flammability and the possibility of ignition or explosion. Vapors mixing with air can become very volatile and may have a flashpoint that is based just on temperature rather than needing to be exposed to a naked flame.
So, how does a woodworker control fumes? A good start is to store all cans in a double-walled metal cabinet that has sealed doors. Most of these units are painted yellow, and their function is to slow down disasters. If there’s a fire in the woodshop, a collection of solvents can turn a small burn into an inferno. If they are stored inside the cabinet, that can delay ignition long enough to give people a better chance to evacuate.
Opening cans under a spark-proof hood that exhausts to the outside is a good idea. The hood can be hung on an external wall above a mixing bench in a paint booth. If a hood isn’t an option, try a spark-proof box fan in an open window, or weather permitting just open cans outdoors or at least do so in a well-ventilated area such as a garage with the overhead door open.
Dispose of rags quickly and properly. Everyone knows that oily rags can spontaneously combust, but we tend to forget that they can also emit chemicals and contaminate the air that we breathe.
And if you only do one thing to control the effects of fumes in the woodshop, it should be this: wear an EPA-recommended mask when spraying, mixing, brushing, wiping, or thinning solvent or waterborne coatings.
This article was originally published in the September 2022 issue.
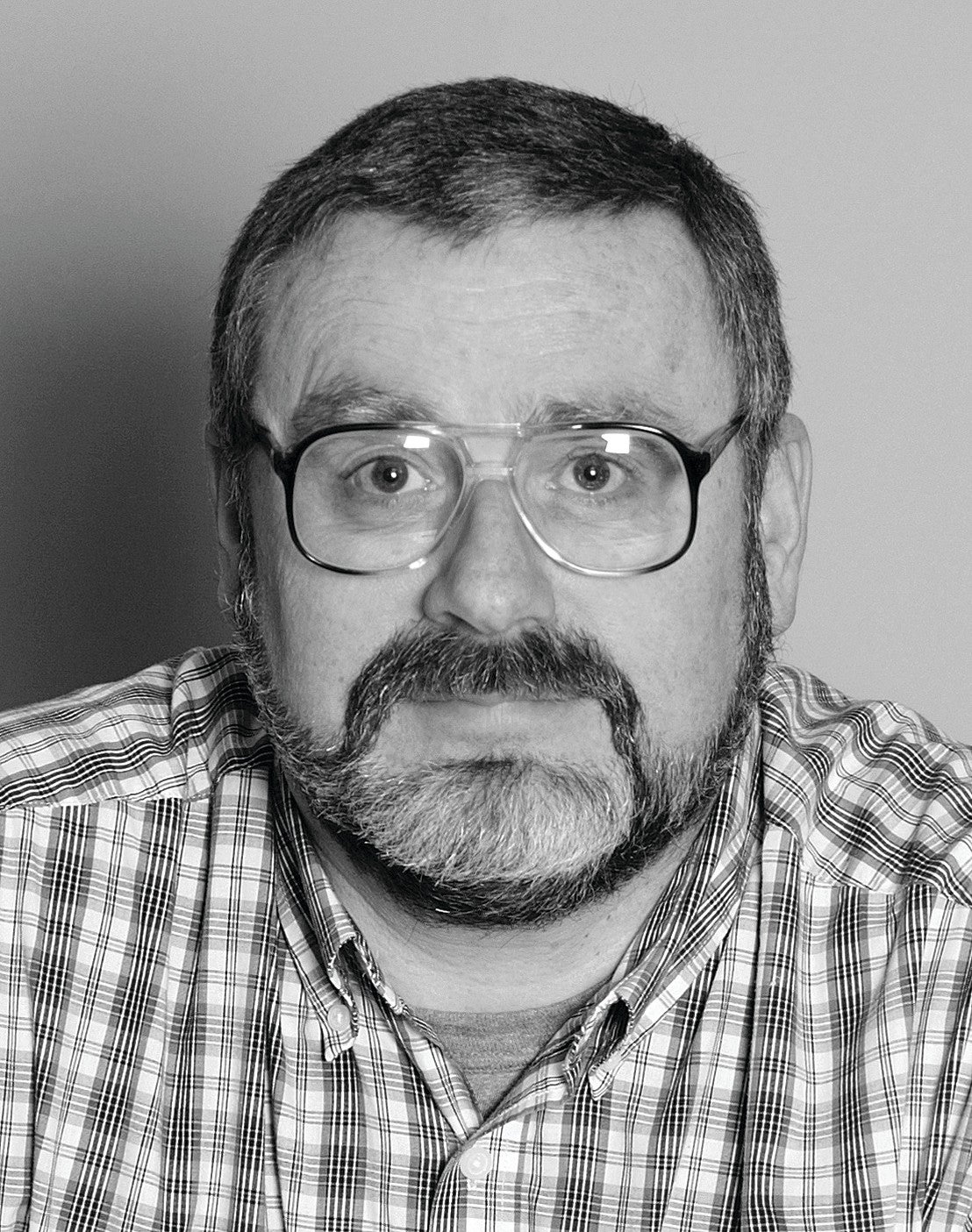