Doing More with Less
The small-shop CNC market is bursting with affordable, user-friendly, multi-purpose options.
Small-shop CNCs used to be all about the budget. For the past decade woodworkers have watched as manufacturers concentrated on affordability and endurance as the watchwords. They were trying to deliver tough, reliable entry-level machines in a very competitive market. Now, those basic qualities are fairly universal and the next generation of machines are beginning to offer something new – a much higher level of versatility. That takes the form of either portability (many new machines are specifically targeted at jobsite use) or adding options such as toolbars, turning abilities and aggregate use to both benchtop and small floor models. Either way, woodworkers are winners as these machines continue to be better engineered, more affordable and more flexible. And it’s not just the hardware. Better software is also changing the game.
Take, for example, the new CNC Shark HD5 from Next Wave Automation (nextwaveautomation.com). The company says that this is its most robust and feature-rich machine to date, but that may not be what sets it apart from the herd. The HD5 comes with Next Wave’s new Virtual Zero Unlimited software package. This adds a high degree of versatility by allowing a woodworker to map the entire surface of the workpiece (a board, a part, or just plywood) by registering an unlimited number of reference points. The program then uses these points to auto-adjust the G-code to conform to the actual surface of the material. This eliminates problems caused by even slightly warped or bowed material, and also allows a user to maintain a constant cutting depth on oddly or intricately shaped projects. That’s something that would usually require the creation of a CAD 3D model.
Next Wave has also introduced Ready2Control control panel software for multiple machine operation and a new website that includes a vastly improved visitor experience, including a Dealer Locator and a wide array of project plans and information.
ShopBot Tools (shopbottools.com) has come up with a new and much more versatile way for woodworkers to get their hands on a CNC than the traditional financing route. The company has introduced a simple and straightforward subscription service that provides shops with the CNC machine itself, plus everything it takes to make it work. A subscription begins with one monthly payment and includes no shipping or cancellation fees. There’s a minimum three-month commitment, and after that a shop can trade up, trade down, or cancel the subscription at any time. The program includes ShopBot’s Handibot, Desktop, Desktop Max and Buddy models.
At AWFS, Legacy Woodworking Machinery (lwmcnc.com) debuted its new Renegade CNC that allows woodshops to create complex joinery, process sheet stock, and create turned parts such as stair spindles, table legs and the like. There’s a tool-changer, an industrial controller, and a few added extras. Those include Legacy’s automated tool measurement system and Delta’s motion control algorithm that delivers faster, smoother cornering. But what really sets the machine apart is the Turning-Indexing system, which adds a whole new dimension to the type of jobs that small- and medium-sized shops can handle efficiently.
AWFS also featured the Yeti Smartbench from Yeti Tool (yetismartbench.com). The SmartBench changes some ground rules by letting woodworkers bring large-scale and very precise machining to the jobsite. Features include a color touchpad and a hand-held control unit that can receive jobs and cutting instructions through Wi-Fi or a USB drive. It can handle full 4’ x 8’ panels, with a cutting height (Z axis) of almost 6”. Plus, longer items can be tiled in the software allowing the shop to machine products that are longer than 8’. It’s dust collection ready, and it can drill, pocket, mortise, carve or dado parts.
More muscle
Laguna Tools (lagunatools.com) recently made some serious upgrades to its workhorse, the SmartShop M. The new M2 comes with an eight-position automatic tool changing system, four to six zone vacuum table. all-steel gantry, direct drive motors with Shimpo gearboxes, and a pod-ready phenolic vacuum table. Laguna has also redesigned its SmartShop II CNC router.
Velox CNC (veloxcncrouters.com) offers seven table sizes at or under 5’ x 5’, and some full-size (4’ x 8’ and 5’ x 10’) models, too. These machines are designed, manufactured, assembled and tested in the U.S.
Axiom Precision (axiomprecision.com) offers four small-shop models. The newest is the entry-level i2R, which comes with 24” x 24”, 24” x 36” and 24” x 48” table configurations and an optional stand. Each model comes with prismatic guides, ball screws, and a DSP pendant controller. Targeted specifically at first-time CNC users, the new i2R lineup is supported by a comprehensive manual and video library, which are both intended to dramatically shorten a new user’s learning curve. The company’s Basic and Pro+ Series upgrade the action with options such as greater Z travel, USB storage, electro spindles and fourth axis capabilities, depending on the model.
Axiom also offers a full line of accessories including bits, dust collection, clamps, toolboxes, stands, laser attachment, software, lighting and fourth axis rotary kits. i2R CNC in Brooklyn, N.Y. (shop.i2rcnc.com) offers the i2R brand and distributes the Axiom line.
Woodshops that are looking for an entry-level machine that’s heftier than a desktop model but is still budget sensitive might want to take a look at the Basic line from Castaly (castaly-cncmachine.com). The smallest table starts at $11,900 and there’s a rotary axis available. Named the Basic-404, it comes with a DSP controller that’s set up to accept standard G-code along with on-board conversational applications. An optional CAD/CAM system can create and edit part programs, and then send them to the machine for cutting.
Thermwood (thermwood.com) offers a system called Cut Ready that requires no CNC programming. That makes it a good option for shops looking at entry-level systems, and the company continues to add versatility to this platform. For example, Thermwood has just released a new component, Combination Cabinets, that adds the ability to create a single structure comprised of multiple cabinets.
Limtech Industries (limtechindustries.com) has an entry-level CNC designed for nested base manufacturing.
