One Piece at a Time
There are many options for a shop to upgrade its digital fabrication equipment rather than replacing it.
Back in the 1970s, Johnny Cash had a hit song called “One Piece at a Time”. The song is about an assembly line worker in a Cadillac factory who stole enough parts over the years to build himself a complete car. Before he became a country singer, Cash had actually worked at a car factory in Detroit. While we’re not recommending that employees at CNC manufacturing facilities follow his example, it is possible – and often advisable – to update many aspects of an older router rather than replacing the entire machine. A shop can bring it up to date, one piece at a time.
Adding options and upgrading elements such as the control panel, servo motors, spindle, vacuum table and toolholders all represent substantial investments. They make sense when the CNC is large enough to handle the tasks being set for it, and rugged enough to go another hundred thousand miles. Size refers to both the bed and the travel, both of which need to be able to accommodate the kinds of work the shop now handles. While the cost of a new machine has certainly come down a bit over the years, the basic form (essentially, the parts that don’t move) hasn’t changed much. But almost everything that does move has evolved, and some components have come a long, long way.
Along with building brand new, state-of-the-art systems, Indiana-based Thermwood (thermwood.com) has been rebuilding and upgrading CNC routers for several decades. The company explains that “the process of upgrading a CNC router will vary with [the] extent of the upgrade. If the control system and drives are being replaced, the machine may need to be shipped to Thermwood for the work to be performed. If a Universal Vacuum Table is being added, the components can be shipped to the customer, who can generally install [them] without additional help. When the machine is shipped to Thermwood for control and drive replacement, we can laser calibrate each axis. In many cases this results in a machine which is more accurate than when it was new.”
Keeping control
The heart and soul of many CNC upgrades is the control panel. A good example of what’s possible here is the newest Anderson America (andersonamerica.com) panel, which the company calls the Anderson Group Machine Virtual Panel, or AGMVP. It can easily and quickly load programs or worklists from a local disk, a removable storage device or online Cloud storage, using a familiar Windows interface. AGMVP runs on Windows 10 or Windows 7 and is compatible with Fanuc’s Oi-Model F and Fanuc 31i control systems.
CNC routers that include automated loading or automatic off-loading pusher/sweeper devices can now include Anderson’s WorkList software that offers better production and workflow management. Using it, lists of individual program files can be loaded all at once and executed sequentially, with on-screen status, sheet count and countdown functions. The tool lengths, diameters, locations and number offsets are easy to set up, review and change. When combined with a standard automatic tool length measurement device, mistakes and crashes are minimized, and often eliminated. The operator can also graphically see and control the status of vacuum zones, working fields, and even twin tables or additional peripherals, plus spindles and heads such as multi-drill blocks. The software also makes it easy to visually inspect, verify, and quickly edit tool diameter compensation and G54-G59 work coordinates. There are 48 extended work coordinates on 3- and 4-axis machines, and 200 on 5-axis machines. Plus, the operator can configure custom buttons for commonly repeated functions or programs such as facing a spoil board or fixture, routine maintenance or cleaning, spindle warm up, and start-up or shut-down procedures.
Given the nature of this technology, it’s no surprise that most CNC manufacturers offer occasional control panel upgrades. For example, woodshops with a Techno LC Series, RG, Pro Series, Gantry III, Patriot or Servo DaVinci machine can now upgrade their controller to a version that has no PCI card requirements or short SCSI cables. The new panel is compatible with Windows 8 and higher, includes a real-time preview and has a real-time 3D toolpath display and G-code listing view. The company (technocnc.com) says it’s “a simple package and an easy upgrade”.
Innovation for small shops
NextWave Automation (nextwaveautomation.com) caters to smaller shops and prototype builders. While some of its machines work well for short-run production, their real value lies in their versatility. They don’t require a great investment, and they can be almost endlessly upgraded to meet new challenges. Among the company’s more recent innovations are a mini fourth axis system that runs about $500; 2- and 7-watt laser modules that turn CNC routers into engravers; a Plexiglas and aluminum machine enclosure that enhances safety, reduces dust and minimizes machine noise; and the 3D Digital Duplicator that attaches to the router and traces objects down to 0.001” detail, allowing the user to import image data for replicating objects, shapes and patterns.
