Hi-tech Edge Banding
Today’s production machinery operates in a work cell with automatic functions and no glue lines
With a market that continually leans farther away from five-part wood doors and a world around us that’s desperately looking for clean surfaces, edge-banding is becoming hotter than ever. But applying banding can create a bottleneck in shops that aren’t set up adequately for higher volume. In response, manufacturers are creating new forms of work cells that rely heavily on robotics and sensors to create workflow paths that streamline the process.
For example, SCM Group (scmgroup.com) is helping woodshops integrate edge-banding machines into cells that are fitted with rollers, panel return devices and automatic loading and unloading systems. These are often assisted by robots and fitted with IoT sensors to instantly control the machine functions. The company’s Stefani cell H is a state-of-the-art edgebanding and square-edging cell that’s fitted with an automatic panel feeder system. It also has an external milling unit to size panels, and a display in the operator’s area that shows how to position the panel so it can be correctly machined. It can process batches ranging from a single panel to damaged panels and the standard pack without the need for any production downtime to change the format, thickness, ornamentation and gluing quality.
Beyond building better cells, there’s a tidal wave of webinars in these post-pandemic times. Many discuss edgebanding, and some of those can be really useful for shop owners. If you haven’t participated in one, a webinar is just an online session that includes a select group of viewers who have the ability to ask questions in real time. One of the most discussed edgebanding topics right now is the ability to create a bond with no visible glue lines. Traditional edge joints have a tiny line between the tape and the adjoining face that can fill up with dirt and bacteria over the years. The gap is as wide as the glue layer is thick. Sometimes edgebanding becomes brittle and starts to chip, revealing more of a gap. Zero-joint edgebanding eliminates any gap by filling the space with a malleable layer that delivers the look of a monolithic (one-piece) door, drawer front or counter edge. The interior design market demands this cleaner, seamless joint on contours and edges, and thankfully that has become an attainable goal because of new methods and products. Essentially, the woodshop (or for smaller shops the outsourcing supplier) uses a hot air, laser or NIR bander to melt the filler, which the industry describes as “a co-extruded polymer functional layer”. Yup, it’s plastic.
FusionEdge from Ontario based Doellken (na.doellken.com) is one of many new edge-bandings that can be applied so that it shows no evidence of a joint. The secret, according to the manufacturer, is that there’s “a premium functional layer (which is a proprietary, pre-applied glue) that is consistent and color coordinated with the edgebanding”. The glue matches the band color, and can even be made to match grain. The system works with hot air, laser and infrared bonding technologies, and it is available in solid colors and wood grains.
Dual purpose machines
Biesse N.A. (biesse.com) has its own answer to the invisible glue line – going glue-less! The company’s new Ray Force system uses infrared lamps (actually NIR, or near infrared rays) to fuse a reactive layer between the substrate and the banding. It works especially well on curves, as it is applied using an easily removed contour edgebanding unit that has been designed for Biesse Rover A, B and C edge machines. The technology can considerably reduce production costs when compared to standard glue-based methods because it requires no maintenance, there’s no clean-up and the time spent waiting for glue to warm up is eliminated. On top of all that the process means is more environmentally friendly. Compared to laser technologies, Biesse says that Ray Force requires a much smaller investment and is also much easier and safer to use. And unlike laser technology, it can be quickly switched back to traditional EVA or PUR glue with just an easy manual equipment change. The bottom line on Ray Force and NIR is that they eliminate having to apply conventional hot melt glue and the accompanying glue pot maintenance, while still delivering an excellent bond.
The new powerEdge Pro Duo from Homag (homag.com) was designed with the latest in sensors and control algorithms, and the result is a machine with an intelligent control system that defines speed, temperature and contact pressure at every point on the contour. In most cases, no manual fine adjustment is required. It has edge positioning and 360-degree gluing, where the start and end of the edge are positioned precisely, even on the smallest components. It also comes with a genuine combined function for zero joint or hot-melt glue application. The unit can do both, with no conversion required. The hot air nozzle for reheating the hot-melt glue also activates the functional layer of a zero-joint edge.
