Let There Be Light, Heat and Storage
Perhaps the most obvious aspect of the workshop environment is lighting.
Perhaps the most obvious aspect of the workshop environment is lighting. What’s not quite as obvious is that light is not a steady stream. It arrives in very close waves that, like the frames in an old movie, are so frequent they seem uninterrupted.
The color of light depends on the gaps between the crests of those individual waves. If the gaps are larger, the light appears red, orange or yellow. This is the warm end of the spectrum. Wavelengths in the middle are green and blue, and those with the shortest intermissions start trending back toward what humans think of as warm. They appear as indigo (purple) and then violet (a pinkish hue).
Seeing the light
People can only see a small number of wavelengths, and the light we do see is called visible light. By changing the types of bulbs that we use, or the temperature of those bulbs, we can change the visible light in the woodshop from warm (reddish yellow) to daylight (a colder blue). The temperature is usually stamped on the bulb or the packet it came in, and it’s not the familiar Fahrenheit or Celsius. Those are not baseline scales (they can travel below zero and go on forever, theoretically). Light is measured using something called the Kelvin scale, which has a baseline. In the case of light, that baseline is the absence of light, which is black. The Kelvin scale measures temperatures, which makes sense because light is either warm or cold, or somewhere in between. The range runs from 1000 to 10000, and the whitest, most neutral spot on the scale is 5500.
From that one might assume that the best color for light in a woodshop would be 5500 K, right? Well, that’s a pretty good starting point, and it’s very close to the average color of natural daylight. So, if we select boards for color and clearcoat them, the color we see in the shop is going to be very close to the color that the furniture will appear outside at noon on a nice, bright day. At noon, the light is called vertical daylight, and its temperature is usually in a range from 5500 to 6000 K.
Unfortunately, light is fickle and that’s why there is a range. It changes if it is absorbed by dark matte surfaces that don’t reflect it. Daylight also changes depending on where we are on the globe and the time of day, both of which alter the angle between a specific geographical location and the sun. It changes depending on how light is refracted by the moisture content of the atmosphere. Photographers prefer overcast days to bright sunshine because the light is less intense. On very bright days, light reflects more and produces sharper edges, and of course, larger and more well-defined shadows.
The best light color at the workbench is going to lie somewhere between 4500 and 5500 K. In the finishing room, somewhere close to 5800 K is going to produce the truest colors. That difference is because people prefer a slightly warmer range of colors. In our bedrooms and living rooms we tend to use soft or warm white bulbs (2500 to 3000 K), which is where we’re most relaxed. That range is a bit too warm to encourage energetic work, and a bit too red to judge finishes.
There’s an adage that says, “better light, better work”, and there’s quite a bit of truth in that. The volume of light obviously makes a huge difference, but so does the direction. A workspace needs overhead or saturating light, but it also needs concentrated local or task lighting. For example, woodworkers use a raking light shining across a board to reveal pits, scratches and blemishes that an overhead light won’t illuminate, because the raked light creates shadows that can exaggerate the size of the flaws and make them more visible.
We are spoiled for choice nowadays when it comes to bulbs. We have LEDs, fluorescents, incandescent, halogens and even sodium lamps in large buildings, to mention a few options.
Incandescent bulbs are disappearing because they are very inefficient, require a gas such as argon inside the globe, and create a lot of heat. Both standard and compact fluorescent bulbs are cheap to run but their light can be harsh and greenish (you’ve probably seen the green show up in photographs). Plus, fluorescent bulbs that contain mercury vapor are potentially toxic if they break. Halogens are energy efficient, but they can get very hot, so the best place to use them might be on a patio rather than in a shop with fine dust.
LEDs seem to be the wave of the future. They’re inexpensive to use, easy to control and tune for color, and available as programmable smart bulbs. They last a long, long time and aren’t slow to start if the shop gets cold. They don’t radiate much heat (although they do produce a little), and they operate on low voltage. LEDs don’t care how frequently they get switched on or off, and they are easy to direct at tasks. For shops with a big light bill, LEDs are usually a great option.
Too hot to trot
The temperature of light can affect work, but so can the temperature of air. Warm air retains moisture better than cold air, so temperatures are related to humidity. And as every woodworker knows, wood is almost as responsive to moisture content as we are.
In northern climates, heat is an issue and the biggest challenge with that is make-up air. That’s especially crucial in spray booths, where the whole function is to expel warm, contaminated air. There are spark-free air replacement systems for spray booths that provide heated air that equals the exhausted air, and some of them can even be used to bake finishes. Depending on the size of the booth and the outside temperature, the units can run anywhere from $1,000, such as the Fantech MUAH 10/12, to more than $25,000. Electric units can be expensive to run, so another option might be to add a solar heater to the south wall of the shop. One way to do that is to install windows and a trombe wall that uses no fan, so there’s no spark. Shops with solar kilns often ‘steal’ some heat from the kiln to keep the spray booth warm, especially if they’re not cycling the kiln when they’re spraying coatings. There seems to be universal agreement among economists that energy prices will continue to rise while the world switches from fossil fuels to renewables, so an alternate energy solution for make-up air could be quite timely.
In southern locations, the challenge is cooling air to reduce humidity. The most comfortable indoor relative humidity is about 40 percent. High moisture levels can play havoc with wood movement, freshly sprayed coatings, and hard-working employees. We’ve all heard that the problem is not the heat, it’s the humidity. Unfortunately, dehumidifiers cost almost as much as air conditioners to run, with the added downside that they don’t exhaust the hot air. It’s a lot less expensive to run fans than air conditioners, so placing lots of them strategically around workbenches and the most-used machines can make a considerable difference in the workshop environment. Opening the shop at night and closing it during daylight hours can help with the power bill, too. If it’s not a security issue, have a fan in one window blowing air in at night and another in an opposite wall sucking it out. Rock salt can absorb some moisture from the air, as can calcium chloride (as in Damp Rid), and these desiccants will work surprisingly well in smaller spaces such as offices and breakrooms. Put plants outside during the summer months, if possible, as they add moisture to the indoor air.
