The biggest challenge for custom woodshops when they’re adding flat panels to their traditional solid wood catalog is edgebanding. Cutting panels to size is nothing new, but then sealing their edges with decorate tape can be a real learning experience.
Neither the shop nor the customer wants an adhesive bond to fail and allow the tape to peel off. The edges of the tape also need to be of the highest quality, where they are smooth to the touch, properly sealed, and don’t reveal the substrate through an uneven or overly assiduous sanding job.
A sticky solution
Edgebanding is a viable option for shops of all sizes because even though the machines change with scale (as in, the volume of doors or fronts being made), the manufacturing basics don’t. For example, there are only a couple of serious choices for hot-melt glue, no matter whether it’s one door or a thousand. Those are ethylene vinyl acetate (EVA) and polyurethane (PUR). There is also amorphous polyolefin (APO), which is akin to EVA but has only moderate heat resistance and doesn’t do well with oils or alkalis. But APO is quite customizable in terms of hardness, tackiness, and open cure time. It has its uses, but mostly with paper and fabric.
The way that EVA works is a lot like the familiar white and yellow woodworking glues (PVAs) that we’ve used for decades. Perhaps the biggest difference is that those cold-applied wood glues have a water base that evaporates over a longer period of time than the heat-treated solvent in EVA.
The industry has been shifting a little bit away from EVA and toward PUR over the last few years, even though PUR is more expensive. That’s because PUR works a bit differently than EVA. First, it very quickly forms a solid layer between the edgebanding and the substrate (in a few seconds), and then it takes a day or two to react with humidity and expand, which completes the bond. It creates an exceptionally strong bond between most bandings and substrates, and micro emission versions don’t release significant levels of VOCs or isocyanate vapors. The new bond is also relatively heat and moisture resistant, so it’s a better choice for sink cabinets, bathroom furniture and lab or clinic applications.
EVA is a mechanical bond and PUR is a chemical bond. Once cured, PUR will not re-melt while EVA will.
As with any product, there are some disadvantages to PUR adhesive. First off, it has a finite shelf life of about a year and if it’s exposed to air it begins to cure (so, keep it in the manufacturer’s sealed packaging until right before it is to be used). Plus, any excess that squeezes out needs to be cleaned up with a solvent, rather than just wiped with a damp cloth. It can be a nightmare if it isn’t purged properly from equipment with the appropriate wax – it sets like a rock. PUR can’t be stored in a cold environment and then used immediately because it won’t bond properly. But it can handle a lot more heat around, say, ovens, than EVA.
Another reason for the industry switch is that the PUR glue line is not only stronger but thinner and less visible.
Even though PUR will bond with more edgebanding types and substrate surfaces, EVA adhesive isn’t going anywhere. It’s less expensive to get into, has a longer shelf life and a short cure time, and is easier to use and clean up.
With all those factors in mind, woodshops have developed a habit of using less expensive EVA in places where it won’t be seen or it won’t have to endure a lot of contact and use, and then using PUR on the aesthetically critical and more handled surfaces and edges. A woodshop that chooses to go that route might want to consider having two glue application stations (one for EVA and one for PUR), or else invest in a hybrid head that allows switching between the two glues. A third choice is to be very careful when cleaning the glue pot and applicators before switching adhesives. There are special granules available for cleaning. Some machines simply won’t handle both EVA and PUR, so that’s something else to verify before deciding on a glue.
Hybrid heads are also handy if the shop is using colored glue that matches or complements differently colored laminates, because they allow faster switching. Different glues require different application temperatures, too. There are no standards, only norms, so be sure to check the packaging and adjust the glue pot temperature setting accordingly. And during application, it’s a good idea to check the temperature at the rollers, too, especially in shops located in cold climates.
The most common causes of glue-line failure are an inadequate volume of glue, cold glue, cold shops, and cold banding. So, keep the climate right, and store the glue and edgebanding in a warm but not hot area. A slow feed rate can be problematic, too, as can inadequate roller pressure. And keep in mind that the panels can actually be too hot. They may need to cool down if they’ve been through a process that uses heat to laminate or veneer them, because their substrate may be too hot to accept the edgebanding glue properly. Other glue-line problems can be caused by the banding being over or under tensioned, or the rollers are misaligned, or the feed rate is too fast, or the substrate isn’t flat (it may have mill marks or be concave or convex across its width).
These are all glitches that can be spotted with a little experience, so it’s a good idea to train new operators on scrap. One idea is to have them do a test run building something such as storage cabinets for the shop, rather than jumping right in on casework for clients.
A poor edgebanding job may not be evident right away but will probably present itself within a few months as cabinets endure seasonal changes or some degree of use. There is an upside: it can be relatively easy to sand or cut away edgebanding on a straight edge and reapply new tape.
A broad band of choices
Woodworkers are generally comfortable using veneer and solid wood edgebanding, but when it comes to colored bands the material choices can give one pause. Some of the more common materials are PVC, polypropylene, melamine, and ABS.
PVC or polyvinyl chloride is inexpensive and widely used, but it isn’t the toughest material available, and it can shrink or expand a little over time. It can be purchased with a layer of hot melt adhesive already applied to the back face. The band or ‘tape’ is an extrusion, which means that it’s not laminated in layers. The color is the same all the way through, which helps when a shop is cleaning up ragged edges. It can also be UV printed and lacquered. The normal way for the pre-glued banding to be applied is with a low temperature hot air roller. That’s because PVC melts at relatively low temperatures, although that hasn’t stopped it becoming one of the most common plastics in the furniture industry.
