Getting the Best Connection
Shops of all types can improve their joinery methods and procedures with these new jigs, fasteners and CNC solutions.
Woodshops can choose one of three very distinct options when it comes to joinery.
There are traditional methods, often aided by jigs and fixtures, that use standard woodworking machinery and tools. Then there’s CNC joinery that’s built into CAD design, where parts are milled to fit together. Or a shop can choose one of a host of mechanical fasteners that join the face frame, door and box parts together.
The choice often boils down to volume – the more parts that need to be joined, the more mechanized the joinery needs to be. Another influencing factor is cost. Is it less expensive to hire and train a woodworker to make joints, or spend the money on a new CNC? Do the time savings from using plastic or metal fasteners offset the cost of milling, gluing and clamping? And there’s also precision: CNC controlled machines tend to have fewer rejected parts, but that can sometimes be offset by the fact that people can read grain and defects in the wood. That can be especially important when the joinery is visible.
Year after year at shows such as IWF and AWFS, new options tease us. Are we missing the boat, or is this just a fad? Staying on top of evolving technology is critical when it comes to remaining competitive.
New jigs, old methods
Whether they’re commercial or shop-built, joinery jigs can often improve speed, accuracy and the strength of a joint. Best of all, most of these are relatively inexpensive. One of the earliest volume production techniques in woodshops was the pocket screw. Though it’s now firmly ensconced in CNC joinery, there are still ways that woodshops can use this solution without investing in a CNC, and the incumbent staff training.
Companies such as Kreg Tool (kregtool.com) and Castle (castleusa.com) build jigs that work for everything from occasional use to entire kitchen building. Now Armor Tool (armor-tool.com) has launched the Auto-Jig ($149.99), a device that automatically sets the drill guide block and drill bit collar based on the thickness of the workpiece. That means there’s no more manual setting, measuring or adjusting. A woodworker just clamps the workpiece and starts making pocket holes. The jig works with materials of different thicknesses and uses color-coded screws. When the block self-adjusts, the correct screw length color is displayed.
Shops have used wooden dowels in production work for centuries, and they’re still quite popular. A new jig from JessEm Tool Co. (jessem.com) will create 1/4”, 3/8” and 1/2” dowel holes on the end or face of a workpiece, pre-setting the holes in 1/8” increments. What’s new is that a built-in alignment slot allows the woodworker to match up dowel holes that are spaced further apart, for perfect alignment. Included in JessEm’s package is the main jig body, three guide mounts with the respective drill bits, and indexing pins.
Rockler Woodworking and Hardware (rockler.com) is offering a new jig that adds decorative details to the mitered corners of boxes, while also reinforcing the joints. The Corner Key Doweling Jig guides an extended-length bit at a perfect 45-degree angle. The resulting holes allow users to add visual interest with contrasting wooden dowels, or perhaps metal or plastic materials. The jig includes interchangeable 1/8”, 1/4” and 3/8” diameter drilling guides, and it’s adjustable for both different thicknesses of stock and for fine-tuning the hole position. Drill bits are included and there’s even a free plan for a training project. It’s a kitchen knife block that incorporates a decorative corner dowel pattern that is created with the jig.
And for woodworkers who want to train new people in old-fashioned joinery, Lie-Nielsen Toolworks (lie-nielsen.com) has just released a two-DVD (or streaming video) class on mortise and tenon joints. The company says it shows hand cutting of mortises in detail, as well as a quick look at a hollow chisel mortising machine and techniques for producing accurate tenon cheeks. The video covers small draw bore mortise and tenon joints, plus the wedged through tenons of Arts and Crafts furniture. Mitered through tenons and table leg mortises are also shown.
CNC joinery
One of the biggest challenges with joinery on a CNC is that the tooling rotates, so the bits naturally create round inside corners and square outside ones. Some shops use panel joints such as the dog bone and T-bone to combat this, where the bit creates a small circle beyond each corner of a mortise. That’s a great way around the problem of fitting a square tenon into a rounded hole, but unfortunately it can create a new challenge. Parts of those rounded corners can often be seen after the joint is assembled.