Legacy Woodworking Machinery (lwmcnc.com) has added two new table sizes to its Maverick machine. The Maverick allows a woodworker to instantly move from 3-axis machining to 5-axis turning to 4-axis vertical machining, and it’s now available in both 3x5 and 4x8 models.
Woodworkers often think of C.R. Onsrud (cronsrud.com) as an industrial-scale CNC manufacturer. And indeed it is, with machines placed in some of the largest manufacturing facilities around the world. But the North Carolina company also caters to small- and medium-sized shops, offering them a tailor-made solution rather than an off-the-shelf, stock machine. The entry-level M Series, for example, boasts rigid frame construction, highly responsive drive mechanisms, and many more of the top-end features one might expect to find on bigger models. The idea here is that this moving gantry machine can grow along with a shop’s requirements, making it a viable option for a smaller new work cell.
Komo Machine (komo.com) in Lakewood, N.J. offers several series of CNCs, among which is the Flex. They come in moving single table, twin table or moving gantry configurations, and all feature a side-mounted tool changer. And they come with a lot of optional upgrades, including a tooling package, vacuum pumps, boring blocks, aggregate heads, automatic material handling, a dual screen, mist cooling, a C axis for aggregates, and an aluminum table with a universal grid and integrated pop-up roller balls.
Safety concerns
Felder Group’s safeSpace (felder-group.com) is essentially an office cubicle for a CNC. Designed to work with the company’s H350, H300 and H200 machining centers, it “massively” increases working safety, according to Felder. The safeSpace has a large monitor on the outside that delivers an immediate status overview as jobs are being processed. A 10’ wide door makes loading and unloading easy, and huge windows in the door let the operate see what’s going on inside.
Holding parts on the worktable securely and safely has come a long way, too, and this is one of the easier facets of CNC milling to upgrade. For example, Busch LLC (buschvacuum.com) in Virginia Beach, Va. offers the energy-efficient and low-maintenance Mink claw vacuum pumps, which are used for clamping components for processing. And Better Vacuum Cups in Chino Hills, Calif. is constantly updating its catalog of vacuum cups for both standard and nested based router tables.
Most manufacturers offer a range of options when it comes to clamping. A good example is Weinig’s Holz-Her division (holzherusa.com) which publishes a handy chart on its panel processing webpage that lists all of the options for its Nextec CNC machines, including workpiece clamping. The chart also lists tool changers, drilling heads and a host of other choices available, even software packages.
Perhaps the most encouraging, and certainly the most exciting innovation in woodworking over the past five years has been the evolution of robots. Biesse (biesse.com) has developed the Robotically Operated System (ROS), which is a perfect example of how robots can upgrade CNC operations. These incredibly versatile, fluid and strong robotic arms can customize loading and unloading cells, and be seamlessly integrated with CNC, sizing, boring, edgebanding and sanding machines. They make a work cell more efficient, more productive and less likely to have problems, while at the same time reducing idle time and the risk of material damage. Thanks to their compact size, strength and ability to turn and twist, they can move and rotate panels and thereby automate the machine loading/unloading processes. That frees the operators to carry out other added value tasks.
Change Is good
Few upgrades deliver results as quickly as upgrading the machine’s ability to carry and change tools. Benz Inc. (benztooling.com) has recently updated its options with the Hybrix, a rotating tool carrier magazine with a fixed housing. This is a hybrid of a magazine and a turret, and as such it offers several advantages. For a start, it delivers 30 percent higher power density than a tool turret alone. There are higher limiting speeds (approximately 40 percent), plus more precision and flexibility. On top of that, this upgrade is both cost-effective and space-saving, and even a little more energy efficient. There’s less moving mass when it’s rotating, fewer roller bearings, and any pitch errors are irrelevant. It offers the option of minimum quantity lubrication (MQL) and cooling lubricant (CL) without any restrictions. There’s process optimization, thanks to a high degree of automation, and customer-specific adaptations are possible for shops doing unusual milling. The technology is suitable for all machine types, plus versions in a star (single-row, multi-row) or crown design are possible, according to the company.
