Outsourcing Doors, Drawers and More
The secret to increasing sales and production while lowering costs
Ralph Waldo Emerson once observed that a man who could build a better mousetrap would soon have the world beating a path to his door. It’s a slight misquote, but the essence is valid: higher quality and innovation lead to more sales.
That’s one of the four tenets of outsourcing – the belief that large ‘factory’ shops with lots of machines and skilled employees can make better boxes, doors, and drawers than a small woodshop that is limited in its resources. Outsourcing, the industry gurus tell us, can lead to higher quality. Of course, the word ‘can’ is subjective. Although it’s rare, a careless supplier can ruin a shop’s reputation, so it pays to ask questions and seek recommendations.
The other three tenets are cost savings, more choices, and scheduling advantages.
Buying product from a large supplier can cut costs because the small woodshop then needs to hire fewer employees, make a lower investment in equipment, and buy or lease less physical space.
Outsourcing can expand a custom shop’s catalog by offering peripherals, accents, hardware, species, profiles, and sheet stock that a small business simply can’t afford to inventory.
And outsourcing can expedite jobs through economies of scale that translate into faster turnaround. Projects that used to take months to design, plan and build in-house can now take mere weeks, and sometimes even just a few days to materialize.
Higher quality, cost savings, more choices and predictable delivery may be the cornerstones of outsourcing, but the process is also layered with nuance. Like Emerson’s mousetrap, suppliers are constantly updating and improving options while nibbling away at costs (even in the face of the current supply woes). For example, flat packing allows custom shops to have entire kitchens delivered directly to the customer’s house with lower shipping costs. But it also means there’s a definitive delivery date, so the other subs such as electricians, countertop installers and plumbers can be scheduled with some degree of confidence. That’s important to homeowners and general contractors, and consequently to the custom shop’s reputation.
And when it comes to labor, innovative joinery systems can be paired with CNCs and aggregate heads to build RTA casework that requires very little expertise or time to assemble onsite. Larger shops attend more trade shows and have more salespeople call on them, so they usually hear about new trends and products (hardware, coatings, even software) sooner, and that in turn can keep a small shop more up to date.
There’s nothing static about the wood industry as it responds to higher tech hardware and gadgets, new LED lighting options, the need for sanitary solutions in the face of contagious diseases, style and color trends, and even evolving dimensional norms such as those associated with an aging and shorter, less agile population. Keeping up with industry advances is easier for large corporations, and well-heeled suppliers are also in a better position than small woodshops to deal with issues such as skilled labor shortages and supply chain problems. They can afford the robotics, 5-axis machines and other technologies that can replace lost or unaffordable workers, and the sheer volume of their purchasing power can move them up the supply chain. Manufacturers and distributors know that the bottlenecks will eventually ease, and their biggest customers will remember how they were treated when things were tight. Distributors can’t afford to force outsourcing suppliers to stand in line with small woodshops.
All in one
Full-line manufacturers can supply all the cabinet boxes, doors, drawers, hardware, and accents that a shop could possibly require. A woodshop in essence can become a retail distributor for these companies and use their catalogs and software to reduce its own role to just measuring the space, helping a customer make some design choices, and then installing everything when it arrives. The woodshop can take maximum advantage of all four aspects of buying in: top quality components, cost savings (and perhaps even some short-term financing if a line of credit is established), a vast array of style and finish choices, and a reliable and predictable delivery schedule.
The obvious dilemma here is overreliance. If the supplier has problems, the shop will inherit them. Problems can range from something as simple as a new and less impressive drawer slide screw to complete corporate bankruptcy, so it’s very important to choose a full-line supplier who has a history of success, rather than just going on price. Fortunately, there are many suppliers that build components in North America, and most have been doing it long enough to gain a good deal of respect and a great wealth of knowledge.
One of the most important advantages of working with a large supplier is that company’s ability to spot, understand and move with design trends. That last word, move, is the most important. The supplier must be flexible enough to react to trends before they fade. A small shop can get caught in this trap, where it buys into specific colors or species only to discover that clients have already moved on. Large suppliers can even affect trends because their product reaches so many market segments. But what’s most important to the woodshop is that the supplier is tuned into trends.