There are definitely some easy ways around this for a good CAD designer. For example, the tenons can be rounded. But there are some inspiring, creative techniques, too. For example, there’s a really good article on digital joinery on the ITP Fabrication website at New York University (itp.nyu.edu/fab). It starts out with a chart of some 50 joints that can be made on a CNC, and then shows some examples of perfectly executed, visually pleasing joints that are used in furniture and casework. There are also some larger images of both the drawings and executed joinery at the source site, winterdienst.info, where shops can even download a folder that contains CAD files for the joinery. Anyone building virtual parts in sheet stock will learn something new here.
Beyond designing joinery that fits together, several CNC manufacturers are adapting their machines to handle new joinery fittings. For example, at the 2018 IWF, Komo Machine (komo.com), Felder Group (felder-group.com) and Holz-Her (holzherusa.com) all ran demos where the Lamello Clamex system combined convenient assembly system with nesting. And about a year ago, Laguna Tools (lagunatools.com) introduced a new boring/inserting machine for use by cabinet manufacturers that uses Lockdowel (lockdowel.com) fasteners. Called the SmartShop LD4, it is faster and more precise than any other method when drilling and inserting these products. The machine drills for and then inserts Lockdowel’s clip products. It’s perfect for cabinets, drawer boxes, closets, desks, solid wood furniture and many other applications. It has four zones and two drilling units, one for 5mm and one for 8mm. And its two vibratory barrels have the ability to insert 30 or 40mm spring pins and Lock Dowel E clips, H-clips, or channel locks.
California-based CNC Factory (cncfactory.com) has also introduced a Lockdowel automatic inserter. Called the Scorpion LDR, it has four working zones (a single employee can run it), automatic material loading, laser-guided robotic measuring and advanced wireless barcode reading.
Joinery connectors
In hardware, there are two families of connectors. Some are simply mechanical ways to join parts, while others are designed with shipping in mind.
Outsourcing has changed the fundamentals of the cabinetmaking industry over the past decade. And while ordering online has improved dramatically, shipping is still a bit of a challenge. Ready-to-assemble (RTA) technologies are increasingly seen as the primary solution when it comes to more affordable and efficient ways to ship and assemble. A few of the latest mechanical connectors are designed for shop installation, but most were specifically created to accommodate RTA. The connectors not just for boxes. They are also used to join five-part doors, face frames and even drawer components. Some are permanent and often require gluing, while others are knock-down, and most are hidden. Some, such as Fastenlink (fastenlink.com), just use a woodshop’s existing traditional or CNC machinery and simply replace older options like wooden dowels with a simple Industry 4.0 option.
Among the newest products is OVVO’s (ovvotech.com) V-1230 invisible connector, which has a deeper profile than the company’s original V-0930. The new device significantly increases its holding strength in chip and wafer core sheet stock. By the way, Biesse (biesse.com) has now named OVVO as one of its Selected Partners. The fasteners are available in the U.S. through E.B. Bradley (ebbradley.com) in Los Angeles, and they can be installed in slots cut by the company’s own stationary and portable machines, or they can be used with CNCs and auto insert techniques. For small shops, OVVO has just teamed up with PantoRouter (hybridpantorouter.com) to semi-automate the process. That machine operates in three axes. Other than the positioning of a workpiece on the X and Y axes, a woodworker can set the exact plunge depth of the router cutter on the Z axis.
Knapp Connectors (knappconnectors.com) is an Austrian company that makes furniture and millwork connectors. All of its connectors are concealed, self-tightening and can simply be snapped together for fast assembly. Woodworkers can order sample packs from the company online.
The least complicated joinery option is the simple screw, but even that has evolved of late. For example, the Quickcutter (also called the QC) from Quickscrews (quickscrews.com) features an extra groove in the shank to eliminate splitting, and doesn’t require a pilot hole or countersink bore, according to the company.