Castaly Machinery (castaly-cncmachine.com) in La Puente, Calif. says it “can assist in new product development or modifying an existing machine to suit your custom needs”. A good example is Castaly’s relatively inexpensive rotary axis lathe add-on for a CNC router. This simple to set up component can add lots of new abilities to a small- or medium-sized shop, including the capacity to turn, carve and cut in the round.
ShopBot Tools (shopbottools.com) has just launched the new Desktop Max ATC, which is its larger desktop tool but with an automatic tool changer (ATC). A tool changer can reduce production time by quickly and robotically changing cutters between tool paths, eliminating the need to change and zero tools individually. The Desktop Max has a 36” x 24” work area and is available with an aluminum tool deck or a universal vacuum hold down deck.
CNC operations can also be upgraded by a new take on CAD/CAM, according to the engineers at Cim-Tech. The company’s founders realized that a CNC machine was only as good as a woodworker’s ability to program it. They decided that Computer Integrated Manufacturing (CIM) was needed to bridge the gap between CAD and CAM. CIM provides for a seamless solution with a common interface for design and manufacturing. For example, the Router-CIM program has an all-in-one screen for tool path parameters that is easy to learn, and use. It organizes all of the machining parameters into one easy-to-use interface, which is set up and saved as ‘knowledge’. The information is easily archived and can be transferred from one computer to another. From there, the program offers a number of unique upgrades to standard machining that can be seen at cim-tech.com.
Another great development over the past few years is upgraded service that is possible thanks to advances in other industries, most notably wireless communication. Hendrick Mfg. in Salem, Mass. (hendrickmanufacturing.com) is a prime example. The company offers an array of remote access and diagnostic tools to keep its customers up and running. Its CNC routers and computerized panel saws come standard with technology that allows the Hendrick’s technical team to dial in to a woodshop’s system and troubleshoot, adjust parameters and resolve conflicts from a remote location.
Other considerations
Sometimes upgrading an existing machine isn’t the best way forward, but new stock machines don’t quite check all the boxes either. In that case, a shop might want to look at choosing among the various options to create a custom CNC. Most manufacturers offer this.
For example, Laguna Tools in Irvine, Calif. (lagunatools.com) has created a family of CNCs that run the gamut from desktop to high production, and each machine can be fitted with options to fulfill multiple or very specific applications. The entry-level Swift machines are available with an optional upgrade to a 4-hp quick change spindle and vacuum tables in various sizes, while the top of the line Multi-Tool routers come with the option of multiple heads. That means they can house a router, oscillating knife, tangential knife, Laguna Vision System, creasing wheels, and other upgrades and options.
NewCNC (newcnc.com) offers a customizable package where the shop can configure a table, choose a spindle from 12.6 to 22 hp (HSK 63), configure a changer that handles up to 26 different tools, and include up to a 9-spindle head. Other custom choices might include C-axis, rotary axis, aggregates, and Z axis clearances.
Diversified Machine Systems (dmscncrouters.com) is another very responsive manufacturer that can create a machine that is completely customized to specific needs. Its Freedom Machine Tool division supplies CNC machining solutions in 4x4, 4x8 and 5x10 configurations. Upgrades here include equipping the 4×8 platform with a Rotary Axis CNC Router, which is a perfect tool for a woodworking shop that is looking to expand their capabilities by adding turned components. And an upgrade on the standard 5x10 to a 5x10 Plus offers up to 15” in Z travel, which is made possible by switching out to a heavier and larger bridge.
Shops that are getting into sign making or working with new, thin materials such as foam might want to take a look at Donek Tools’ drag knife (donektools.com). It fits into a CNC router or spindle collet and uses a utility knife blade.
If your upgrade is just to replace a worn-out part with a new one, don’t despair. There are suppliers out there for that, too. For example, Atlantic Machinery in New Milford, Conn. (atlanticmach.com) stocks parts for 17 different CNC brands. And CNC Warehouse in Houston (cnc-warehouse.com) offers a huge parts inventory.
