Just scratching the surface
Panel producers continue to innovate with new products and more offerings
Technology keeps marching onward, and the wood industry seems to stay in step. Our machines are evolving rapidly, but so are the materials they cut, shape and coat. The transition from carbon-based fuel to electric vehicles over the next couple of decades may be one of the biggest factors here. There’s a perception that oil-based plastics and resins may become more affordable over time as demand for gasoline declines, and that hints at a whole new array of surface materials.
But there’s no need to wait. There are already some very interesting options available to woodshops.
New materials
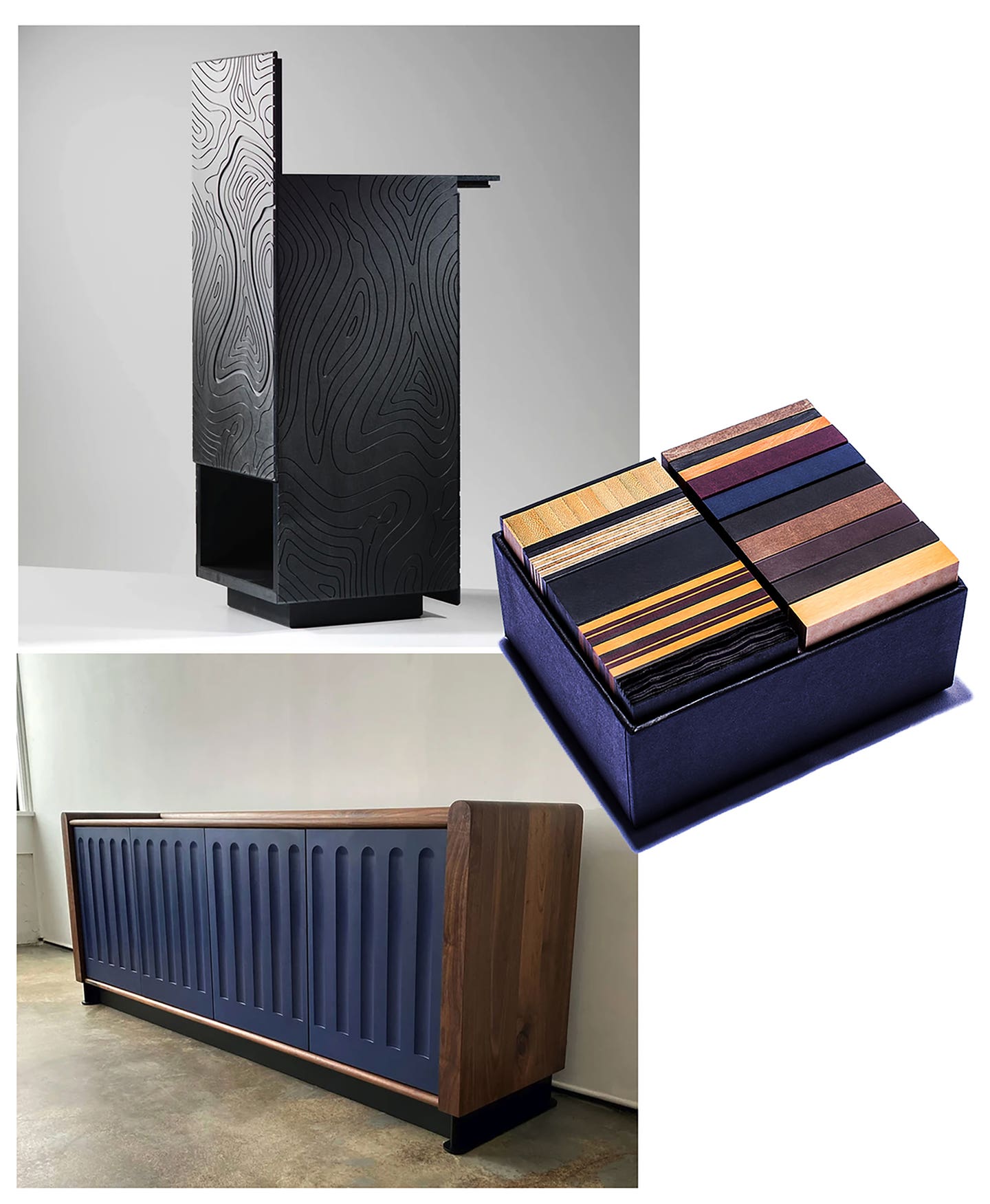
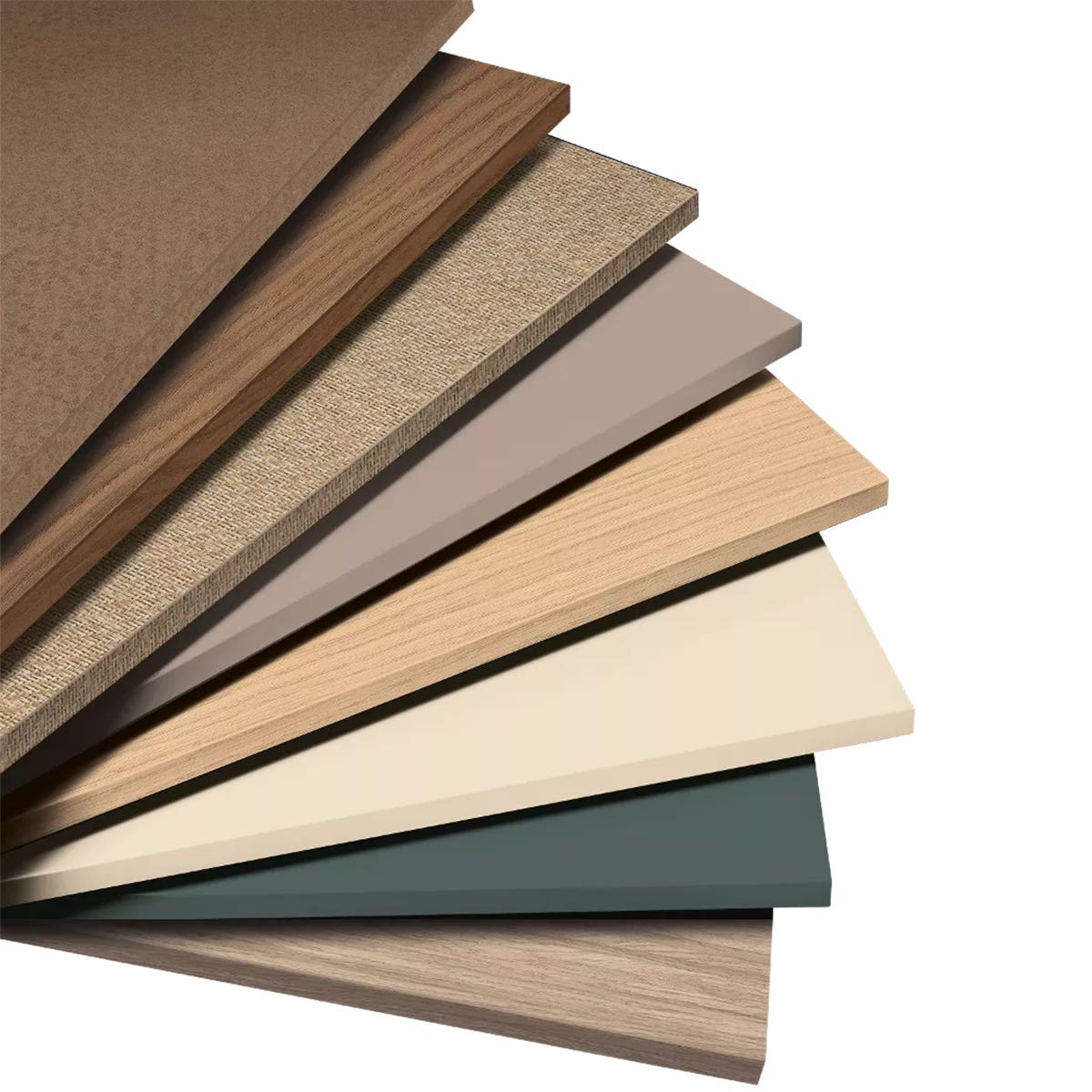
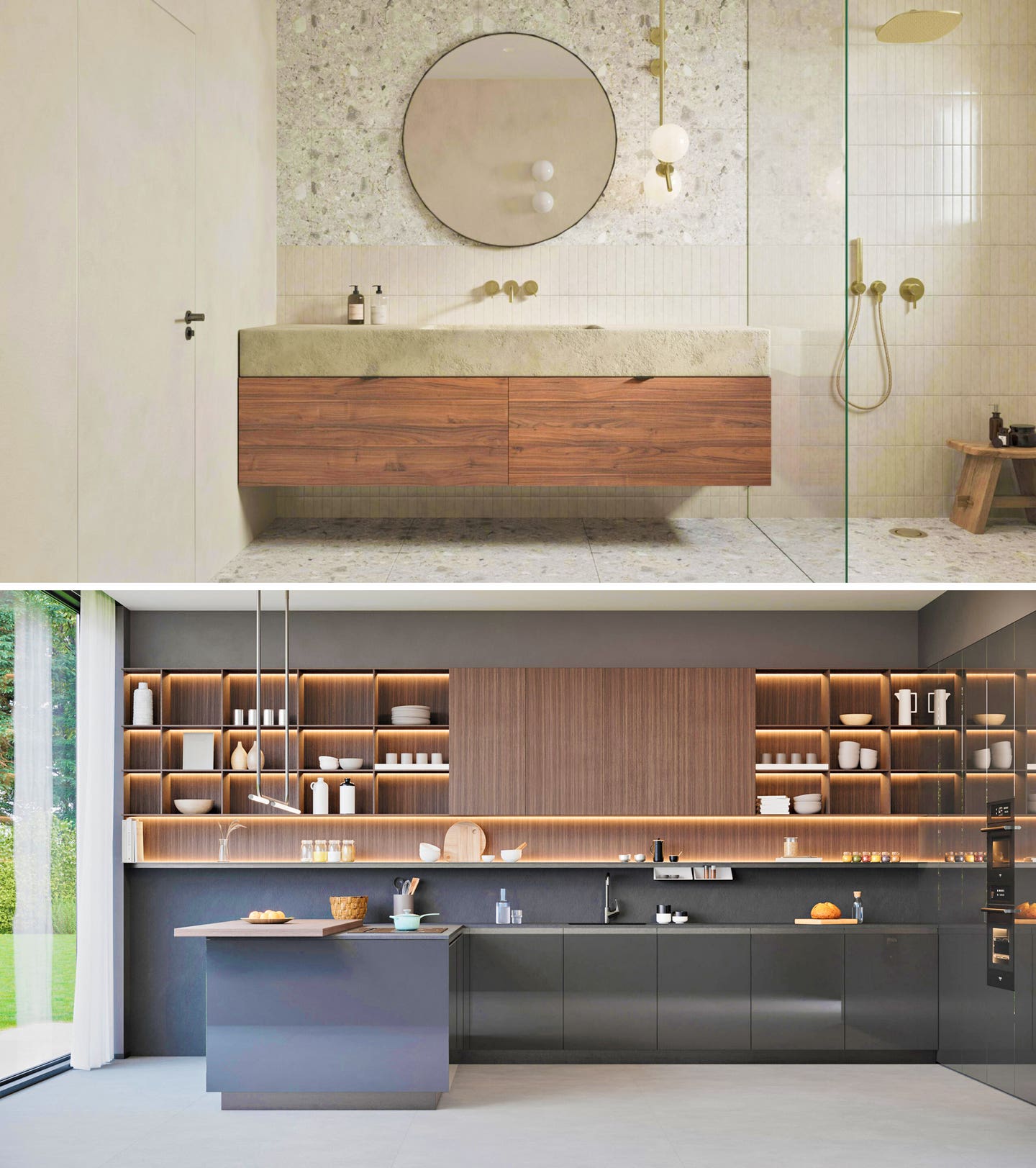
Founded in 1943, Richlite (richlite.com) makes a surface material that is very resistant to chipping, scratching or denting. Over time it has evolved into a significantly sustainable choice, now made with 100 percent recycled products while using an exclusive waste-to-energy process. Its core is Forest Stewardship Council (FSC) certified paper sourced from responsibly managed forests. Layers of this engineered paper are infused with thermosetting resin, then pressed under heat and pressure to produce a solid and stable sheet material that can be used indoors or out.
