Schooling for CNC Tooling
Cost, durability and accuracy are among the factors involved in sourcing specialized tooling.
Customers can push our limits. Their demands often force us to learn and grow, to test our own competencies and the abilities of our machines.
There’s hardly a job that comes through most custom shops that doesn’t require at least one unique setup, profile or tooling solution. That challenge can be frustrating, but most of the time it’s fun, too. There’s some satisfaction in going online or calling a supplier and finding exactly what’s needed to do what needs to be done. And it’s a special feeling to watch a part that is absolutely perfect as it comes off a CNC because the right tool was used.
The first challenge is knowing what the machine can do. The second is knowing what tooling is needed to make that happen. There’s often more than one way to make a part, so the issue here is efficiency. What tool will deliver perfect results at the lowest cost, both in terms of money and time?
Showing some metal
The interplay between time and money shows up most in the material used to make the tool, or at least to make the cutting edge. There are many different grades of steel, carbide and commercial diamonds, and there’s always a little give and take. High speed steel (HSS) is the least expensive option, and also the one with the fastest failing edge. Tearing down a setup to sharpen a bit or replace it is a timely and thus expensive choice, so it’s not terribly popular.
S Alloy is a nickel-based alloy (a mix of two or more metals) that allows the steel to withstand greater heat, and thereby outlast standard HSS. It retains more of its strength and ductility (the quality of giving a little without becoming more brittle) as it heats up. That option was brought to woodworking tools by Charles G.G. Schmidt & Co. (cggschmidt.net) of Montvale, N.J., in the 1960s.
Since then, the company has expanded its options to include carbide CNC bits and diamond-tipped router bits. That larger menu is now the industry standard, and woodshops looking at new tooling should discuss this aspect in detail with a salesperson. It can be difficult to find the right relationship between cost and durability, and accuracy is also an issue. As with hand tools, a perfect edge on a carbide insert may deliver a cleaner cut that a manmade diamond cutter, at least on a microscopic scale. But the diamond will perform at the same efficiency for much longer.
Custom toolmakers such as H3D Tool Corp. (h3dtool.com) in Connelly Springs, N.C., can inform buyers about the differences between diamond, solid carbide and insert cutting tools. In addition to saw blades, spiral routers, tool holders and collets, this company has manufactured custom tooling for the woodworking and solid surface industries since the mid 1960s with a slight nuance. H3D doesn’t just braze diamond to a steel body and cut in a profile. Its tooling, whenever possible, incorporates a split wing design to allow for opposing shear angles. This has the added advantage that the smaller diamond segments minimize repair costs, should an accident occur. Given the initial cost of upgrading to diamond from carbide, that’s a valid consideration.
Product literature from Riverside Tool Corp. (riversidetool.com) in Elkhart, Ind., points out that PCD (polycrystalline diamond) tooling lasts a long time because it renews through erosion, rather than edge breakdown. Its diamond aggregate is laid onto a substrate of cemented tungsten carbide in a coating that is 0.6 to 0.8 mm thick, and the carbide backer is from 1 to 2.7 mm thick, depending on the task. The company also says that, given its durability, PCD is the lowest cost per foot tooling option, and the way that it cuts also delivers more efficient dust collection. That’s worth thinking about – sometimes a cut will need to be cleaned up, and complex profiles can present quite a challenge and be very time-consuming for traditional sanding stations. So, Riverside offers SuperSand profile sanders for any custom profile (think raised panels or moldings), and they’re non-directional so they can take advantage of reverse rotation if it’s available. Plus, the company will work with a woodshop to make the sanders fit pretty much any machine.
Another solution, Turbosand, is offered by California-based Voorwood (voorwood.com), which includes more than 4,000 stock profile options. The device can be tilted, and it has a simple, two-piece construction that uses short strips of sandpaper in various grits. The sanding strips can be changed quickly and easily, and Turbosand comes in HSK or ISO toolholder options with available custom adapters and a variety of diameters from 3” to 8”. It can also sand edges from 1/2” to 3”.
Another dust aid for CNC tooling is Techniks USA’s AirPro dust extractor. This device mounts on ER32, ER40 and SYOZ25 collet chucks, and works with standard bits to reduce both floor and airborne dust. AirPro can be found in Techniks wood-based catalog (online at techniksusa.com), which also includes a large selection of aggregate heads. These include options designed to add an axis to small routers, all the way to custom built versions that can dramatically expand the CNC tooling’s ability to work on complex and unique forms. An aggregate head can not only deliver more angles, it can also save on setups.
Other considerations
Recognizing that setup time can be costly, Leuco (leuco.com) is one of a handful of companies that offer distinct color coding on tools to help woodworkers easily and instantly choose the right tool. Leuco not only provides sales and sharpening, but also offers leasing on some tooling. That can help a wood products manufacturer with the cost of upgrading to diamond tools.
Sharpening is definitely an issue when choosing tooling. It helps to find a company such as FS Tool (fstoolcorp.com) in Lewiston, N.Y., that uses the same robotic grinding center to sharpen the tools that actually made them in the first place. FS also addresses balance, tension and seating as part of the sharpening/service regimen.
Dust collection, color coding and lease options can all influence a shop manager in choosing a CNC tooling supplier. And sometimes, the decision is nuanced by something even more subtle. For example, woodshops near a coastline have to deal with rust issues, so it might help to find a supplier who is familiar with the challenge presented by salty air. The sales office for ComSurge Industrial Tooling (comsurge.com) is in Mission Viejo, Calif., a stone’s throw from the Pacific, so it’s familiar with the challenge. ComSurge has OEM relationships with several major U.S. cutting tool companies and can also help source industrial quality tooling in Taiwan or China. Among its offerings are router bits, collets and insert knives.