Ltronic is a new laser edging unit from Holz-Her’s Lumina series (holzherusa.com), and it, too, has a NIR module on board. The machine’s design makes it possible to change over from the Ltronic to a traditional Glu Jet unit in less than five minutes, using a very precise HSK interface. The Lumina has an automatic attachment recognition feature, so it knows when a change-over occurs and is ready for use immediately afterward. The change-over uses two special carts that were designed by Holz-Her that can be conveniently rolled up to the machine and docked on the guides. Then the HSK lock is engaged, the power supply is connected using quick-release connectors, and you’re up and running.
Ltronic doesn’t require heat-up and is ready for operation at the touch of a button. It operates without any noise emissions whatsoever, and without compressed air. The wavelength of the NIR module is very close to the intensity of the diode laser, allowing it to optimize energy with the utmost precision over the entire length of the workpiece. And no energy is lost between workpieces. There’s a database onboard with all the latest co-extruded and subsequently coated types of edging already stored for simple selection by the user. Each laser edging requires a specific quantity of energy, depending on factors such as edge thickness and color, and the unit automatically sets those as needed.
Paint and glue advances
Another interesting new direction for woodshops that paint their edgebanding to match doors is a program being offered by RAMS Ind. in Arthur, Ontario (ramsindustries.com). RAMS sells thermoplastic edgebanding, hotmelt adhesives and technical profiles for the woodworking industry. The company has created a new program where it provides banding that exactly matches some of the most popular Benjamin Moore cabinet paint colors, and does so in both hue and sheen. With this, a woodshop no longer needs to sand, prime or paint edgebanding to match the door color.
PUR adhesives are essential to the edgebanding industry, but they give off emissions called diisocyanates. According to the American Chemistry Council, these “are organic compounds containing two isocyanate groups”, TDI and MDI, which affect the respiratory tract. Both chemicals have been shown to be portal-of-entry toxicants, and to cause a decrease in respiratory rate in mice and rats. The council notes that among other negative effects, “MDI and TDI-related occupational asthma can occur from overexposure in the workplace.” As a response, Henkel Adhesives (henkel-adhesives.com) has created Technomelt MicroEmission (ME) PUR adhesives for the furniture industry. This is a PUR adhesive range that contains less than 0.1 percent of monomeric isocyanate, and as such it is exempted from workplace environmental restrictions and doesn’t require any additional training or safety measures other than those currently in place. We’re going to be hearing a lot about ME PUR over the next few years from Henkel and other glue manufacturers.
Speaking of PUR, a new edgebander from Cantek (cantekamerica.com) comes with a state-of-the-art PUR glue pot. The machine is called the MX370PUR, and its PUR glue system has many advantages over older machines including a precise and thin glue joint, high heat resistance, and high moisture resistance. It comes equipped with working units including high frequency end trim, high frequency top and bottom trim, high frequency corner rounding, PVC scraping and a buffing station.
The Altendorf F5 edgebander also has an easily exchangeable and cleanable glue pot. machine (altendorfgroupamerica.us) comes with a lot of options from a 10” touchscreen with memory function to a pre-milling station, a trim saw, top/bottom trimming, a radius profile scraper, a corner rounding unit, a surface scraper and a buffer unit. It’s pretty speedy (22 feet per minute), and it can also be fitted with a practical multi-radius profile scraper.
One other timely note: the pandemic has generated a renewed interest in metal surfaces that are naturally antibacterial, and DC Distributing (dc-dist.com) has now developed a substantial collection of metal-coated edgebanding to support that need. The company’s MKT Alpha-Tape is ABS covered with real metal foil, to give the look of aluminum, stainless steel, polished chrome, or brushed gold/brass. DC stocks this banding in half, one and two-millimeter widths.
Shopping for an edgebander?
For smaller woodshops, several manufacturers offer edgebanding machines with budgets in mind. Castaly’s EB-1SC is one of seven machines that the company (castaly-cncmachine.com) offers in this category, and it’s a manual edgebander with a MSRP of $6,290. There are four larger automated machines in the catalog, too.
