Making it all Better
Products and thoughts for tackling dust, moving materials, and working with better light in the shop.
Quality and speed are watchwords for a successful woodshop. Several elements play a role in meeting those goals, and some can be tweaked more easily than others to deliver immediate rewards.
Among the least expensive and most effective shop upgrades are those related to a cleaner environment, more efficient traffic through the shop, and higher visibility at workstations.
Better Dust Control
Fine dust is a challenge in every shop. And while health is by far the greatest concern, woodshop dust also has many other negative effects that waste both money and time. The solution is to catch it where it’s born.
Woodshops create dust by either cutting or abrading. Cutting happens at saws, shapers, CNC routers, molders, drill presses – anywhere the shape of a part is changed. Abrasion occurs with portable sanders at the workbench, or with stationary profile machines and wide belt sanders, or during the finishing process as we sand between coats. Cutting produces fewer fine (small) and more gross (big) particles than abrading. The gross particles tend to settle close to the source, while the fines like to travel. Any air movement will carry them, and the causes can be anything from an open loading bay door to forced air heating and air conditioning, or ceiling fans, or even just employees and parts moving around the shop.
There is a very efficient way to grab those fines.
We’ve all heard the word HEPA, but many of us don’t quite understand it. According to the U.S. Department of Energy, it’s an acronym for the phrase High Efficiency Particulate Air, and it describes the effectiveness of a certain type of pleated air filter. The government isn’t kidding about that high efficiency: HEPA filters can remove at least 99.97 percent of airborne dust particles that measure 0.3 microns (µm). And particles that are larger or smaller than that are trapped with even greater efficiency. The 0.3 µm number is essentially a baseline that describes the most common size of particle. A micron, by the way, is one millionth of a meter. Good eyes might be able to see a speck of dust that is about 25 µm.
The National Institutes of Health ran some tests on wood dust and discovered that the majority of common wood dust particles are pretty sizeable, at more than 10 μm in size. That’s 30 times as large as the most common fines that HEPA filters remove. The tests did reveal that smaller particles that are still several μm in diameter can be produced when wood is sanded with fine sandpaper. But the bottom line here is that we’re looking at fairly large dust particles in the air in a woodshop. And a HEPA filter will catch them if there’s enough airflow.
Here’s another funny word, MERV. This one stands for Minimum Efficiency Reporting Values, and it’s used to describe a filter’s ability to trap those large particles (the ones between 0.3 μm and 10 μm). MERV ratings for dust filters range from 1 to 16, and the bigger the number the better. So, switching to HEPA high MERV rating filters should immediately improve the air quality and reduce the amount of ambient dust in a woodshop. But before doing so, it’s essential to vacuum out every crevice, corner and possible hiding place for dust, or you’ll just keep moving it around. One area that many woodworkers fail to clean properly is on top of the ductwork.
Some machines are harder to set up for efficient dust collection than others. Many cabinet saws have poor collection because they have a single 4” hose attached to the base halfway up the cabinet, and no topside collection at all. Catching debris at the blade will greatly improve the machine’s performance, and the best way to do that is with an arm that delivers a hose to the blade guard housing. Another idea is to install a compressed air nozzle inside the saw base and run a little air through the compartment when that 4” hose is working. The compressed air can make the dust airborne, which makes it a lot easier for the large hose to collect it.
If the dust inlet is appropriate and a collector still isn’t quite gathering all the available debris, the problem is either velocity or volume. Velocity is the speed at which the air is moving through the ductwork (about 3,800 fpm is recommended), and volume is measured by the number of cubic feet of air that pass by any one point in the system. If one of these values and the diameter of the ductwork are known, the other can be calculated. For example, a standard 4” duct in a small shop has a cross section of about 0.09 sq. ft. (the area of a 4” circle). If a small dust collector is rated at 350 cfm, then the speed of the air is 3,888 fpm. That’s determined by dividing 350 by 0.09. This speed would slightly exceed the recommended velocity for scooping up all the fine and coarse debris.
The problem is that the longer the ductwork, the lower the volume. Simply adding a bigger collector will probably not solve the problem, because the existing ductwork can only accommodate so much volume. The least expensive option is to divide the load – install a second collector, and then separate and seal the existing ductwork so that each unit serves about half the machines. Or, if the shop is growing, a larger collector with new and larger ductwork might be worth exploring (see the resources section below).
