Space Savers
A dozen or so ideas to gain some valuable real estate in your shop.
No woodshop has ever been large enough.
No matter how many square feet are available, we always seem to expand into every corner and eventually feel cramped. That’s just as true for a one-man shop as it is an operation producing several kitchens a week. So, here are some ideas that can organize everything from workstations to inventory, and perhaps recover some of that lost space.
Make it mobile
Over the past few years, several of the major power tool manufacturers have developed storage container systems for organizing portable tools and supplies. Festool, Makita, Milwaukee, DeWalt, Stanley, Bosch, Ironton (Northern Tool), Ridgid and Craftsman immediately come to mind, but there are many others. Several of these systems involve stacking boxes on a wheeled base – they look like large carry-on luggage. Storing portable power tools in these containers makes them easy to find, access and take to a jobsite.
Be aware that you do tend to get what you pay for. The more expensive ones are generally better engineered, more thoughtfully designed, more rugged and a little easier to use. Some will work with other systems – for example, several of Makita’s boxes are compatible with elements of Festool’s Systainer cases and other similar modular storage systems. Some of the portable toolboxes are completely empty inside, while others come with partitions, drawers or small parts organizers. Most are weatherproof and lockable, for jobsite security, and those with larger wheels can handle stairs and rough terrain more easily.
Another slightly mobile idea is to add a sliding/rolling ladder to the woodshop. Often called library ladders, hardware kits to build them are very affordable and they allow a woodworker to hang and store items high up on the shop walls. They can be used to access cabinets, shelves and racks that are mounted above arm’s reach, seriously extending the shop’s storage and workable spaces.
Speaking of carts, every woodshop needs two – one for clamps and another for scraps. Putting them on sturdy casters makes them mobile. Both can be built with a 2x4 base and a vertical wall. Small blocks can be used as spacers to keep longer bar or pipe clamps in place, and spring clamps can be stored on a 1x2 that’s secured on edge. One side of a scrap cart can be used to store sheet stock while the other can provide a home for hardwood cut-offs.
Bins win
Many plastic garage shelving systems are just the right size for large, clear-sided, lidded totes that let a woodworker see what’s inside at a glance, and also keep the contents dust free. The totes are easy to carry around the shop or throw in the truck, and they can hold everything from machine accessories to rags, clamps, portable power tools, drawer slides, pulls and other hardware inventory.
Many plastic totes come with wide lips around the top. These will slide easily into ceiling-mounted L-shaped brackets/cleats and act just like drawer slides. That’s a great solution for seldom-used items, but not so handy for tools or parts that are frequently needed.
Next time you’re at the lumberyard, throw a sheet of slatwall in the back of the truck. This can be cut into small sections and screwed to walls above workbenches, the ends of storage cabinets or even the backs of doors. Big box stores sell all kinds of hooks and organizers for slatwall, and it’s a great way to save space and get organized. The system can be used to store small jigs, or even wrenches and screwdrivers. Add small eye hooks to the ends of tools with wooden handles such as lathe chisels, and then store them on slatwall hooks.
Get a sheet of pegboard, too. There are many uses, but one in particular works well in my shop. By attaching a small section to a plywood backing, you’ve got portable storage for hex bits that will fit into the holes. The trick is to use the back end of the bit to enlarge the holes for a proper fit.
Jigs take up a lot of space, especially in shops that build furniture. The key to organizing them is to label them clearly, so one doesn’t need to dig through piles to find a specific jig. That way they can be stored in order from tall at the back to small at the front on shelves, or perhaps atop tool cabinets.
Adding casters to workbenches and machinery can free up space. Several companies offer mobile tool bases that minimize how much the machine is elevated, while still providing a sturdy and stable platform. Some of them supply corners with casters, and the woodworker can just add dimensional lumber to create custom-sized bases.
Framing lumber can be used to create knockdown assembly systems that can be erected quickly and stored easily after use. These are just sawhorses and 2x4s that replace large, permanent benches. The new Speedhorse XT from Bora Tool (model PM-4550) is an excellent candidate here: it has height-adjustable legs that can raise the working level six inches to save backs, and the feet are independent, so they work well on uneven ground.
If the shop is simply too small to accommodate long parts, follow woodworker Ken Froelich’s lead. He’s a professional furniture artist with a very small space, so he cut holes in the walls for outfeed stock from his miter saw, table saw and thickness planer. He made small insulated boxes that are held in place with magnets, and the outside faces match the siding on his shop.
Waste knots, want not
There’s something in the nature of woodworking that encourages hoarding. Perhaps it’s the way we can constantly use little bits and pieces to create useful objects. But given the physical restrictions of most shops, it’s incumbent upon us to throw away or at least recycle scraps or they will eventually overwhelm the space. One solution is to make a size rule (kind of like that frame at the airport where your carry-on luggage needs to fit through), and then stick to it.
