The history behind glues holding pattern
It’s pretty astounding when you think about it. Dress a couple of board edges on the jointer, spread a little glue, clamp for an hour or two … and they’re…
It’s pretty astounding when you think about it. Dress a couple of board edges on the jointer, spread a little glue, clamp for an hour or two … and they’re united for life!
How can a little bit of liquid work that well?
The first clue we have about what’s going on is the distinction between adhesion and cohesion. Merriam-Webster defines adhesion in a number of ways, one of which is “the molecular attraction exerted between the surfaces of bodies in contact.” What that means is that adhesion describes the ability of two different things (wood and glue) to stick together. Cohesion, on the other hand, is a “molecular attraction by which the particles of a body are united throughout the mass.” So, cohesion describes the way in which a substance sticks to itself. Well, more precisely, it’s the way in which the molecules within a compound like to hang together.
Have you ever taken apart a piece of furniture where the wood failed and the glue is still intact? That’s an adhesion failure. Two different materials failed to bond. If, on the other hand, the joint came apart along the glued seam, where half the glue stayed stuck to each piece of wood, then that’s a cohesion failure.
We’re talking about adhesion and cohesion on a molecular level here. Surprisingly, both processes depend on physical laws that are fairly similar to the way that magnets work. Remember when, as kids, we were fascinated when two magnets would attract or repel each other because of polarity? Well, it turns out that molecules do something fairly similar. We know this because of the work of a guy who probably never even walked through a woodshop — Johannes Diderik van der Waals (1837-1923). He was a professor at the University of Amsterdam in Holland and he won the Nobel Prize for physics in 1910. One of his achievements was defining what has come to be known as van der Waals force, which is used to describe the attractive or repulsive forces between molecules. In simple terms, he discovered how molecules either attract or repel each other. That can be true of both similar (cohesive, as in glue-to-glue) and dissimilar (adhesive, as in glue-to-wood) structures.
One of the factors that govern how well van der Waals force works is the proximity of the molecules. The closer they are, the stronger the reaction (either attraction or repulsion). We’re talking microscopic distances here — the width of an atom can make a difference. So, while clamping pressure keeps the parts of a cabinet aligned where we want them to be, it is also helping this unseen reaction to take place. When glue squeezes out of a joint, the remaining glue is being compressed between the wood parts and spreads thinly across the surfaces that are to be bonded. That reduction in volume helps adhesion (squeezing glue into the cells of the wood means there are more square inches of contact) and also helps prevent cohesive failure. That’s because the thinner the layer of glue, the less chance there is that the bonds within the glue itself will fail.
Well, that’s generally true, but there are exceptions. Some glue types have excellent gap-filling qualities. That is, they have very strong cohesive bonding properties (where they stick well to themselves), and this is often accompanied by poor adhesion to wood. Other glue types are the other way around: they might bond tightly to wood, but not to themselves, and thus are poor gap fillers.
Other forces at work
So far, we’ve talked about a chemical bond between glue and wood and also between glue and glue. There is another physical science at work here, too: mechanics. It’s not as powerful as a molecular bond, but theoretically it also contributes to the way in which glue will stick two pieces of wood together.
You’ll need to look at this through an imaginary microscope because the scale is so tiny. Think about the fibrous cells in wood and the physical properties of splinters. Run your fingers across a rough-sawn board and the odds are that a few small pieces will penetrate your skin and make you reach for the tweezers. Those diminutive splinters have two characteristics that simultaneously combine to make them do that. They are both flexible and inflexible. They’re like tiny, hinged spears that stay straight and rigid along their length, but can move at their base and change direction — so they are at exactly the right angle to pierce your skin.
Now think of what happens when you clamp two wooden edges together. The action is, of course, less dramatic than it is with rough-sawn wood, because you have either jointed or planed the rough wood to what looks and feels like smooth surfaces. But looking through the microscope, those planes are anything but flat. When they are wetted with glue, they become more flexible and swollen — much in the way that grain is raised when a thin coat of sanding sealer is applied. Mash these wet surfaces together under clamping pressure and the fibers and cells comingle and entwine. There isn’t much of a mechanical bond happening yet: these are very small parts dancing with each other and they’re still flexible. But leave them under pressure for a while and as the glue cures they become permanently locked together. They harden, entwined, and contribute something to the bond.
Drying and curing
So why doesn’t glue harden in the bottle?
The answer lies in a couple of basic terms. Set time (also called dry time) is the amount of time that needs to elapse before you can handle a glue-up assembly. Cure time, on the other hand, defines how long you need to wait before subjecting the new joint to pressure or stress. By the way, open time — that wonderful window of opportunity when you can still move parts before the glue begins to stiffen — is not the same thing as set time. Glue can become sufficiently tacky to prevent adjustments long before the set time expires.
On most woodworking glue bottles, the instructions will indicate that the assembly needs to be clamped for at least a couple of hours, but that one should wait overnight before machining the parts or subjecting them to stress — such as being moved from machine to machine or perhaps passing through the rollers of a thickness planer.
That first stage where the parts are still clamped (set time) allows the carrier to evaporate and the glue to dry. A carrier is a chemical compound that allows the glue to take the form of a liquid at room temperature. The most common is dihydrogen monoxide, which is just ordinary, everyday water. As the carrier evaporates into the air (dries), a molecular level process takes place that reduces the liquid glue to a solid state. Even though it becomes stable, with many glue types it is not yet strong. A further chemical reaction needs to take place that causes the now solid compound to harden and gain strength. That reaction (curing) takes more time because the elements in the glue are not as volatile as water.
