Space-saving, multi-function machines
Multi-function woodworking machines are, by their nature, a trade-off. The idea is that the woodworker gains floor space and surrenders some speed and convenience.
Combination machines have been around for a long time. For example, the British manufacturer Samuel Worssam & Co. designed and built a multi-function woodworking machine back in the mid-19th century. Called the Patent General Joiner, it was capable of rip and cross cuts, miters, chamfers, single and double tenons, mortising, boring, molding, beading, rabbeting, and grooving. The key to its success was that one setup didn’t have to be dismantled to perform another task, so as many as three people could work on the machine simultaneously.
Multi-function woodworking machines are, by their nature, a trade-off. The idea is that the woodworker gains floor space and surrenders some speed and convenience. There are also some cost implications that we’ll look at in a minute, but to gain some insight into the space and convenience angle, Woodshop News spoke with master furniture artist Mark Koons. He worked in a small woodshop located a couple of hours north of Denver for four decades, and he has only recently expanded into larger premises. Some of his observations as a multi-function machine user over a long stretch of time will underscore questions that shop owners may have when contemplating the purchase of this equipment.
The Interview
We began with a question about traffic and congestion. Conventional wisdom says that the square footage demanded by a multi-purpose machine can be significantly less than the floorspace required by several dedicated machines. We asked him if he found that to be true.
“In my case, the space savings were minimal,” Koons noted, “because the path for the operation of each function must be kept open.” Koons built studio furniture, cabinetry, and architectural elements, and he noted that one of the notable constraints on space management was not the infeed and outfeed space but the dust hoses. Some multi-function machines require an octopus of dust collection hoses to run efficiently, and those tentacles can get in the way.
“All of that marginally effective ducting will be under foot,” he says. “Or it needs to drop from above, unless the owner is lucky enough to be able to route dust collection from below.”
That’s a significant point for shop owners to consider. And so is the idea that the shop’s collection system may need an update. Many bag and duct suppliers will help woodworkers assess the ability of their current dust collection systems to effectively serve multi-function machinery. How the ductwork attaches can be an issue. Can the shop install hoses and ducts so that they don’t interfere with the operation of the machine, and do the hoses get in the way during changeovers from one task to another?
Next up, we asked about size and power. Many multi-function machines are equipped with 3-phase motors that consume a little less power while delivering similar or better torque.
“I bought a new cast iron 5-hp, 3-phase multi-function machine way back in the 1980s,” Koons noted. “The model that I chose had a rolling crosscut table, could spin a 12” saw blade, had a 30mm shaper shaft along with 16” jointer/planer functions, and it also had a horizontal mortiser. That cast iron spec is important – a lot of budget machines are built with stamped tin and aluminum, but I remain heavily prejudiced toward cast iron machinery.”
His point is well-taken. The mass of cast iron reduces vibration, and it’s a more stable material over time than sheet metal.
“On the subject of power,” he continues, “I don’t think small shops should automatically buy a 3-phase machine even if they have ‘cheap’ 3-phase power. Not all 3-phase power proves to be cheap – a lot depends on whether the shop is zoned commercial or industrial. The exception would be if the machine is going to be installed in a busy commercial shop, where it will run most of the time on most days. But then, why would a high-volume shop want five functions tied up by one worker doing a single operation?
“There’s also the issue of resale. Even if the machine makes sense today for a specific woodshop that has access to 3-phase, the shop may have a difficult task in finding a buyer because most small shops only have access to single phase. And if you do finally find a buyer, you may realize the return of only a small fraction of your investment. If I remember correctly, an $18,000 original investment soon cost me about $25,000 with blades, cutters, and attachments. Those were 1980s dollars. I recently sold the unit for about 18 percent of what it cost, not adjusted for inflation.”
Koons also notes that while a multi-function machine can work very efficiently for small, repetitive solid wood parts in a furniture shop, it may not be the ideal solution for a cabinetmaker building primarily with MDF or plywood. A sliding table saw and a CNC may be more appropriate.
