Service call
The old adage “If it ain’t broke, don’t fix it,” makes a lot of sense. But woodshops still need to do routine maintenance or else machines and production both suffer….
The old adage “If it ain’t broke, don’t fix it,” makes a lot of sense. But woodshops still need to do routine maintenance or else machines and production both suffer. While shops are relying more and more on high tech, software-driven equipment or outsourcing, the daily workload in most woodshops is still handled by machines and cutters that need a little routine TLC.
The word “routine” is key. There are some things that need to be checked every day and others that might only need a look-see once a month or year. Keeping track of that process begins with a list. Cutters and blades, fences, lubrication points and filters are some of the hot spots that should find their way onto a maintenance checklist.
The first step in building such a list is to do an inventory of the tools and equipment that need to be included. Every office has a computer with a basic spreadsheet program such as Microsoft Excel that can make quick work of sorting data. The sort function means that sub-lists can be generated for daily or weekly tasks or the list can be sorted according to machines, cutters or even who is responsible for completing maintenance.
Each shop will, of course, be different and many of the items that need to be lubed or cleaned might not even be woodworking machines. The equipment on the list might include a forklift or a furnace or perhaps even a panel truck used for deliveries. As long as it has moving parts, there will probably be some routine maintenance tasks to perform.
Making one employee responsible for maintenance has both advantages and disadvantages. The downside potential is obvious: he or she might not be as diligent as one would hope or as competent. What happens when he is sick or on vacation or finds a different job? On the other hand, having one person accountable means the buck stops somewhere and that person should get pretty good at taking care of things over time. But training a backup still makes a lot of sense, especially if the backup is the foreman or owner. That way, the regular employee’s work can be audited every now and then and tweaked to keep routines up to date.
What is servicing?
For most shops, service includes routine maintenance, some minor repairs and the ability to acknowledge when it’s time to call in a pro. For a one-man shop, the latter can often boil down to the question of whether he is in the woodworking or machine repair business — he needs to balance the cost of lost production against the invoice from a machine shop. For larger outfits, bringing in a pro is almost always the way to go, because downtime affects more than one workstation and there’s a domino effect. If the motor on the table saw fries, several people can be idled while it’s down.
Many machine manufacturers offer comprehensive repair or replacement programs, especially for items such as CNC spindles or servo motors. And routine maintenance on most woodshop equipment is usually handled in-house or through a service agreement with a nearby machine shop. But major repairs are a different matter and can’t always be done locally. A woodshop needs to have a couple of reputable companies it can rely on, where the local technician can remove a part and send it to a specialist who has access to both brand-based expertise and OEM components.
Hermance Machine is a good example of such a resource. The company offers a full range of repair and reconditioning services and parts can be shipped to its facility in Williamsport, Pa., where technicians can perform precision repairs or fabricate replacement parts to OEM specifications.
If you’re having work done on a machine, see if there are any performance or safety updates that can be added. It’s often less expensive to do that when the equipment is already in for service. At a minimum, you’ll save on shipping costs.
Reliability and experience are both important when choosing a service facility. The best choice is a machine shop that can make parts in-house and has been doing so for a while. For example, Northfield Woodworking Machinery Co. began life in Minnesota back in 1920 and is still a leader in the intermediate and heavy-duty woodworking machinery fields. The company’s own product line was the first to adapt hydraulics in woodworking machinery and beyond building new machines Northfield also does a large volume of outside machine work. If a woodshop uses older Northfield equipment, the company says parts availability even for its discontinued machinery is excellent. By bringing machines back to the original builder for repair, a woodshop also benefits by having it worked on by factory service technicians that are familiar with it and can handle everything from tune-ups to complete rebuilds. Northfield works both on site and in its own machine shop and on most brands.
Many other North American machinery suppliers also do repair and maintenance. Akhurst Machinery Ltd. is the largest independent machinery distributor in Canada. The company sells and services a full range of woodworking and panel processing machinery to the cabinet, millwork, furniture and door manufacturing industries. Akhurst has 16 factory-trained service technicians who can often diagnose problems on the phone.
Larger service outfits are often regional in their coverage. In the southeastern U.S., for example, First Choice Industrial offers repair, installation and training across Georgia, Florida, Alabama, Tennessee, North Carolina and South Carolina. And woodshops located in Texas, Louisiana or Oklahoma can call on Dallas-based SIS Machinery for rebuilding that includes complete disassembly, component cleaning and degreasing, inspection for wear or defects, replacement of bearings, seals and gaskets, and replacement of electrical components so your equipment meets current manufacturer’s specs.
Among ways to find a reputable service supplier are networking with other shop owners through woodworking organizations and trade shows or through brand-specific chat rooms, tool owner websites and discussion groups. Some of these are very active and many organize tours of woodshops, saw mills or other venues where shop owners can meet each other and discuss matters of common interest. Start the search by plugging your machine brand and model number into a search engine and add the words “forum,” “chat” or “group.”