So the simple answer is that glue doesn’t harden in the bottle because the carrier can’t escape and evaporate. In a way, one could say that glue hardens when it reacts with air. But that’s not really what’s happening. More accurately, glue transforms from a liquid to a solid state when the carrier evaporates into the air.
Some “instant” glue is built around more volatile (highly evaporative) carriers than water and these disappear more quickly and produce a stable bond in very little time. These glues are sometimes less effective, long-lasting or forgiving than standard wood glues, so there can be a tradeoff. It might be convenient to have the glue cure very quickly, but the bond might not have quite the same integrity as a slow-curing compound.
Other glues, such as hot-melt adhesives, forego the evaporative stage. They don’t depend on a carrier. They are already in a solid state (pellets or cartridges) at room temperature and actually require a physical catalyst (heat) to change their state temporarily. That is, they need to go from a solid to a liquid so they can be used and then almost immediately return to a solid state so they bond without clamping.
That quick metamorphosis isn’t the only reason that shops use heat-based glue. The most common adhesive in processes such as edgebanding is ethylene-vinyl acetate (EVA), which is also known as polyethylene-vinyl acetate (PEVA). While it’s essentially a plastic, EVA is also soft, flexible, waterproof, resistant to ultraviolet radiation (so it doesn’t delaminate on furniture in basic sunlight) and it also doesn’t have too many stress cracks in its dry/cured state. The vinyl part of EVA is essentially the same compound used to make things like car seats and dashboards, while the ethylene is a highly bondable hydrocarbon (it has four hydrogen atoms bound to two carbon atoms). EVA has strong adhesive and respectable cohesive qualities, which makes it a great choice for applying banding to the relatively rough surface of MDF.
This article originally appeared in the July 2015 issue.
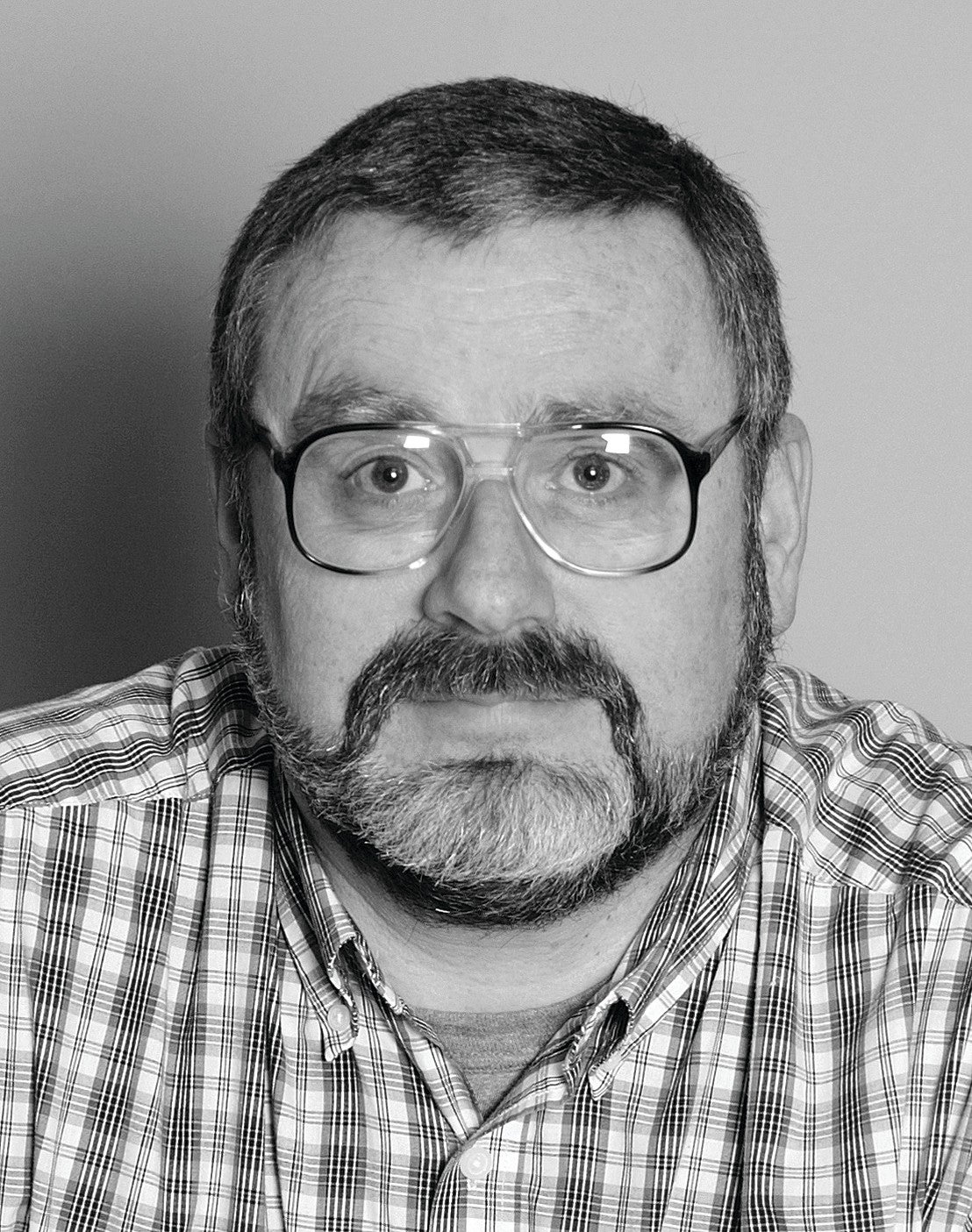