Polypropylene (PP) edgebanding is a thermoplastic that is valued for its flexibility, stability (it won’t shrink), and heat resistance. It’s ideal for curves and twists, even on small radii. It can be produced in both solid colors and patterns, and even woodgrain. It can also be imbued with a high gloss, which can be quite useful in modern casework designs. PP is a bit more environmentally sound than some other plastics, and it can be burned without creating an airborne health hazard.
ABS is a bit like PVC without the chlorine. It’s an environmentally friendly extrusion that is impact and thermally resistant, and it has the same color all the way through. Some municipal projects will specify and require ABS edgebanding because of its safe disposability and recycling properties.
Some edgebanding materials such as melamine can be applied with contact cement, or they come with a pre-applied layer of glue so they can be ironed on. Materials such as metal or acrylic may have issues getting around tight corners, while the plastics can generally be doctored with plasticizing chemicals that make them more flexible. However, some of those chemicals can eventually become airborne and there may be health issues there.
A shop that is just exploring edgebanding options can make a small initial investment in a portable bander and run a couple of jobs that way before investing in a serious, stand-alone machine. The options for upgrading include machines that go far beyond just applying adhesive and rolling the tape in place. A shop can have the machine trim and soften (break) edges, make seamless joints, and even become part of a CNC cell that is almost completely automated.
This article was originally published in the April 2022 issue.
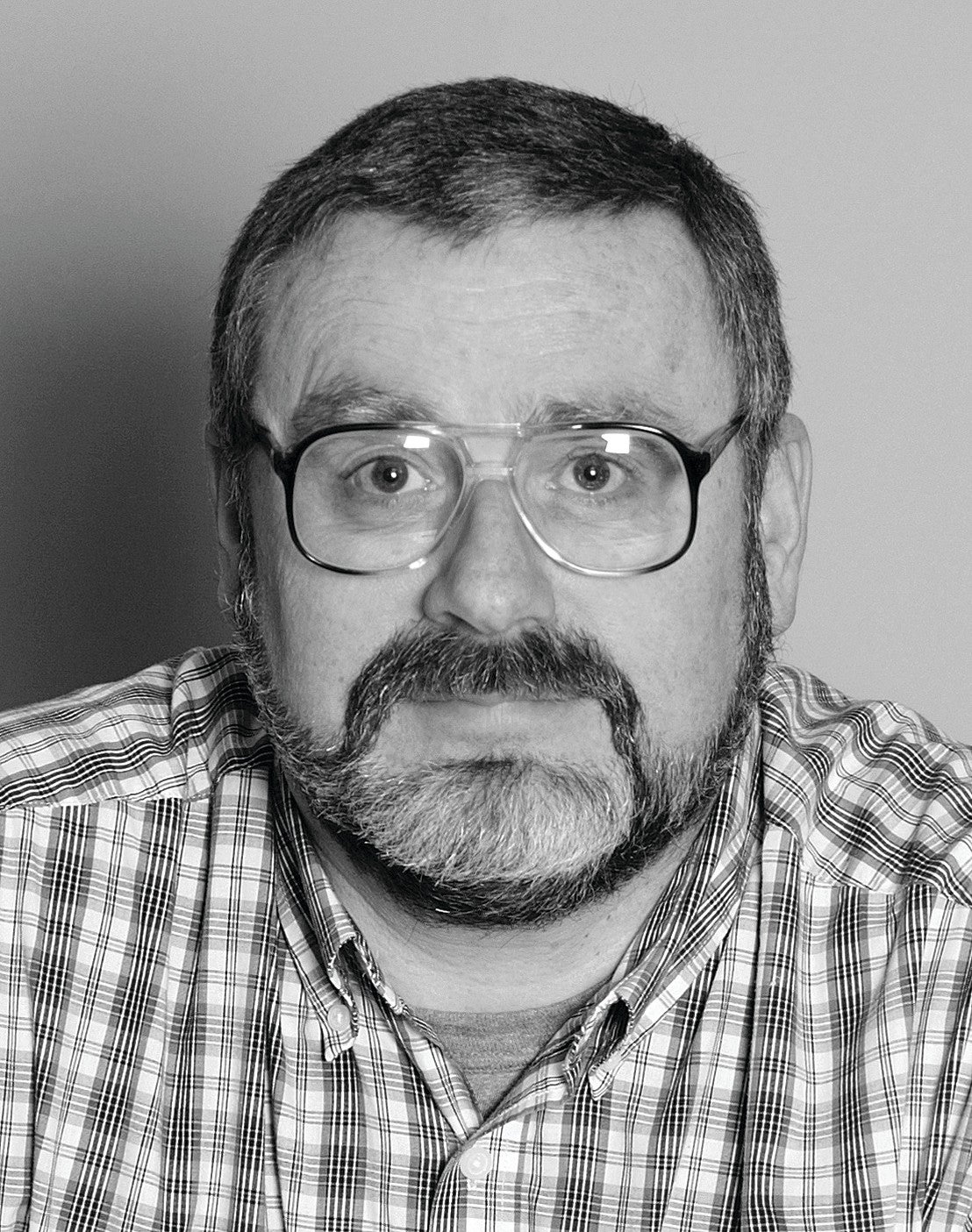