Freeborn Tool Co. (freeborntool.com) offers brazed shaper cutters, insert cutters, spiral surfacing cutters, router bits, custom tooling, and options for CNC tooling that is all made in the U.S.A. The company uses optical comparators to individually match sets so that the tooling delivers product that has no manufacturing defects or transition lines. Comparators magnify a part on a screen, and then measure the geometry and dimensions against a baseline to achieve extremely accurate results.
Once you have the tooling, holding it properly in the machine can be the next hurdle. Companies such as the German-based T-Tool (t-toolusa.com) offer tapered holders for virtually any CNC configuration, along with collets, nuts, pull studs and wrenches. The company’s SuperSpeed collets have extended lengths in HSK-63F and E options that offer an advanced level of set-up options in multi-axis machines. And T-Tool’s new line of collets can help minimize runout, which will increase the useful life of tooling.
One of the best ways to save both time and money when it comes to CNC tooling is to find a supplier that is renowned for customer support, and few in the industry do that better than Stiles Machinery in Grand Rapids, Mich. (stilesmachinery.com). The company offers 24/7 technical support, and in-house training through Stiles University. It’s easy for a smaller shop to get lost in the world of major manufacturing, and to feel as though its small problem has no place in the high-tech, hi volume tooling market. So, in addition to bits, collets and tool-holders, the supplier you choose needs to have experts in-house that can not only tell you what’s available, but can take the time to listen, too.
This article originally appeared in the April 2019 issue.
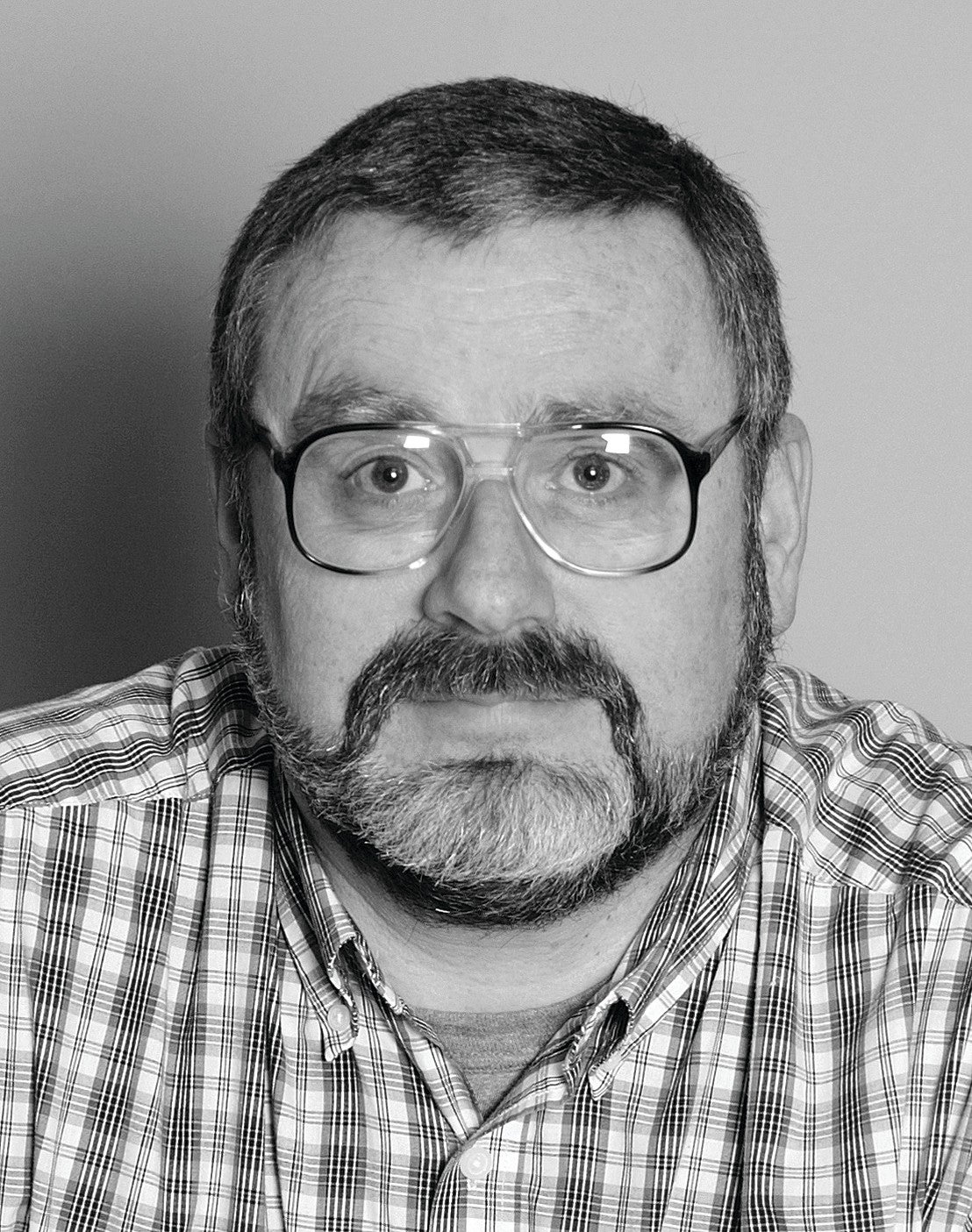