More options
Grizzly Industrial (grizzly.com) is introducing the G0894, a small-shop CNC router that boasts a large 23” x 35” cutting area and 3-hp spindle motor. An integrated controller allows a woodworker to store commonly used programs on the hard drive, as well as load programs from a flash drive or connect directly to a PC. The spindle has ER20 collets, so it can handle a range of tooling options.
CAMaster (camaster.com) offers several American-made CNC routers that are designed for smaller woodshops. The company’s Stinger Series (starting at $6,995) come in multiple sizes, ranging from a 2’ x 3’ benchtop model to a full 4’ x 8’ machine. The company offers free lifetime technical phone support and online diagnostics.
The Format-4 c-express 920 Classic, from the Felder Group (felder-group.com), is a CNC drilling and milling center that was specifically designed for smaller shops but with industrial-level endurance built in. It has a pretty small footprint at about 36 sq. ft. Felder offers tailor-made financing solutions, and a wide assortment of machine setups and arrangements for specific tasking.
AXYZ describes its Z Series machine as “an entry-level, low-cost CNC router for first-time users”. The newest addition, the Z5, features steel frame construction and a solid aluminum vacuum/clamping deck.
We started out talking about versatility, and smaller woodshops are not going to find many options that are more versatile than the Shaper Origin. This remarkable tool looks a bit like a standard portable router, but that’s where the similarities end. The operator applies a special tape to the wood and the machine then scans that and makes a map using dots on the tape as reference points. After loading a job, the operator just follows the map on a screen, and the tool makes small adjustments as it travels, so that it delivers perfect results. The motor moves in the X, Y and Z planes within the tool housing to make corrections.
This article originally appeared in the October 2019 issue.
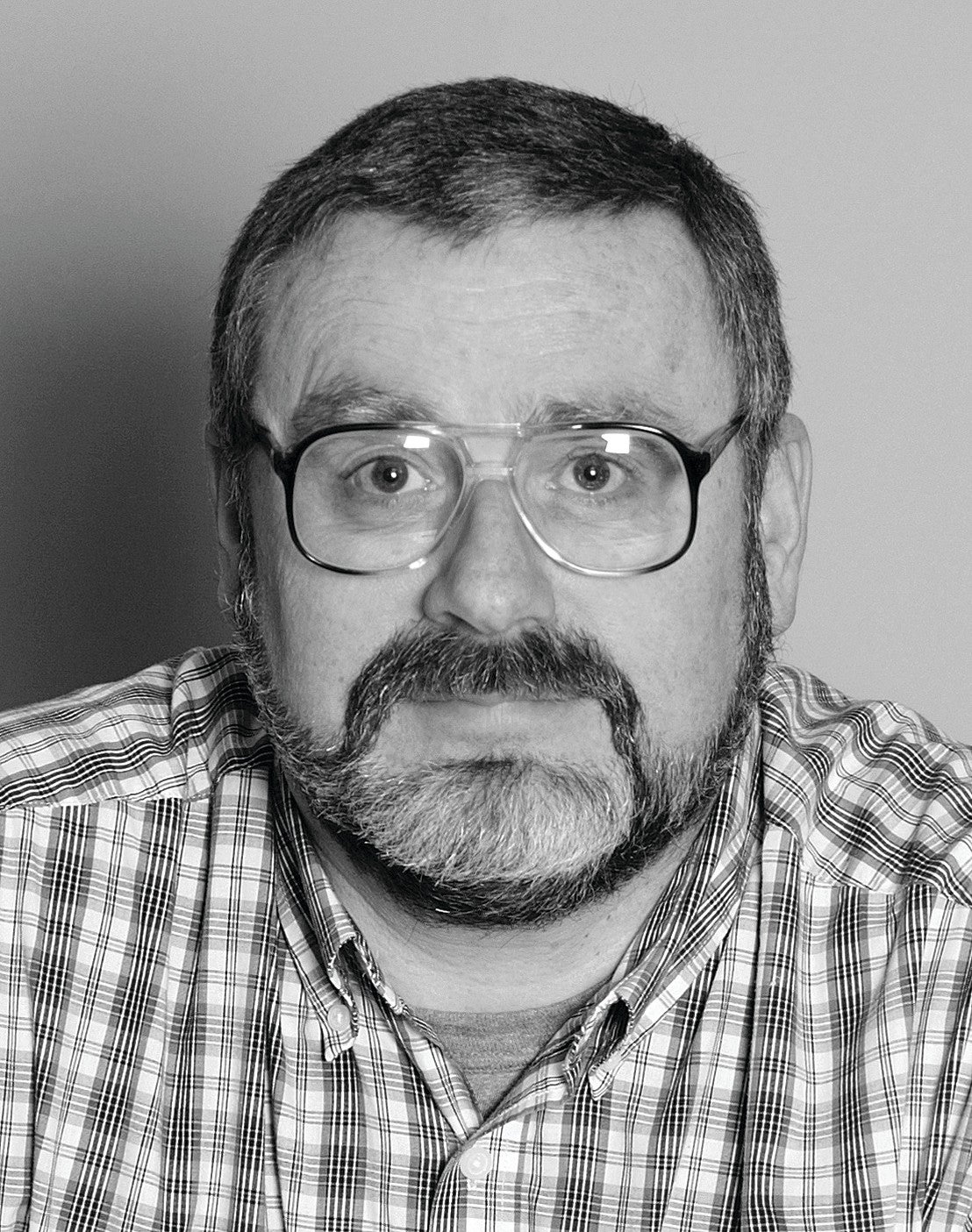