The new Decorative Collection 24+ from EGGER (egger.com) offers more than 80décor/texture combinations that come in sheet stock, laminate and edging options. Egger is an Austrian family-owned business with a presence in Linwood, N.C. Its products include raw particleboard, MDF boards, thin MDF boards, thin MDF boards with foils, lacquered boards, thermally fused laminate (TFL), laminates with a colored core, edge banding, and MDF moldings. Egger laminate is made with decorative paper infused with melamine resin and one or more layers of soda craft paper infused with phenolic resins, which are laminated under high pressure and heat.
Duramar Interior Surfaces (duramar.com) makes TFL and polymer laminate panels in its 50,000-sq.-ft. Facility in Irvine, Calif. The products are in line with Leadership in Energy and Environmental Design (LEED) certification, and if a project is based in Southern California, products sourced within 100 miles of the jobsite double in LEED value.
Plywood and lumber
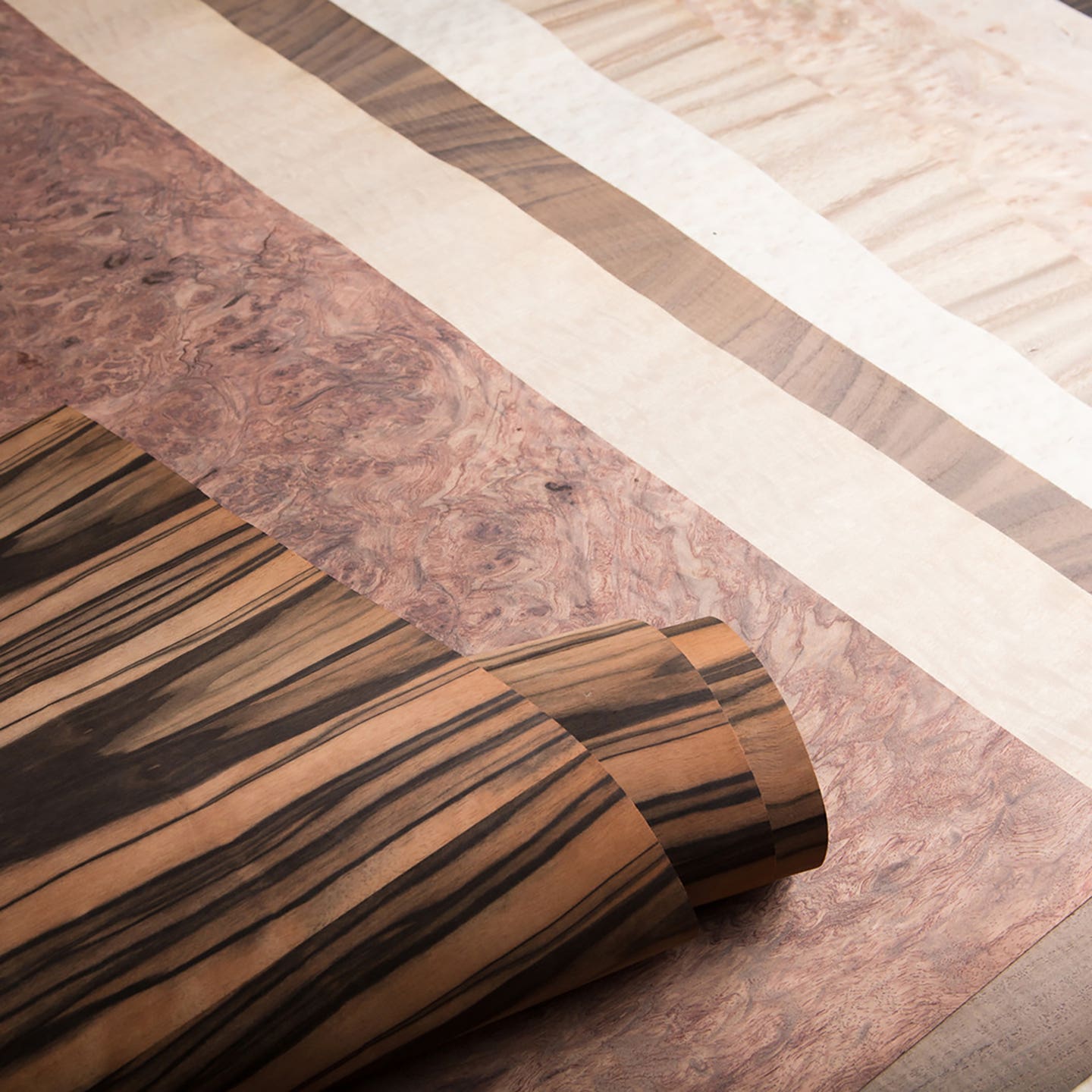
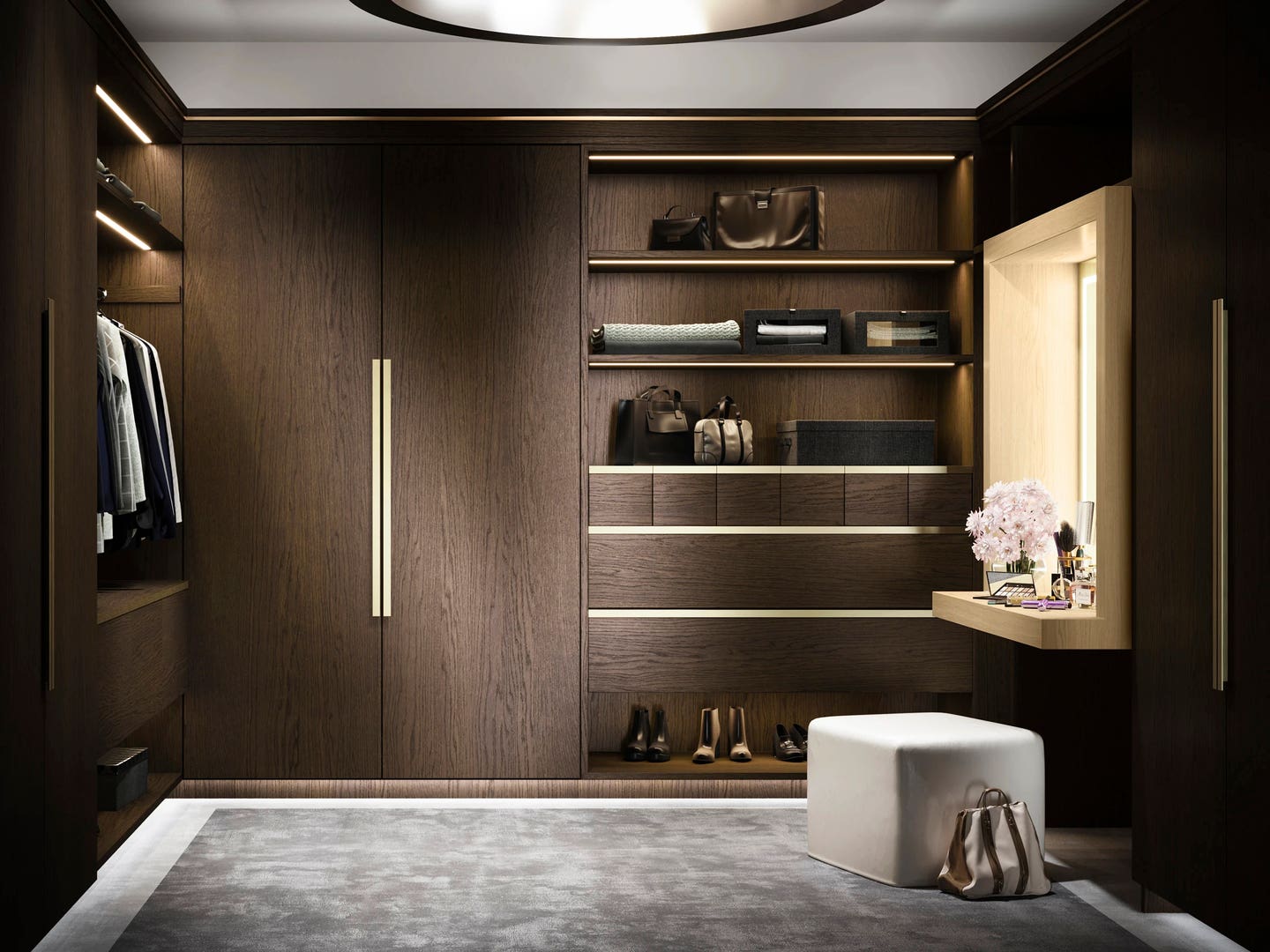
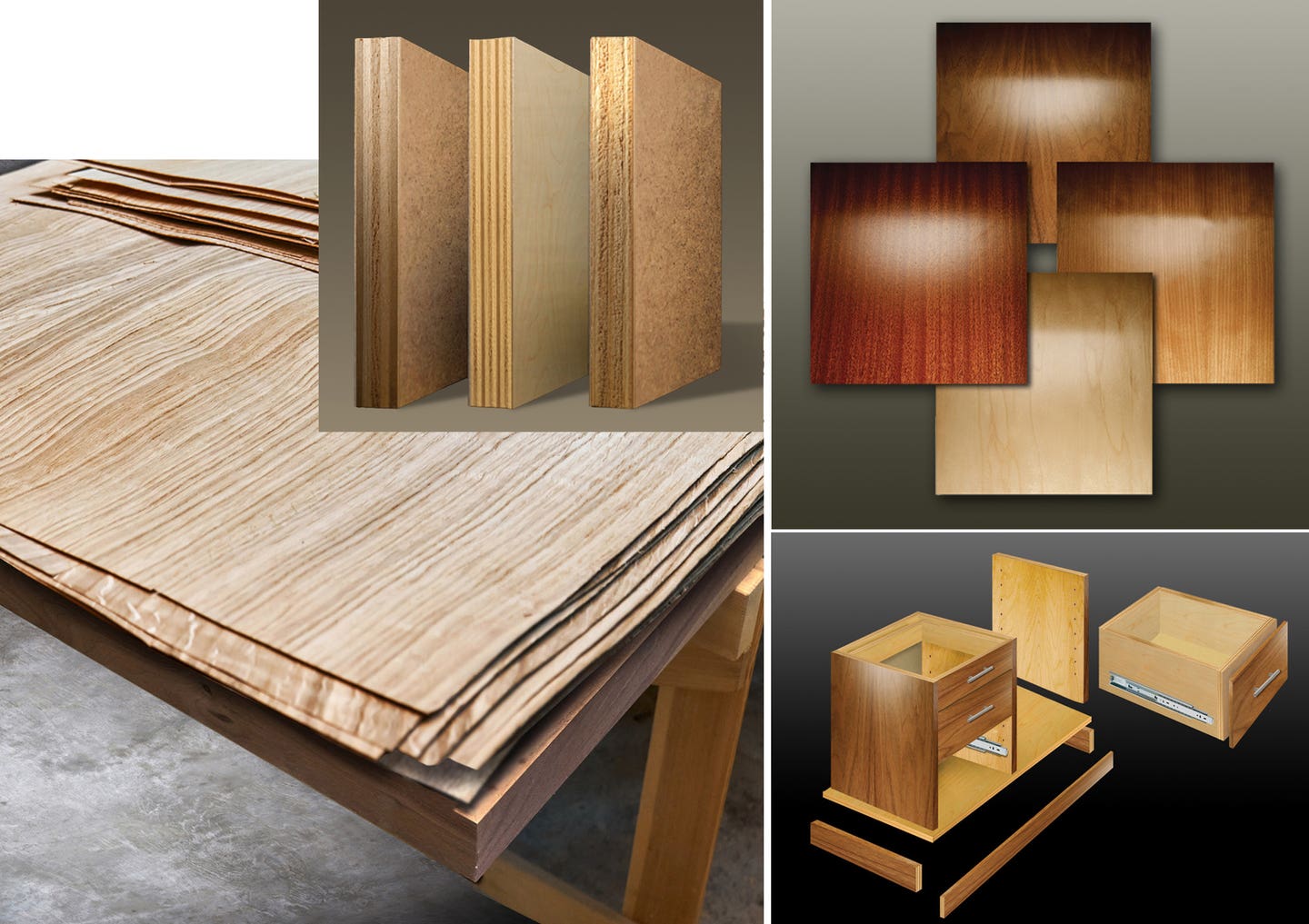
Formwood (formwood.com) makes Uni-FormWood reconstituted veneer that features guaranteed color and grain consistency and is surprisingly less expensive than naturally imperfect, real species counterparts. These reconstituted wood veneers are defect-free, identical from sheet to sheet, and are offered on a choice of backers from paper to plywood. And the company’s RainboWood product is real wood veneer that’s infused with luminous colors. The natural tones are extracted from real wood and replaced with luminous color, while the rich wood grain remains. The veneer requires only a natural sealer or topcoat finish.