This article originally appeared in the June 2019 issue.
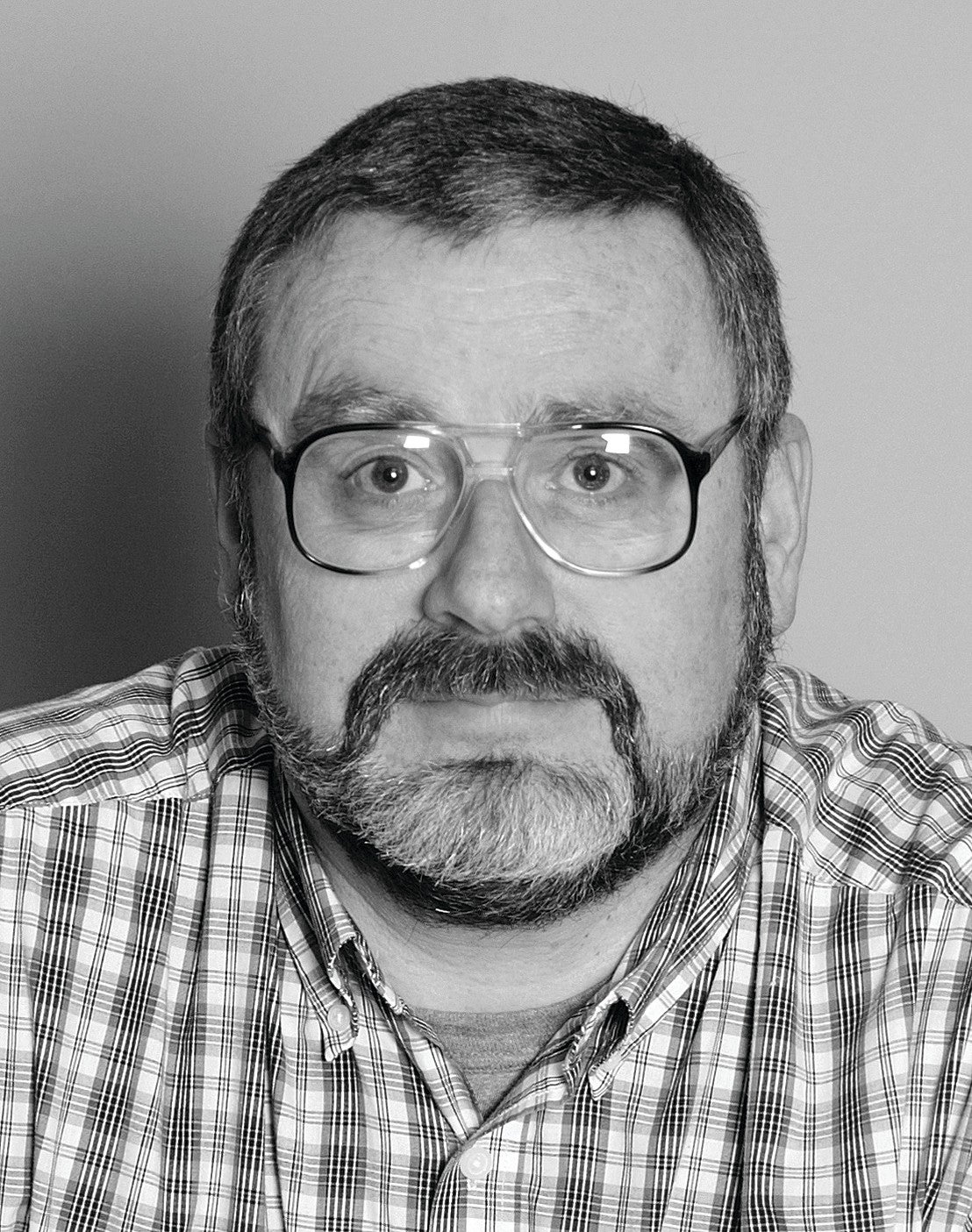