A good example of this was an April introduction by Elias Woodwork (eliaswoodwork.com) of several new stain colors and door styles that are a direct reaction to consumer feedback. Over the past few years, nearly everything new in kitchens and baths has been white, plastic, and sanitary – no surprise given what the world has been through. But recent trends have shown an uptake in warm, earthy tones and a return to incorporating wood stain components in kitchen design. This means lighter, neutral stains that show a muted wood grain, which exactly describes the new Desert Trail and Cossack Brown stains from Elias. And the company has also reacted quickly to door trends by adding five-part traditional wood doors (Grand Rapids, Sahara, and Primera) in species that work well with the new stains. The overall effect is to bring some warmth back to a market that was leaning toward sterility.
Keystone Wood Specialties (keystonewood.com) is another well-established supplier, and the company celebrated its 50th anniversary in January. Seeing where trends are going, Keystone introduced a simple but clever update to its drawer dividers this spring. It’s in keeping with customers’ needs to be able to change the layout of drawer interiors to accommodate items such as chargers, phones, and kitchen gadgets. The new system is like shelves on their sides. It uses adjustable dividers with holes and pins, where the dividers can be removed, replaced, or relocated.
WalzCraft (walzcraft.com) is a full-service supplier based in Wisconsin that epitomizes the “more choices” aspect of outsourcing. The catalog includes DLV, RTF, solid wood and MDF parts, old-world and contemporary designs, applied moldings, mortise-and-tenon joinery, and both mitered and French-mitered doors and fronts. That last is a clever option that looks like an applied mitered molding on an M&T five-part door from the front, but a quick look around the back reveals that the joinery is a mitered stile-and-rail. It’s more cost-effective than an applied molding, and it provides more structural integrity. It’s also less likely to misbehave in response to arid or humid climates, and there are more profiles available than with an applied stick.
Most of the well-established full line suppliers will have a design software option that works with a popular program that the woodshop is using. That lets the shop select cabinets and other parts from large libraries of options. The scale of the library can be important as some suppliers offer so many sizes that something is bound to work.
The advantages of RTA
One of the most convenient evolutions in cabinetry has been the growth of ready-to-assemble (RTA) options. Arkansas Wood Doors (arkansaswooddoors.com) notes several advantages in outsourcing boxes that are built onsite. They include the fact that RTA cabinets are more easily customizable, require less time to construct, and cost less.
Ordering RTA cabinets is easier than buying fully assembled case goods. For example, Decore-ative Specialties (decore.com) in Monrovia, Calif. builds Streamline RTA cabinets for woodshops across the country and the online ordering process has been honed into a very user-friendly format. Kitchen designers can choose from a variety of cabinet configurations, edge banding, and cabinet materials, and their orders can include assembly hardware. The cabinets then ship from plants in either California or North Carolina with short lead times (6-10 days). Doors, drawer fronts, drawer boxes, and pullouts can all be added, and prices are instantly calculated.
Other major suppliers include CabinetParts.com, Cabinets Quick (cabinetsquick.com), CabParts (cabparts.com), Canary Closets & Cabinetry (canarycc.com), Conestoga Wood Specialties (conestogawood.com), Cooper Enterprises (cooperenterprises.com), Dura Supreme Cabinetry (durasupreme.com), Hardware Resources, (hardwareresources.com), and Stratton Creek Wood Works (strattoncreek.com).
Drawer suppliers
Most cabinet shops enter the world of outsourcing by buying either drawer boxes or doors. They still build the boxes in-house, where they can make small adjustments so that the cases fit the space exactly and the face frames can then accommodate stock door and drawer openings. Square drawers with dovetailed joinery can take a lot of time to set up and make in-house, but cases are relatively quick and not too labor intensive.