California-based GL Veneer (glveneer.com) offers a huge range of veneer species and substrates — there are more than 880 SKUs. When these are laminated onto the large number of substrates the company carries, GL Veneer can produce over 100,000 possible custom plywood products. And if that doesn’t meet a shop’s real wood surface materialrequirements, there’s also one of the most extensive collections of live edge slabs in the country, if not the world.
Hardwoods Inc. (hardwoods-inc.com) carries Shinnoki prefinished wood veneered panels that let architects and cabinetmakers design and create some very stylish and distinctive interiors. Unlike regular veneered panels, these are ready-to-use and as easy to work with as a melamine board. They offer huge time and cost-savings but deliver the unique look and feel of real wood veneer. They use a proprietary mix-match technique to guarantee a continuous look without significant visual interruptions, and they bring color consistency to the entire project. Shinnoki is a complete program including matching panels, veneers and edge banding that are all available from stock in 18 colors.
The mills at States Industries (statesind.com) can build custom plywood panels to a woodshop’s exact specifications. A proprietary manufacturing process allows the shop to customize every detail about a panel, from the substrate to the veneer species, the color, and a NOVA finish.
L.L. Johnson Lumber Mfg. Co. (theworkbench.com) makes very large, edge-glued hardwood panels, and also carries Bally Block edge-glued butcherblock counters.
For smaller shops in and around Connecticut, it may be handy to know that Parkerville Wood Products (parkervilewoodproducts.com) carries a large selection of stock hardwood plywood and sells half sheets in either a vertical or horizontal orientation, for which it charges $6 more than half the cost of a full sheet.
