DON’T WASTE THE WASTE
DON’T WASTE THE WASTE: Instead of looking at scrap and sawdust as a nuisance, consider it as a resource that can generate greater profits.
Neither glamorous nor fun, waste management is still an intrinsic step in production. It impacts issues as wide-ranging as safeguarding employee health to meeting environmental goals. But there’s one aspect to controlling waste that always catches the attention of good shop managers – making money. That can involve spending less on raw materials, reducing the cost of cleanup and disposal, and transforming waste into a value-added product that can be repackaged and sold.
Material savings
Virtually every CAD/CAM package on the market includes some type of optimizing program. And for shops that don’t own a CNC and its incumbent software, there are several stand-alone apps available such as Cutlist Optimizer, SketchCut Lite and MaxCut. Plus, there are also free online programs such as Optimalon or Workshop-buddy.com. What all of these programs do is help a woodworker cut parts from sheet stock in the most efficient manner, thus minimizing waste.
Another way to save on material costs is to limit inventory. One of the base tenets of lean manufacturing is a concept called JIT (Just-in-time), which when it’s boiled down to its essence means that a shop should only order materials for the job in hand, rather than holding onto a warehouse of sheet stock, hardware, finishes and other casework ingredients. Woodworkers who take a look at this concept (and there are countless resources online) will immediately come across other aspects of lean manufacturing that deal with the problem of controlling waste. While many of those relate to physical inventory, others show shops how to reduce other kinds of waste such as employee time and effort.
Beyond a rack for partial sheets of MDF and other cut-offs, woodworkers might consider building a few cubbies in some unused corner of the woodshop to store and sort short lengths of lumber. These can be arranged first by species, and then by length. It’s amazing how often an employee will take a couple of feet off the end of a ten-footer when he only needs a few inches. And avoiding unintentional waste also extends to storing cut-offs in a dry place where mold isn’t going to be an issue, and stacking horizontally rather than standing boards up against a wall, where bowing will occur.
What a woodworker might consider waste, a customer might think of as character. A few knots can liven up a hickory door panel, and a less expensive cut can sometimes be more appealing – and more profitable – than using all heartwood.
Clean-up costs
A well-engineered dust collection system will dramatically reduce the amount of time that employees spend cleaning their workstations, setting up machines and dusting off parts before and after machining.
Emptying bags can be a time-consuming chore, but Indiana-based Iron Bull (ibhoppers.com) has a solution for shops that have a forklift. The company’s Drop-Bottom Sawdust Hopper is essentially a big box that hooks to a cyclone collector with an optional quick disconnect inlet port. There’s a site gauge on the unit, and when it gets full it can be emptied gently through the bottom, reducing the amount of ambient dust that’s released into the air. Larger units come with a ladder, and the inlet port on the top is customized to fit a woodshop’s existing cyclone system. The Sawdust Hopper comes in capacities from three-quarters of a cubic yard up to ten cubic yards, so it works for most shops. And Iron Bull also offers a range of self-dumping solutions for shorts, cut-offs and other types of woodshop waste, including small ones that tuck under a cut-off saw.
Dust collection needs to concentrate on the points where dust is actually made. An enclosed CNC with integrated dust control makes a huge difference in the cleanliness of a woodshop. But not every small shop can afford such a solution, so woodworkers need to be a little creative. That begins with getting a hose as close as possible to the point where a cut is being made, but it also means taking a look at trajectory.
For example, efficient dust collection is notoriously difficult on miter saws because the waste is projected in a wide field. FastCap (fastcap.com) has come up with a couple of fairly effective solutions, including the ChopShop Saw Hood and Saw Hood Pro. Rousseau (rousseauco.com) also makes a tent-like device for corralling dust. Simply called the 5000, it pops up like a child’s play tent and folds compactly away when not in use.
Such devices are a boon on a jobsite when installing trim or casework, so that the customer’s home or office doesn’t fill up with fines. In the shop, a more permanent, shop-built box that sits behind the saw may be more appropriate. I saw one many years ago in a hobbyist’s shop that was on a simple wooden track, so that it could slide from side to side to accommodate cuts other than simple 90-degree ones. A hose attached to the back caught the finest dust, and the rest fell into a garbage can below.
Fine dust is also a huge challenge because of the possibility of a spark setting off an explosion. Masterduct (masterduct.com) offers an extensive line of Master-PUR hoses that are specifically designed for the woodworking industry to eliminate static electricity at the source. They’re also extremely flexible for easy maneuvering in any workspace and flame resistant. Plus, they have a smooth inside that ensures optimum flow.
Processing waste
There are several ways to create new products from waste material that let a shop avoid both the cost and the guilt of sending everything to the landfill. Pet stores, farm and home stores, horse boarding stables and dog kennels will accept and often pay for clean, nontoxic chips. They may object to irritant species such as black walnut and cedar, but if a shop’s waste is primarily pine, spruce and fir, this can be a profitable option. And landscapers or garden centers will often accept or buy dust and chips for mulch.