Most reputable drawer suppliers will offer a range of quality/price options that can help a small shop cater to a larger clientele. For example, Indiana-based Amish Country Woodworx (acwoodworx.com) offers a range of material choices and 5-, 10- and 15-day turnaround options. CCF Industries (ccfdrawers.com) is based in Pennsylvania and offers a broad selection of materials, including most species of solid woods, Baltic birch and Ultrafoil melamine. A shop can upgrade with personalized laser engraving, edgebanding, adding front or side scoops, and more.
Drawer Box Specialties (DBS, online at dbsdrawers.com) is a States Industries company that’s located in Orange, Calif. This manufacturer offers a premium drawer in white maple that has been graded for color uniformity, plus standard, Baltic birch and melamine boxes for jobs on a budget.
Drawer Connection (dcdrawers.com) has recently partnered with a company called OrganizeToSize to offer a complete selection of custom-made adjustable and fixed American-made drawer dividers.
New England Drawer (newenglanddrawer.com) has switched from Blum slides to a version from Comtrad undermounts, and now offers both its existing Premium and new Select grades of drawer boxes. The new version is a box made in solid maple with whole piece sides up to 9-1/4” tall and dovetailed corners. It’s the same as the Premium drawer in every aspect except the molder applies the eased edge prior to assembly, rather than after. The 1/16” ease goes through the top joint upon assembly, and that minor detail saves a woodshop 10 percent in cost.
Timbercraft Custom Dovetailed Drawers (timbercraftdrawers.com) calls New Milford, Conn. home and the company promises 3-5 days turnaround for current customers and 5-7 days for new customers. They’ll even work with a woodshop and use customer-supplied species such as walnut and mahogany.
Top Drawer Components (topdrwr.com) has been turning out dovetailed drawers for more than three decades and the Arizona-based business also offers a product called the Sliding Susan that is basically a pullout shelf that can carry a wide variety of inserts and organizers to match the drawers they build.
And Western Dovetail (drawer.com), located in Vallejo, Calif., is one of the oldest and most established drawer box providers that has added doors, accessories, and hardware to its catalog over the years.
Doors and more
Shops looking to buy doors may wish to stop by the websites of ACS (atlantacabinet.com), Camtech (campanatechnology.com), Northern Contours (northerncontours.com), REHAU North America (rehau.com), and TaylorCraft Cabinet Door Co. (taylorcraftdoor.com).
For furniture parts, Artisans of the Valley (artisansofthevalley.com) does outsourced custom woodcarving and sculpture, and the company also builds period furniture.
Adams Wood Products (adamswoodproducts.com) offers a wide selection of solid wood cabinet and furniture components that can customize shop-built boxes. Designs of Distinction/Brown Wood (brownwoodinc.com/dod) also offers furniture components, including a wide range of metal accents. Josef’s Art Woodturning & Son (josefsartwoodturning.com) makes everything from bun feet and balusters to corbels and mantels.
Osborne Wood Products (osbornewood.com) carries one of the largest catalogs of furniture components including legs, pilasters, cabinet feet, corbels, brackets, and hardware.
Outwater Plastics & Architectural Products (outwater.com) is another huge resource for woodshops that want to outsource some furniture parts, exterior millwork, interior moldings, carvings, and a whole lot more.
Rev-A-Shelf (rev-a-shelf.com) is one of the most innovative kitchen, bath and closet parts and accessories suppliers for shops that want to buy in organizers, lighting, and just about any add-on that one can imagine for cabinets.
Cabinotch (cabinotch.us) is an award-winning company that developed an innovative system for assembling face-framed and full-access cabinet boxes that feature American-made, formaldehyde-free PureBond hardwood plywood.
The Cabinotch cabinet box system involves a patented interlocking joint, and the company delivers a top-quality, all-wood, custom-sized box including the face frame, sides, backs, bottoms, tops, and shelves that the cabinetmaker can finish and assemble. The boxes are a snap to assemble. The shop them completes the cabinet with in-house or outsourced doors, drawers, finishes and hardware.
Hall’s Edge (hallsedge.com) is a CNC shop in Stamford, Conn. that supplies professional cabinet shops in the surrounding region with custom parts.