“A potential buyer needs to evaluate processes,” he says. “Consider the necessity of, say, taper-jointing a single piece during a build, or trimming 1/64” off a dozen pieces, or replacing a single botched part that must be surfaced, ripped, jointed, planed, crosscut, and mortised.”
Every shop works differently, and a lot depends on the size and shape of parts.
“For instance,” he says, “breaking down 4’ x 8’ sheet goods, or even ripping smaller panels can be a challenge on the restricted workspaces available on many smaller multi-function machines. So can cross-cutting 8’ stock, shaping the edge of a desk or tabletop, or perhaps jointing and planing several hundred feet of rough cut hardwood.”
Those tasks are not challenging on larger, industrial machines with sliding tables, but they can be for small, entry-level equipment. Installing infeed, outfeed, and conveyor tables to alleviate that issue will probably negate much of the space savings, because those tables can eat up square footage when they are supported by carts or scissor lifts, and they also require more room for the operator to move around them. The point here is to match the multi-function machine to the work, and to begin with a scaled drawing of the workspace and the workflow before committing to a specific machine or configuration.
Paper, he notes, is less expensive and easier to revise than cast iron and ductwork.
Downtime issues
When it comes to multi-function machines, the biggest question in most shop owners’ minds is the downtime involved in changing functions and the need to rebuild set-ups after each changeover. While that isn’t usually a huge problem for one-man artisan shops, it can be a real issue for production shops and one that the shop owner should consider.
“Though salesmen and promotional videos demonstrate switching from one function to another in seconds,” says Koons, “that has not been my personal experience in real life, and especially not so when effective dust collection is required. But the biggest trade-off, and this was true of the machine that I had, was that to switch from one function to another meant losing the adjustment of the first.”
It can be very time-consuming to set up a machine to perfectly match a previous batch of parts. So, it’s important to engage the salesperson in a deep conversation about maintaining setups between changes, and to question the ability of the machine to accurately return to its former setup. Koons stresses that a shop owner needs to fully understand the physics involved. How the shop works is also an issue here. Is it possible to run all the parts through one function before switching to the next, thereby obviating the need to return to a former setup? If that’s true, then it makes the option of a multi-function machine a lot more attractive. If it’s not, then there’s going to be downtime required for setups, and resetting.
Koons also advises potential buyers to pay attention to quality issues and engineering, and to read the reviews before choosing a specific model. Thankfully, the Internet now provides a way to easily research machines before buying them. Feedback from existing users can be invaluable. Forty years ago, when Koons bough his machine, that wasn’t an option.
“Nowadays when I see YouTube videos of combination jointer/planers in use, I remember my machine’s short, drooping jointer tables and their tendency to bow across their width when the cam locks were tightened. A planer’s feed rollers belong in the bed and should be elevated two to four one-thousandths above it. Many combination machines that I’ve seen have a feed roller and a pinch roller, alongside a small diameter cutterhead. That arrangement results in difficult, jerky feeding and burned or burnished planed surfaces.”
He also recommends joining a users’ group before purchasing and then spend a little time chasing the threads. It won’t be long before salient issues surface, and you can see how current machine owners are addressing them.
Other thoughts
Some multi-function machines have several tools that share a single motor, while others rely on separate motors for different tasks. Either mode requires less infrastructure than installing several separate machines, so there can be some cost savings. There’s less wiring and dust collection ductwork to hook up, fewer traffic lanes to maintain, less lighting and HVAC, significantly fewer footsteps with a single machine, and maybe even some savings in maintenance. However, if all functions are powered by a single motor, and it goes down.
Some high-end multi-function machines from established manufacturers are quite expensive, in part because the engineers use premium parts to withstand the increased usage. You get what you pay for. The increased cost can deliver a much longer life, fewer maintenance issues, cleaner and more accurate parts, and a manufacturer that stands behind their product and offers exceptional support.
One thing that has changed since the days of Samuel Worssam’s innovative Patent General Joiner is that today’s machines are almost universally designed for a single operator. That’s in part a result of the way that woodworking has become more specialized and compartmentalized over time. Today, fine furniture building and cabinetmaking have drifted into separate spheres, so a woodshop may want to examine the direction of its own drift when assessing how a multi-function machine fits into the plan.
