The damage done by dust
We breathe in two types of wood dust — organic and inorganic. The former can be spores or fungi released by deteriorating lumber, pollens, seeds, oils, plant toxins, pesticides and…
We breathe in two types of wood dust — organic and inorganic. The former can be spores or fungi released by deteriorating lumber, pollens, seeds, oils, plant toxins, pesticides and so on. Inorganic dust in the woodshop is primarily composed of dead cell walls ground fine (such as sanding dust) or residue from MDF, plastic laminates, finishes and other chemicals used in furniture and cabinet building.
Here’s what happens when a woodworker breathes in dust:
The largest particles are trapped by nose hair and eliminated when we sneeze or blow our noses. Finer particles that the nose doesn’t capture reach the windpipe. This passageway leads to two large pipes going to the lungs, which are called bronchial tubes. Each of these organs produces mucus that traps fine dust and eliminates it by expelling the mucus. Small hairs known as cilia do this and the action induces a reaction that causes us to spit or cough.
In the lungs, any fine particles that finally make it through all of these lines of defense are trapped in alveoli (air sacs), where they are surrounded by cells called macrophages that are then moved back up the system through the bronchial tubes and into the mouth and throat.
All in all, the body is extremely well-equipped to deal with dust. But our natural defenses can give way over time because of long or intense levels of exposure.
If a woodworker’s nose is constantly being clogged year after year, this can lead to rhinitis, which is an inflammation of the membrane that produces mucus in the nasal cavities. Untreated and constant irritation over several years can cause the tissue to develop cancerous cells.
Farther down the pulmonary system, between the mouth and the lungs, dust can cause bronchitis or a condition known as tracheitis, which the National Institutes of Health defines as “a bacterial infection of the windpipe (trachea).”
The bottom line is that the health of woodshop owners and their employees is a significant reason to take a good look at a shop’s dust control system. There are other reasons, too. For example, the quality of sprayed or brushed finishes relies on clean air, especially during the curing process, and both walkways and workstations need to have clean floors.
Collecting most of the dust really isn’t good enough. A dust control system needs to collect virtually all the residue, especially fine particles that are light enough to become airborne.
Ductwork
The first place to look for problems (and possibly upgrade) is the ductwork. A few rolls of duct tape can be a really good investment here. Metal ductwork expands and contracts through the years, especially in parts of the country that have wide variances in climate. Every year, joints in the system move a little and this can create small gaps that leach fines into the shop’s atmosphere. Remember that the air inside the pipes is under a lot more pressure than ambient air in the woodshop, so small gaps become avenues of escape. Sealing these with silicone caulk (when the system is turned off or the leak will blow the seal away) or using duct tape can eliminate the problem.
Are your ducts sized properly? Running the same diameter pipe throughout the shop is not an efficient or effective way to manage airflow. Ducts should reduce in diameter as they traverse distance and as branch lines intercept them. That is, the pipe should get smaller after each Y-joint or as they travel farther from the dust collector. For help here, visit the website of almost any ductwork supplier and they will offer a design service that suggests the correct diameter pipes for your shop’s floor plan. Air Handling Systems (www.airhand.com) offers a free downloadable guide to building a dust collection system that answers virtually any technical question you might have on design.
One of the basic elements of any great design is the length of the runs. To keep them short, one can either place the collector in a central location or install a smaller unit in each “nest” of machines. The latter is a better choice when a shop has more than one area where it makes parts. For example, one collector can handle saws and milling, while the other is designated to sanding operations. Trying to do everything with one collector could mean that nothing is done well. The only other viable option is to install a system that is so oversized for the task that inefficiencies don’t matter. That can be expensive to buy and expensive to run.
A professional designer will take into consideration the dust collector(s) you already own and the type of machines you are running. That’s important, because the residue from a wide belt sander is a whole lot different in both texture (particle size) and volume than, for example, the residue from a thickness planer.
A design service is also going to be able to point out some problems with your existing system and might even be able to help you upgrade without replacing a whole lot of ductwork. One of the most common problems is undersized pipe, especially near the collector. Go with the biggest diameter you can for a main duct and resist the temptation to turn the inlet close to the machine into two smaller and relatively ineffective main runs.
When transitioning down in size, it’s better to use a tapered fitting rather than a stepped one. That is, allow the pipe to get smaller gradually, rather than in one dramatic step. This will more aptly maintain the level of static pressure, which is essentially a measurement of loss in both speed and volume of airflow. Think of it as “resistance.”
One should also try to avoid inexpensive flexible hose. A lot of shops install a great system until they get close to the machine that’s producing dust and then they make the final connection with cheap, ribbed, flexible hose. Low-end hose is often corrugated and this disturbs and reduces air flow. A little research online will reveal several manufacturers who make flex hoses that provide excellent flow and virtually no resistance. They’re more expensive, but their application usually calls for short lengths, so the cost isn’t prohibitive. And the results can be quite impressive.