This article originally appeared in the August 2019 issue.
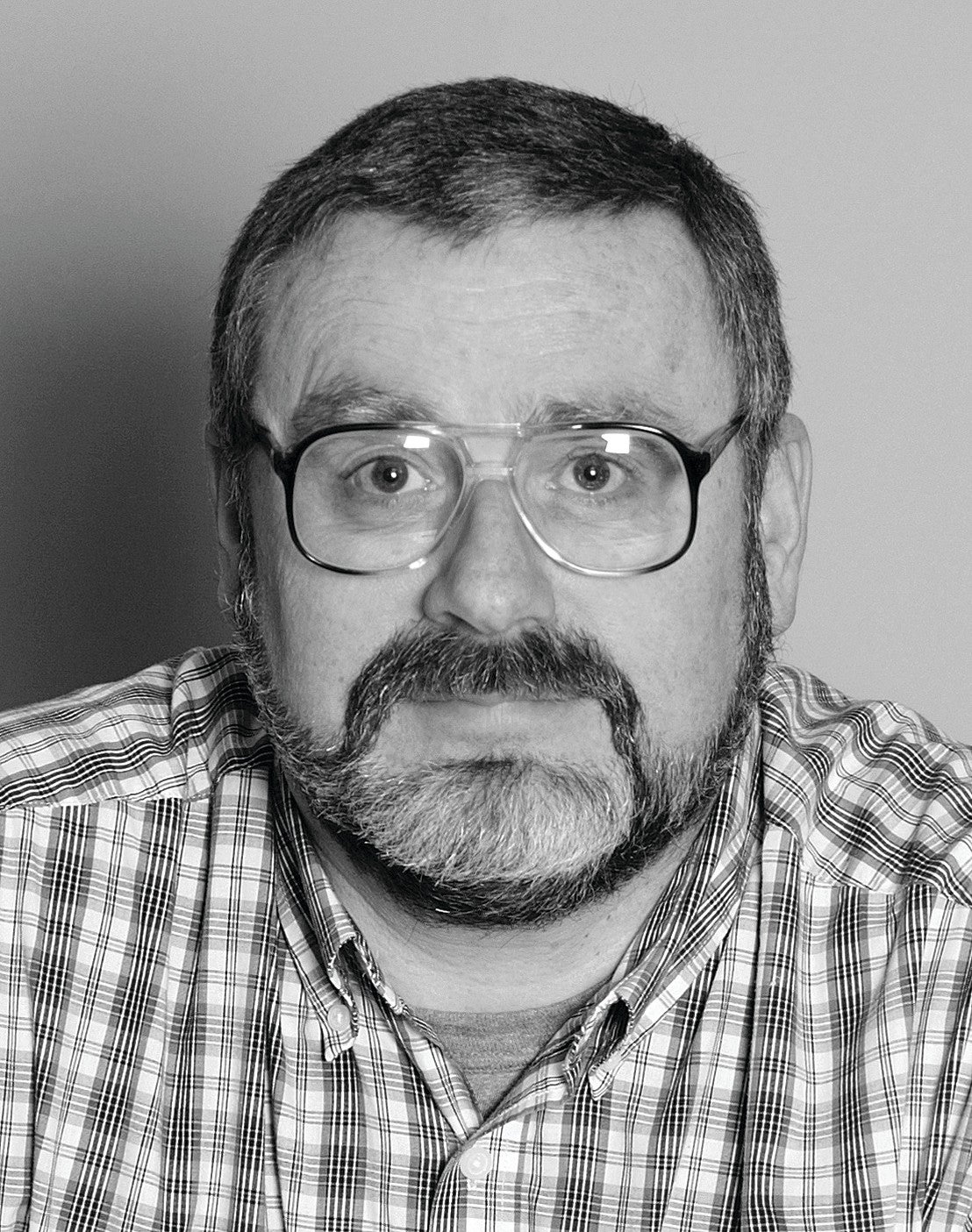