Robots to the rescue
They can perform repetitive tasks and solve labor issues, but not all are created equal
It’s the perfect storm. Inflation, supply woes, full employment, low interest rates, huge demand for product and rapidly advancing technology have all combined to spark what can only be described as an industrial revolution in robotics. It’s economy-wide, but especially visible in production sectors such as auto-bodies, food packaging and, yes, woodworking. Those are all industries where qualified employees are hard to find, there is a high level of repetitive tasking, and orders are currently backlogged.
Robots can mill sand, and coat parts. They can handle and move raw materials, and protect employees from dust, heavy lifting, and sharp tooling. So far, robots in the woodshop are essentially programmed machines that operate arms in six or seven axes and follow designed protocols and pathways. Over the next decade, as A.I. (artificial intelligence) comes into its own, they will begin to think for themselves and learn on the job. For example, Walt Disney Imagineering is currently working on lifelike, ‘thinking’ robots that will soon inhabit its theme parks.
One of the more surprising aspects of this emerging technology is its affordability. Machines can often be leased or purchased for considerably less than the cost of hiring and training a low to medium skilled employee, and they can work two or three shifts a day. They also do exactly what they are told, don’t take coffee breaks, deliver accurate repeatability, and don’t catch Covid. Woodshops that produce large volumes of identical or nearly identical parts such as doors, shelves and drawers can be well-served by the addition of robots. Shops that produce highly customized and individual or unique work can still find areas where the current crop of robots can help, but they may also look down the road a decade at machines that will add a whole new level of art to their craft.
Types of robots
While loading, unloading, and positioning robots are doing a lot of the heavy lifting in larger shops, the most common type of tasking robot in small- and medium-sized woodshops is an automated arm called a collaborative robot, or cobot. This is a step up from a simple lifting and placement arm because it can sense the presence of humans and avoid contact with them, thereby essentially eliminating collision-based injuries.
The National Institute of Standards and Technology (NIST) is part of the Commerce Department, and it has categorized industrial robots into four groups: articulated, SCARA, Delta and Cartesian.
Articulated robots are generally bolted to a bench, wall, floor, ceiling, or larger machine surface, and they have an arm with a base, shoulder, elbow and wrist that can swivel. These familiar robots can pick and place parts, tend CNCs, do both additive and subtraction processes (3D printing, routing and shaping), and even perform some gluing and assembly tasks. They can have four, six (most common) or seven axes, and some have considerable reach and payload capacities. They can reach up, into and around parts and subassemblies, and because they are sealed, dust and coatings are not issues. These are not the cheapest robots, but they’re probably the most flexible and usable when it comes to casework and furniture manufacturing. They’re also not the fastest, so if a shop has a very simple task to perform there may be a more economical solution. But when it comes to complex tasks, articulated robots are hard to beat.
SCARA (Selective Compliance Articulated Robot Arm) robots are less expensive than articulated arms, and these simple machines are the best choice for picking and placing parts or hardware components. They can, for example, drop a piece of hardware into a slot or mortise, if the slots are always in the same location on the worktable. SCARA robots have a simple swing arm which is very rigid, so they can operate at higher speeds but in a much more limited manner than an articulated robot.
Delta robots don’t often find their way into woodshops. They are more delicate and very lightweight, and they are used in industries where high speed and accuracy are more important than strength (such as cosmetics and food). These are three-legged spider robots that look a lot like the arcade claw games.
Cartesian robots can often look a bit like a CNC. These are gantry robots that are designed for heavy lifting. They move in X, Y and Z planes (those are the Cartesian coordinates, hence the name), and they can have a fourth (rotary) axis in some applications. One advantage to Cartesian robots over, say articulated 6-axis robots, is that their reach is defined by the gantry. Swing your own arm and it describes an elliptical or circular shape. That is the range of motion for an articulated robot. But a Cartesian robot’s movement is defined by the gantry, so it can travel all the way into, and then reach into square corners.
The ways they work
The robotics industry describes robots in terms of manipulation, mobility, and data acquisition/control. According to the University of Leeds in the U.K., “robotic manipulation refers to the ways robots interact with the objects around them: grasping an object, opening a door, packing an order into a box, folding laundry… All these actions require robots to plan and control the motion of their hands and arms in an intelligent way.”
Robotic mobility is as simple as it sounds: the robot can move around the shop. This can be on tracks, or within a defined work area where sensors locate limits. Some service robots can travel autonomously from one machine to another, but this is high-end, expensive technology that’s generally beyond the reach of small- to mid-sized woodshops. Those robots can have wheels or legs, and some can even swim. For the most part, woodworking robots are not mobile. Yet.
Data acquisition and control robots can monitor processes, machine performance, and even employee performance. This type of robot is often used to create signals that tell less sophisticated robots what to do next.
Other terms that a woodworker may come across when researching whether to invest in a robot include cylindrical, polar, pre-programmed, humanoid, autonomous, teleoperated and augmenting robots.
Cylindrical robots are simple machines that have a base with a vertical shaft that rotates, and some variety of sliding arm or tool attached to the shaft. They’re commonly used for simple assembly of two parts, and they are more likely to find a home in an environment that requires tasks such as spot welding than installing woodscrews.
Polar or spherical robots have a linear (sliding) joint and two rotary (revolving) joints. The result is a spherical work area, so they can pick and place parts, assemble parts, apply glue, or even install and remove tooling on a machine.