If the ductwork turns a corner, it shouldn’t have an L-joint. The transition needs to be smooth and gradual. One solution is to replace a 90 with two 45s that have a short length of straight pipe (maybe a foot or so) between them. This allows the air flow to change direction in two small steps rather than one large one.
For smaller shops, an easy way to reduce lots of bends near the collector is to build a platform that raises the unit as high off the floor as the ceiling will allow. That way, any ceiling-mounted pipework doesn’t have to travel all the way to the floor to get connected, so it doesn’t have to try to carry its load through several changes in direction.
Collectors
Choosing the right collector requires quite a bit of thought. For larger shops, the best answer is perhaps to employ a consultant or a knowledgeable salesperson from a reputable company. For small- and medium-sized shops, the process can be broken into two stages — design the system and then go shopping. Knowing exactly what is needed is essential, before looking at shiny new toys.
Oneida Air Systems offers a very handy flowchart, walking a shop owner through the various choices, at www.oneida-air.com. There’s a pretty good basic guide to designing a system for a small shop at www.artofwoodshopdesign.com.
Building a system that can’t handle expansion is a fairly common error and overbuilding can be expensive. One should also take a look at aftermarket filter bags. On a lot of smaller dust collectors, efficiency can be greatly improved by swapping out the factory filter for a custom bag that either increases the air volume or air flow. And it’s not just size and shape that can affect airflow. The actual fabric material plays a big role, too. American Fabric Filter (www.americanfabricfilter.com) manufactures a huge range of fabric products such as optimized air filtration/dust containment bags and sleeves in any shape and size. It also customizes products with inlets, outlets, flanges, support hardware, windows and other options, such as maybe adding a few loops so you can hang the bag from a ceiling hook.
Machinery is always evolving and sometimes two technologies combine to create a new and better one. Manufacturers have understood for a long time that a cyclone system can separate fine and gross particles, allowing filter bags to do a better job. And filter manufacturers have been steadily working on the problem of catching smaller particles while still allowing air to flow freely.
Recently, Grizzly introduced a new line of dual-filtration, HEPA filter, cyclone-style dust collectors. What HEPA does for a filtering system is that it catches those very small particles that escape our natural defenses and cause harm over time. The Grizzly models have a primary filter efficiency of 99.9 percent at 0.2-2 microns and a secondary HEPA filter efficiency of 99.97 percent at 0.3 microns in size. That is, they can catch particles that are less than a micron in size and do so more than 99 percent of the time.
A new approach to dust control is being pioneered by Servair. The company’s sanding booths are available in 5-, 10- and 15-hp models that use a bank of pleated filters to scrub the air and return it to the room. That means heating and cooling costs are no longer major issues. Previously, booths that evacuated dust outside also eliminated pre-cooled or warmed shop air, and running a furnace or AC unit to compensate for that was expensive. The new booths are quiet (less than 80dB), the filters self-clean, and each unit comes with filter monitoring gauges.
Sanding booths can be even more effective if the task is being done on a downdraft table. Marrying these two technologies can potentially remove all volatile particles from the sanding process. Companies such as Sandman Products (www.sandmanproducts.com) have developed a range of tables in various sizes, so choosing the right one is as simple as measuring the parts that will be processed on it. When a downdraft table is in place, much less dust makes it to the booth filters, so they can go a lot longer between cleanings.
The idea of collecting dust at the source (the point where it is generated) has been raised to a fine art by engineers at Festool (www.festoolusa.com) and several other manufacturers are now following. Many of the company’s sanders deliver virtually dust-free sanding when used with one of their HEPA CT Dust Extractors. The more dust control that happens at the tool, the less needs to be handled by a large central vac system.
The Danish company Nilfisk-Alto has been around for more than a century and offers four different models of extremely rugged wet/dry vacs that are ideal for cleanup on kitchen installations. The filters clean themselves and these little machines even have two-stage collection, which helps them last a long time. They can also be fitted with a HEPA exhaust filter that captures 99.97 percent of particles down to 0.3 microns.
Scrubbers and gates
If a shop doesn’t have efficient collection at the tool, a lot of fine particles escape into the air and remain in circulation until they come to rest. Then, every time a board is moved or an employee walks by, those particles are again propelled into the breathable air in the shop. The only way to tackle this problem is to scrub the air. A host of small, ceiling-mounted options are available (search for “hanging air filter”). Among the most robust is the 0-600CI from General International (www.general.ca). It has three air speeds, five timer settings (to shut it down when nobody is in the shop), a 1/3-hp motor and two filters — a fine and a coarse. It also comes with a remote control, so employees can turn on this ceiling-mounted unit when it is hung higher than their heads (maximum distance is 49 feet).
Several manufacturers also tackle the ago-old problem of woodworkers forgetting to close blast gates. A dust control system is essentially sealed, so the fewer “holes” in it, the better it works. In a small shop, if blast gates are left open at three or four machines, the collector won’t be able to generate a vacuum with enough volume and speed to do its job. A California company called Grn Gate (www.grngate.com) has developed simple control systems that are easy to install on new and existing ductwork and they close all but the one gate where any dust-making machine is turned on. Ecogate (www.ecogate.com) is combining simple blast gate controls with advanced electronics.