That seems to work especially well for small shops that only produce a few cubic yards of cut-offs a year. A profitable outlet for larger shops is to sell their waste to a pellet or briquette maker, or buy the equipment to make them in-house. WEIMA (weima.com) makes shredders and briquette presses that make briquettes out of softwoods, hardwoods, chipboard, plywood, multiplex, OSB or MDF. The company’s C-Series machines are ideal for small- and middle-sized operations with an average waste production volume of 400 to 900 lbs. a day. At the other end of the spectrum, WEIMA’s TH Vario Plus series can be adapted for very large volumes. And in between are a whole family of models for medium-sized woodshops.
RUF US Inc. (ruf-briquetter.com) also makes briquetting machines. The company says that “most RUF briquetting systems pay for themselves in 18 months or less”, and that wood briquettes are a great fuel source that releases only as much carbon dioxide as was naturally absorbed by the growing tree during photosynthesis. This makes briquettes an attractive option for reselling to environmentally conscious businesses.
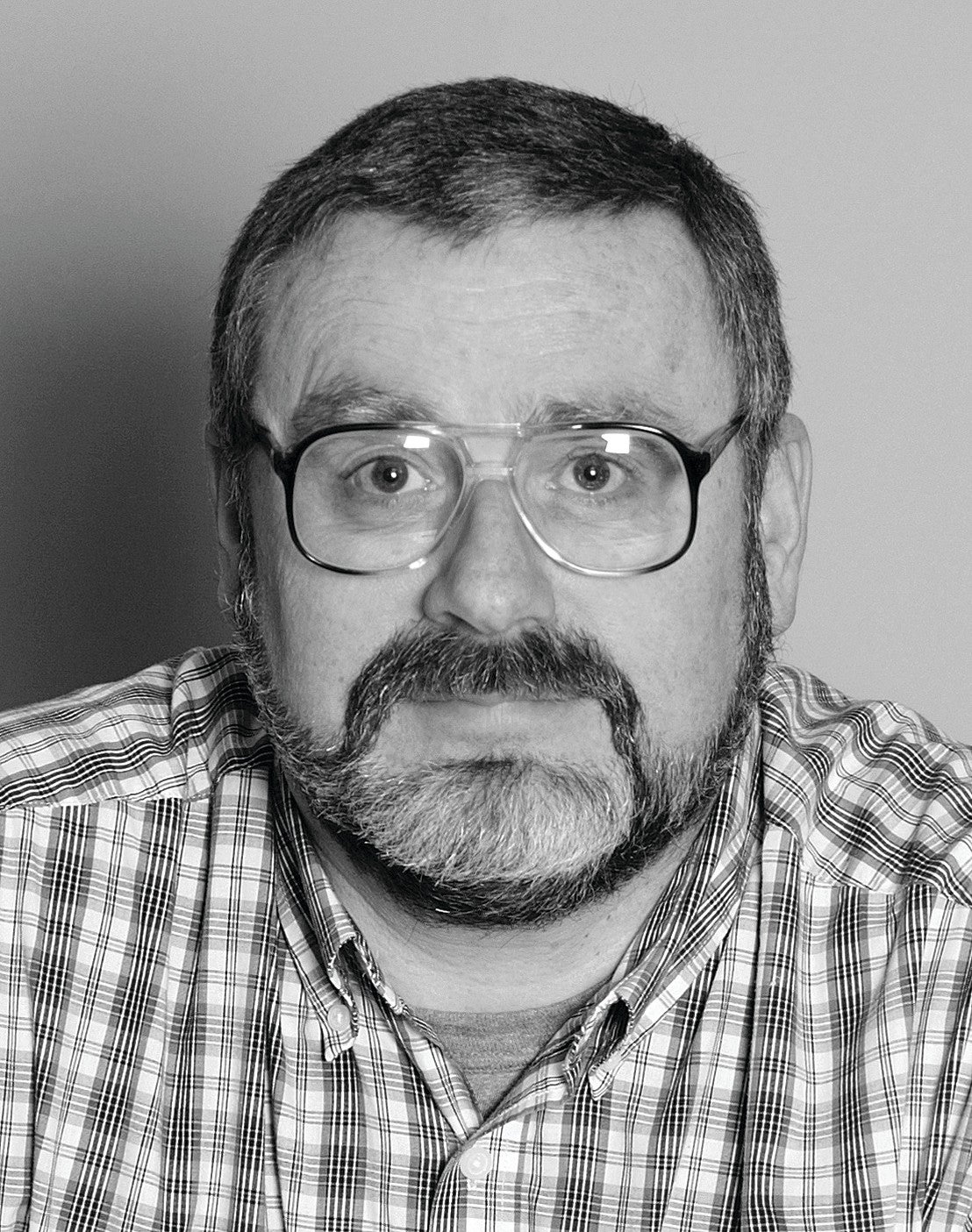