The Felder Group (felder-group.com) also offers an entry-level machine, the ForKa 200 ECO Plus, that can handle workpieces up to 2” thick. The company lists eight machines in the category that cover just about any sized shop’s needs.
Three models from California-based Laguna Tools (lagunatools.com) also cater to a wide range of production volume. The Bandit 3/2 is a compact heavyweight that was designed for every-day professional use with all 2mm materials. The intermediate Bandit 4 is perfect for small shops that are doing thin edgebanding from 0.4-3mm thick. It has top/bottom and front/rear edge scraping and buffing. And the top of the line Bandit 5 adds pre-milling and corner rounding.
Atlantic Machinery in Milford, Conn. (atlanticmach.com) carries both Fravol and Vitap edgebanders. The high-end of the Fravol line includes the Rapid Series, which are automatic machines with many available options and a wide range of applications for PVC, ABS, melamine, veneer, and solid wood strips. The smaller Vitap machines offer manual and semi-automatic options that are definite candidates for one or two-man, or medium-sized shops.
Edgebanders from Casadei-Busellato America (casadeibusellato.com) are now imported and supported by JKL Machinery in Brighton, Mich. (jklmachinery.com). The company offers both manual and automated models that range from the basic ALA 10 for straight and shaped panels all the way up to the Flexa 607 which can process at up to 22 meters per minute, has very fast and precise set-ups, and can be equipped with a pressure belt unit so it can process any type of material.
The new Badger 3600 has a built-in material stop that will open when it’s ready for the next piece of material, according to its manufacturer, CNC Factory (cncfactory.com). The company also offers the Badger 4600 which includes corner rounding, and the 5600 that has a PUR zero glue line feature.
Hermance Machinery in Williamsport, Penn. (hermance.com) offers a huge array of both new and used edgebanders. The company also sells edgebander parts and accessories.
Grizzly Industrial (grizzly.com) also carries a couple of small manual machines, and two portable, inexpensive tools for occasional jobs.
Martin Woodworking Machines in Charlotte, N.C. (martin-usa.com) carries four Bi-Matic brand edgebanders that start with the small Prima 3.2.C manual and extend to the Prima 7.3-r.a. Plus PNE L-Tec Edge. That’s a hot melt and hot air (laser/hot air tape) machine capable of edging material up to 3mm thickness. It comes with a 12” touchscreen, pneumatic panel distance, a pre-milling unit, a double trim saw, servo controlled top and bottom milling stations, a pneumatic end rounding unit, a servo-controlled profile scraper, a glue scraper and a buffing unit.
NewCNC.com in Holland, Mich. (newcnc.com) offers three Fuse edgebanders. The new Fuse 6 is a heavy-duty machine designed for space-conscious shops, which has stations for gluing, guillotine, end trim, rough trim, fine trim, scrape, and buffing. The intermediate Fuse 7 was designed for multi-shift production and is geared towards nested cell manufacturing. And the Fuse 8 is an affordable machine that works well in a nested-based environment when combined with a CNC or beam saw.
NEXTechmachinery (nextechmachinery.com) has two edgebander models. The EB300 Series is a heavy-duty edgebander which is simple to operate and complements woodworking shops both large and small. The EB400 is designed for high output edgebanding and is an operator-friendly machine with touchscreen controls. It’s also equipped with a twin spindle jump pre-milling unit with pneumatic movement and diamond tools.
Safety Speed Mfg. in Ham Lake, Minn. (safetyspeed.com) has a pair of entry-level, American made machines that are available in hot air or glue pot variations and both have a compact and affordable design.
SNX Technologies (snxtechnologies.com) develops and manufactures its nVision line of banders in-house at its Sauk Rapids, Minn. facility. The company’s EVA hot melt contour edgebanders offer woodworkers an easy, affordable, and versatile shaped part edgebanding solution with a minimal footprint.
Stiles Machinery in Grand Rapids, Mich. (stilesmachinery.com) offers one of the largest catalogs of edgebander brands. They range from simple gluing machines to units that can sand, shape, cut and/or apply an assortment of edge treatments. There are banders for hard profiles, for soft-form continuous strips on a contoured edge, for post-forming a banded profile, and machines that are specifically designed for contour forming.
