Measuring up
Laser templating tools save time, increase accuracy and improve quality
There’s an old joke about a kid on a jobsite who complained that he couldn’t stand the 90-degree heat. One of the old carpenters told him to go stand in a corner. When the kid asked why, he was told that there’s never been a corner built yet that was even close to 90 degrees.
Anyone who has worked on settled buildings or followed a lazy framer knows how true that is. Harvesting the dimensions of a room for cabinets when the floors aren’t level, and the trim isn’t plumb can be a challenge. It’s hard to be exact when nothing is square, but it is critical. Recording measurements correctly can save a lot of time later, during both manufacturing and installation. When the production crew can build with precise dimensions, there are fewer fill strips, coping cuts and wedges required on the jobsite.
Laser templating (also called digital templating) started out as a way of measuring for countertops, and it didn’t take long to figure out that the system works just as well for the boxes beneath them. It was a little cumbersome initially, but technology has caught up with the industry’s needs. Jobs can now be measured onsite with the results popping up instantly on a screen back at the shop. The CAD designer can ask an employee to measure (or re-measure!) windows, walls, doors, and ceiling heights in real time, and as the room’s dimensions change, some libraries can even switch cabinets automatically.
Why buy?
There are three main considerations for a woodshop owner who is looking at adding the ability to use laser templates – cost, quality, and time.
When it comes to cost, templating tools are reasonably priced. They can also help save money if they prevent a lot of reworking. Even though it probably doesn’t take a whole lot longer to physically record a space with a tape measure and a notepad, the laser does remove many opportunities for human error. It also cuts down on the time spent inputting data from handwritten notes on a keyboard, but it probably won’t eliminate manual input entirely, even on the most automated systems. Anyone who uses a templating system knows that they often require at least some tweaking. The bottom line is that templating almost always makes sense from a budget viewpoint if the woodshop is building more than a couple of kitchens a year.
The quality issue might be more important. As with most technology, quality can be enhanced when using a laser templating system. Think about trying to see where the tape bends into the corner between the wall and ceiling, or perhaps using a level and a straightedge to determine the drop in the floor between two corners. Sure, an experienced woodworker will be very close, but a laser can be accurate to three decimal spaces, if needed. Precise measurements lead to better lines. There are fewer gaps, better and tighter joints, less fudging and a more seamless installation. It’s that 1 percent thing. The guy who builds the kitchen always has the feeling that it’s great, but he could have done just a tiny bit better. Templating won’t ever eliminate that feeling because we’re human, but it finetunes things and reduces it.
Time is a big consideration. Setting up a laser can take a few minutes, and training on one can be a little time-consuming. But after that, the beam shoots and then records instantly. Laser measurement speeds up the job, especially with practice. It doesn’t take long for the layout person to figure out what parts of a job need the most attention, and what can be done quickly. And sending a digital file is a whole lot less time-consuming and more accurate than making plywood or cardboard templates.
How does it work?
Basically, templating systems use a laser to measure from a fixed point in a room and the dimensions are recorded, stored, used to make a 3D drawing, and most are exported directly into a CAD system. That allows the kitchen designer to use the drawings as a template for adding custom made cabinetry, or to import stock units from a library of boxes supplied by an outsourcing cabinet supplier.
The laser is usually set up on a tripod and the operator points the beam at several spots on the walls, ceiling, and floor, and takes a reading at each. That allows the software to begin drawing the three-dimensional map of the space. The first couple of readings are used to establish a base line that is level, so any deviation in the floor or ceiling height can then be recorded as a distance from this base. The outside dimensions of features such as corners, existing doorways, cabinets, trim, window openings, HVAC and electrical fixtures, lighting, and crown moldings can all be added by simply recording critical points such as the edges of the light fixtures or cabinets.
The more readings, the more detailed and accurate the drawing becomes. Well, to a point. For example, taking several readings along a straight wall can be a waste of time as the software only needs two endpoints to create a path. However, woodworkers know that there is no such thing as a straight wall, so most of us will take a reading about every 16” along a wall because that should catch any undulations that were caused by the stud spacing.
If the shop owner can train an estimator (who may well be himself) to use a laser and a touchscreen properly, all the dimensions that will be needed for the actual build can be harvested during the initial visit when the bid is done. That can save a lot of time, because it eliminates repeat visits, and it also provides all the data to generate files that can be used in CAD and CAM applications. The estimator can even record details such as the profile of an existing molding or a raised panel if those are going to be needed to be matched for production.
All the measurements can be saved on a laptop, tablet, memory stick or even a phone, depending on which software and hardware package is being used. Before investing in a laser template system, it’s a good idea to check with the publisher of the shop’s CAD program, as well as the sales department at any outsourcing supplier, to see whether certain products will work seamlessly with the drawing program and available libraries.
Which one?
DeWalt and Bosch Tools offer a wide selection of laser measurement devices. Many of these products can be married to apps, software solutions, tripods and targets to create a cabinet templating system.
The Leica DISTO is one of the better-known templating lasers. It’s a small device that can connect to apps that organize and share measurements. The native DISTO Plan app comes free with the laser, and DISTOs also work with specialty apps that are designed for cabinetmakers and designers/architects. They’re easy to fit on a tripod, and they work with most brands of smartphones, tablets, and laptops. There are several models in a wide range of pricing, so it will take a little time to research. Shops using Hexagon’s CabinetVision software will be interested to know that Hexagon also owns Leica, so there’s a utility available that combines the two.