The cost of in-house help
A certain amount of equipment servicing can be done in-house without tying up too much of the woodworking crews’ time. But there comes a point when it might make more sense to hire a designated maintenance person who can change out bits and blades, check the filters on the dust collector and pneumatic hoses, vacuum sawdust out of the machines and perform a hundred other minor tasks. It also makes sense for that person to work an overlap shift, where half of his/her time is spent on the shop floor when production workers are present and the rest of the hours are worked before the woodworkers arrive or after they leave. That lets the service person interact with the woodworking crew and ask questions and also have the place to himself without somebody waiting for a machine to come back online while he changes belts, oil or filters.
The cost of in-house maintenance depends on a few things. Is this a full- or part-time position? Some shops have the service person working a half-shift as a woodworker and a half-shift on equipment service, which can make a lot of sense: the technician is not only servicing the machines, but is also using them in their everyday functions, so he becomes much more familiar with their idiosyncrasies.
When it comes to cost, skill levels play a big role. The Bureau of Labor Statistics tells us that a machinist’s hourly pay is $19.97, while a person qualified to repair electric motors will earn about $20.12 an hour (national mean average). Skilled building maintenance workers are listed at $19.13, so it’s probably fair to say that an in-house maintenance person who can do most minor repairs should be paid in the neighborhood of $20 an hour. Cabinetmakers and bench carpenters, according to BLS, only earn $14.78 on average while “woodworkers” make $15.10. Rounding up and down, let’s call that $15 an hour. Of course, custom shops with highly skilled cabinetmakers and furniture builders are going to pay at a different level than large production shops that require very little training.
There are other costs involved, too. As a shop grows, the maintenance person will require training in new areas — everything from servicing CNC routers to boiler maintenance or forklift repair. Some of that can happen on the job, some through Internet webinars and online classes and some at local community colleges or vocational schools. All of it costs money, because the employee is being paid to learn while not directly contributing to the shop’s bottom line during class hours. A shop might also need to invest in new tools and equipment to bring maintenance in-house — from simple stepladders and wrenches to diagnostic equipment or software programs. There can also be insurance riders and changes in workers’ comp premiums.
Sometimes, there are personality hiccups. Older workers who have run the same machine for years or even decades might resent a new person being brought in to tune up their workstation. Or woodworkers might resent the fact that the person servicing the equipment makes more than the person running it.
By and large, there is definitely a point where bringing maintenance in-house is a good idea. If a trained technician can change out the spindle in a shaper in minutes, rather than a woodworker taking time away from building cabinets and spending an hour to do the repair task, then you’re probably at a point where you need to assess the situation.
Prevention beats a cure
Comprehensive Maintenance Solutions is owned and operated by Ron Young in Chagrin Falls, Ohio. The company specializes in servicing woodshop equipment and gives some no-nonsense advice on its website:
“There is nothing more frustrating then missing an on-time delivery due to equipment failure, especially if that failure could have been avoided’” he says. “Preventative maintenance is more than greasing and oiling your machines, though. A good preventative maintenance program anticipates the type of breakdowns you will likely have and takes steps to ensure they never happen.
“There are several ways for you to determine the best time to replace bearings, gearboxes and other mechanical parts on your equipment. Unfortunately if you wait for your equipment’s performance to dictate when to replace a wearing item, it can cost you more money because of damage done to surrounding parts, rework of parts to bring them up to quality standards and unplanned equipment downtime.”
His point is rudimentary: changing the oil regularly is a lot less expensive than changing the motor when it dies. He also says if a machine isn’t performing perfectly, it’s better to stop production and find out why — before production stops because you didn’t. CMS advises that you follow the manufacturer’s recommended maintenance schedule, but don’t do so blindly. Sometimes those recommendations are based on testing that involved extremely harsh conditions. Sometimes a part will far outlast the recommended replacement schedule. It pays to have an expert periodically inspect bearings and other critical elements. And if the technician is using ultrasonic analysis equipment (it measures decibels and detects anomalies), the odds of discovering problems before they become debilitating are a lot higher.
When a piece of equipment fails, it not only slows or stops job production, it can often result in injury. Imagine something as simple as a defective collet on a table-mounted router that releases a bit that is spinning at 20,000 rpm. Or a dado head mounted on an eccentric arbor that shakes loose under a load. Keeping accurate records of routine maintenance, service and inspections can go a long way toward mitigating damages in a lawsuit. But, far more importantly, performing those service regimens can help prevent such an event from ever occurring.