Indiana-based Superior Veneer (superiorveneer.com) is a manufacturer of sheet veneer and plywood, including thick wood veneer faces, sheets and panels. Superior says its SuperBack Hi-Performance laminate is an alternative to high-pressure laminate or phenolic-backed veneer. It possesses most of the moisture resistance found in traditional laminate, but is more flexible, so sheets are much easier to handle and apply.
On the West Coast, Talbert Architectural Panel & Door (talbertusa.com) offers oversized veneered panels, veneer sheets and UV finishing. The factory also makes 90-minute fire doors and cut-to-size parts and panels.
Imaginative solutions
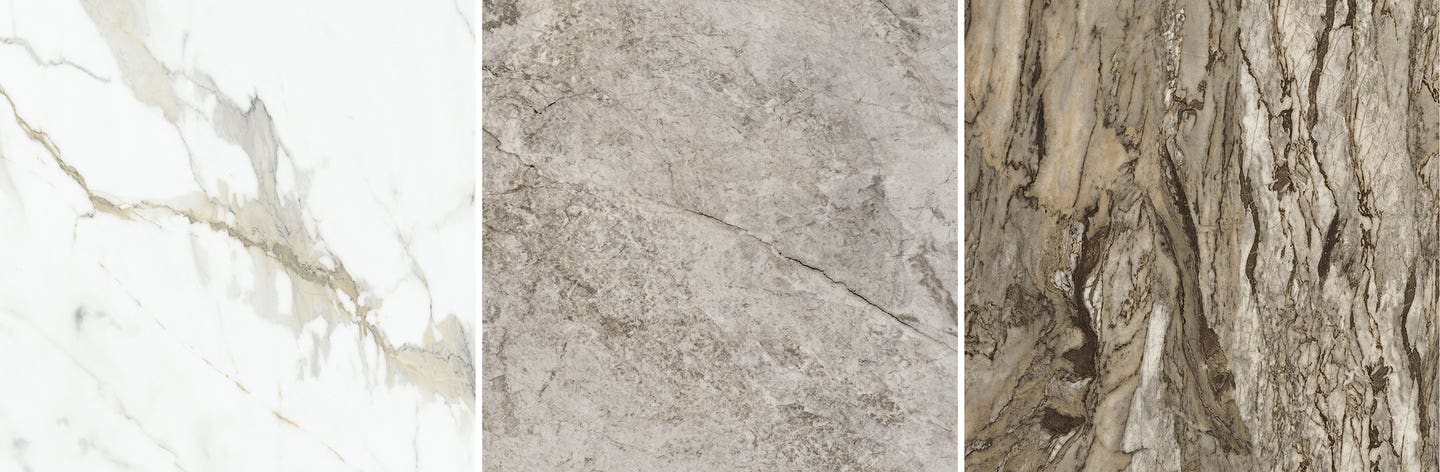
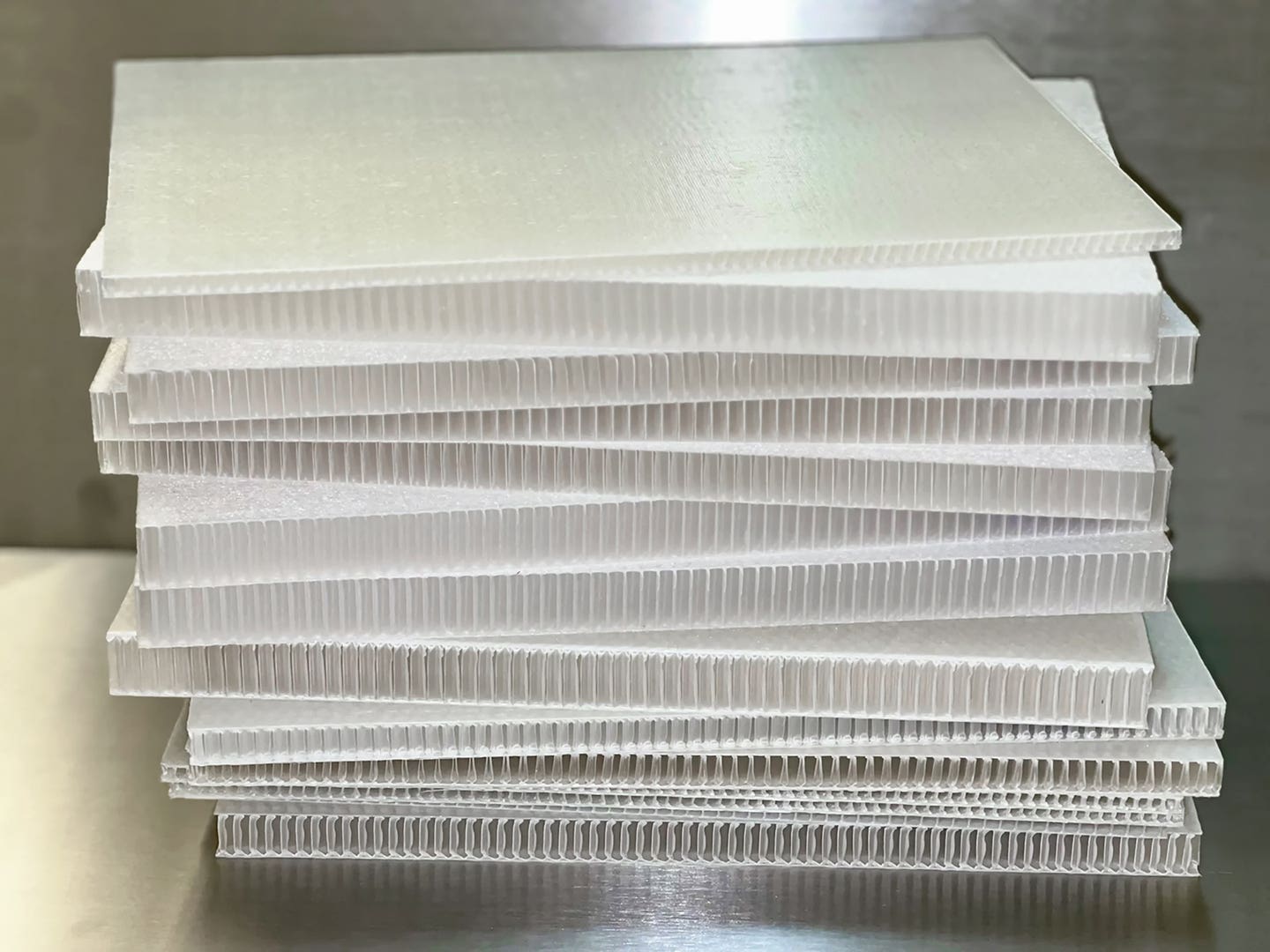
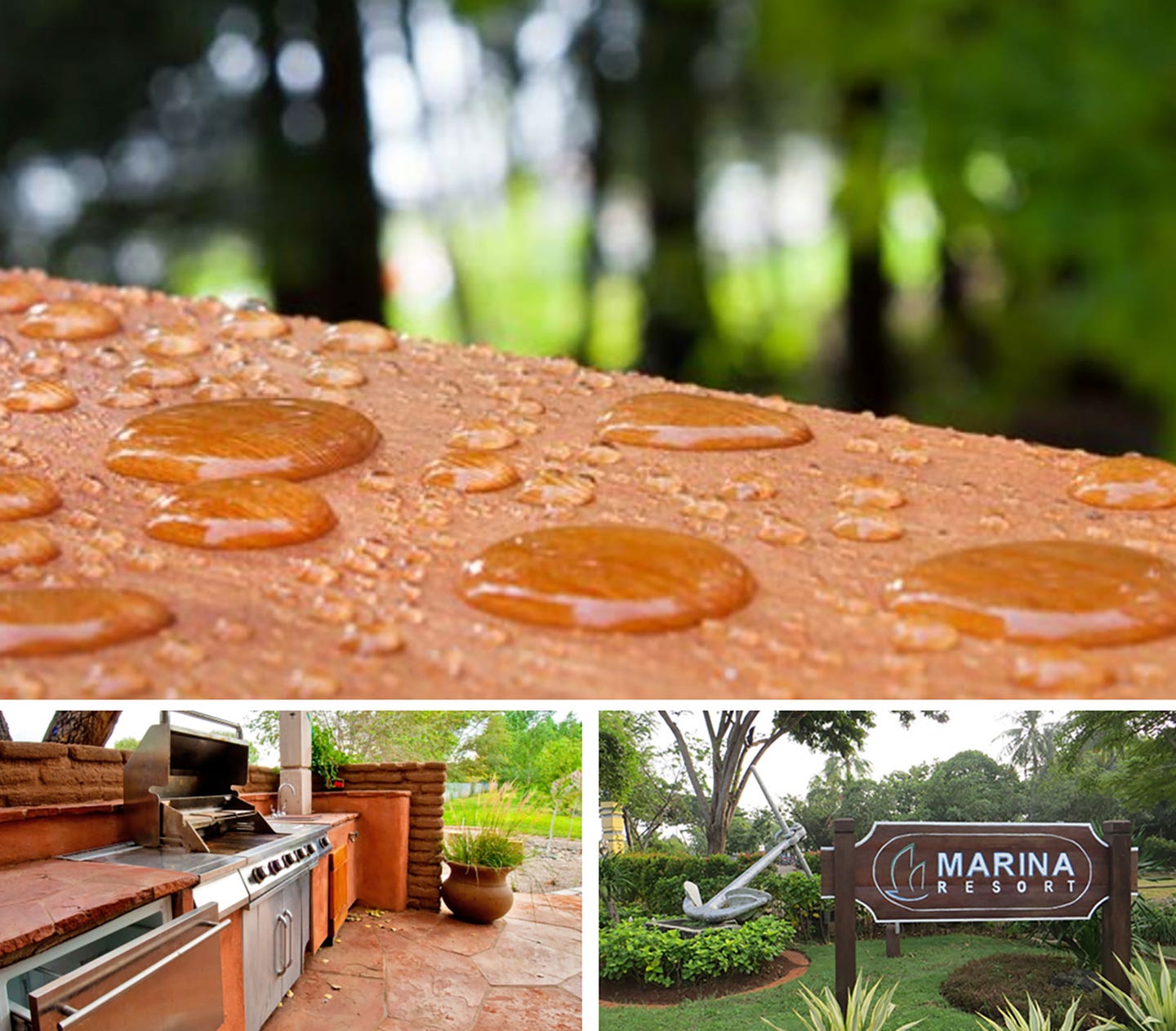
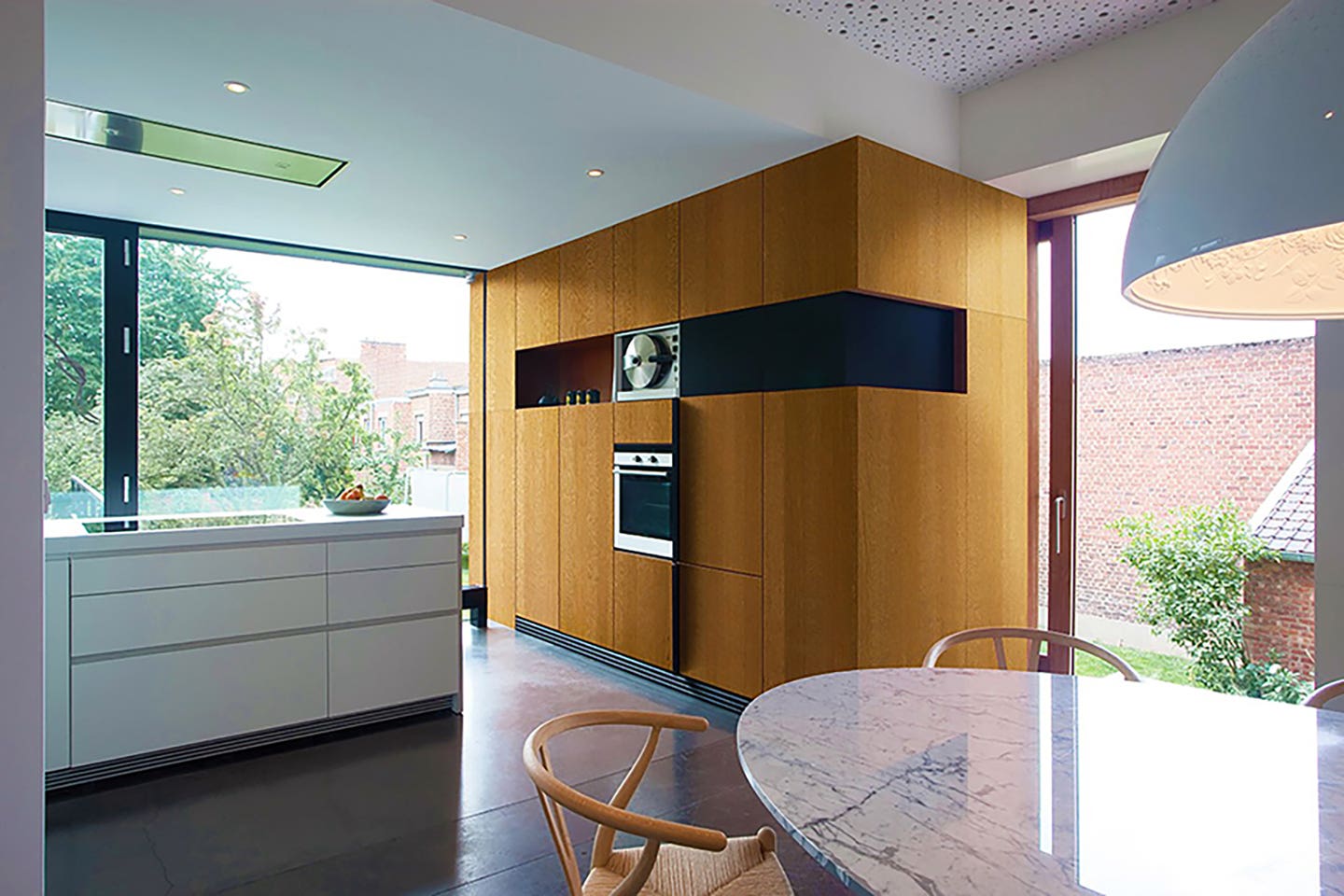
Distributors such as Kencraft (kencraftcompany.com) and Anderson Plywood (andersonplywood.com) offer a phenolic-coated Baltic birch product that has two faces that are coated with a heat-bonded, colored, translucent phenolic film. This reveals the grain (less so in darker colors), and delivers a smooth, glossy and hard surface that is resistant to abrasion, weather, moisture, and many household chemicals. Anderson notes that “the panels are rigid and often used for making jigs and tooling, as they are extremely durable.” They are also used for desks, table tops, shelves, fittings for kitchens, offices and shops, garden furniture, signs and billboards. There are currently nine colors available.
Kerfkore (kerfkore.com) is familiar to woodworkers as a supplier of bendable substrates that let shops build curved reception desks, but the company also makes two foam-core, lightweight panels. The denser version, Worklite XPS Foamkore, has recently had an update to a more environmentally friendly format. The panel is very customizable as it can be cut to a smaller size or extended to meet special orders. And the company can also manufacture it with surfaces such as laminate, veneer, metal, leather, or similar semi-rigid materials, and add custom frames and internal bands to save customers time and resources.