This article was originally published in the June 2022 issue.
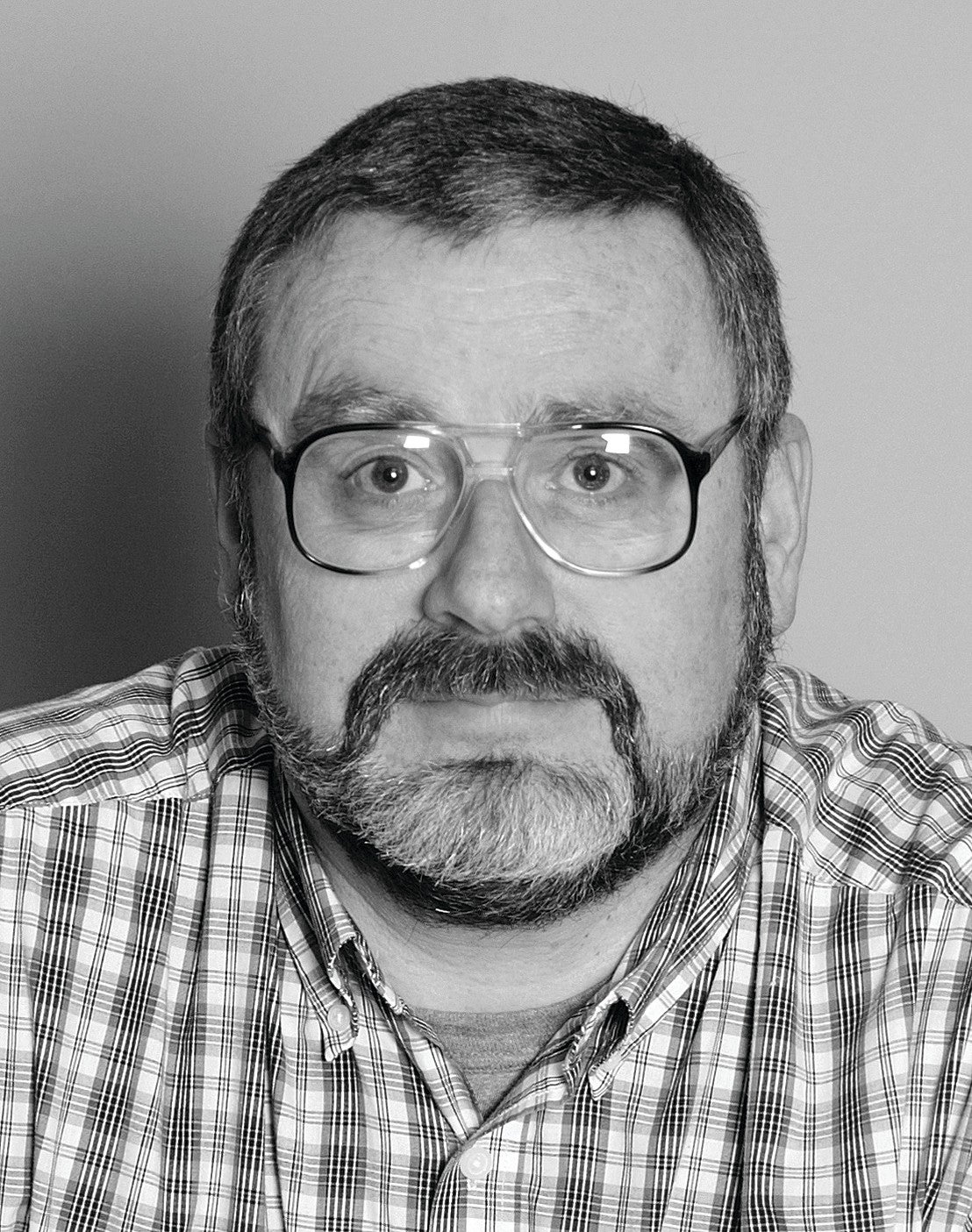