The key to a cleaner shop is to collect dust as close as possible to the point where it’s generated. For abrading (sanding), volume is more important than velocity as the dust distribution pattern is usually quite wide. For cutting, velocity is key as the debris is generated at a small, specific point such as a router bit. So, the hose and hood need to be wider and pulled back a bit for sanding, and smaller and placed as close as possible for cutting.
Better Materials Handling
Bottlenecks might be annoying on a highway, but they’re downright costly in a woodshop. Intelligent and well-planned handling of materials (parts, components, raw product) as they travel through the manufacturing process can reduce and often eliminate bottlenecks that hold up jobs or cause delays in delivery and installation.
The first step is to know where everything is, and many CAD design programs now offer inventory modules that are well worth the price. This software can do things such as letting a cabinetmaker on the shop floor know if there’s a partial sheet available that will deliver the panel he needs, and then tell him where it’s located. Compare that to physically searching through bins or sheet storage racks every time a cut needs to be made.
Moving larger parts and sheet stock through the shop can be a challenge. Saw Trax (sawtrax.com) makes a series of very clever carts that are highly maneuverable. They can carry large and heavy loads on a combination of pneumatic tires and casters.
A lot of smaller woodshops have decided not to automate the panel reduction process by adding a CNC router. They either use traditional machines such as table or panel saws, or they outsource the parts. But there is one area of the production process that is relatively easy to automate and can be done on a sensible budget. Cutting parts to length, such as stiles, rails and drawer fronts, involves an element of repetition that is easy to harness with a cut-off system such as TigerStop (tigerstop.com).
The company’s SawGear and new SawGear Touch are simple and intuitive automated stops that are very accurate and easily attach to an existing miter saw. They can remember several parts, and the stop automatically moves along the fence to make different cuts.
The biggest bottleneck in most shops is at the finishing booth. Handling doors, drawers and even completed cases can be awkward at best and becomes even more challenging when the parts are wet. PaintLine (thepaintline.com) and Guffey Systems (guffeysystems.com) offer spraying and drying systems that can speed up the process and reduce defects and reworking.
The latest way to speed up traffic through the shop is to employ robotic arms that have become surprisingly affordable and very sophisticated over the past few years. These collaborative robots (cobots) can move, sort and stack parts; run small routers and saws; spray coatings; sand and shape parts; and even do some quality control inspections.
Better Lighting
The better the light, the better the work. This old adage has its roots in candles and gaslights, but it’s as true today as it was back then. The brighter and more neutral the work lighting is, the better people on the shop floor can see details and anomalies. That lets them produce more defect-free work.
Bright is easy: just add wattage. Neutral is a little more complex. It’s a subjective term, because light runs along a spectrum from warm yellows and reds to cold blues and greens. One might assume that white is neutral but even daylight isn’t white, and it changes by the minute.
There’s a scale for determining the color of light, and it’s based on temperature. Known as the Kelvin scale, it measures daylight at somewhere between 5500k and 6500k. We like our homes and offices to feel welcoming, so most indoor lighting is in a warmer (lower) range. LEDs generally start at a warm 2700k and can be as high as a cool 5000k. This is important in a woodshop, especially when it comes to the colors of coated wood species, foil, or plastic laminates because they all look different at different light temperatures. The starkness of 5000k in the woodshop will show blemishes, but when a cabinet or counter is installed in a home that has warmer lighting, it may look quite different. So, it’s a good idea to bring finished samples to the jobsite before building, just to see how things look under those lights.
It’s hard to argue with the notion of upgrading all the bulbs in a woodshop to LEDs. For a start, they are far more energy efficient than fluorescent, sodium, or incandescent bulbs, which were banned for sale and production in the U.S. in August. They also have a much, much longer lifespan. LEDs are brighter and more intense than other lighting, but they still need to be evaluated onsite. The height of the ceilings, the square footage and direction of windows, the shop’s winter and summer temperature ranges, and other factors such as colors in the room all come into play.
Tresco Lighting (trescolighting.com) offers an LED aluminum extrusion called Infinex that lets the woodworker place task lighting at the optimum location. Infinex can be cut to fit under hoods, on beams, or anywhere else on a machine or workbench where the dimensions are important.
Dust Control Resources
Shop owners who wish to learn more about designing an efficient dust control system should visit the website of Air Handling Systems (airhand.com). Oneida Air Systems (oneida-air.com) also offers design help for woodshops, and Nordfab Ducting (nordfabductwork.com) provides a range of fittings. U.S. Duct (us-duct.com) has free 3D ductwork design and quoting software.