Lenderink (lenderink.com) has introduced a new composite substrate called Elkboardthat is engineered to deliver unparalleled strength-to-weight performance. It’s resistance to water absorption and has a sleek, non-porous, No. 38 Dyne surface that facilitates easy printing and lamination. It can be used in many ways including compression molding for intricate 3D projects, or serving as a versatile flat inner-ply or overlay. It’s 3D moldable and easy to laminate, cut, glue, print and paint. Stiffer than aluminum, it’s 30 percentlighter than maple.
Omnova (omnova.com) makes a broad range of 2D, 3D and paper laminates that help woodshops meet their budgets. The company’s 3D and surf(x) 3D laminates are used on cabinet fronts, while the 2D and paper products are used on interior and exterior surfaces. There’s an app called the Harmony Exclusive program that lets shops navigate through the various options and deliver the same style and design throughout the project while meeting both functional and budgetary requirements. Omnova’s surf(x) technology delivers increased resistance to scratches, abrasion, and chemical cleaners, making these laminates ideal for horizontal surface applications such as retail fixtures, work surfaces, counters and tabletops.
For woodworkers who need a lightweight solution and are willing to think outside the box, Kerr Panel (kerrpanel.com) has just added ThermHex polypropylene honeycomb panels to its catalog. In comparison to traditional materials such as MDF and llywood, ThermHex can offer up to 85 percent weight savings. Polypropylene is a strong and flexible lightweight material that provides optimal mechanical performance in composite Nexos exterior panels from Uniboard sandwich structures. The honeycomb panels are available in thicknesses from 3mm to 28mm, and in sheets with a maximum width of up to 1400mm. The standard panel length is 2500mm, while longer sheets are available upon request.