Larry Wessling is a mechanic, plumber and maintenance professional in the Midwest who looks after a number of businesses. One piece of advice he offers is to use a digital camera or even a smartphone to record images of labels, serial numbers and even critical parts of machines (perhaps spindles or motors) so that you can email pictures to a service professional in the event there is a problem. Sometimes the breakdown happens when the boss is out of town and having this crucial information on a laptop or phone can prevent all kinds of delays or even avoid wrong repair parts being shipped because maybe the model year was wrong. Plus, having copies of such records off-site means that in a cataclysmic event such as a major fire at the shop, there will be evidence for the insurance company when it comes to replacing equipment.
Such photos (or even amateur videos) can also be used to help train employees in routine maintenance chores. A series of photos on, for example, changing jointer knives, can really speed up the learning curve. A woodshop manager could even print them and create a three-ring binder for each machine. After all, the bottom line on equipment servicing is this: if it ain’t broke, you’re probably being diligent about routine maintenance.
This article originally appeared in the December 2015 issue.
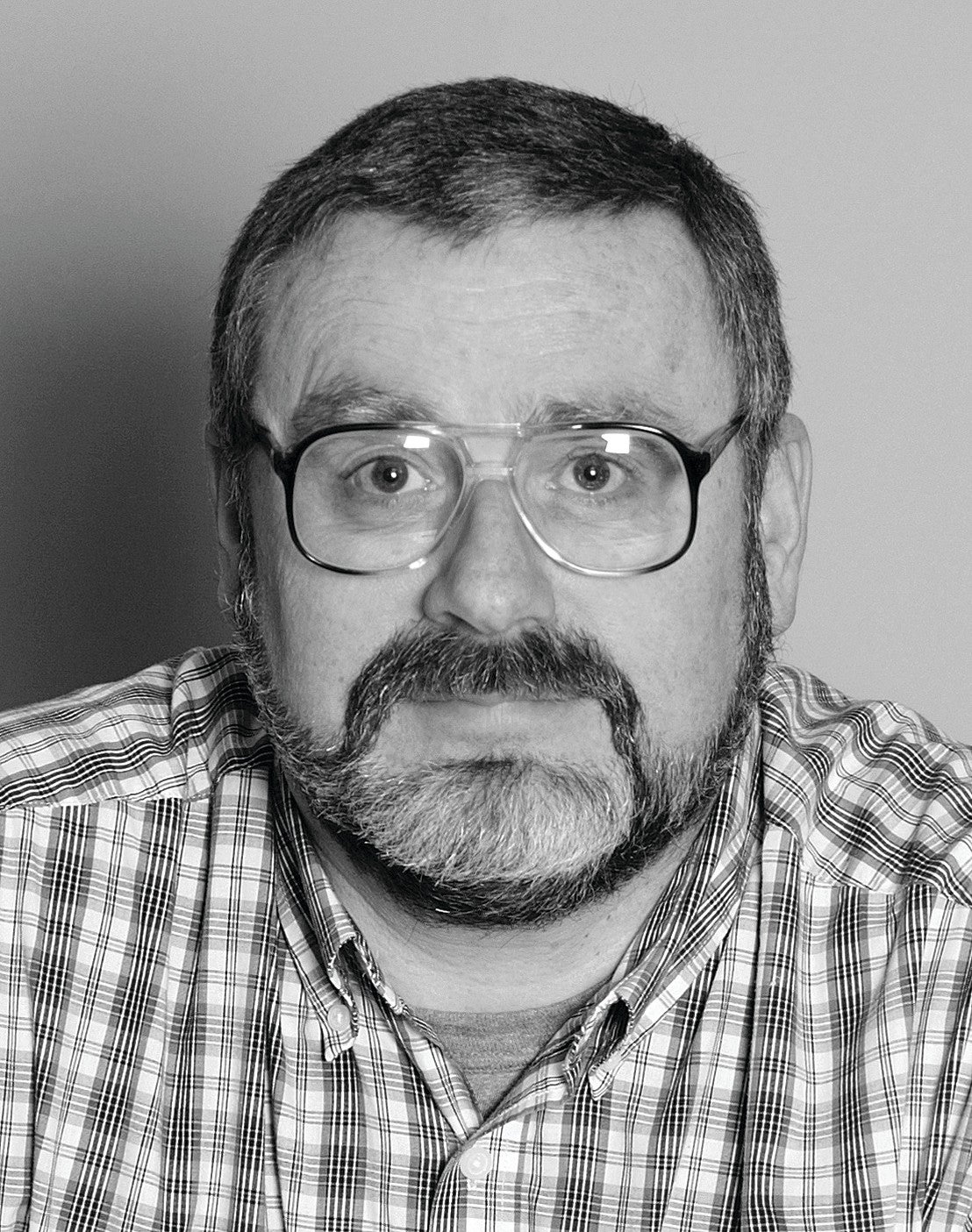