Advanced Dimensions in Unadilla, N.Y., is a DISTO distributer that is a division of Dirig Design. The parent company is a drafting service in commercial and residential millwork, so the staff is very familiar with shop drawings and cabinet production.
ELaser Pro 3D by ETemplate Systems is an award-winning option that combines the company’s Measure Manager software with Leica laser heads that are custom designed for measuring 2D and 3D projects.
The LT-2D3D Laser Templator from LPI is a whole system that only takes a few minutes to set up and it can rotate virtually 360 degrees for optimal coverage and accuracy. The accompanying software is designed to be extremely intuitive, so CAD experience is not required. It will send photos, estimates and even CNC-ready files directly from the jobsite. And it can template horizontal and vertical subjects including full-height backsplashes, fireplaces, showers and more.
Some options may take a little customizing for the average woodshop. For example, Prodim originally developed its Proliner laser measuring system specifically for the door industry. And the PhotoTop 5 system from Minnesota based Fabricator’s Choice is primarily aimed at stone and solid surface countertop fabricators.
The way that a shop operates has a lot to do with why and how it should add laser templating to its toolbox. Shops that buy in most of their casework from an outsourced supplier might want to spend some time talking to the CAD designer at that factory before investing in a specific laser system. The two big questions to ask are whether the supplier can work with imported files (the drawings of the bare rooms), and if the shop can access the supplier’s library of cabinets, accessories, and hardware.
Woodshops that are part of a larger construction company may already have a division that is using this technology for framing and estimating. Owners of smaller shops may want to consult with their countertop supplier.
This article was originally published in the August 2022 issue.
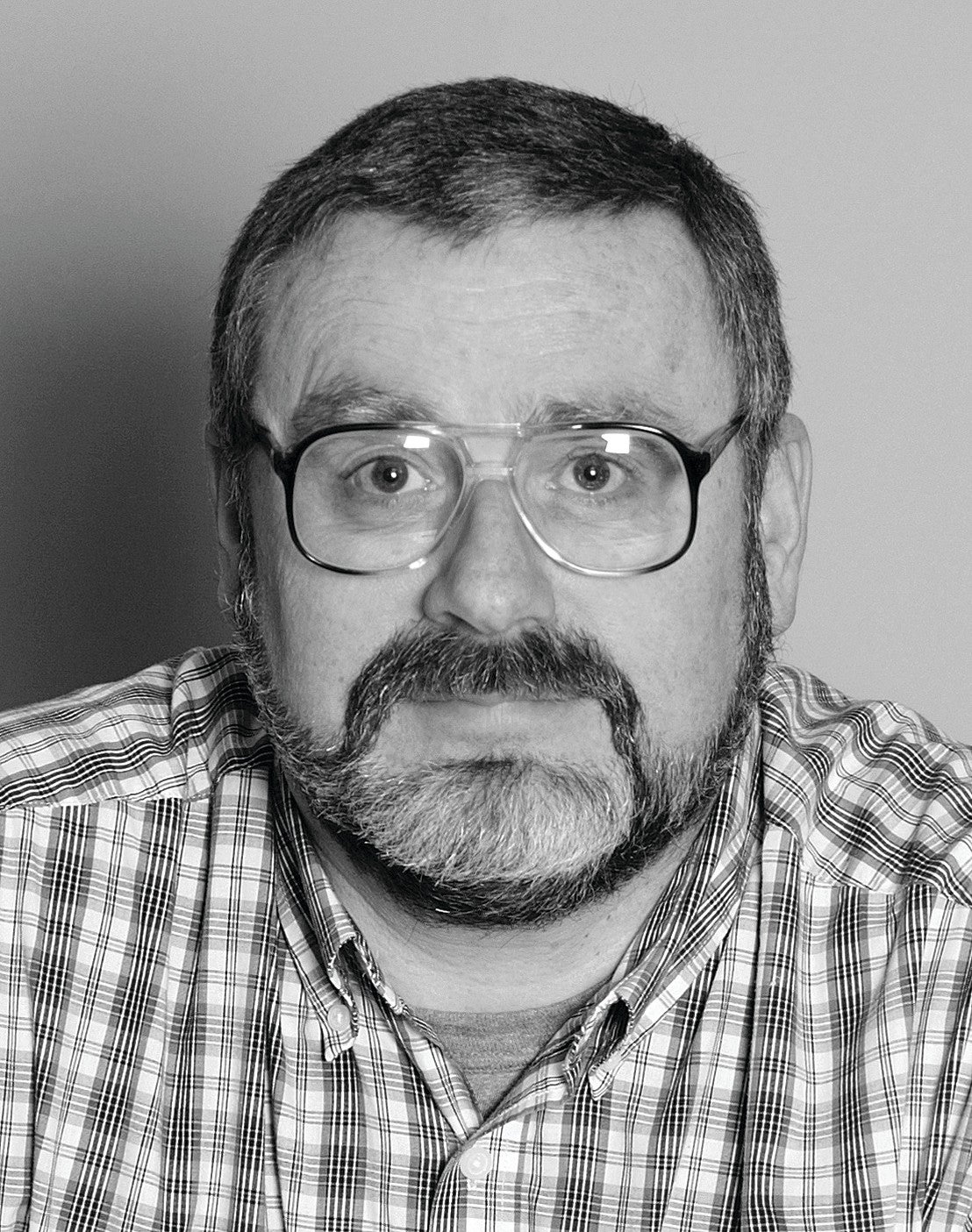