For sources, search combination machines at resourceguide.woodshopnews.com.
This article was originally published in the January 2023 issue.
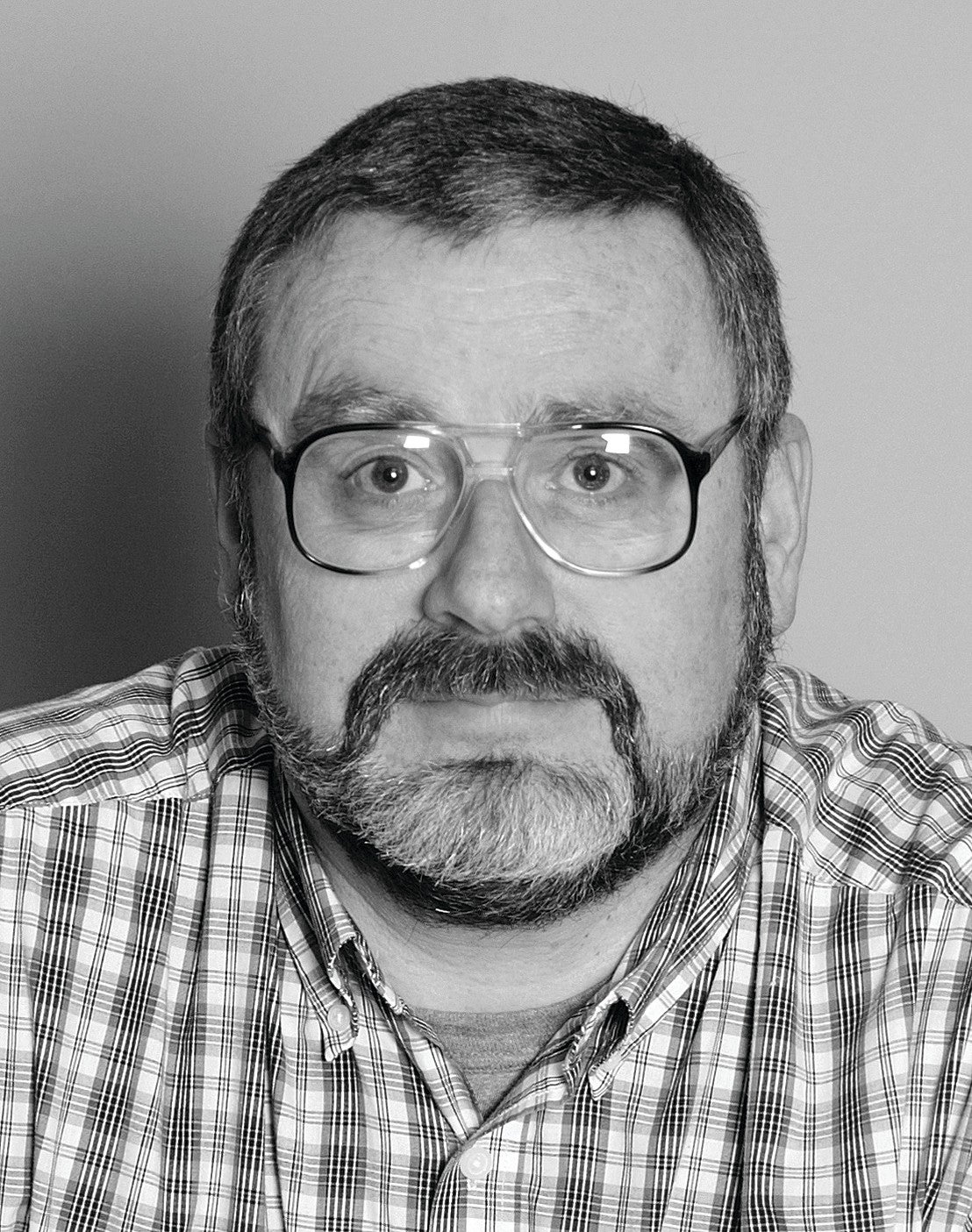