Sing Core (singcore.com) is a new base material for surface materials that is only available under license by the truckload to participating manufacturers. It’s a ‘green’,lightweight and high strength core that is sandwiched between two stress skins, and the manufacturer says it’s stronger than steel (660 psi). It’s an alternative to cores such as balsa wood, plywood, particleboard, MDF, plastic, aluminum honeycomb, paper, cardboard and foam. A Sing Sandwich comes with a plywood surface material that can be worked with woodshop equipment and can be bonded to other surface materials using standard wood glue. It can be cold pressed, vacuum pressed, hot pressed, cut, sliced or ripped just like wood.
Woodshops looking for exterior surface materials might be interested in the Nexos line from Quebec-based Uniboard (uniboard.com). The manufacturer makes TFL and HPL laminates, MDF, particleboard, and door cores. Its Nexos exterior panels are made with 100 perecent recycled and recovered pre-consumer wood fiber. They’re easy to work with and can be cut, routed and machined to various specifications. Designed and produced with proprietary technical properties that resist moisture, Nexos is ideal for use outside where the panels are not directly on the ground. They are available in North American standard sizes and thicknesses.
Surface materials are fairly inert, so they depend on their substrate for much of their environmental impact status. For example, Roseburg’s Duramine is a TFL panel that can be ordered through Paxton Lumber (paxtonwood.com) and other outlets. It comes on stock substrates that include Roseburg’s SkyBlend or UltraBlend particleboard, or SkyPlyhardwood plywood or MDF. A Duramine panel can be specified FSC, which may contribute to LEED credits, and it can meet ULEF (ultra-low emitting formaldehyde) requirements if is delivered on SkyBlend particleboard or MDF, or on SkyPly CFC veneer cores.
While natural wood casework will always be popular, there’s a global trend toward man-made surfaces. These materials allow designers to add color, texture and detail to flat panels and moldings. Beyond the aesthetics, they also offer a sense of sterility in a post-pandemic world, and a degree of durability and wear resistance that sprayed coatings are perceived as lacking. The impression is that manmade materials are tough, pretty, and safe. But wood is warm and will always have a special place in our hearts.
Originally published in the July 2024 issue of Woodshop News.
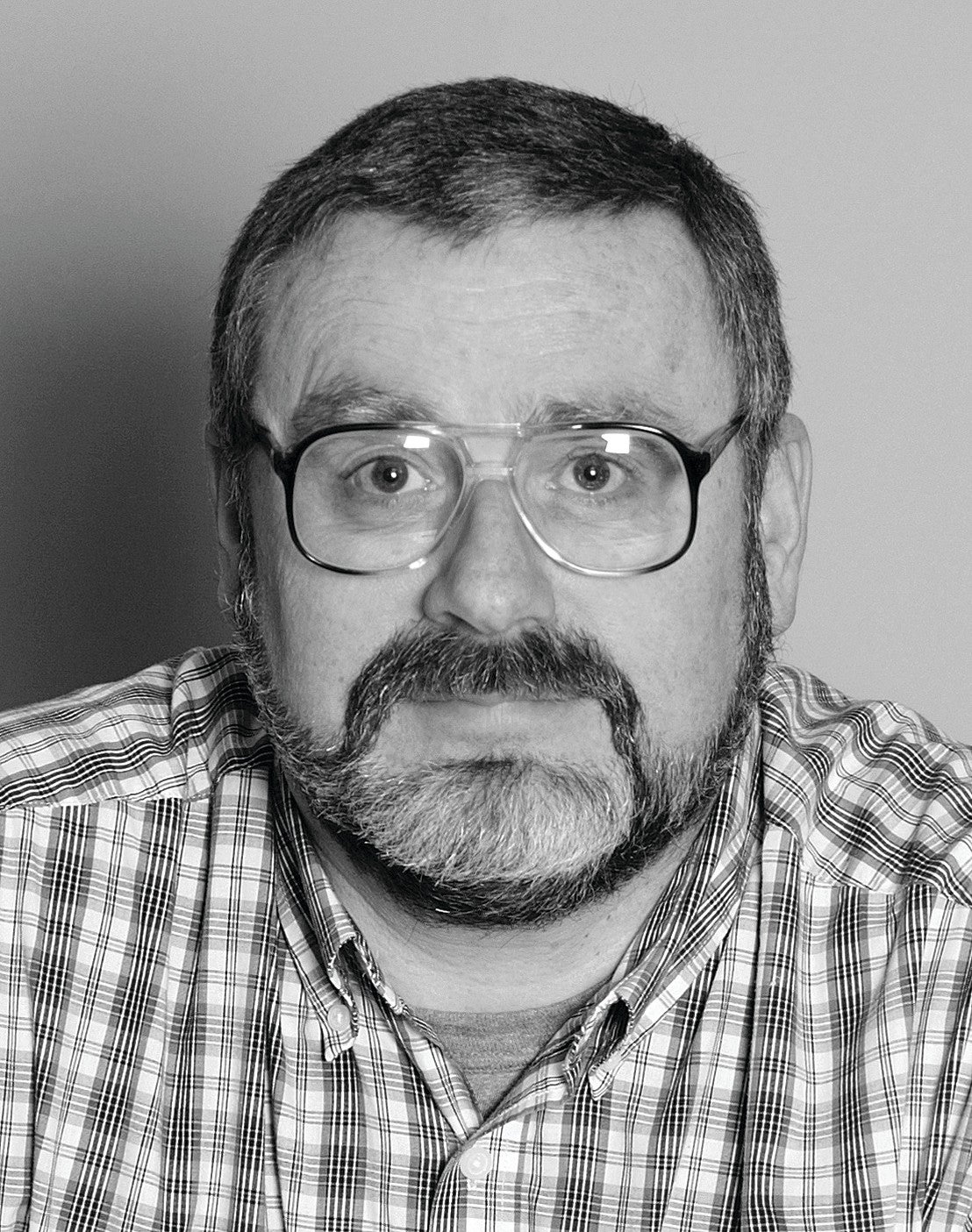