Pre-programmed robots are units that have been told ahead of start-up what they will do, and there is no variance in response to a changing environment. That is, they don’t and can’t change their behavior. So, if they are told to plow a stopped groove in a certain direction and the wood is too short, they’ll simply continue in a straight line. They are ideal for simple, repetitive tasks in uniform parts or raw materials.
Humanoid robots are just robots that look and move like people. It’ll be a while before they grace the average woodshop.
Autonomous robots are those little machines that vacuum your living-room or mow the lawn. They can move and react to obstructions in their environment. Self-driving automobiles will eventually use this kind of technology, and in the woodshop cobots are already using it to avoid bumping into people or letting humans encounter the sharp ends of tools that the robots are using.
Teleoperated robots are remotely controlled machines that are being operated by a human in real time, but from a distance. These are very common in medical applications, but not so much in woodworking. They might, for example, be used in conservation work to strip lead paint or remove mold from wood, or perhaps do sculptural carving on a species that is known to cause allergic reactions. This technology uses Bluetooth or other wireless solutions, and sometimes tethered controls (wires) to operate machines, much as kids drive remote control cars.
The prevalent uses for an augmenting robot are to help a disabled person perform mobility tasks, or to help an able-bodied person increase their performance (that is, make them stronger, faster, etc.). This is the technology used to control prosthetic limbs, and to operate exoskeletons that are used to lift hefty weights.
For the most part, cabinet and furniture shops are going to want to look at robots that can do repetitive tasks, keep jobs moving through the shop when employees are absent or have moved on, and can provide a high level of reliability with few defects and very little re-work. As wages continue to rise and technology becomes more affordable, the woodworking industry is beginning to follow the path taken by the automotive sector and invest heavily in robotics. For shops that do extremely custom work, the future looks rosy. For shops that do production work, that future is now.
This article was originally published in the March 2022 issue.
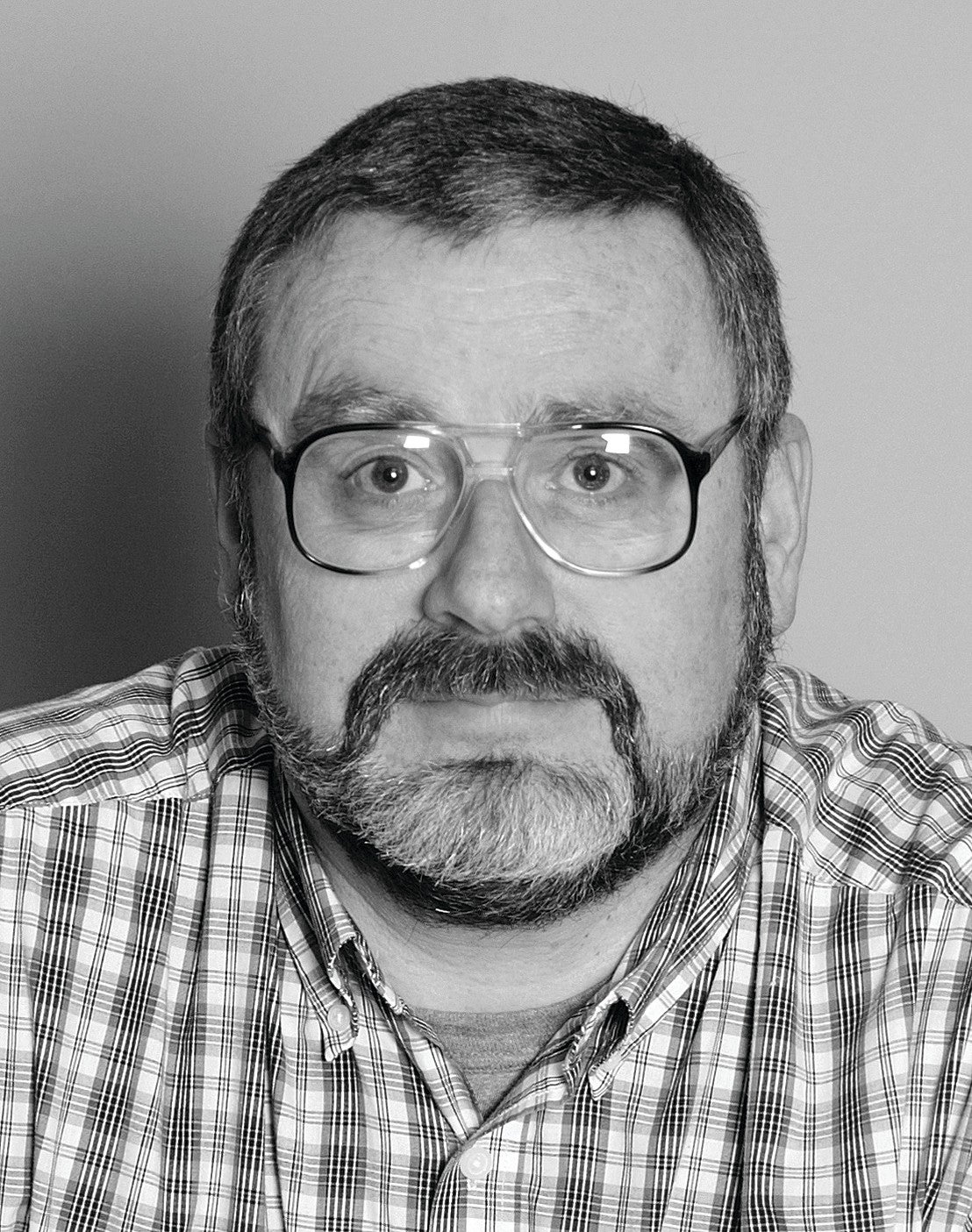