Dust control is all about air volume, especially when it comes to scrubbing the air. One way to maximize the performance of collectors and filtering systems is to break a large space into smaller ones and to confine the contaminated air in a limited space than can be more effectively controlled and cleaned. Rather than build permanent walls that might not work well when production routines change, a woodshop can install relatively inexpensive curtain walls to do the job.
One last thought: dust isn’t the only problem with shop vacuums, especially the small ones found in a lot of one-man or hobbyist shops. Some of them create a heck of a lot of noise for their size. One solution is to locate them in another room or a closet and run a hose to the workstation, but that’s not always feasible.
Another relatively inexpensive solution is to add a muffler. For shop vacs, there are brand-specific versions that are available from big box stores and for small dust collectors. Penn State industries sells a product called the Suppressor Dust Collector Muffler, which will reduce the noise from a typical collector by 5 to 10 db. That doesn’t sound like much (no pun intended), but it’s enough to cross the line between detrimental and innoxious noise levels.
This article originally appeared in the March 2015 issue.
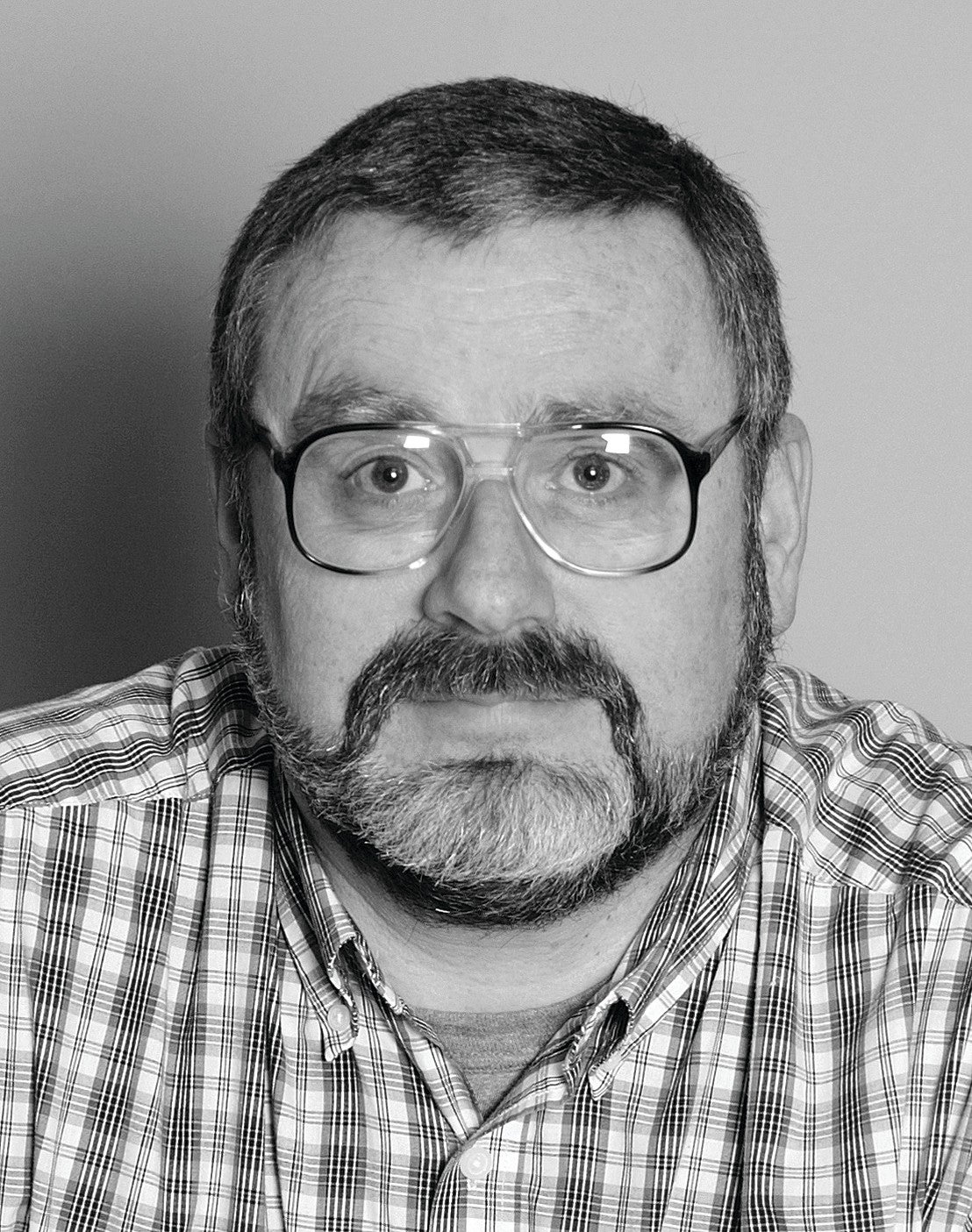