This article was originally published in the October 2020 issue.
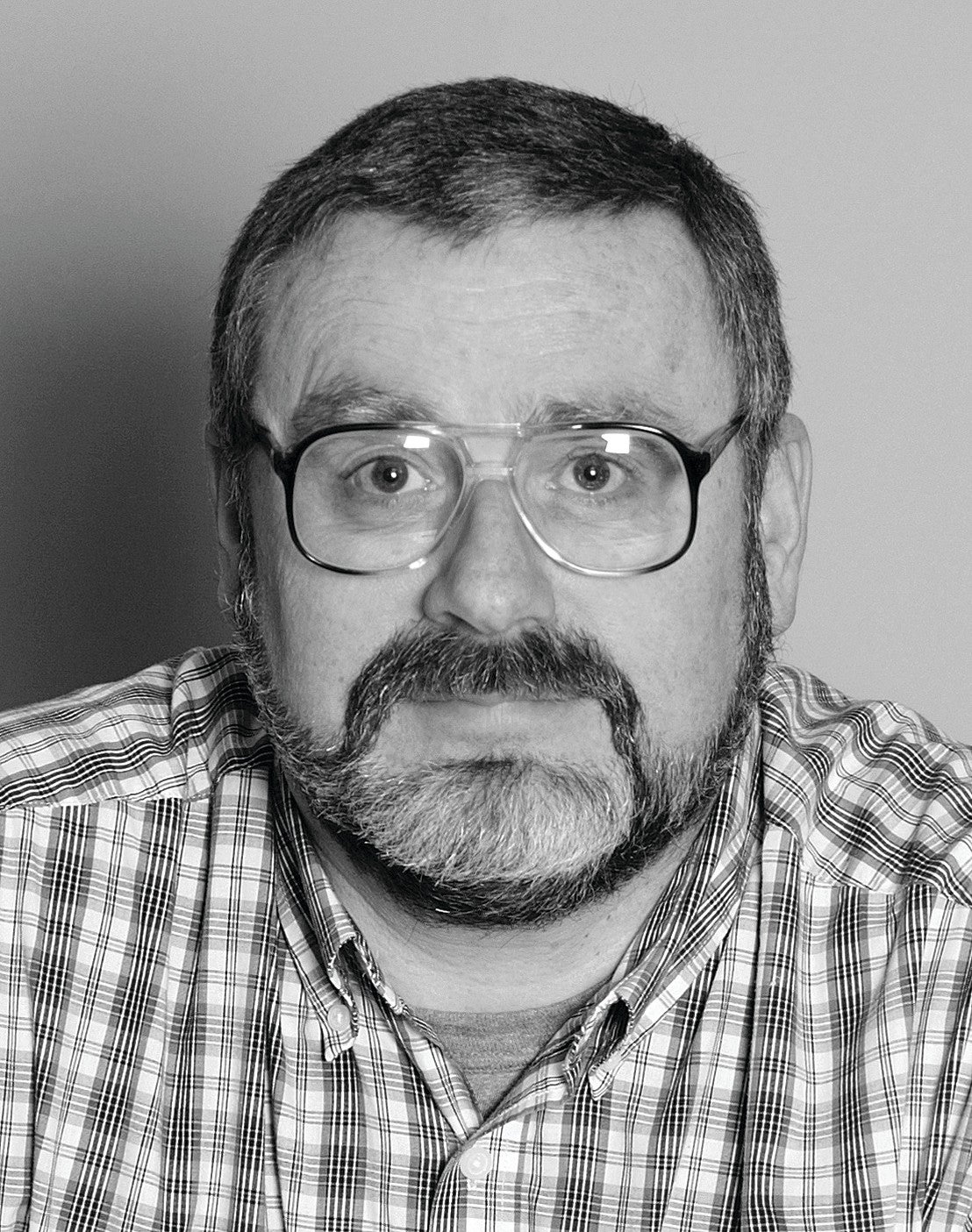