Storing and moving
Robots are increasingly being used to pick parts, load and unload machining centers, and stack components on pallets and carts. But the reality is that most shops will be doing these tasks manually for a while yet. There are several steps a small shop can take to enhance this aspect of the workshop environment.
Components and parts such as fasteners and hardware can be stored as close as possible to the location where they will be used. Rather than stashing everything in a storeroom, most materials can be inventoried under workbenches or on rolling carts. This saves steps, time and money.
It can be a good idea to break down boxes and pallets of supplies into smaller units as soon as they arrive at the facility. Some woodshops decant cartons into smaller baskets that are uniform in size and easy to lift and stack.
One of the least expensive ways to raise materials (especially sheet goods) to a height where they can be slid onto a CNC is to use a hand-cranked mechanical scissors lift. The same carts might be usable as assembly tables too, as they can be raised or lowered quickly and easily for employees of different heights – even between shifts.
A good budget compromise between lifting sheets manually and installing a fully automated loading/unloading system is a vacuum lift. These are basically big vacuums that suck up a sheet of plywood, MDF or melamine and let the operator move and place it with controls that look like a bicycle handlebar.
But perhaps the most effective, and least expensive material handling enhancement is to remind employees once or twice a year how to lift properly with their legs rather than their backs, and to check the dust collection filters daily to keep fines out of the air in the shop.
This article was originally published in the December 2022 issue.
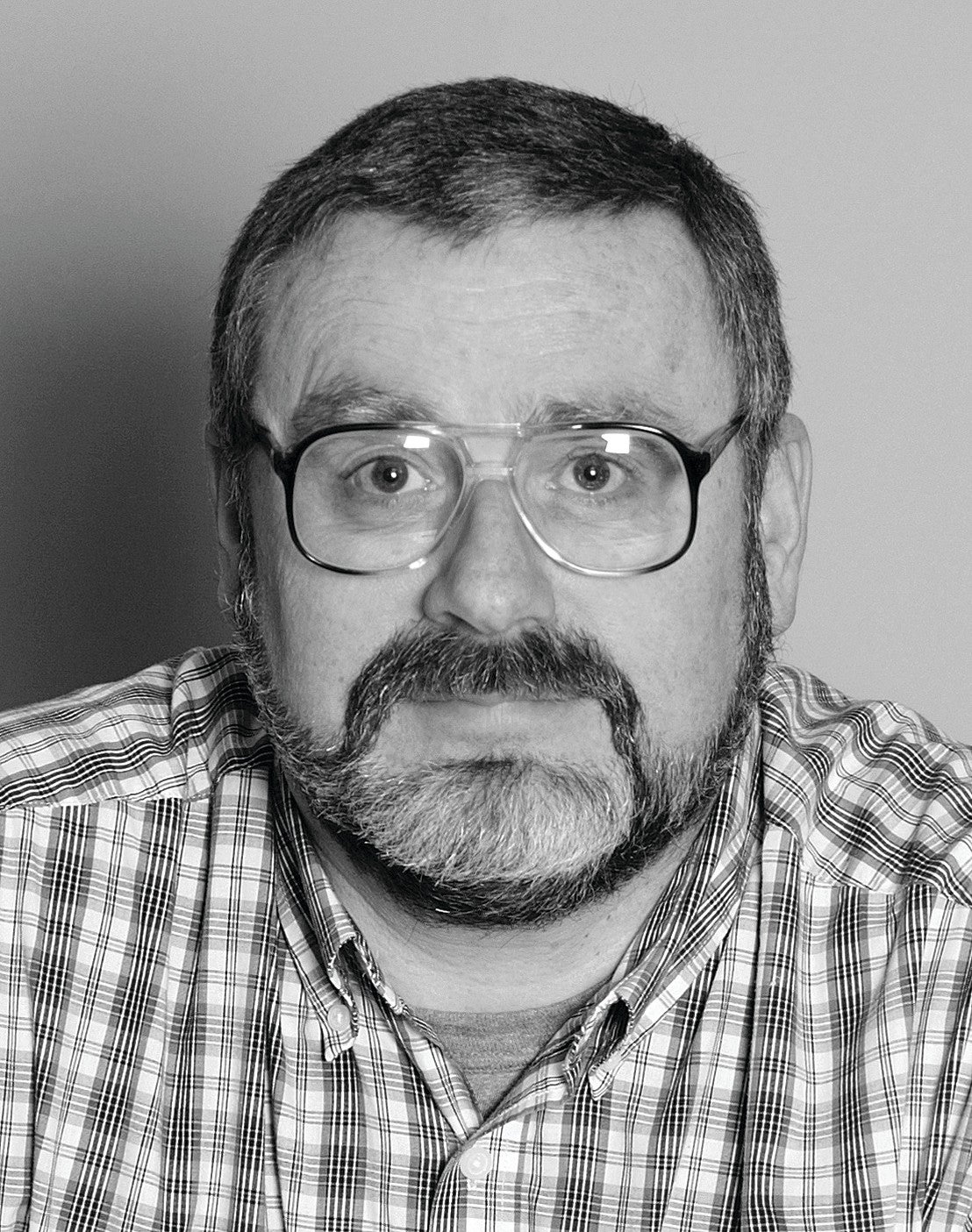