To learn more about the danger of combustible and explosive dust, visit an article in Hose & Coupling World by Rodd Blanford of Masterduct Antistatic Industrial Hoses at hose-coupling-world.com. For shops that are ready to move up to a baghouse, David Wick and his team at Scientific Dust Collectors (scientificdustcollectors.com) can explain why a venturi isn’t the only option. American Fabric Filter (americanfabricfilter.com) specializes in filter bags for small collectors and baghouses and offers custom solutions for tricky spaces such as low ceilings. Another supplier, DustCollectionBags.com, also offers a wide range of plastic collection bags.
This article was originally published in the December 2023 issue.
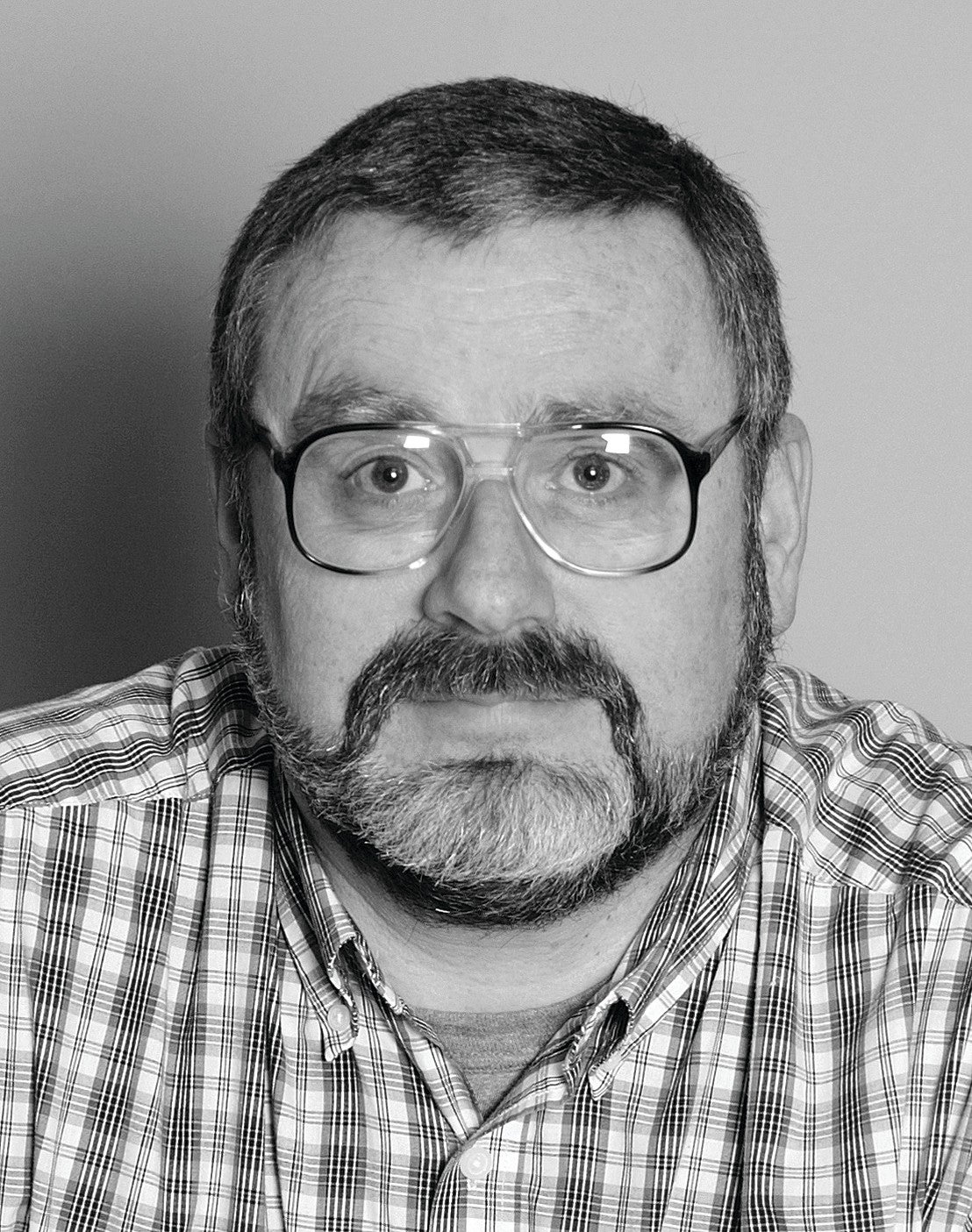