A woodshop can also donate scraps to school districts that have a woodworking program or recycle them as firewood (we drop off ours once a month at a local campground), or even leave them by the curb with a “free” sign, which seems to work really well for a local storage shed manufacturer. The good stuff goes faster than I can get there…
Saving space in the workshop might be as simple as moving some things out of the shop entirely. Is there room in the yard or parking lot for a storage shed? Is there an attic, basement or loft that could become a warehouse?
One other viable and increasingly popular solution to saving shop space is to outsource. That reduces machines, inventory and even completed jobs, if the shop has projects delivered directly to the jobsite. It can also reduce the workforce (which might free up a parking spot for that storage shed).
Another great way to recover lost space is to practice just-in-time inventory management. This is a gateway to lean manufacturing, which has at its heart the elimination of waste. Woodshops that practice lean manufacturing try to incorporate workshop space savers in every aspect of their processes. When it comes to inventory, they only buy enough cabinet hardware, sheet goods, finishing supplies and other materials for the current spate of jobs. That way they don’t need to store, handle or pay for excess inventory that occupies valuable shop space.
And no woodshop has ever been large enough for that.
This article was originally published in the January 2021 issue.
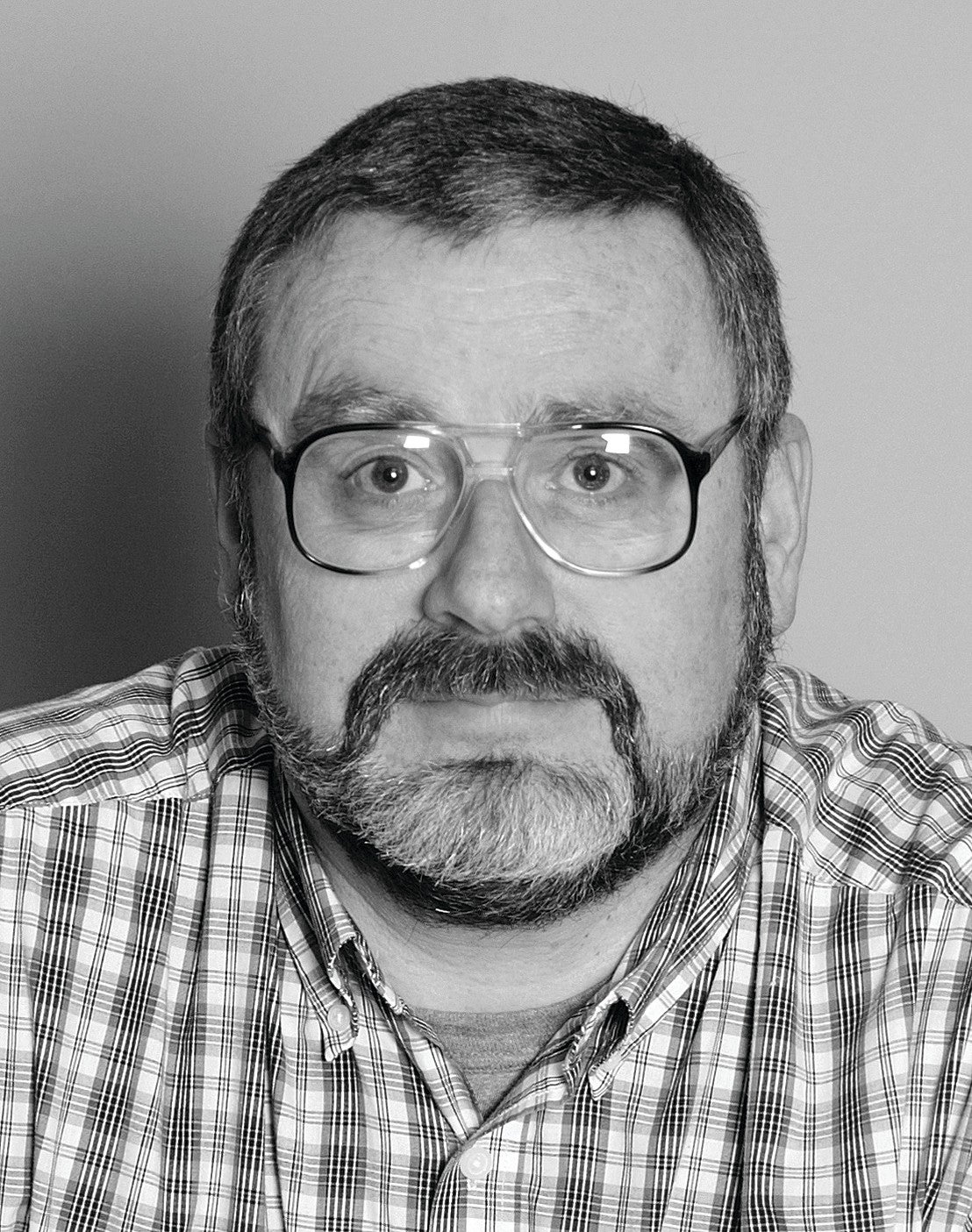